Precision Machining for Energy Efficiency
48-Hour Prototyping
1-Week Small-Batch Production
2-3 Week Mass Production
Reduce Costs by 15%
All uploads are secure and confidential.* Learn More
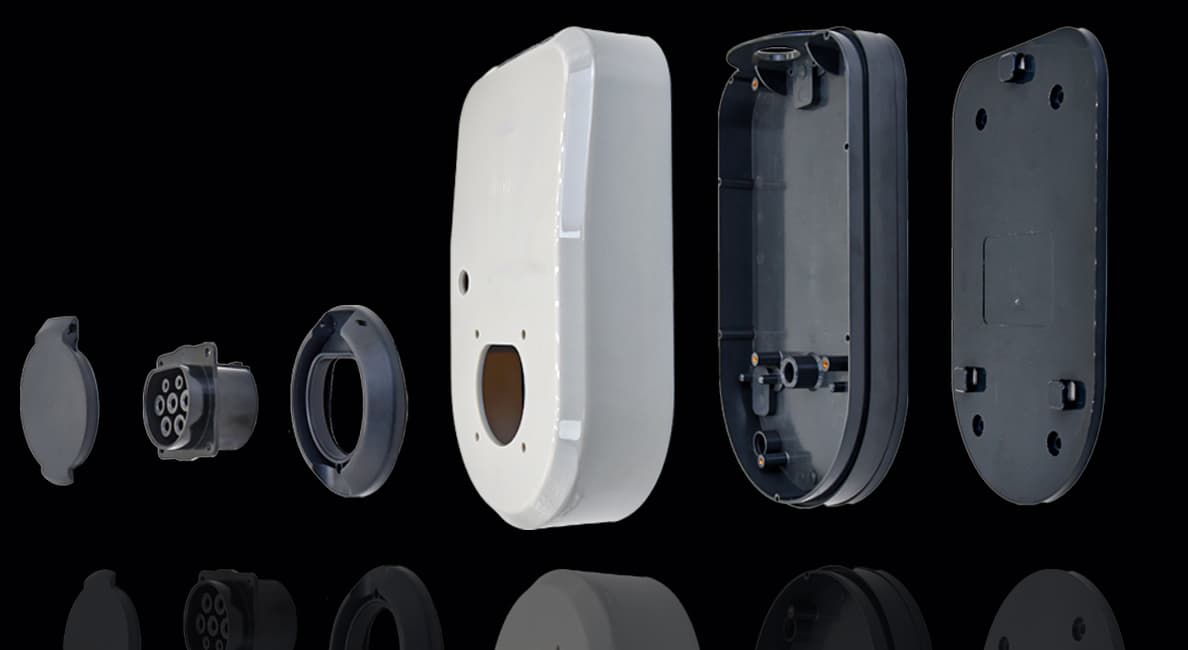
IOS 9001
IOS 14001

About Our Capabilities
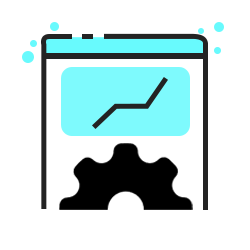
High-Efficiency Machining
Enhancing Conversion
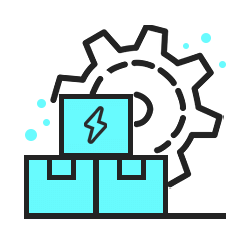
Rapid Production
Shortening Cycles
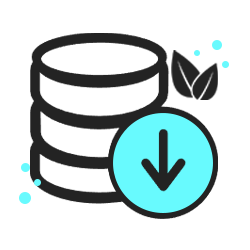
Low-Carbon and
Cost
Optimization
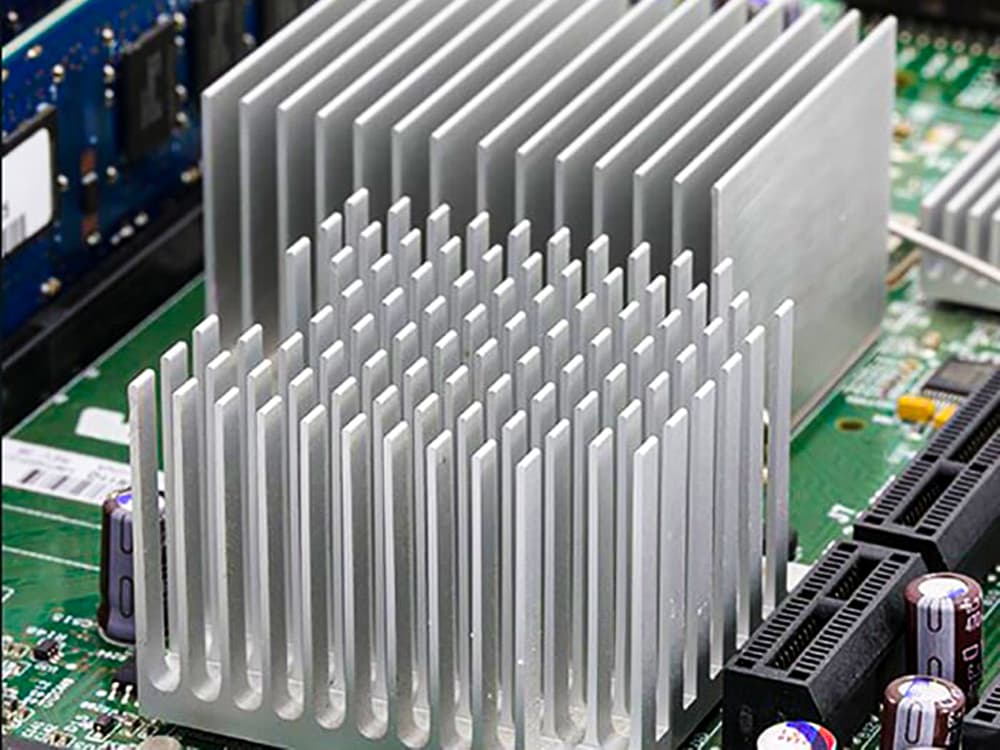
High-Efficiency Part Machining, Enhancing Energy Conversion
Specializing in machining battery housings, heat sinks, and drive system parts.
Utilizing 5-axis and high-precision CNC equipment with tolerances up to ±0.005mm.
Boosting energy efficiency by 15%+ for EVs and energy storage systems.
Rapid Prototyping and Production, Shortening Product Development Cycles
Completing prototype machining within 48 hours after receiving design drawings.
Small-batch production starts within 1 week, speeding up iteration and market launch.
Serving 1,000+ new energy projects annually, with delivery cycles shortened by 20%.
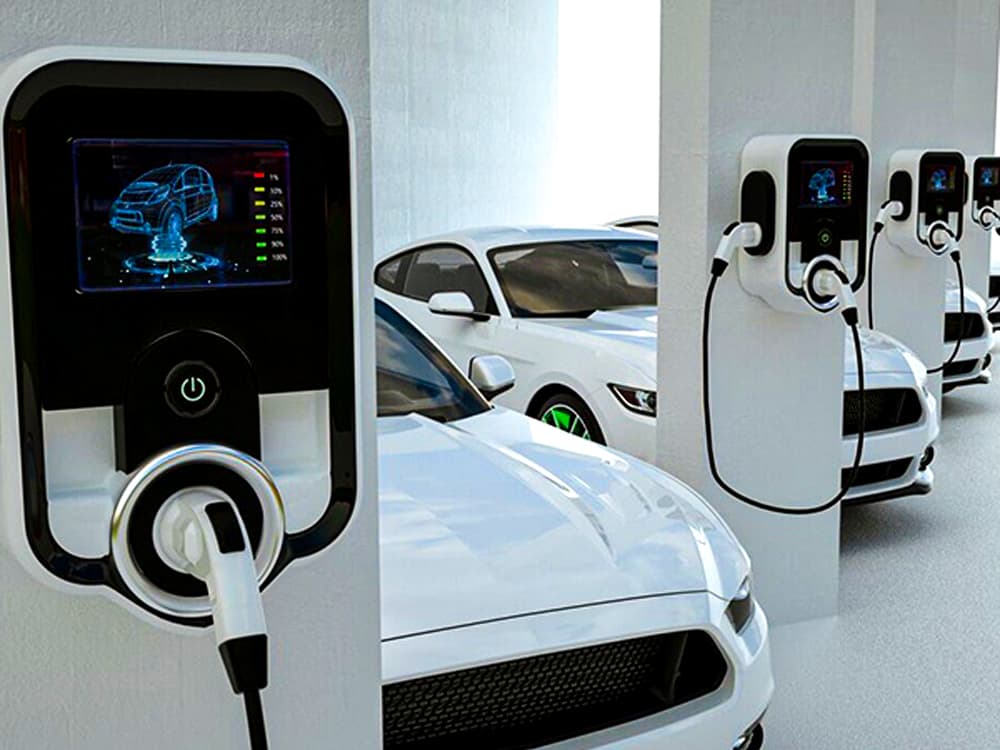
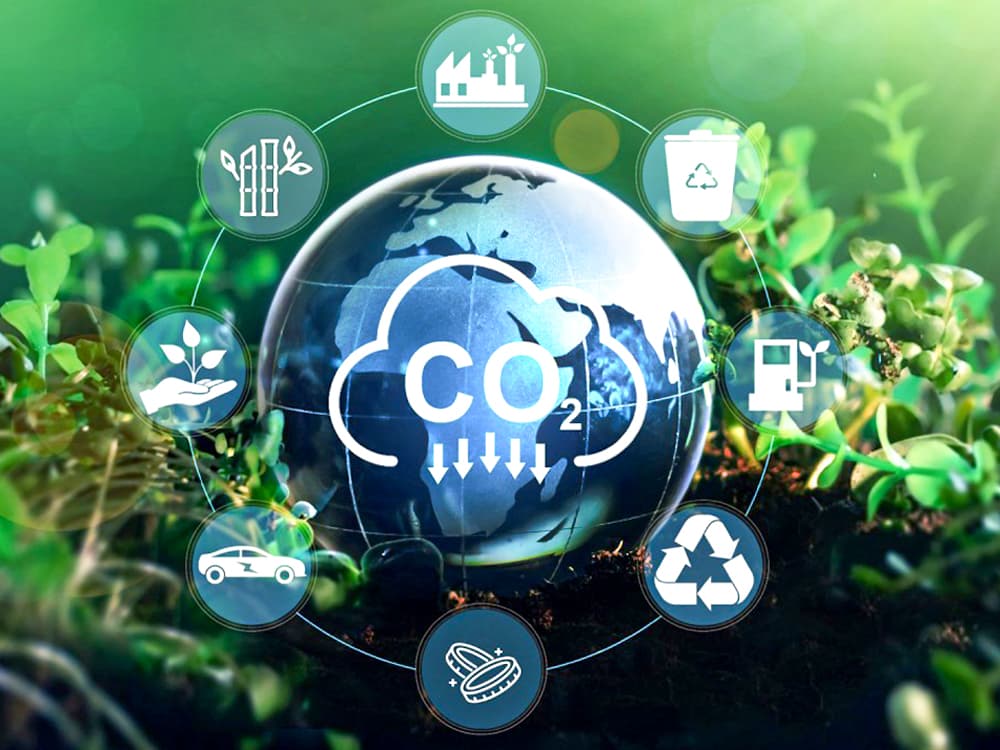
Low-Carbon Manufacturing and Cost Optimization
Implementing lean production, increasing energy efficiency by 10%.
