Precision Machining for Custom Lighting Components
Ensuring Superior Optical Performance and Durability
All uploads are secure and confidential.* Learn More
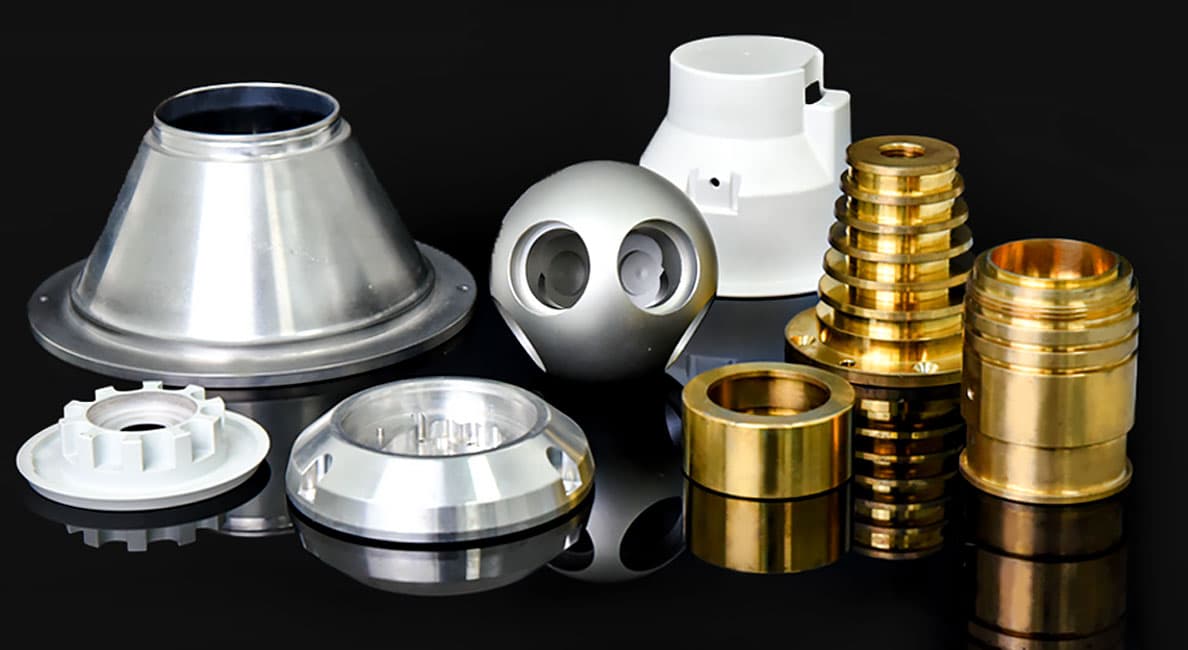
IOS 9001
IOS 14001

About Our Capabilities
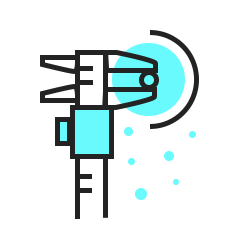
High-Precision Machining for Optical Performance

Rapid Prototyping and Flexible Production
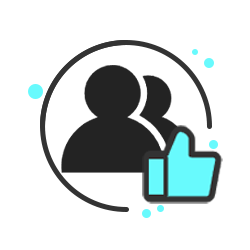
Long-Term Partnerships and Efficient Delivery
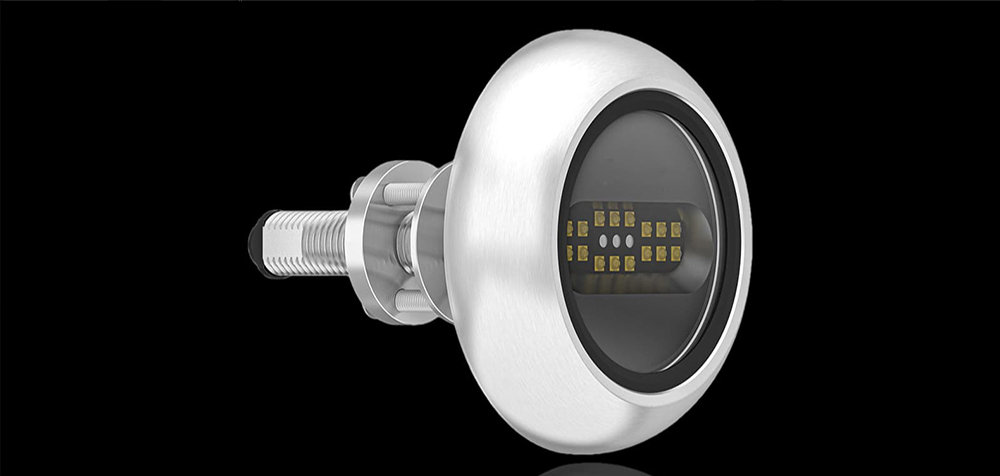
High-Precision Machining for Optical Performance
Specializing in ±0.005mm tolerance for optical lens brackets and precision connectors, with an annual output of over 100,000 pieces, ensuring stability and optical accuracy in high-end lighting equipment.
Rapid Prototyping and Flexible Production
Prototyping starts within 48 hours, and small-batch production is completed in 1 week, delivering 5,000+ custom parts annually, enabling fast market response.
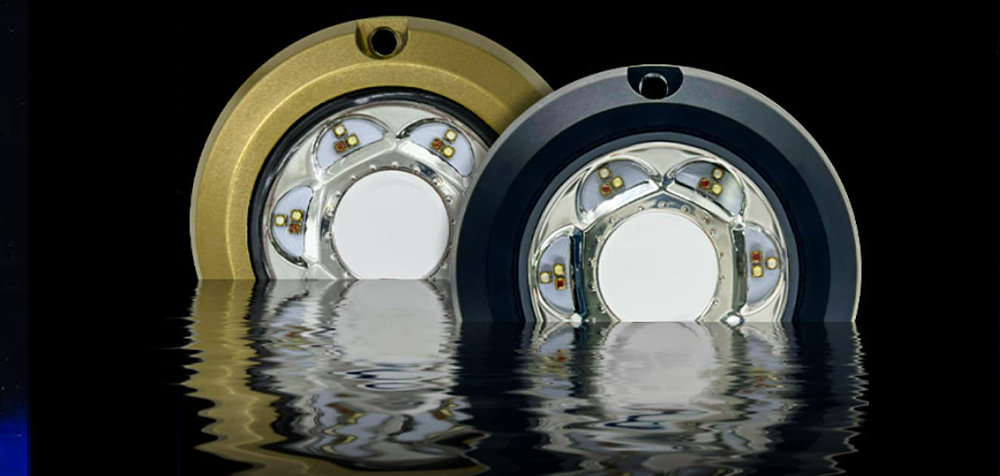
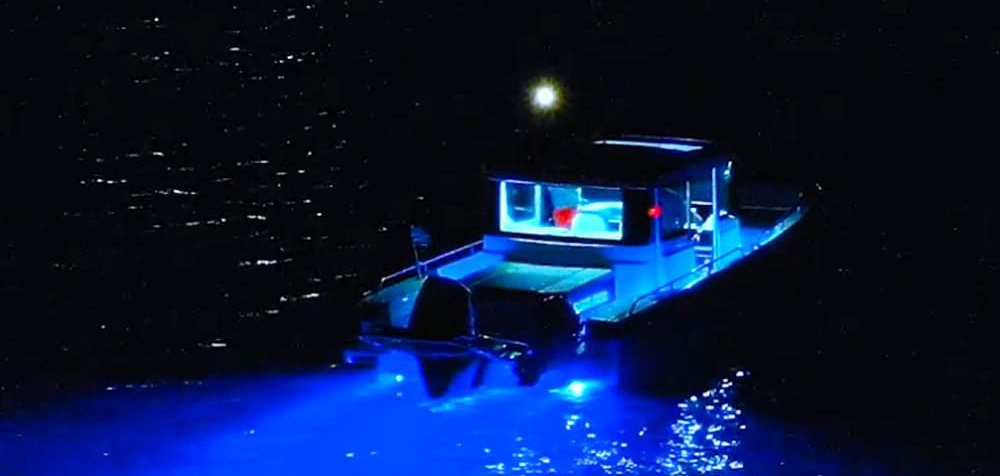
Long-Term Partnerships and Efficient Delivery
Serving 20+ lighting manufacturers, delivering over 500,000 parts annually with a 98% on-time delivery rate, enhancing customer competitiveness in the market.