Optimizing material procurement and machining, reducing manufacturing costs by an average of 15%.
Reducing material waste by 30% in production, supporting sustainability goals.
Materials for CNC automobile parts
Application Area | Application Parts | Materials | |||||||
---|---|---|---|---|---|---|---|---|---|
Solar Energy | Photovoltaic module frames and brackets | Aluminum, Steel | |||||||
Solar Energy | Heat dissipation and cooling components | Aluminum | |||||||
Solar Energy | Connector terminals | Brass, Aluminum | |||||||
Wind Energy | Wind turbine main shaft and gearbox fasteners | High-strength Steel | |||||||
Wind Energy | Blade molds | Steel, Composite Materials | |||||||
Wind Energy | Wind turbine high-voltage parts, battery connectors | Titanium Alloy | |||||||
Electric Vehicles | Motor brackets, rotors, stators, and base plates | Aluminum, Steel | |||||||
Electric Vehicles | Cooling system components | Aluminum | |||||||
Electric Vehicles | Charging pile and charging plug | Plastic | |||||||
Electric Vehicles | Motor connection components, connectors | Titanium Alloy | |||||||
Battery Technology | Battery terminals, connector lugs and bus bars | Copper, Aluminum | |||||||
Battery Technology | Battery module frames | Aluminum, Stainless Steel |
CNC Automotive Parts Surface Finishing Capabilities
Surface Treatment | Feature | Application Parts | ||||||||||||
---|---|---|---|---|---|---|---|---|---|---|---|---|---|---|
Electroplating | Corrosion resistance, electrical conductivity, aesthetics | Battery connectors, conductive rails, fasteners | ||||||||||||
Anodizing | Hardness, wear, corrosion resistance, color aesthetics | attery cases, solar frames, wind turbine parts | ||||||||||||
Powder Coating | Corrosion resistance, wear resistance, eco-friendly | Electric vehicle exterior parts, wind turbine blades, brackets | ||||||||||||
Heat Treatment | Enhances hardness, strength, and wear resistance | Wind turbine gearbox housing, electric vehicle base parts | ||||||||||||
Sand blasting | Cleans the surface, enhances adhesion, aesthetics | Solar brackets, wind turbine pipes, heat sinks | ||||||||||||
Electrophoretic | Uniform coating, corrosion resistance, aesthetics | Electric vehicle body parts, solar frames, turbine components |
CNC New Energy Parts Case Study
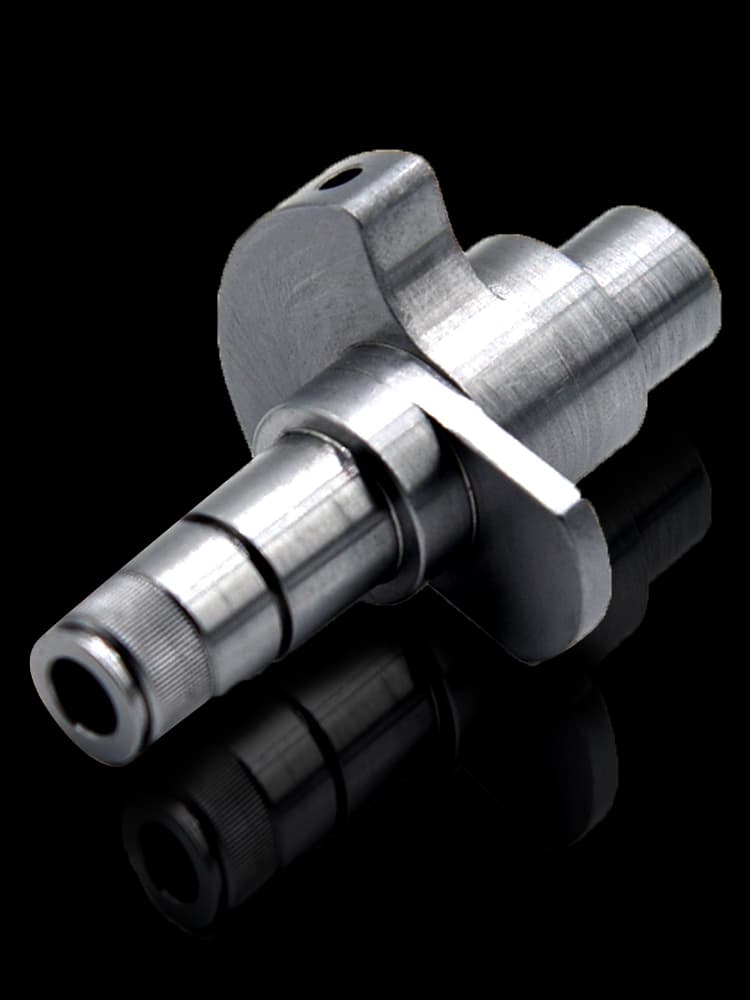
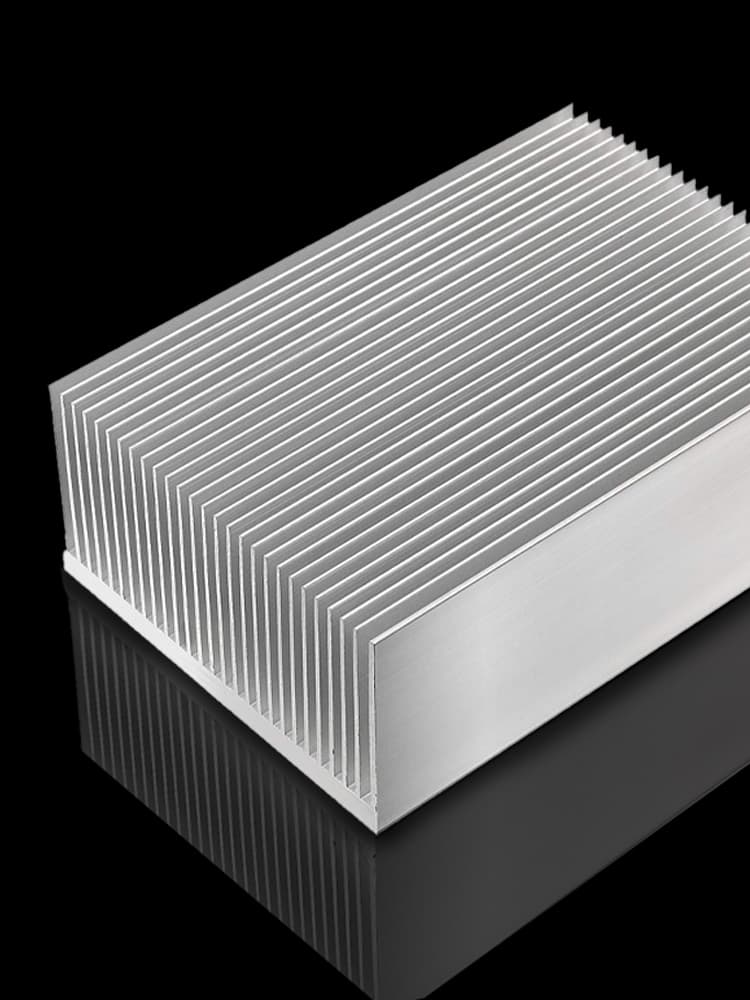
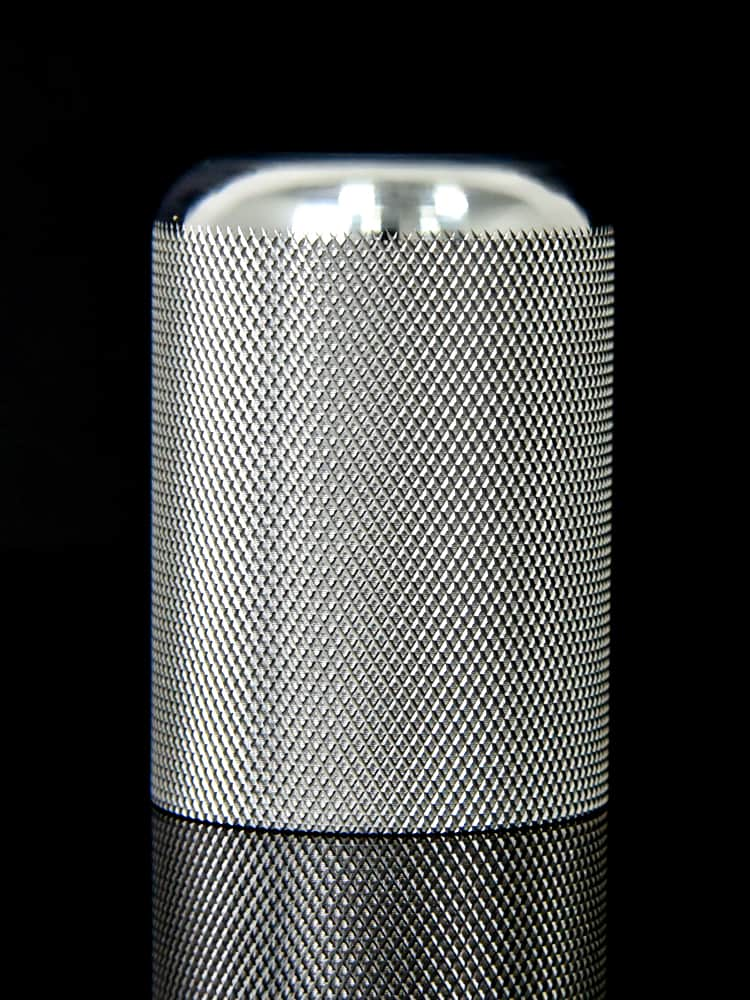

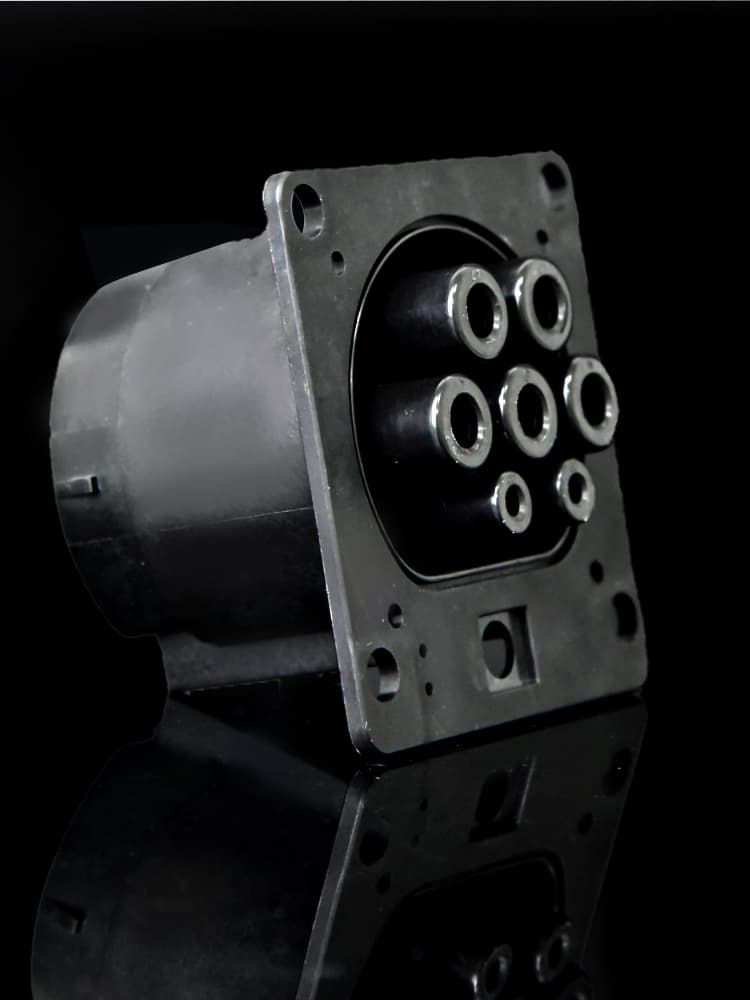
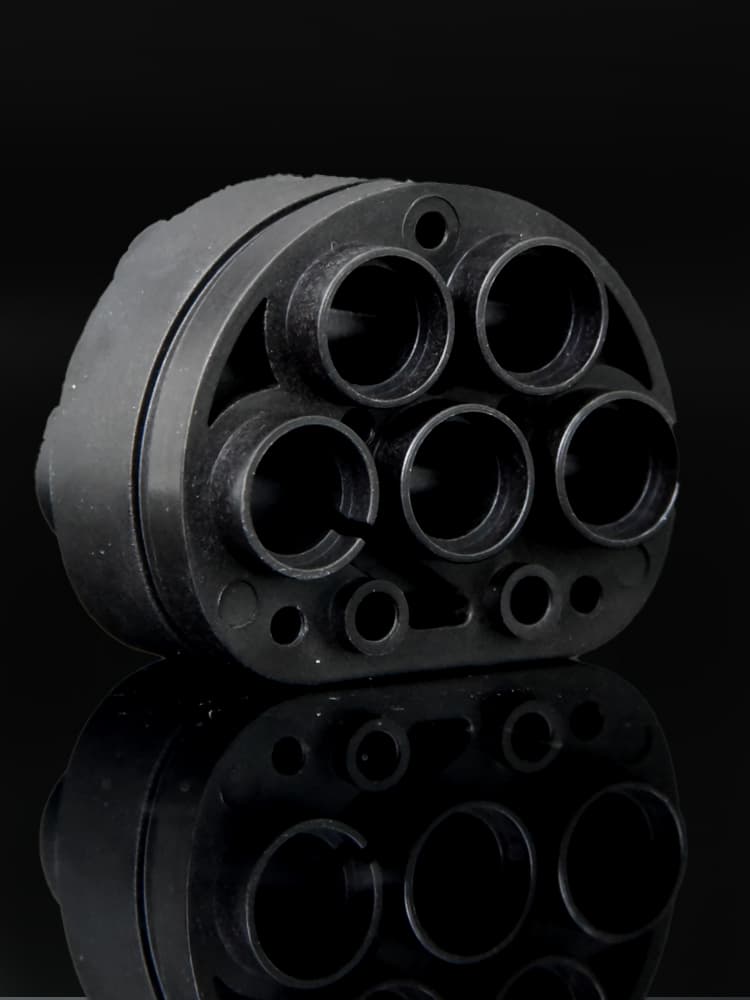
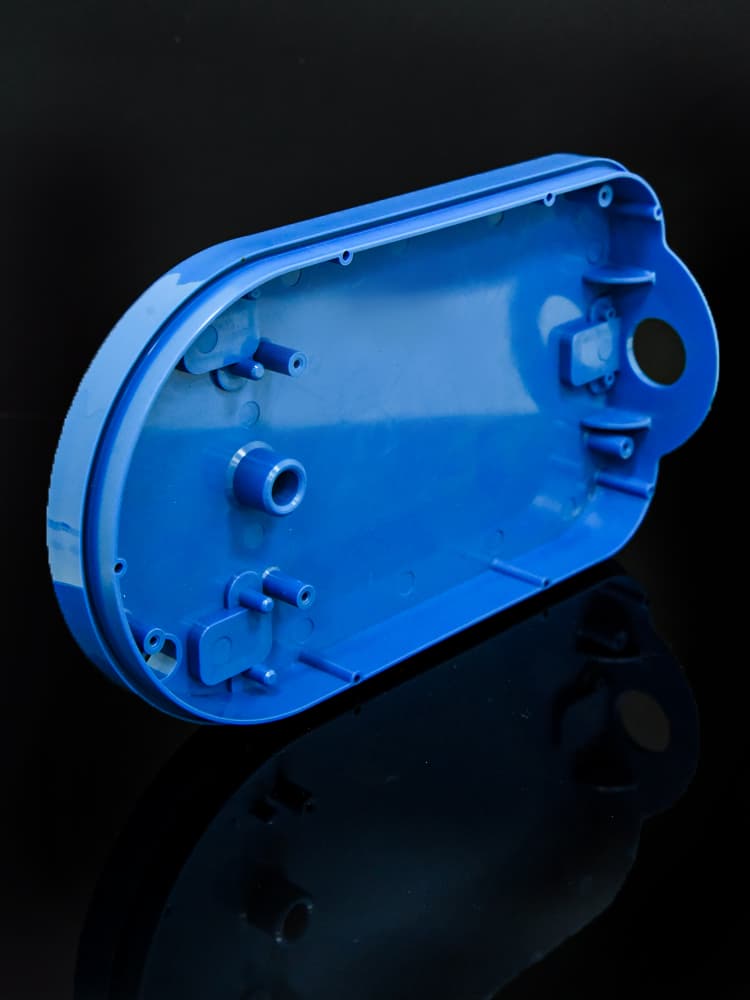
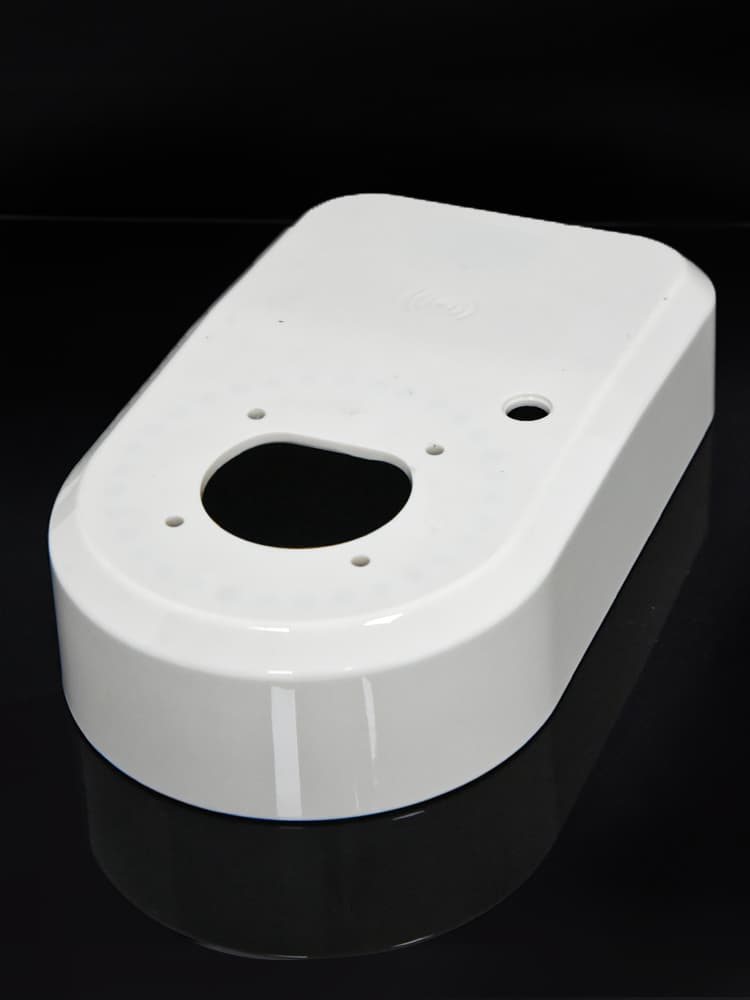
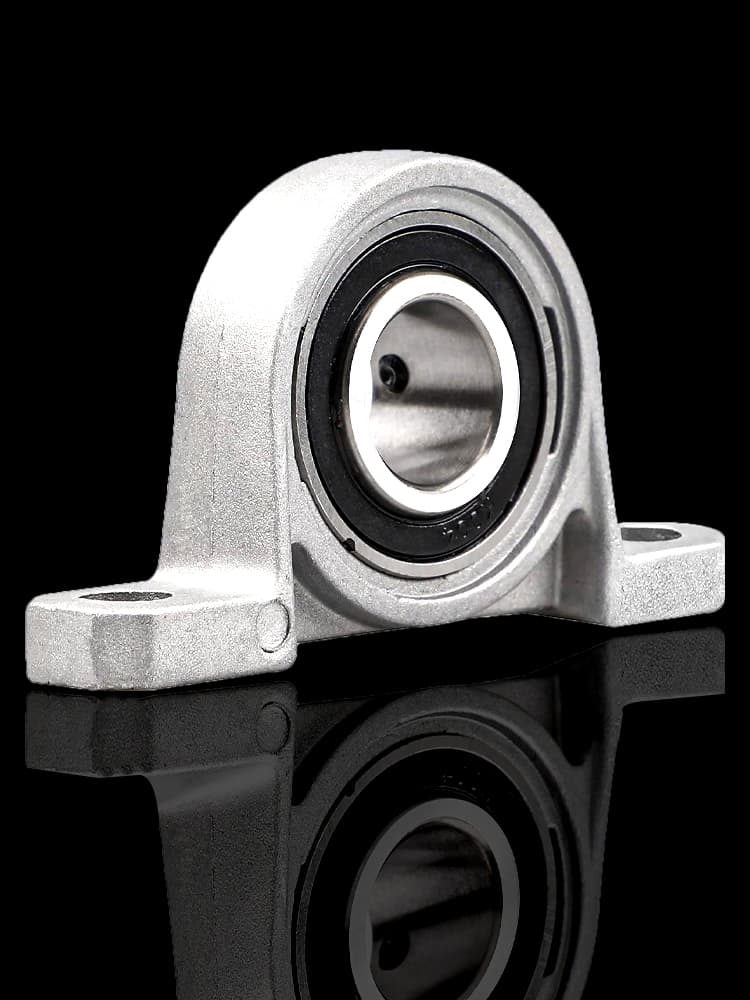
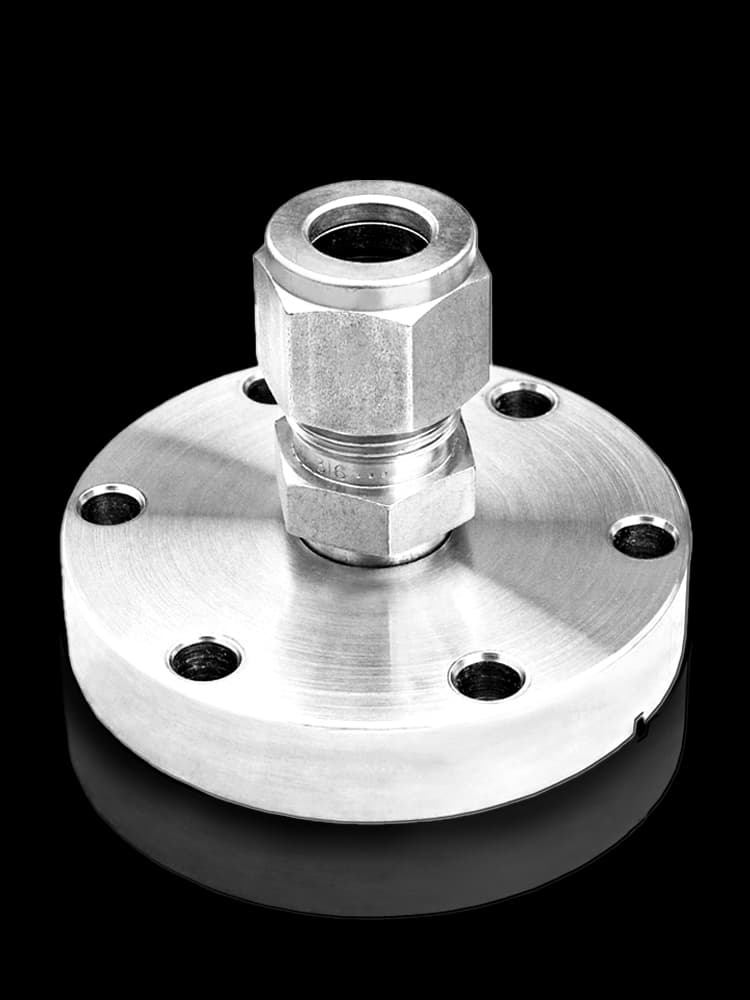
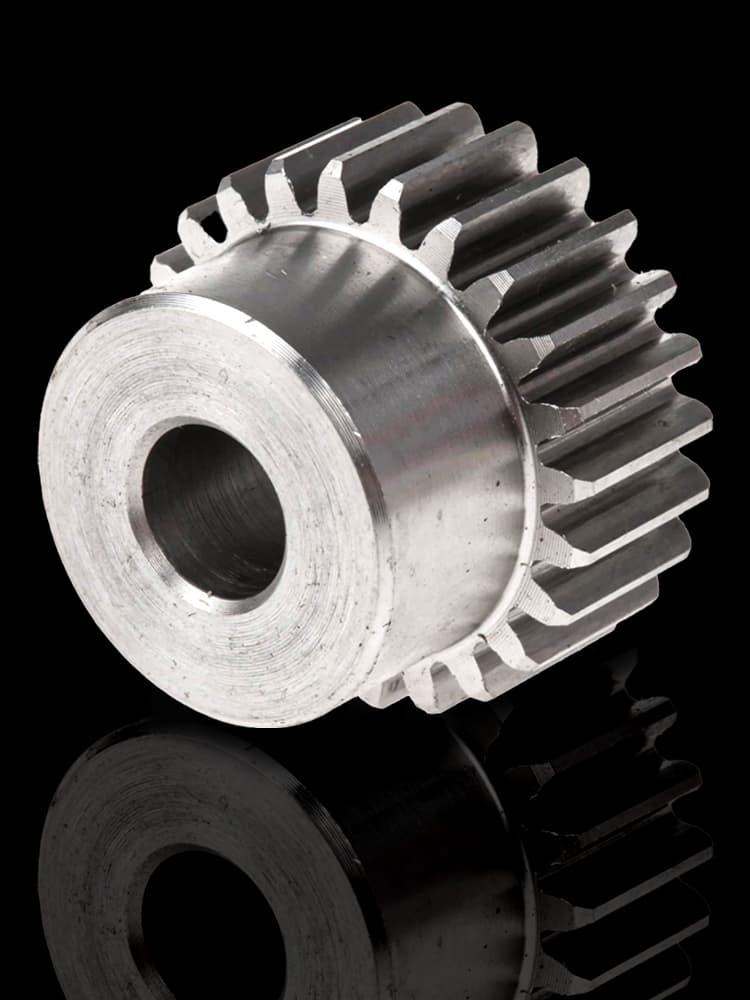
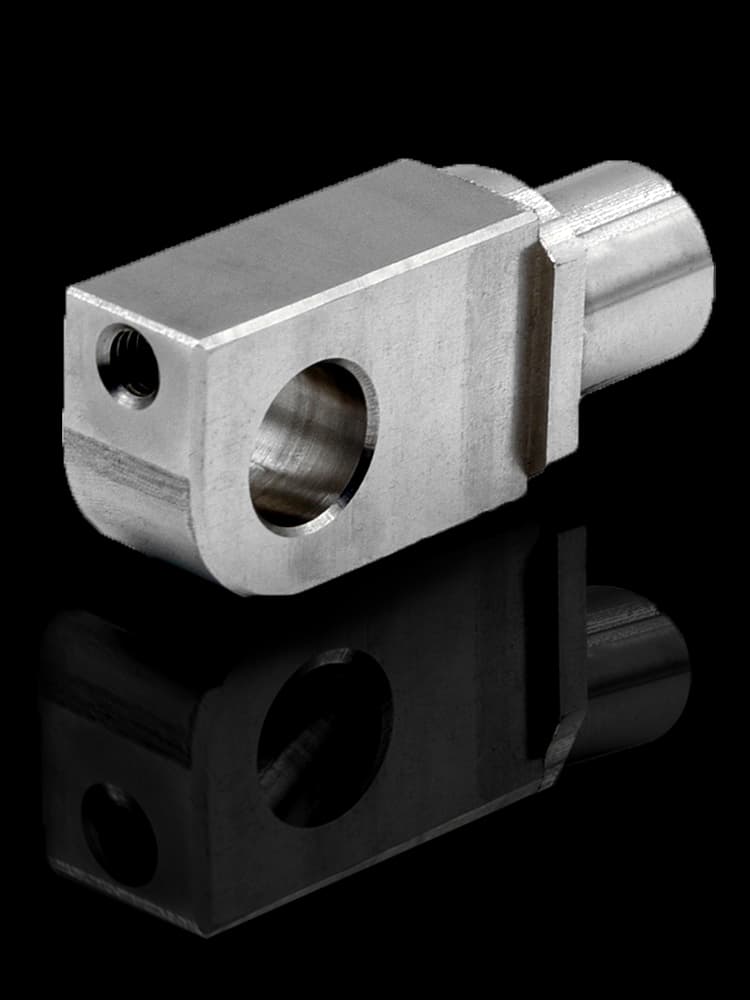
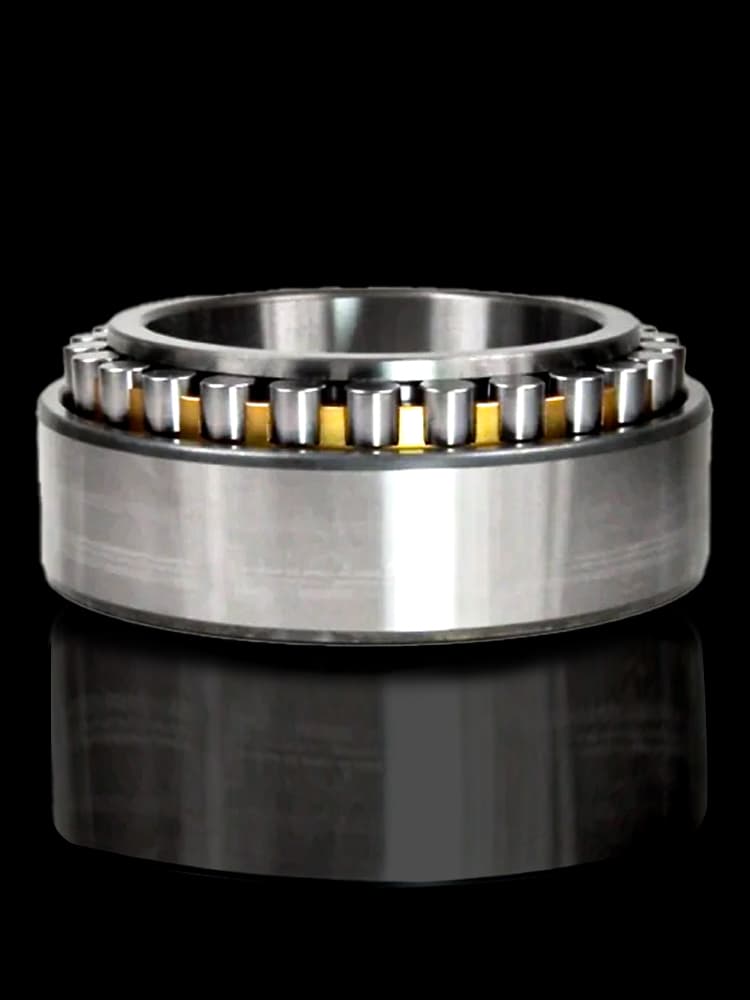
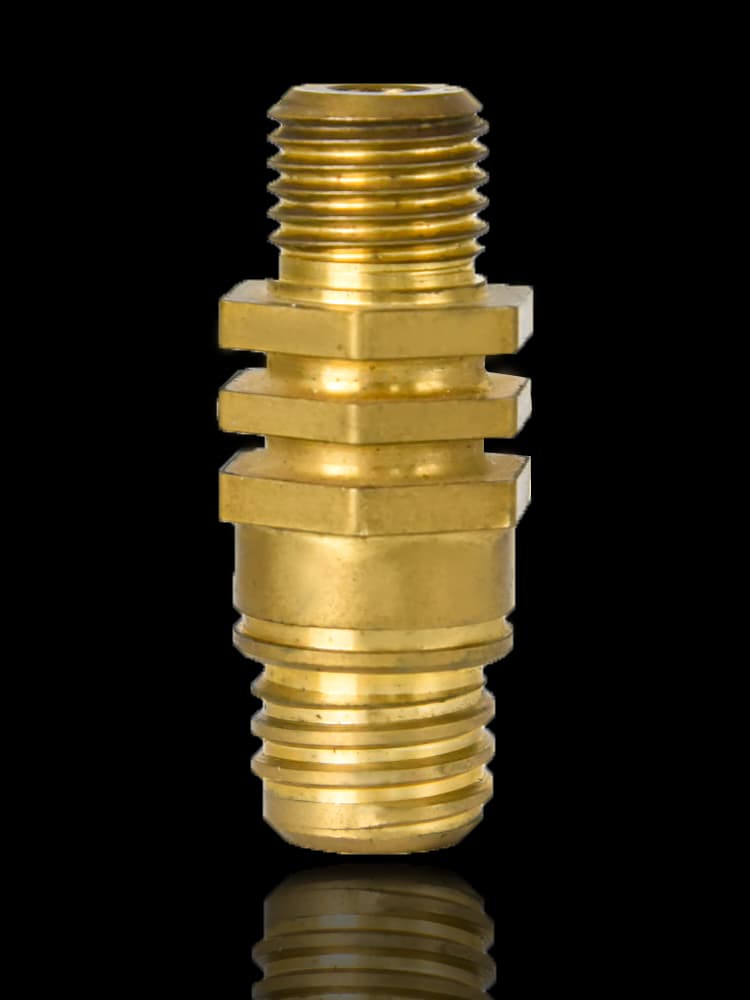
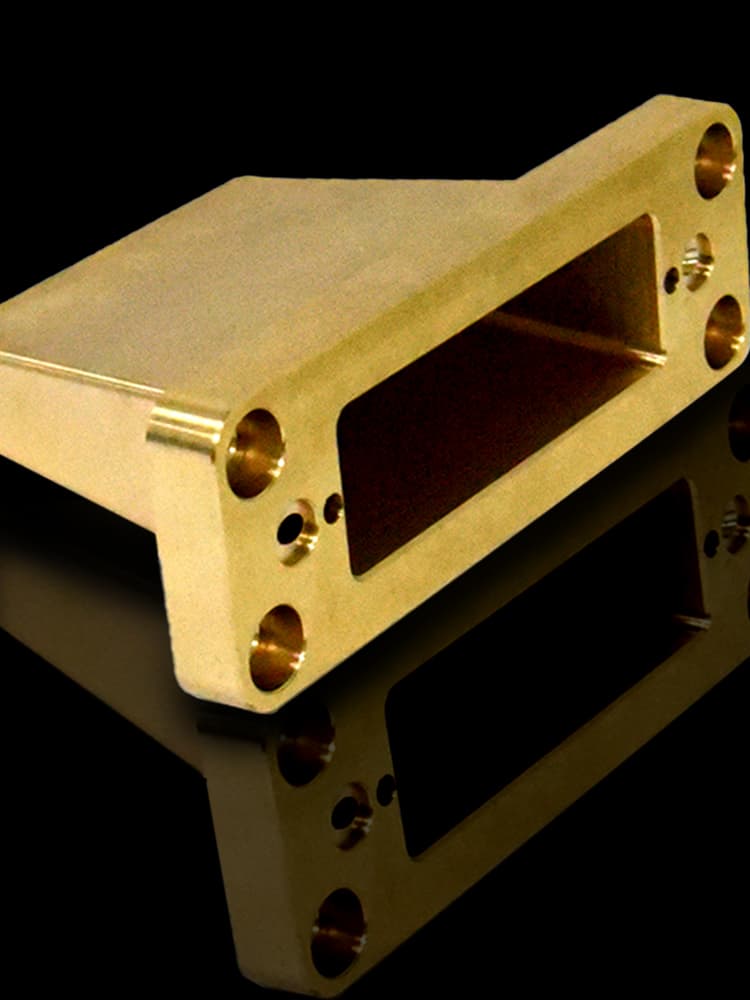