CNC Machined Parts Application for Lighting
Materials | Feature | Application Parts | |||||||||||||
---|---|---|---|---|---|---|---|---|---|---|---|---|---|---|---|
Aluminum Alloy | Lightweight, strong, corrosion-resistant | Lamp housings, heat sinks, mounting brackets | |||||||||||||
Stainless Steel | Corrosion-resistant, strong, aesthetically pleasing | Brackets, decorative parts, fasteners | |||||||||||||
Steel | High strength, low cost | Mounting brackets, bases, connectors | |||||||||||||
Brass | Good machinability, high strength, aesthetically pleasing | Electrical connectors, heat conductive parts | |||||||||||||
PC (Polycarbonate) | High strength, impact-resistant, transparent | Lamp covers, reflectors, lenses | |||||||||||||
ABS | Good strength and toughness, easy to process | Lamp housings, mounting brackets, decorative parts | |||||||||||||
PMMA (Acrylic) | High transparency, good optical performance | Lenses, lamp covers | |||||||||||||
PBT | Excellent electrical insulation, heat-resistant | Lamp housings, electrical insulation parts | |||||||||||||
POM | High rigidity, high strength, low friction coefficient | Fasteners, gears, bushings |
Surface Finishing for CNC Lighting Parts
Surface Treatment | Characteristics | Electronic Components | ||||||||||||
---|---|---|---|---|---|---|---|---|---|---|---|---|---|---|