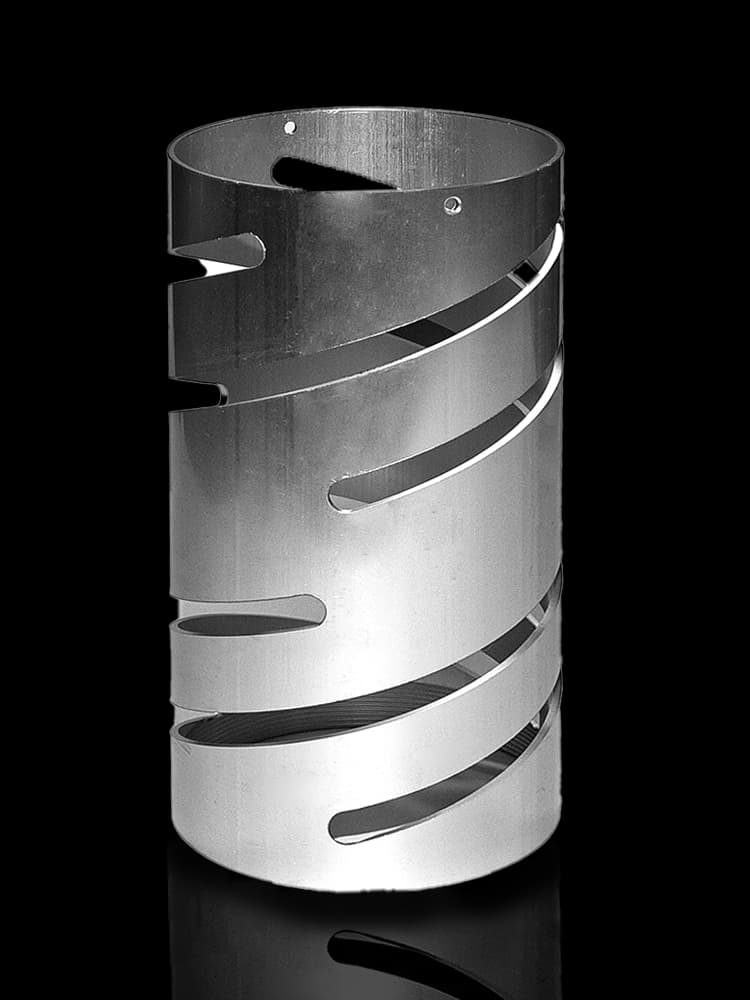
Our Partners
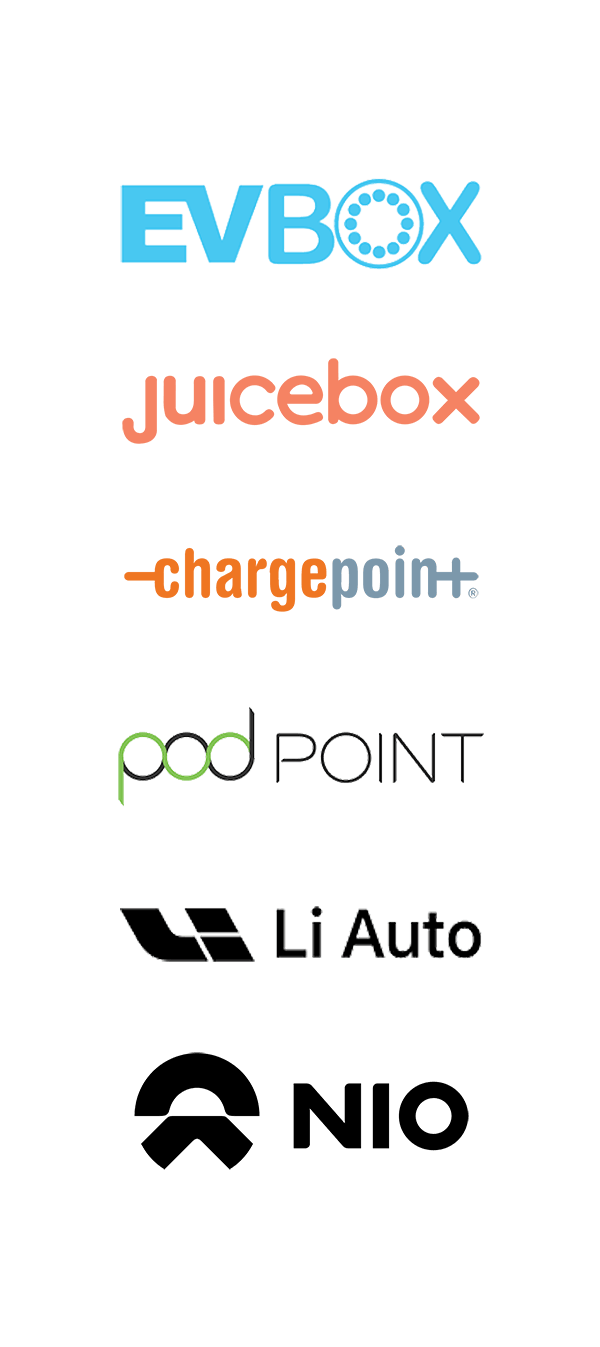
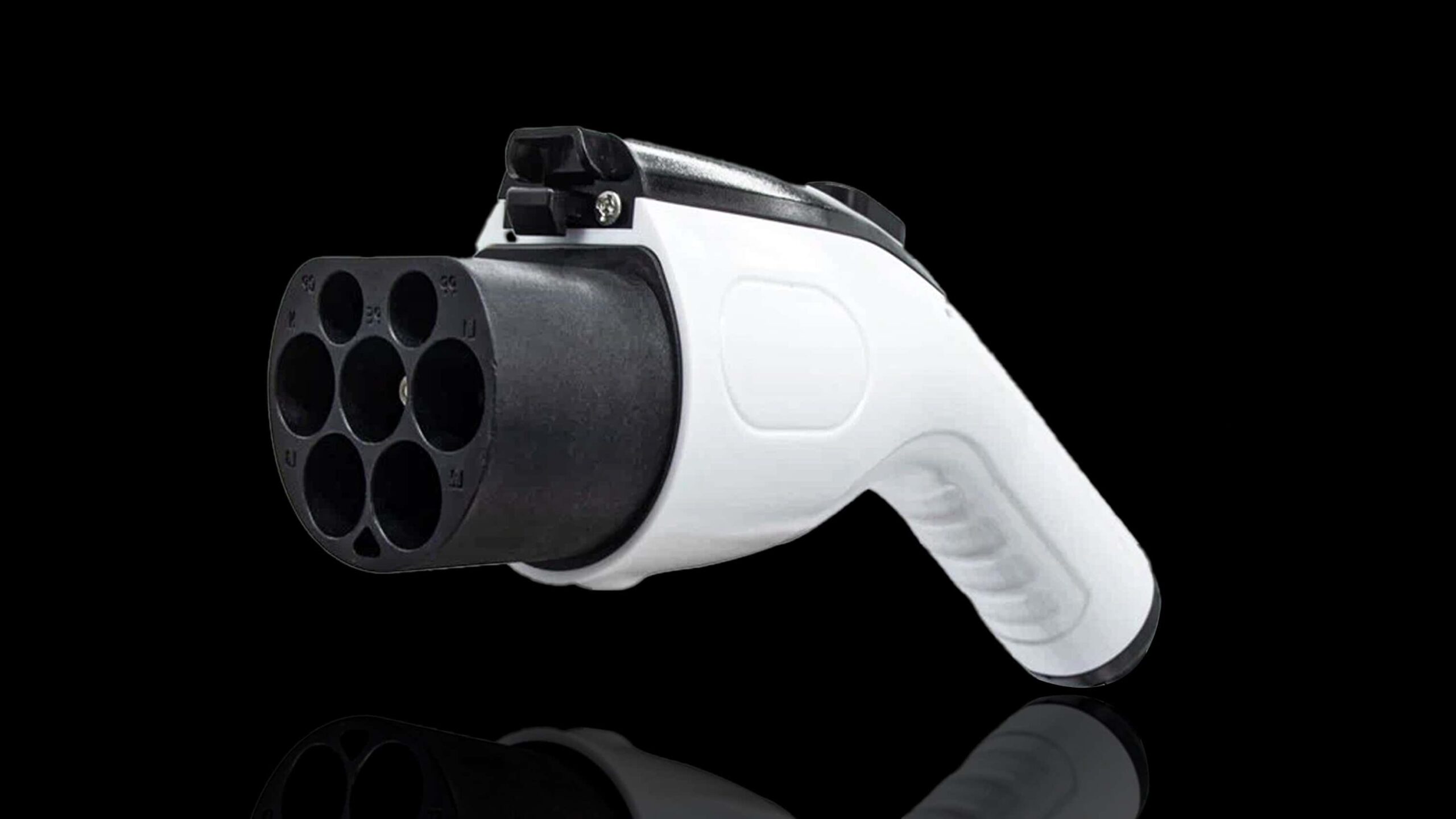
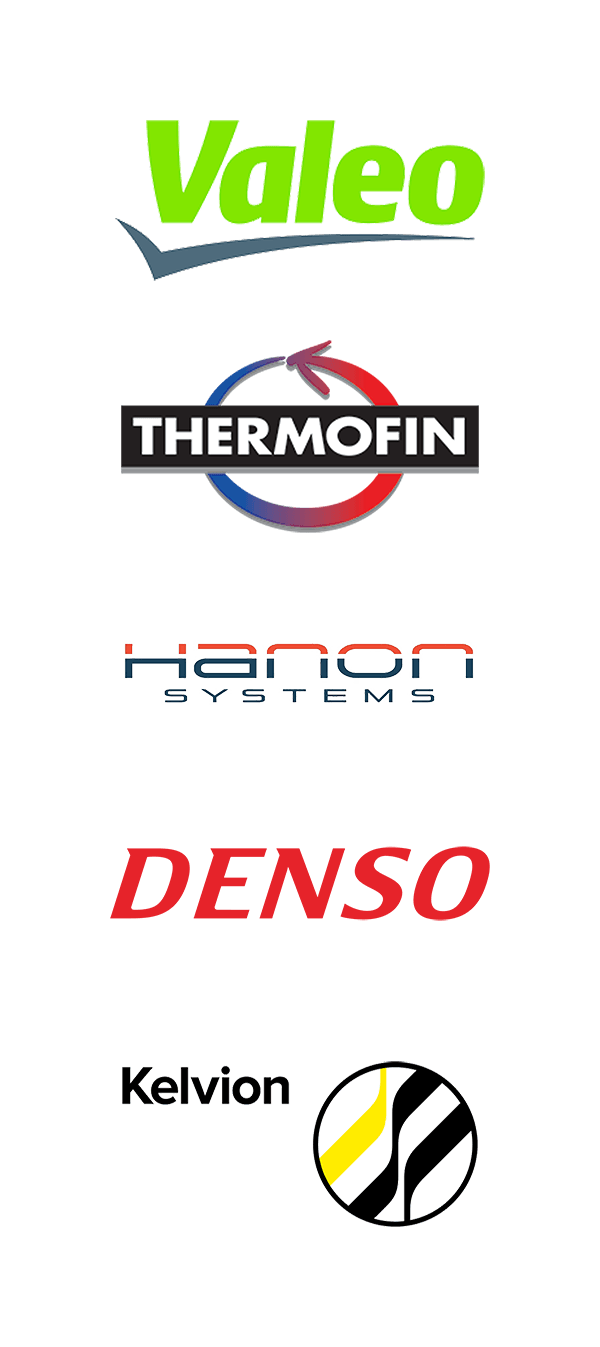
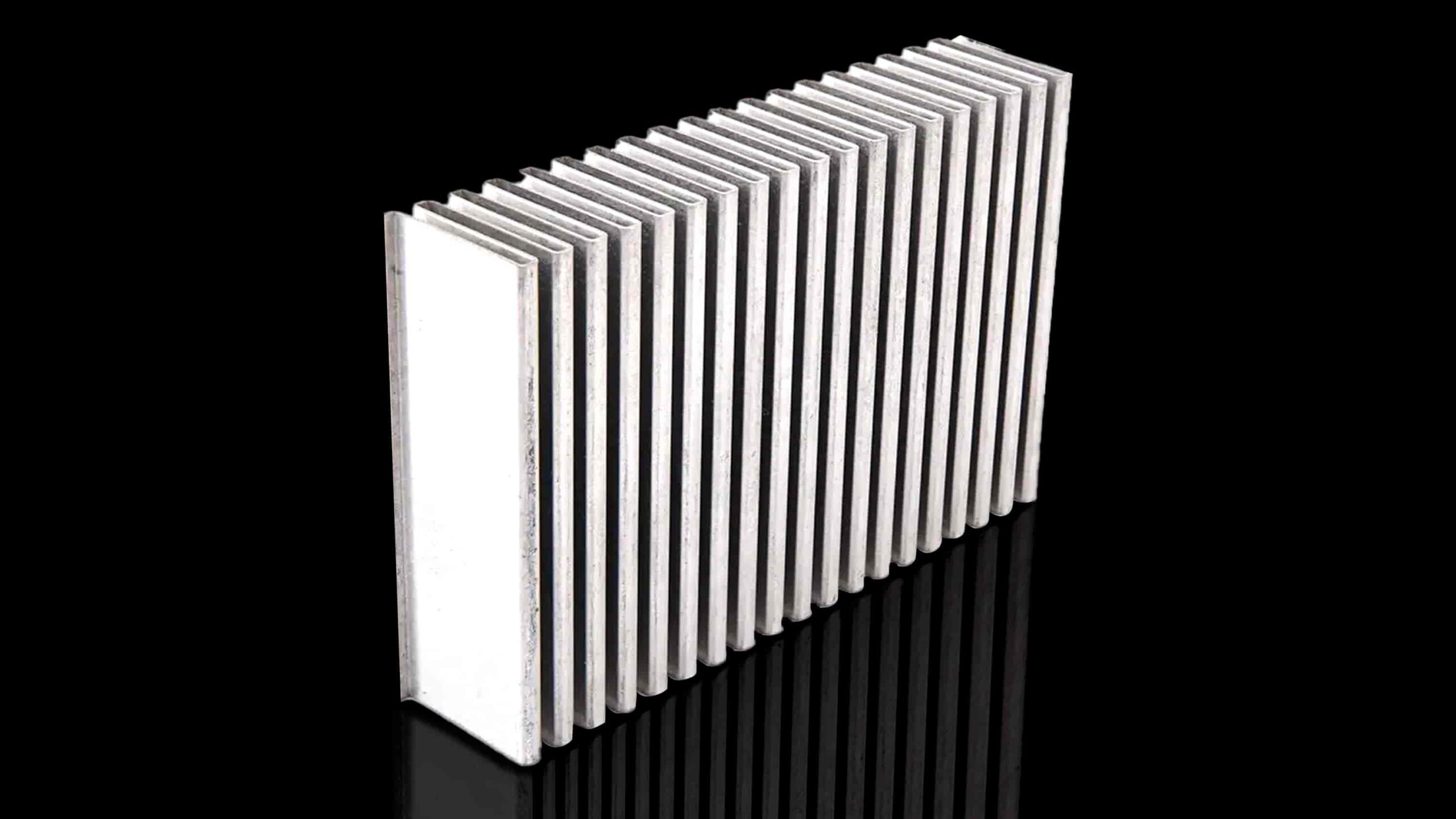
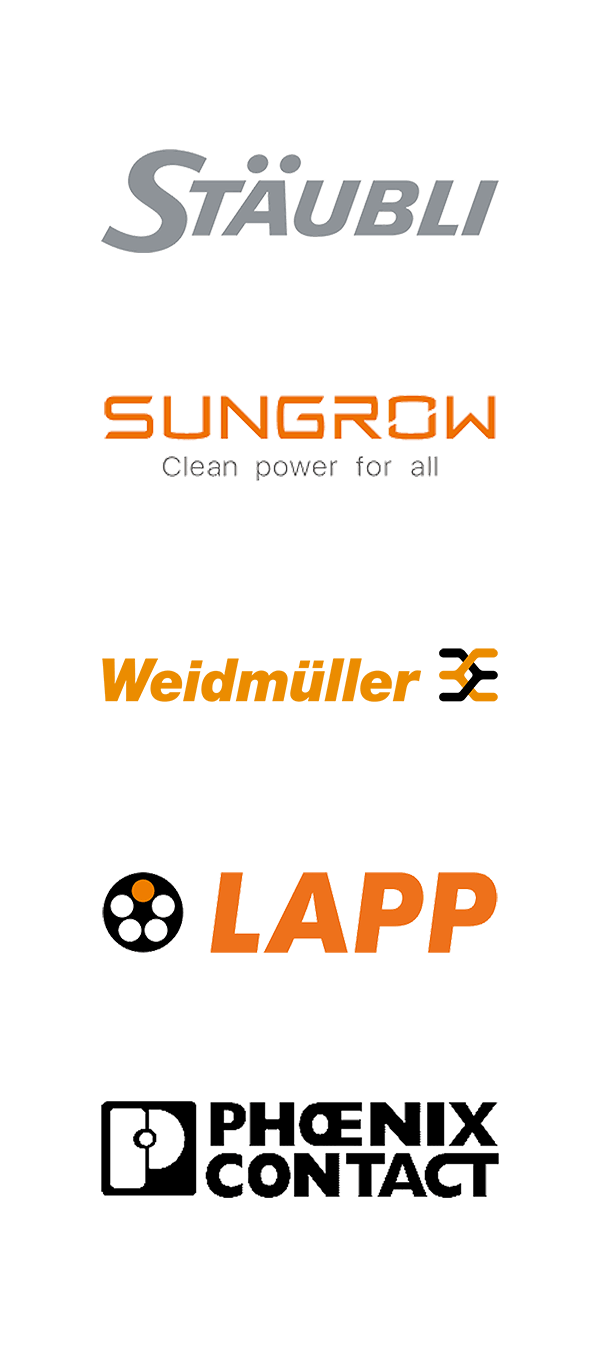
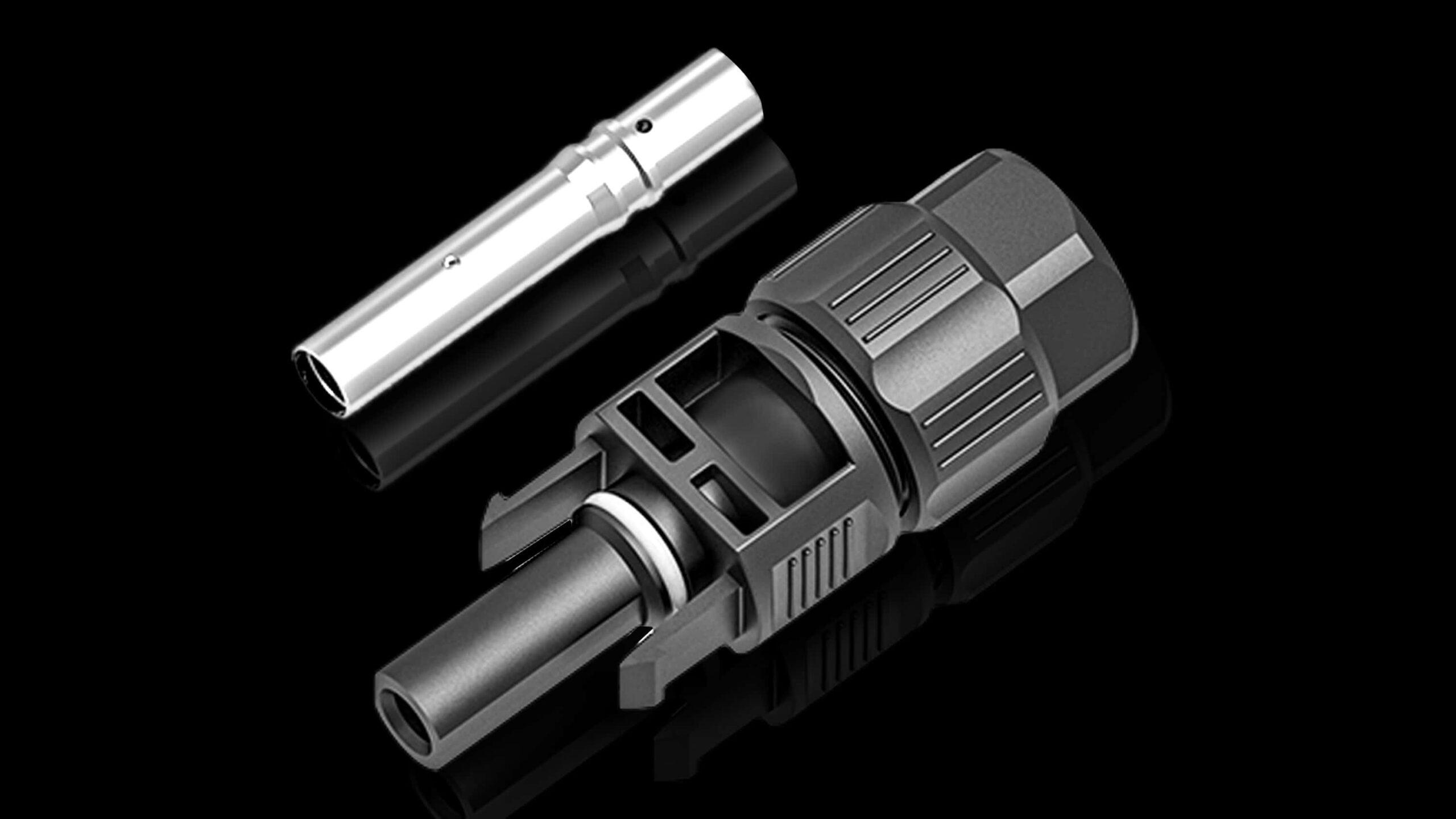
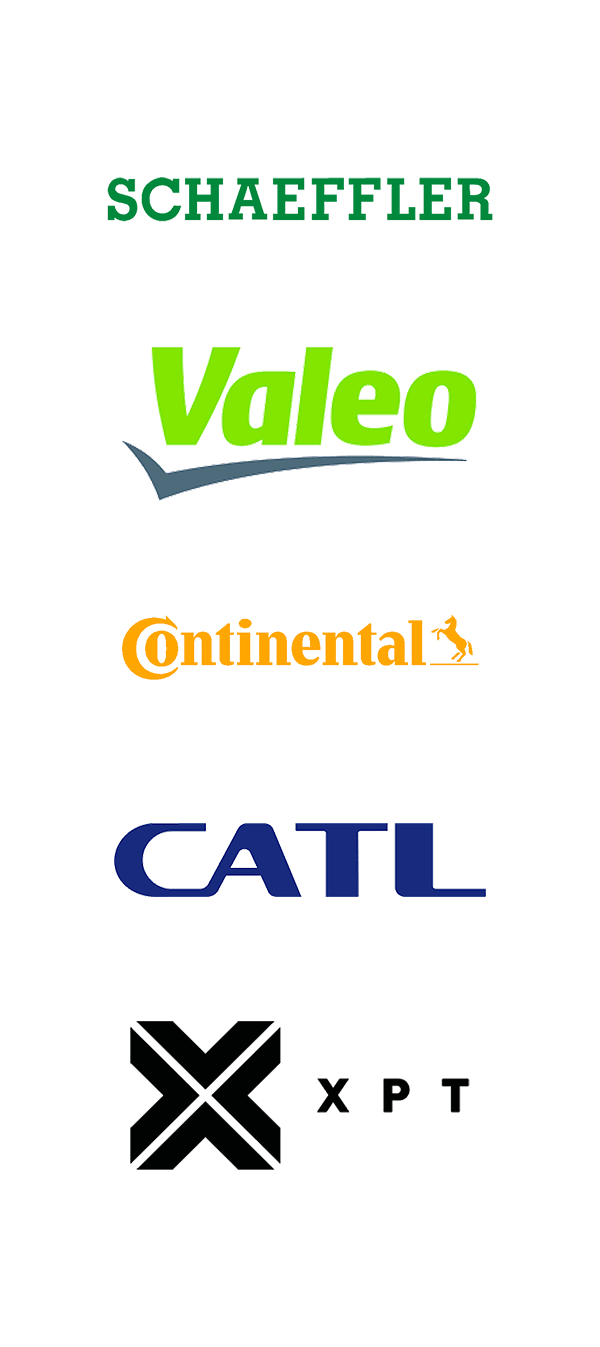
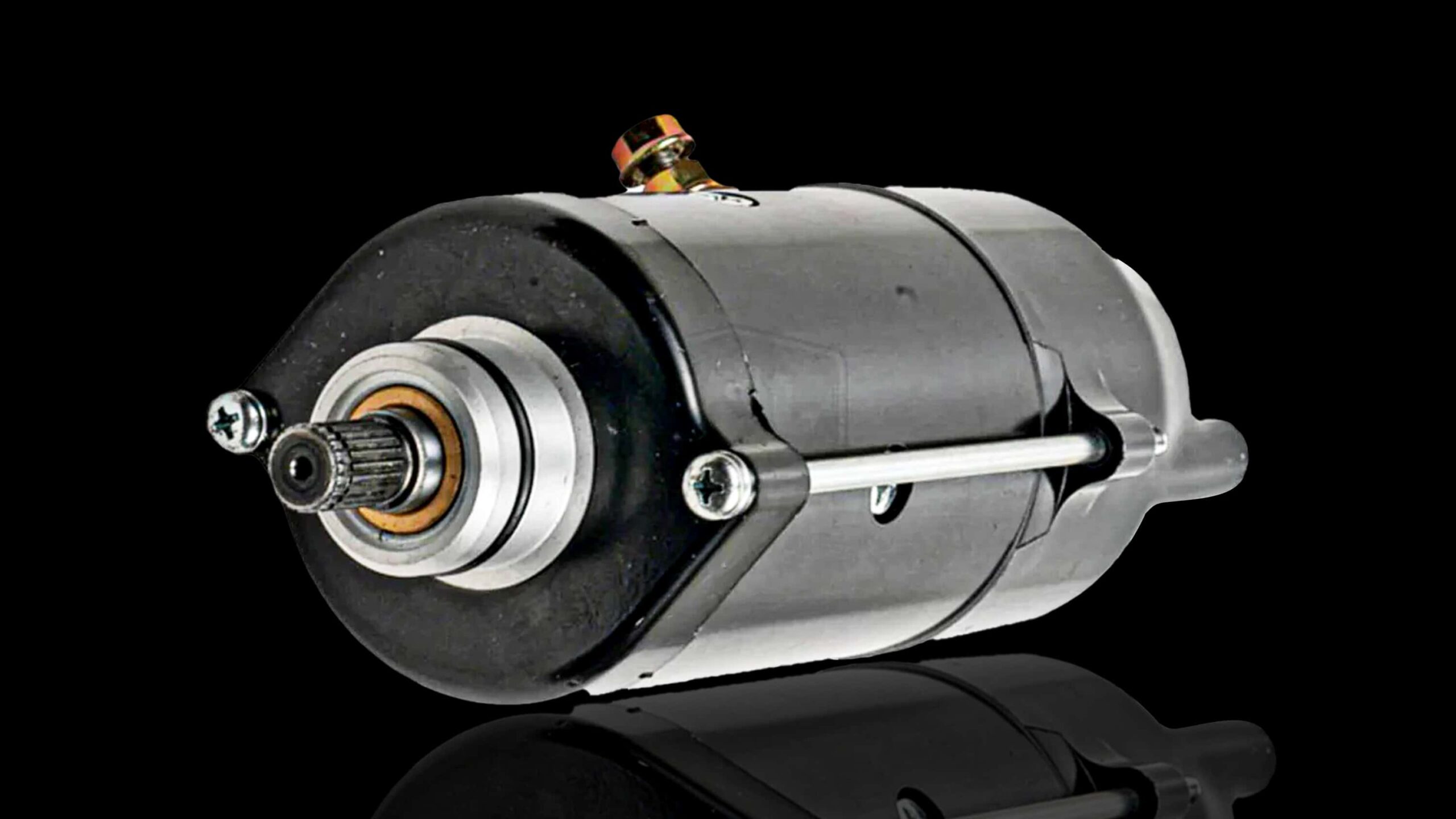
New Energy Parts Engineer Julia from Xielifeng Has Something to Say
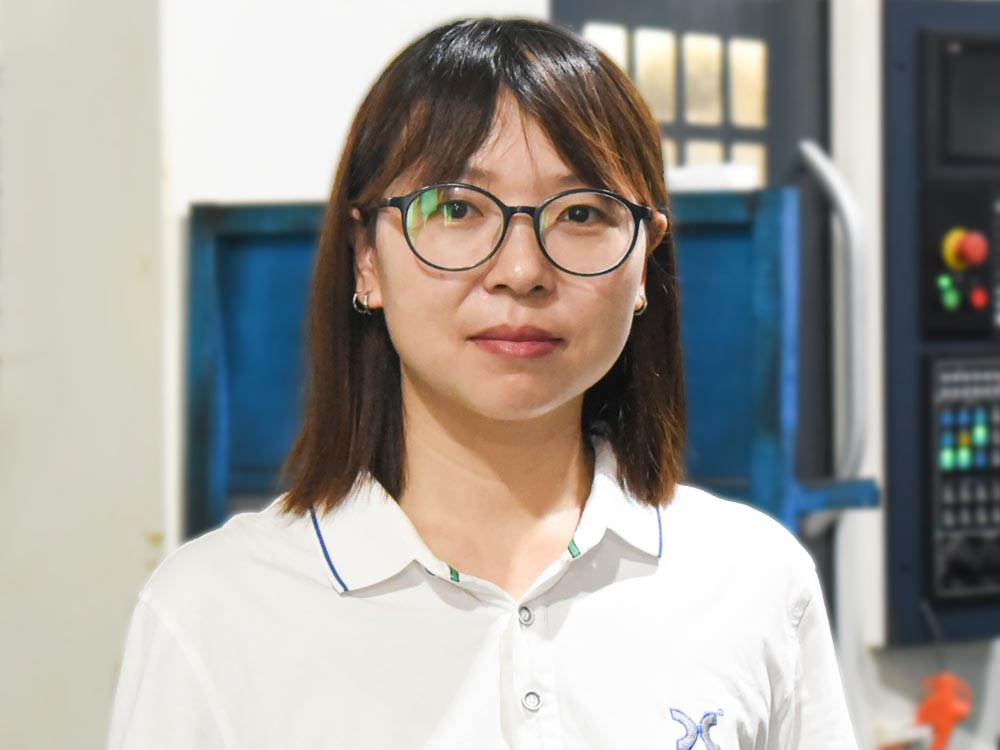
Senior Engineer Julia, 11 years of experience in machining components for new energy applications, such as electric vehicle (EV) batteries, solar energy systems, and wind turbines. Specialized in material processing technologies for efficient energy transfer and sustainable production.
How do you ensure the reliability and durability of new energy components?
We focus on using high-quality materials such as stainless steel, aluminum alloys, and advanced composites. Each part undergoes multiple testing stages, including fatigue tests, thermal cycling, and corrosion resistance evaluations, to ensure it can withstand harsh operating environments. Additionally, we apply protective coatings where necessary to further enhance durability.
How do you address heat management challenges in EV battery components?
We design cooling plates and heat sinks using high thermal conductivity materials such as copper and aluminum. These parts are precisely machined to ensure tight contact with battery cells for effective heat dissipation. Additionally, we apply anodizing and thermal coatings to enhance thermal performance.
What machining challenges do wind energy components present?
Wind turbine components, such as gearboxes and shafts, require high precision and durability to withstand continuous operation. Due to the large size of some parts, 5-axis machining and large-part machining techniques are essential. We also apply anti-corrosion treatments to ensure longevity in outdoor environments.
How do you ensure the precision of parts used in solar energy systems?
Solar energy systems require precisely aligned frames and mounting structures for efficient energy capture. We use coordinate measuring machines (CMMs) to ensure accurate dimensions. Additionally, we provide custom machining for components like tracking systems that need tight tolerances for optimal solar panel positioning.
How do you manage quality control in new energy component production?
We follow strict ISO 9001 standards throughout production and use in-line inspections to monitor quality in real-time. For critical parts, we conduct thermal and corrosion resistance testing. Our goal is to ensure that every component meets industry requirements for efficiency and reliability.
How do you meet the fast-growing demands of the new energy industry?