Anodizing | Enhances corrosion resistance, surface hardness, and aesthetics | Aluminum alloy lamp housings, heat sinks | ||||||||||||
Powder Coating | Improves weather resistance, corrosion resistance, and appearance | Steel housings, mounting brackets | ||||||||||||
Electroplating | Enhances aesthetics and corrosion resistance | Decorative parts, connectors | ||||||||||||
Chrome/Nickel Plating | Increases wear resistance, aesthetics, and conductivity | Aluminum decorative parts, electrical connectors | ||||||||||||
UV Coating | Improves UV resistance and surface hardness | Transparent covers, lenses | ||||||||||||
Polishing | Enhances surface gloss and aesthetics | Stainless steel and copper decorative parts, fasteners | ||||||||||||
Brushing | Improves surface texture and aesthetics | Stainless steel housings, decorative parts |
Custom Light Parts Case Study
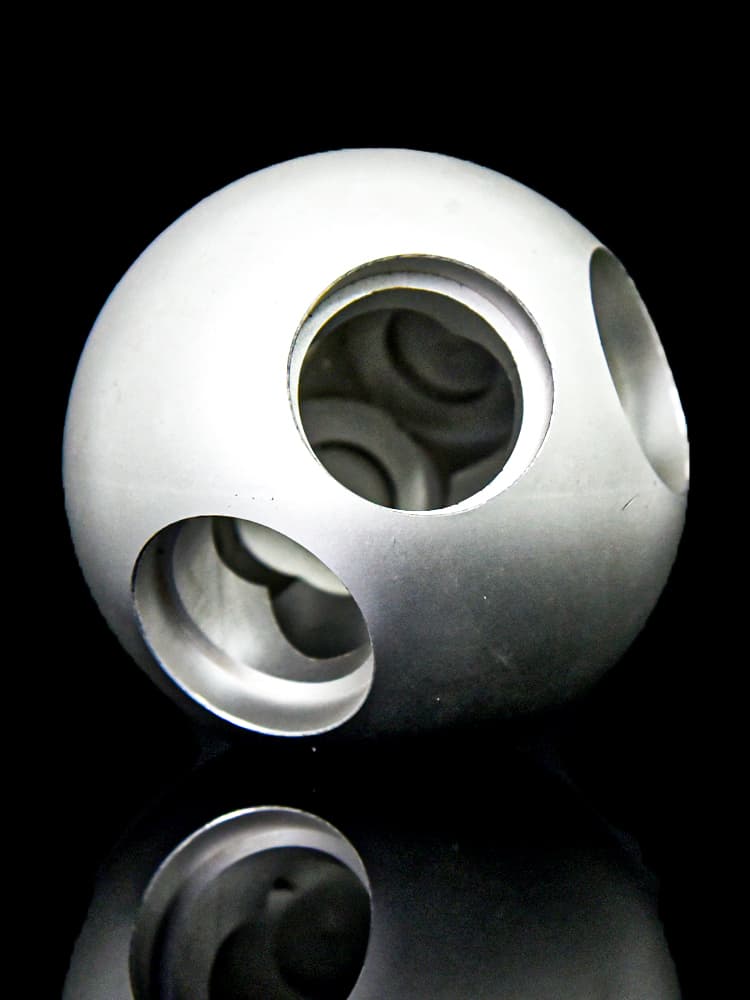
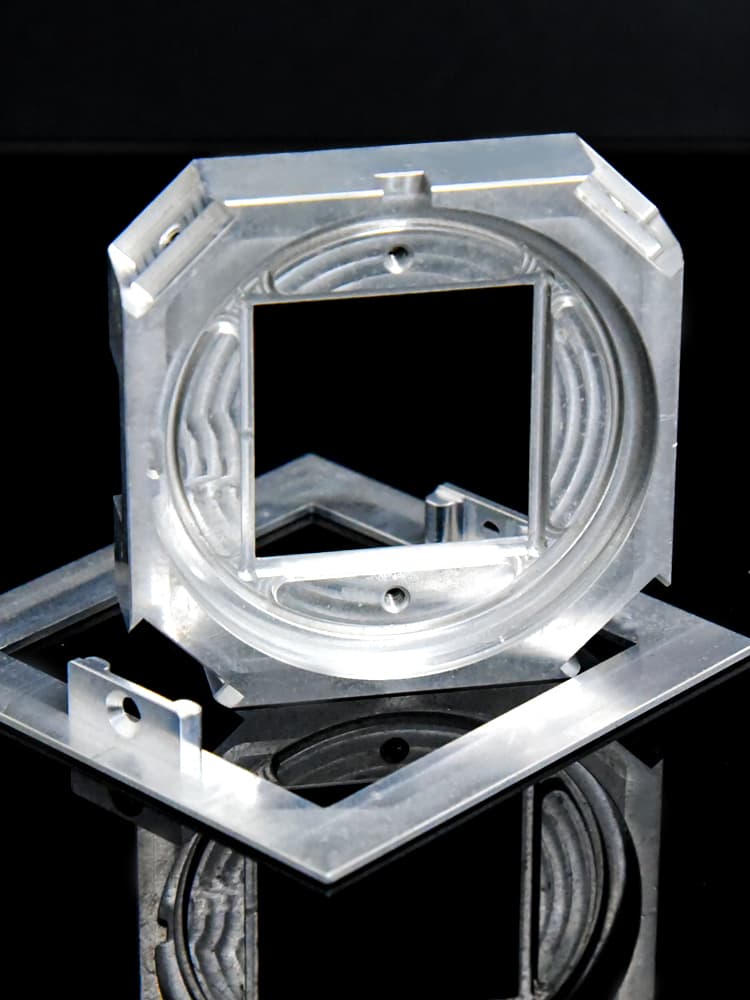
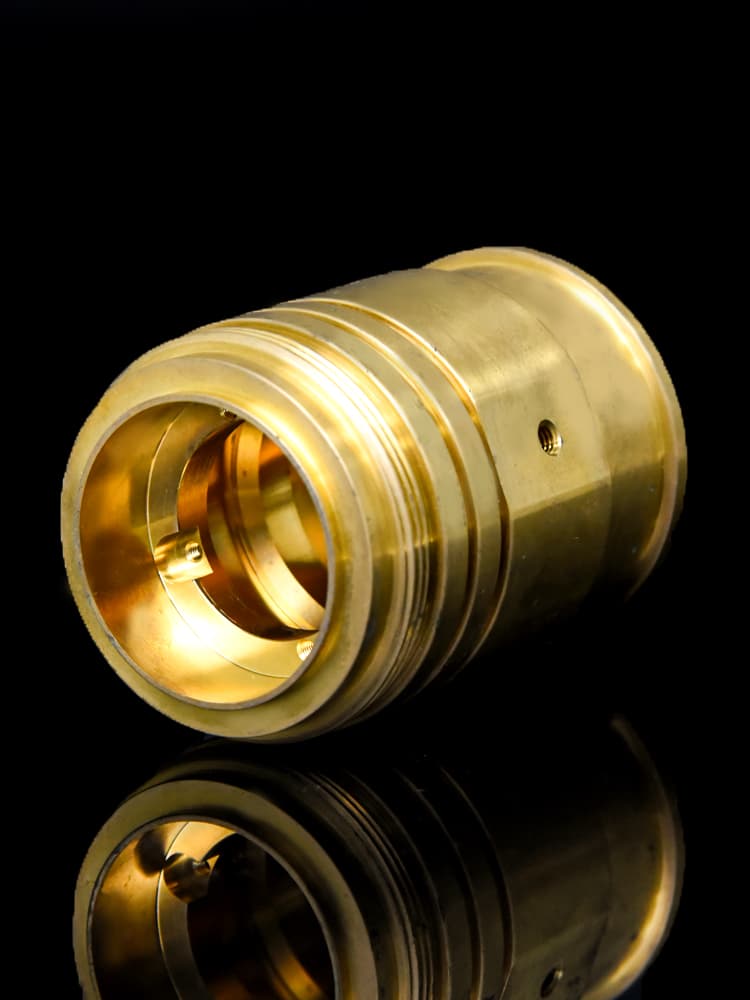
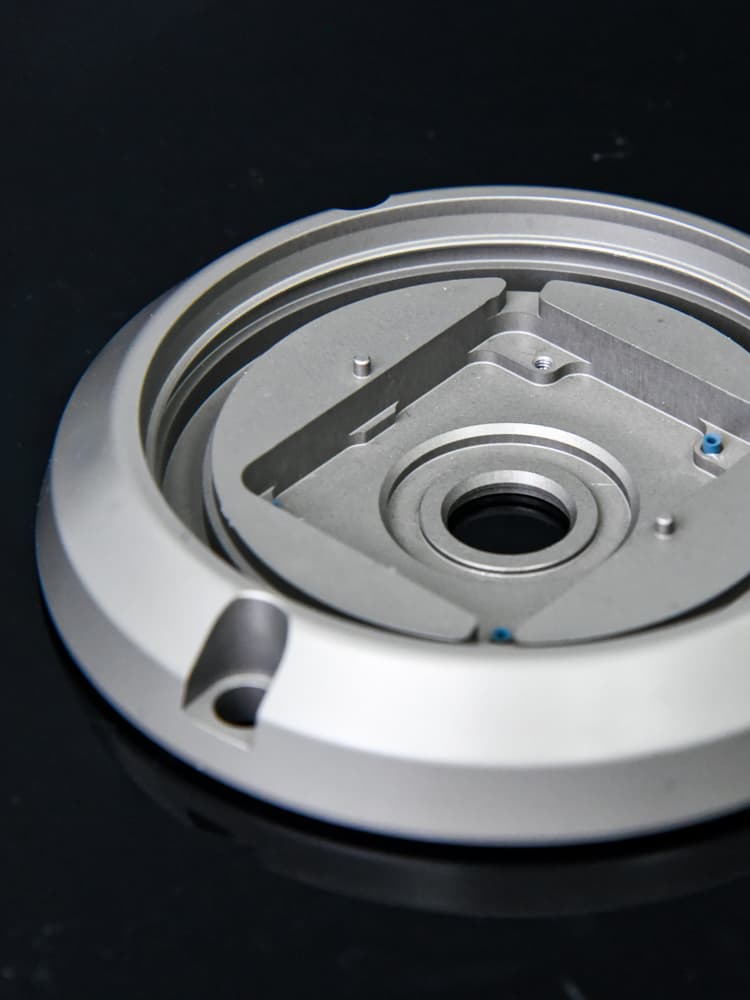
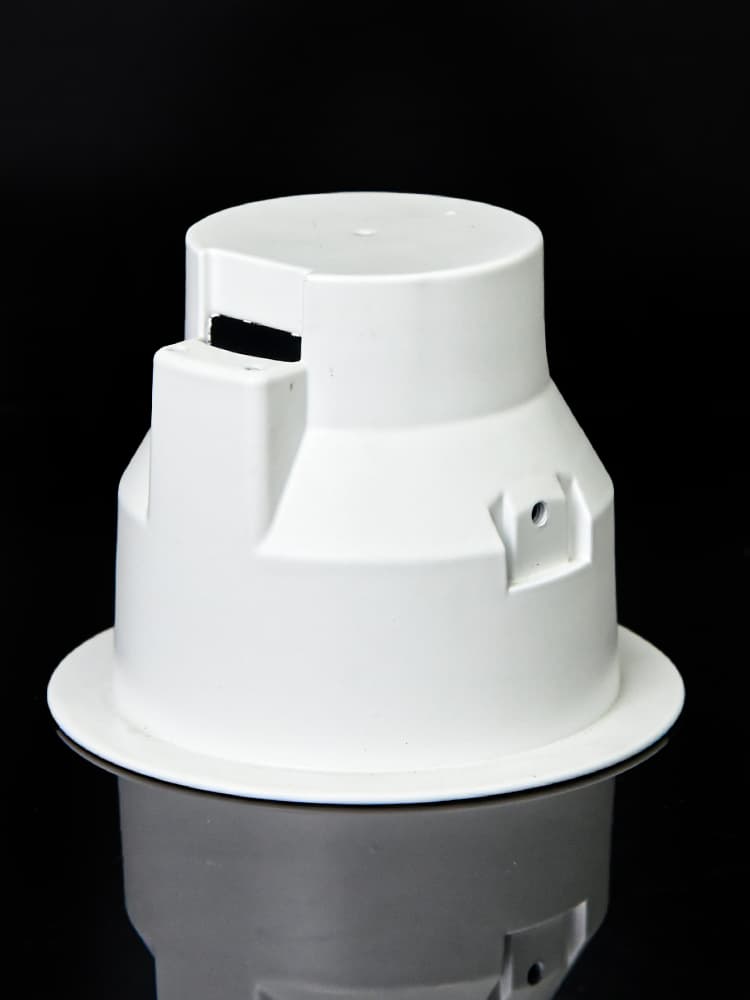
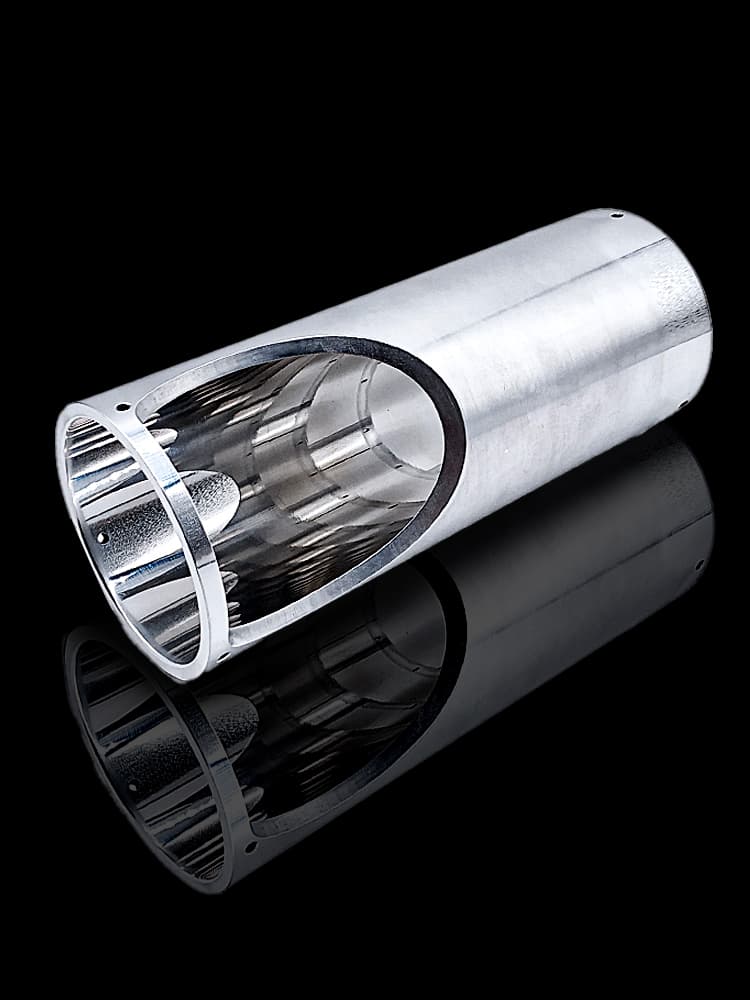
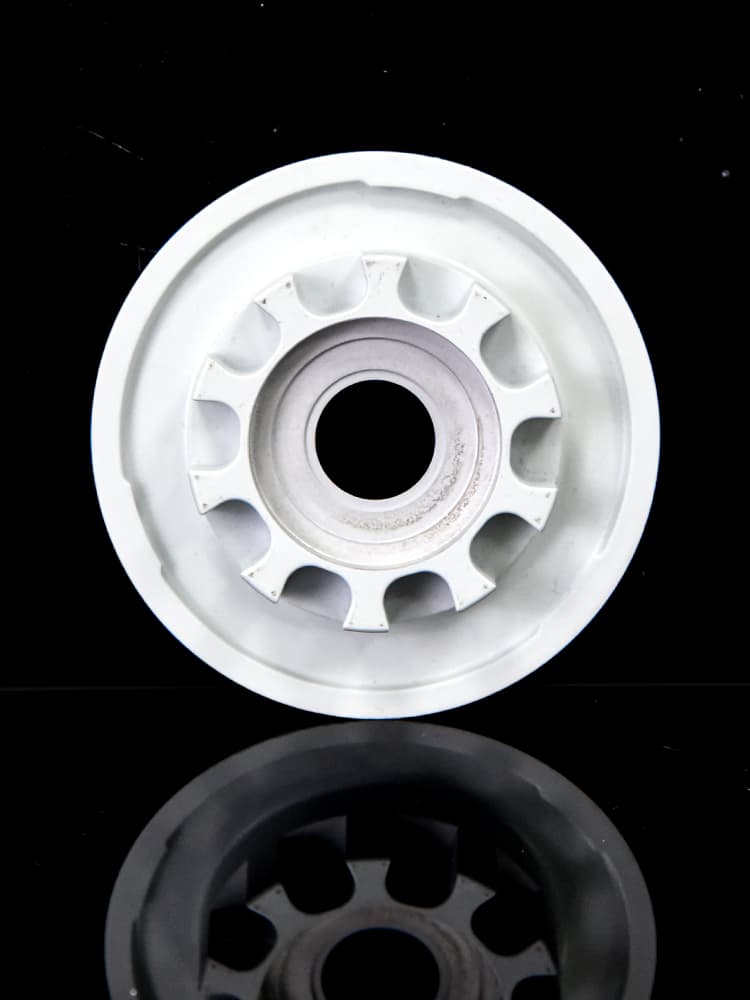
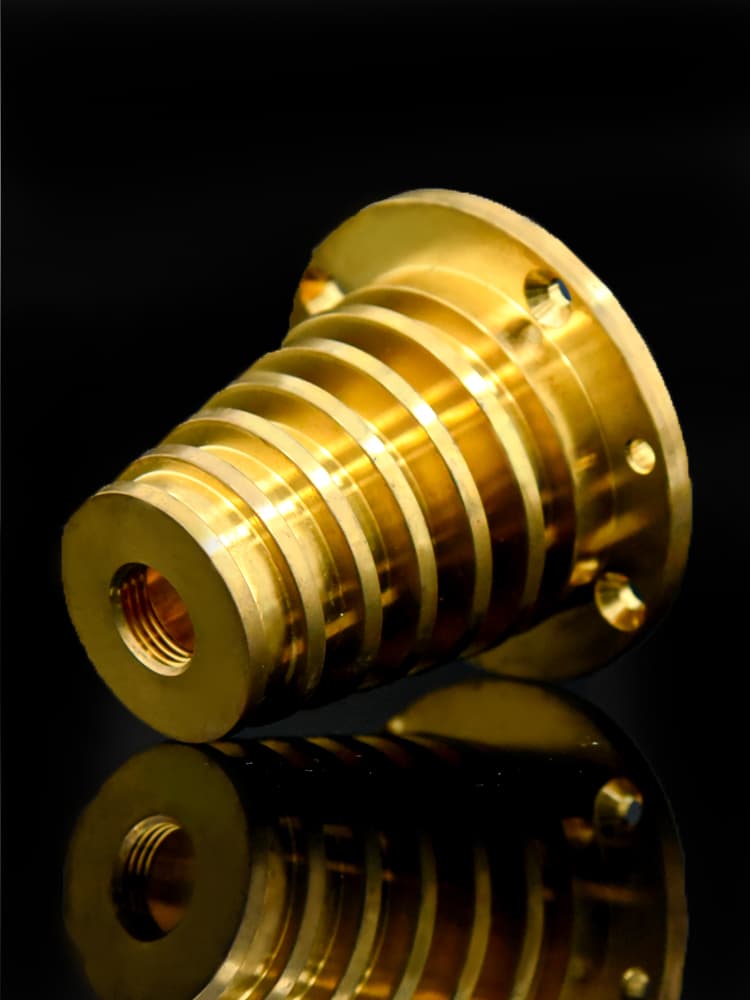
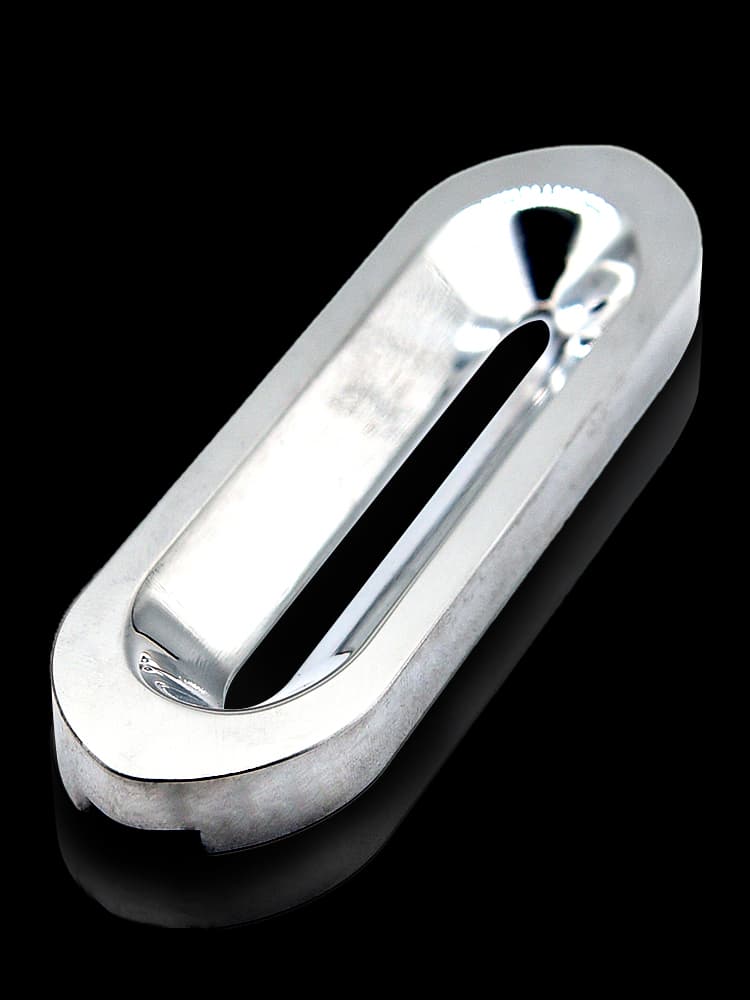
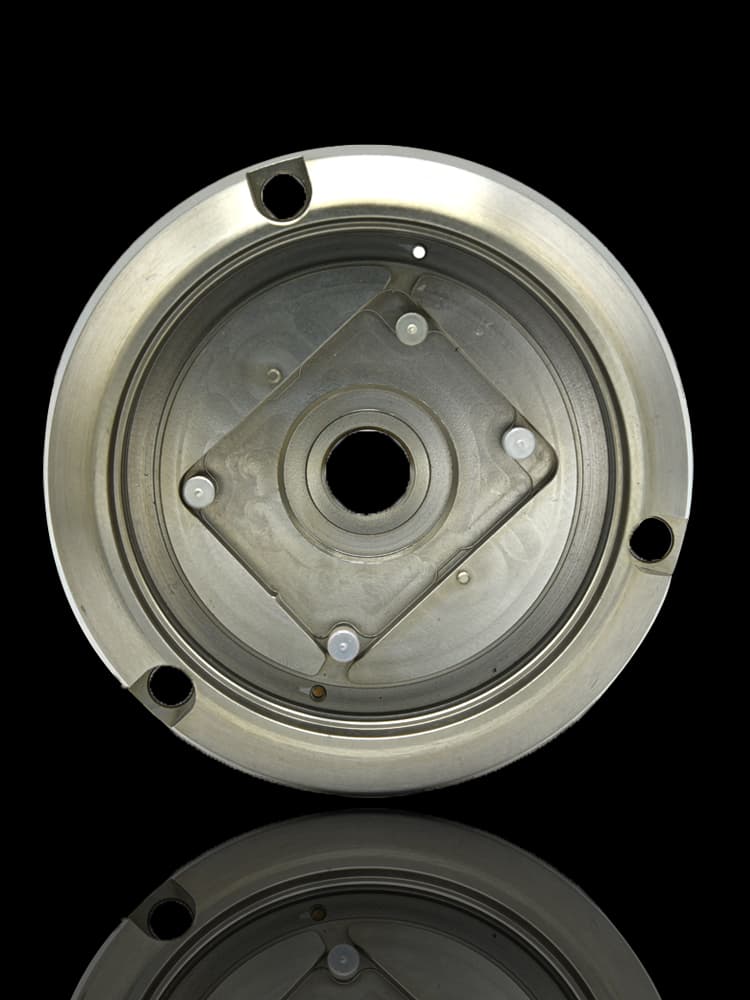
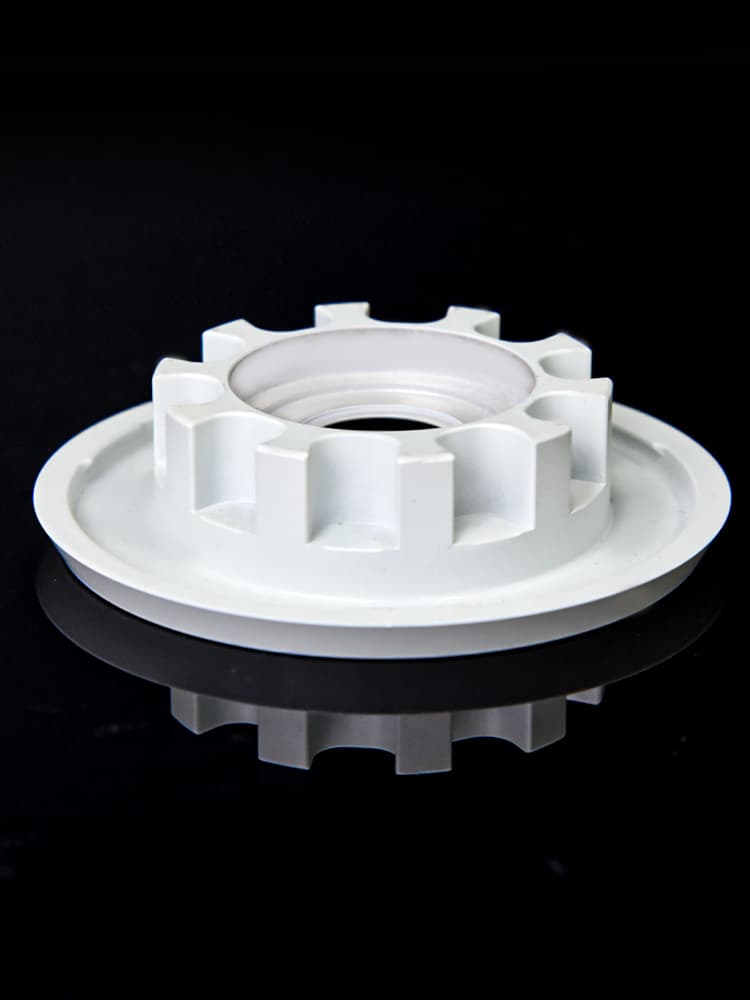