We maintain flexible production schedules and modular production lines to quickly adapt to changing requirements. Our rapid prototyping services allow clients to validate designs early and accelerate product development. We also keep a strategic inventory of key materials to meet urgent production needs.
How Xielifeng Works
From quotation to delivery, we provide efficient, high-quality services, making manufacturing more convenient.
01
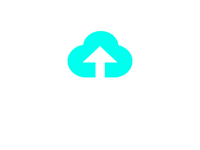
Upload drawing
CAD files: 2D: DXF | DWG | PDF 3D: STP | STEP |IGS | IGES| X_T | SLDPRT
02
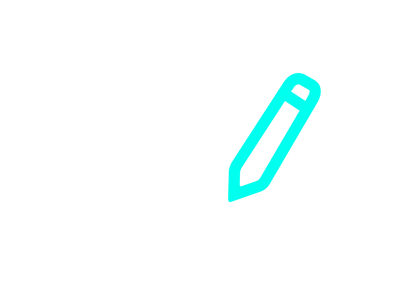
DFM Evaluation & Quote
- Drawing review
- Process analysis
- Material inspection
- Feasibility proposal
- Cost estimation
03

Order Confirmtion & Production
- Sample processing
- Sample quality inspection
- Customer confirmation
- Mass production plan
04
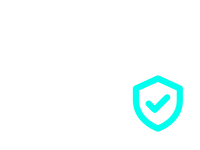
Quality Inspection & Delivery
- Raw material inspection
- First piece inspection
- Process inspection
- Final inspection
- Inspection report