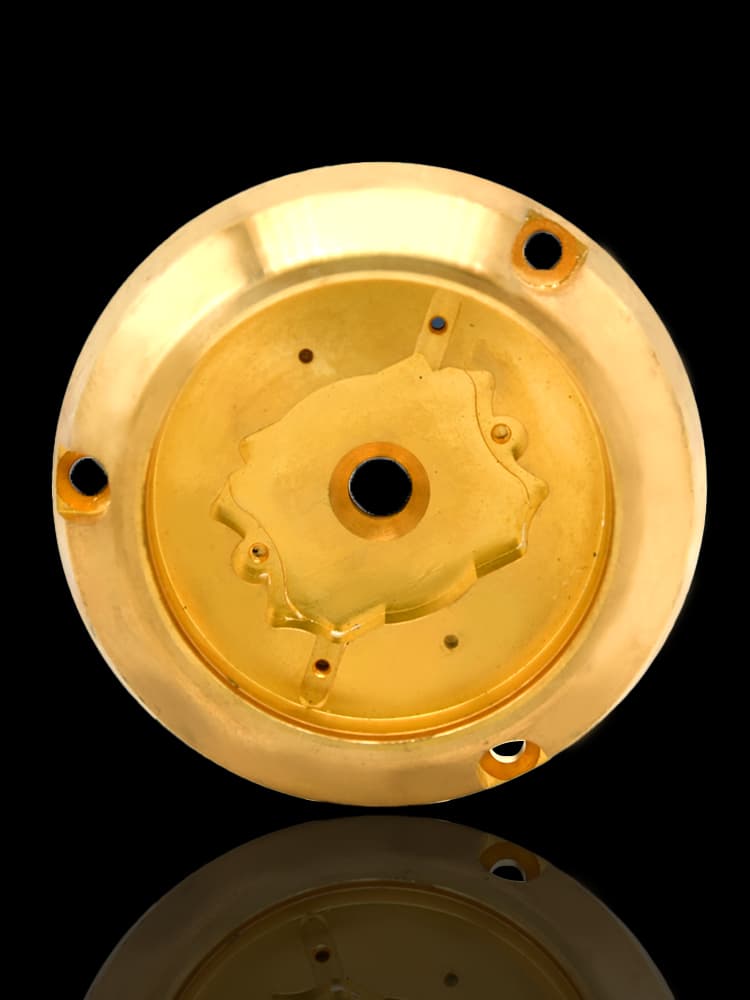
Our Partners
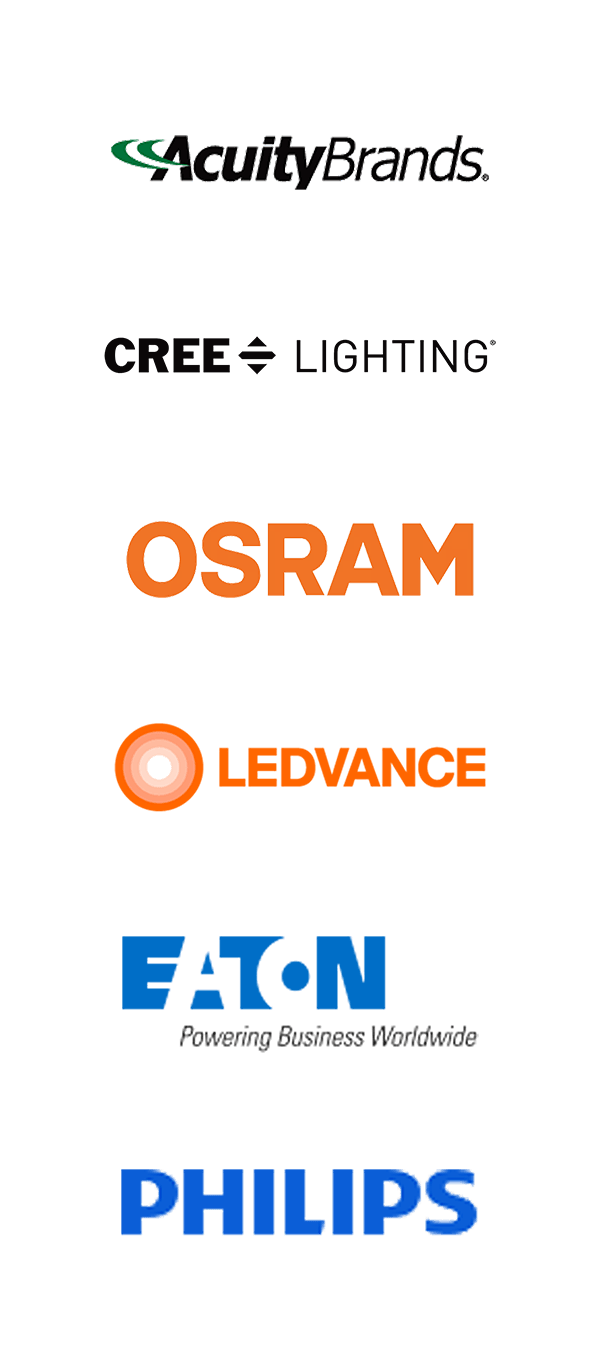
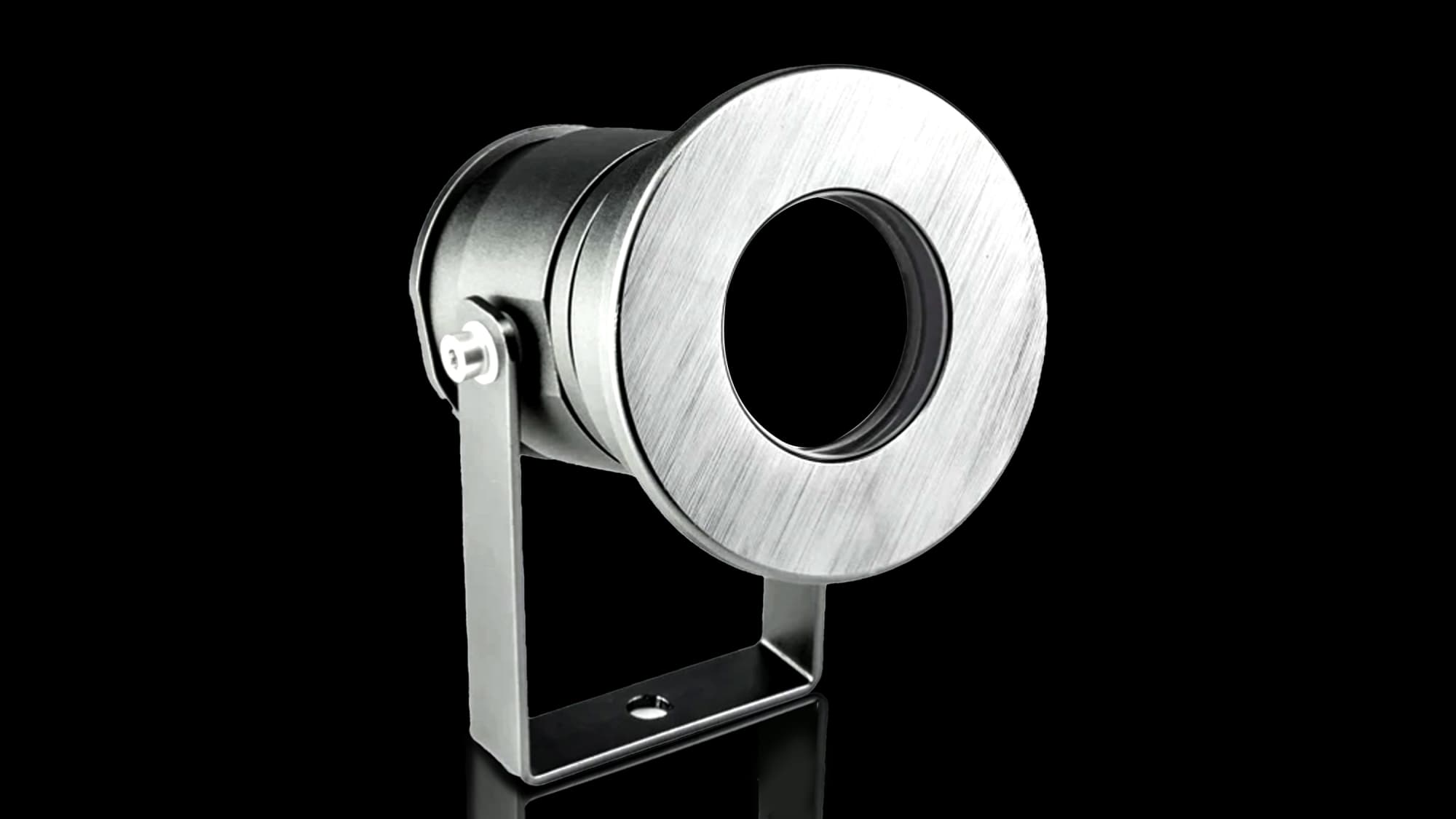
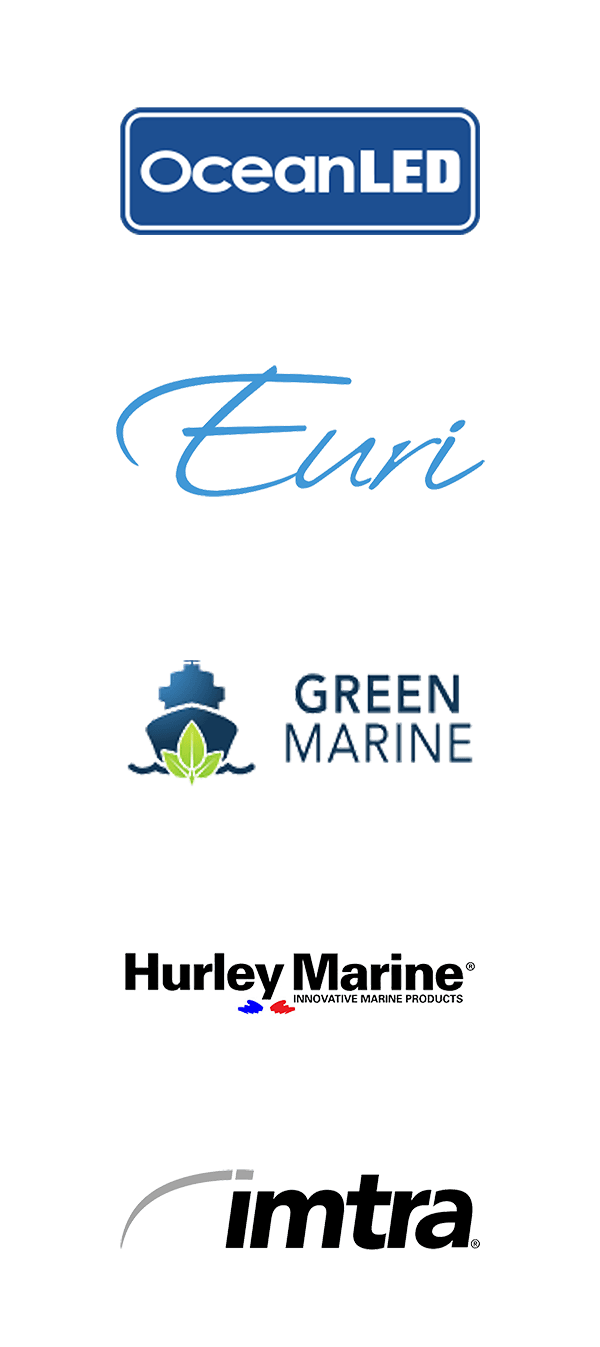
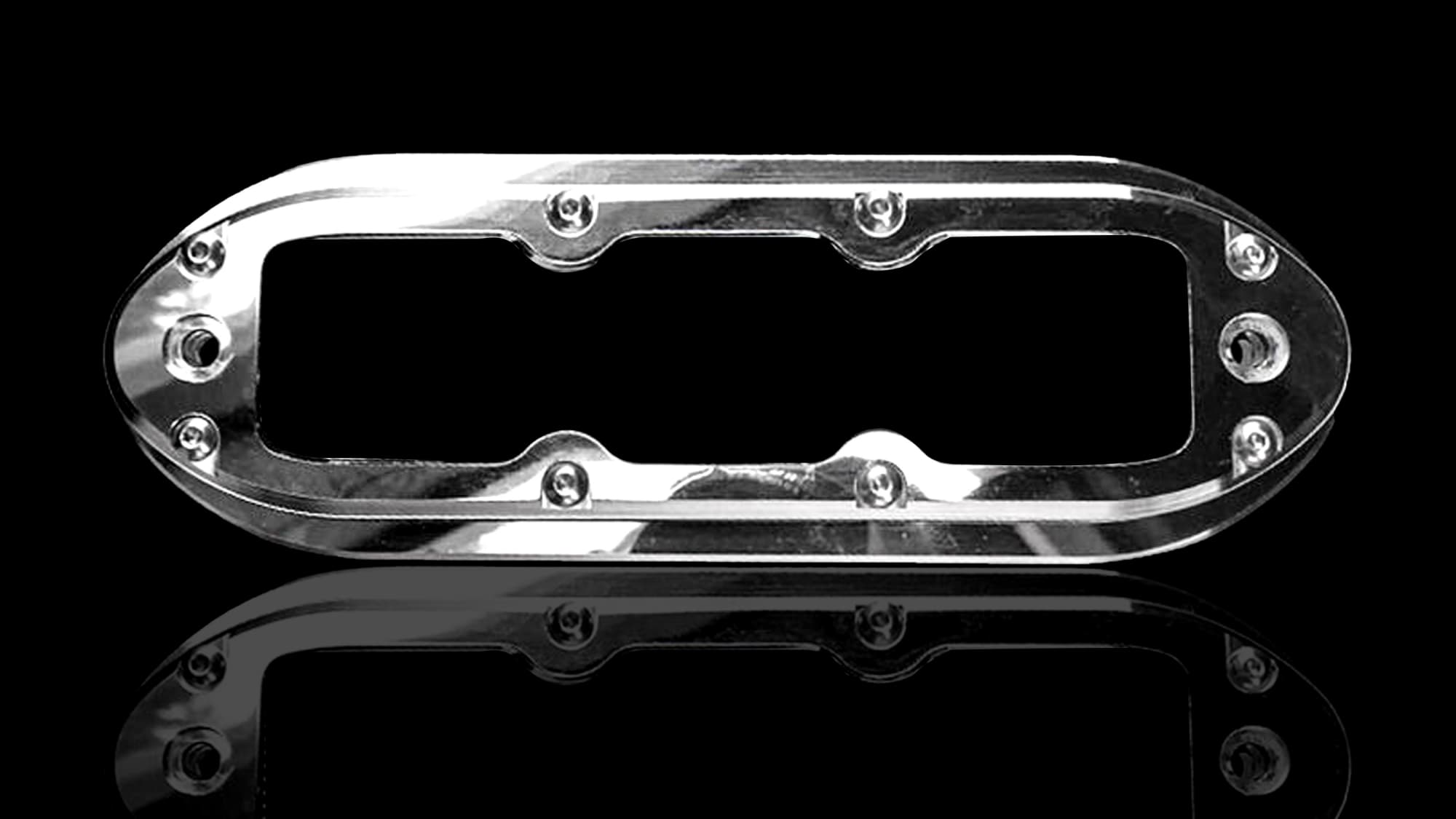
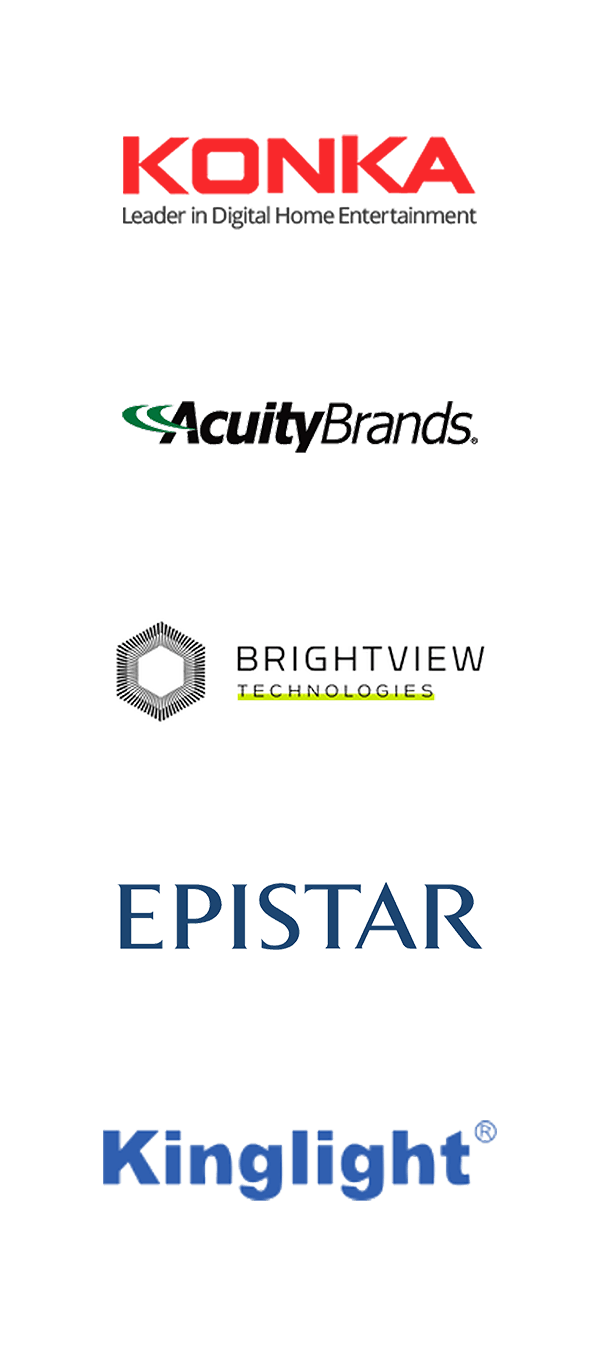
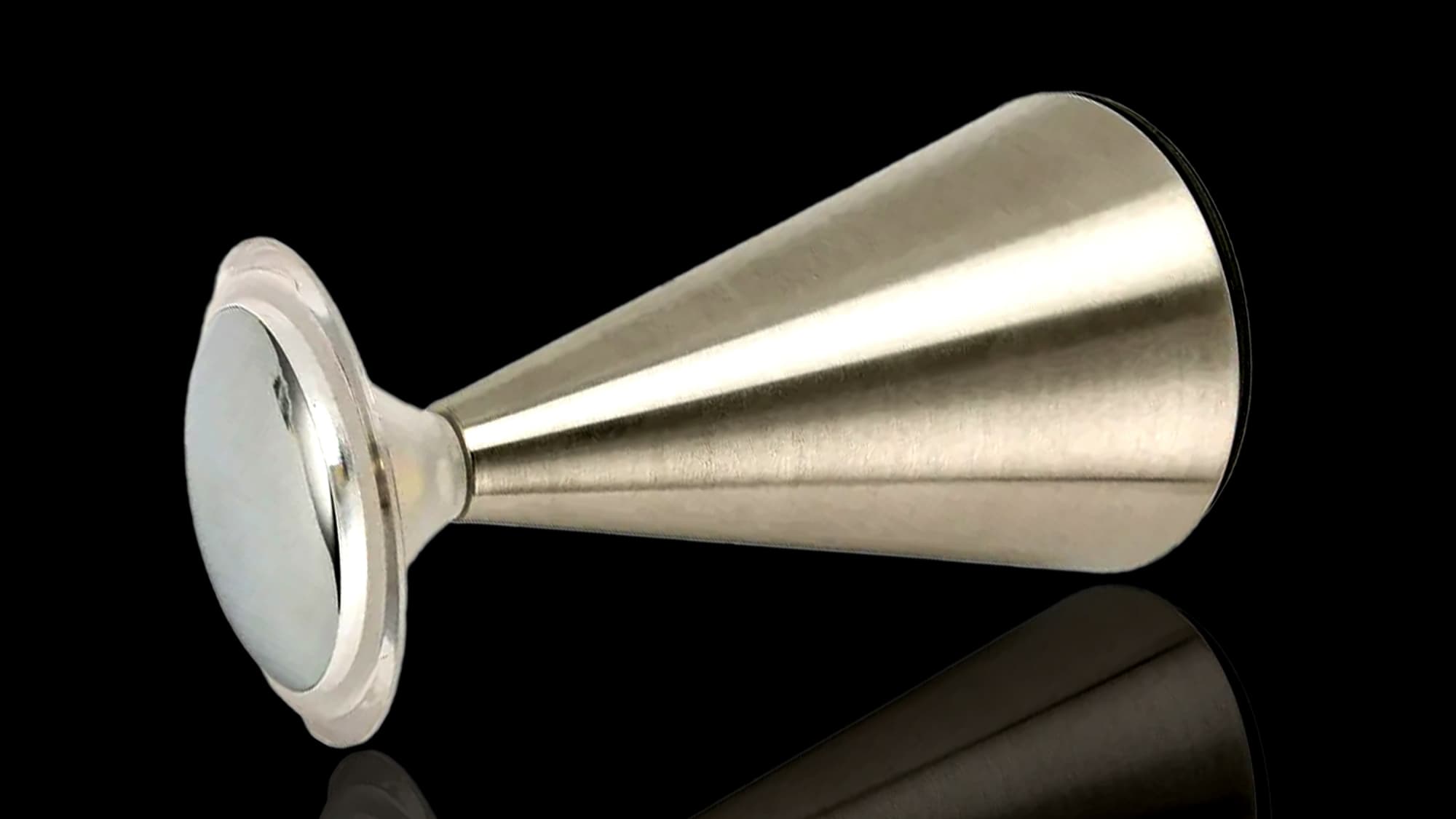
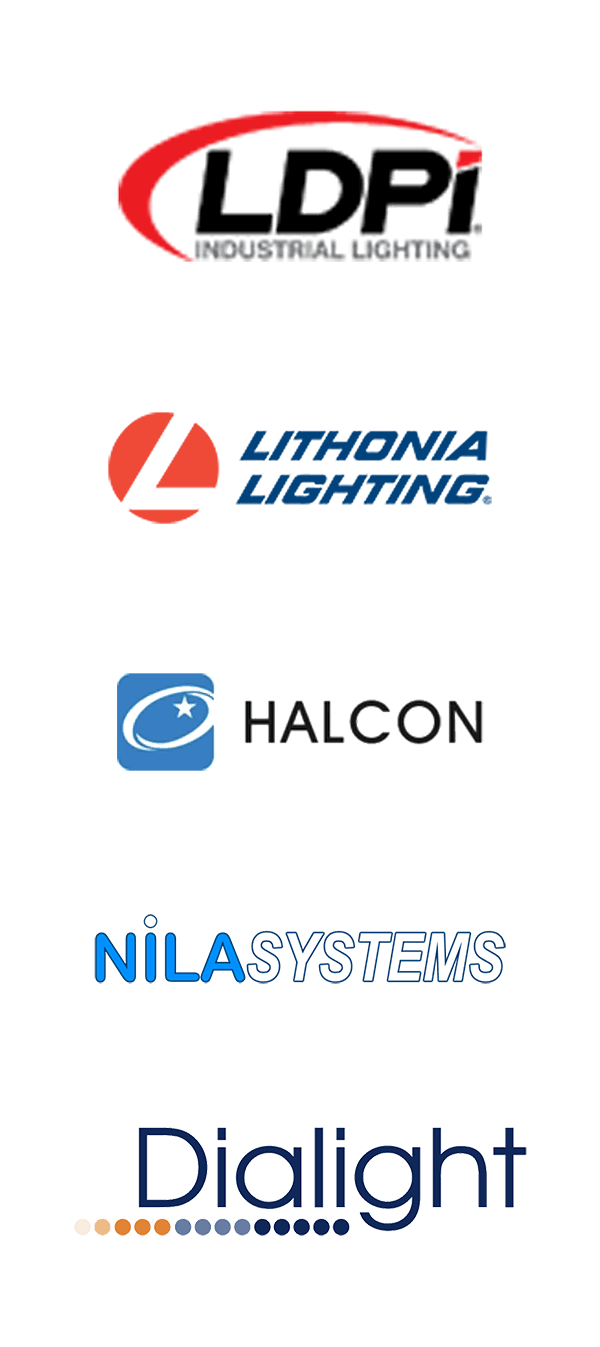
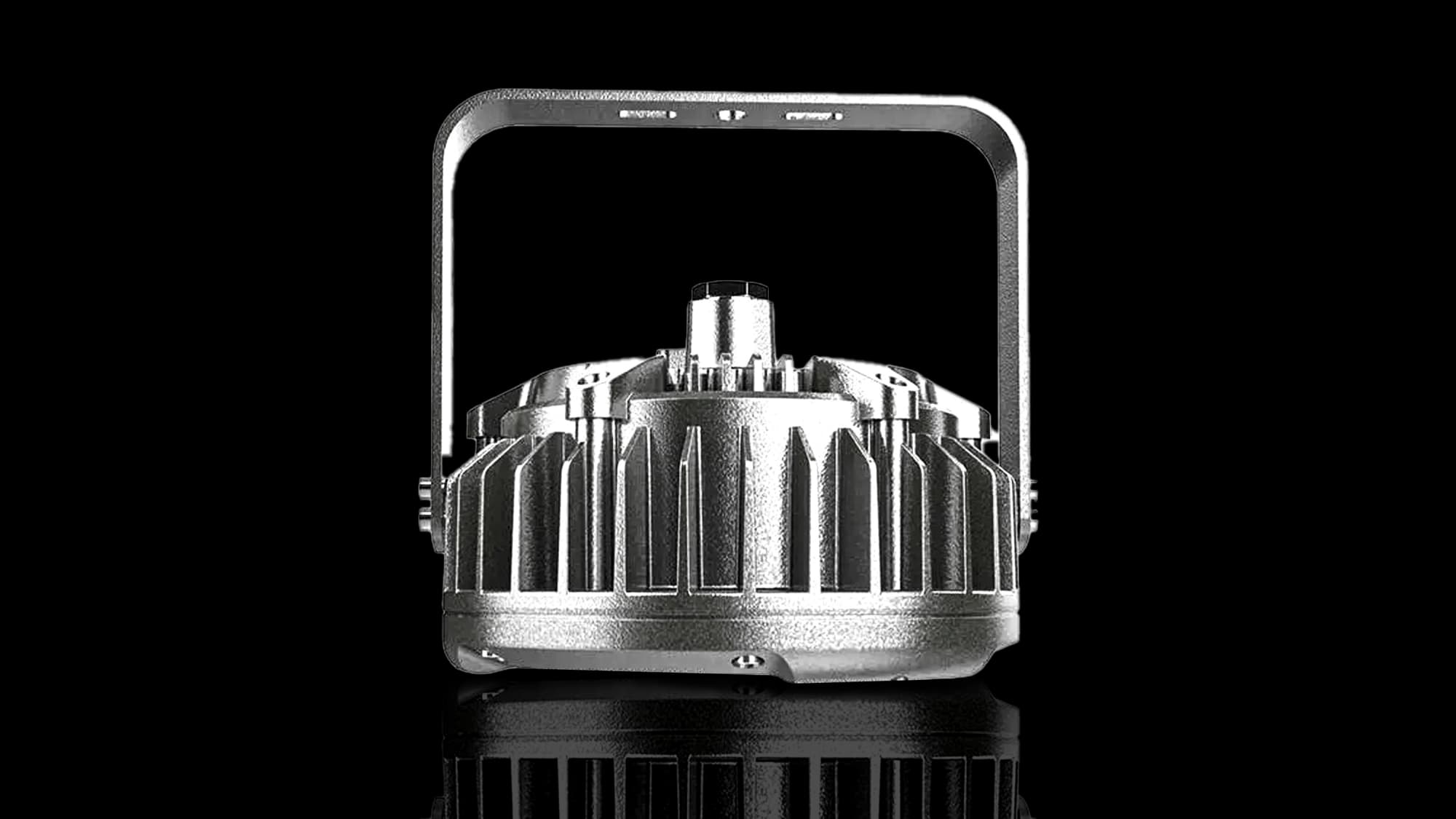

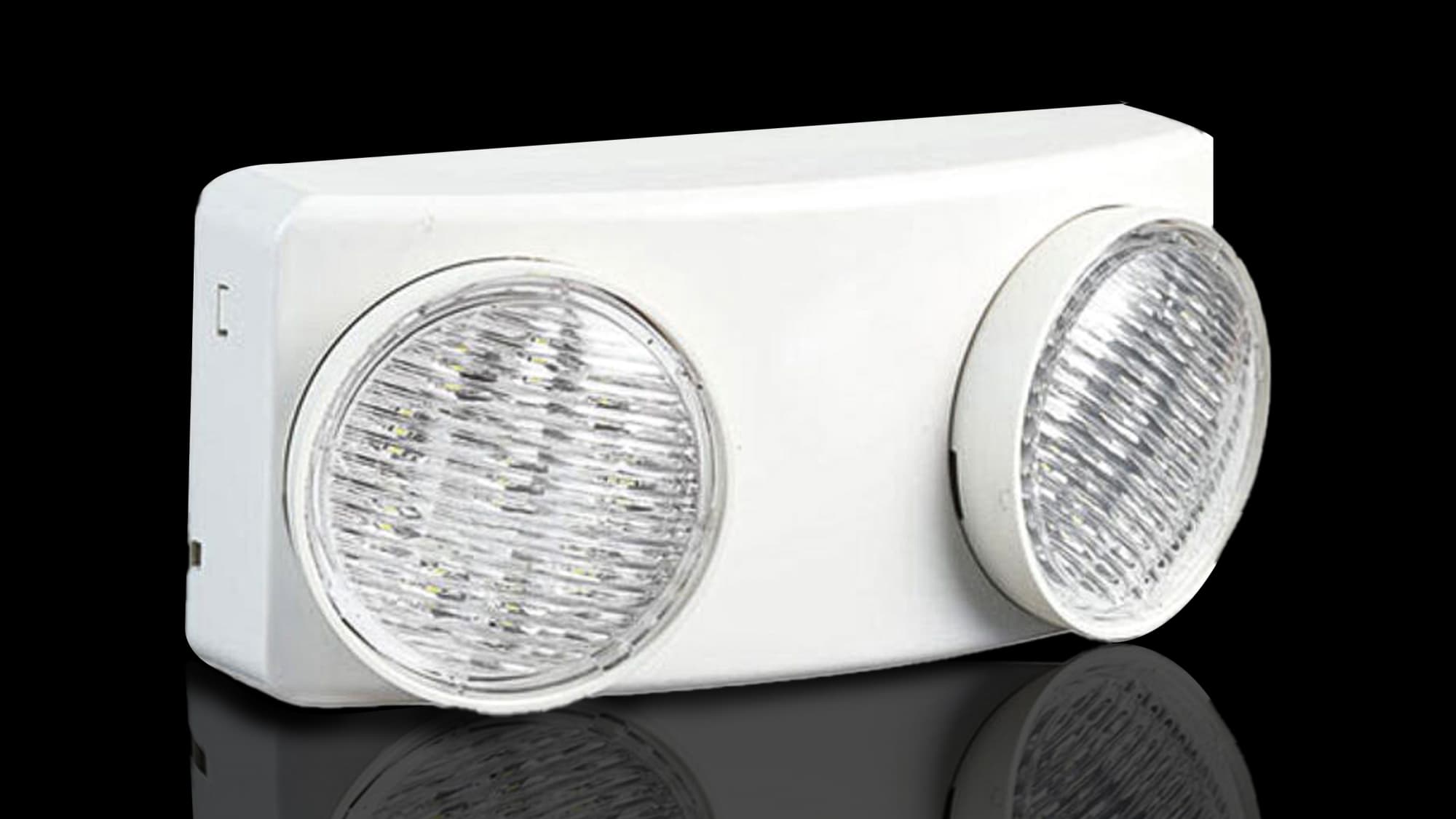
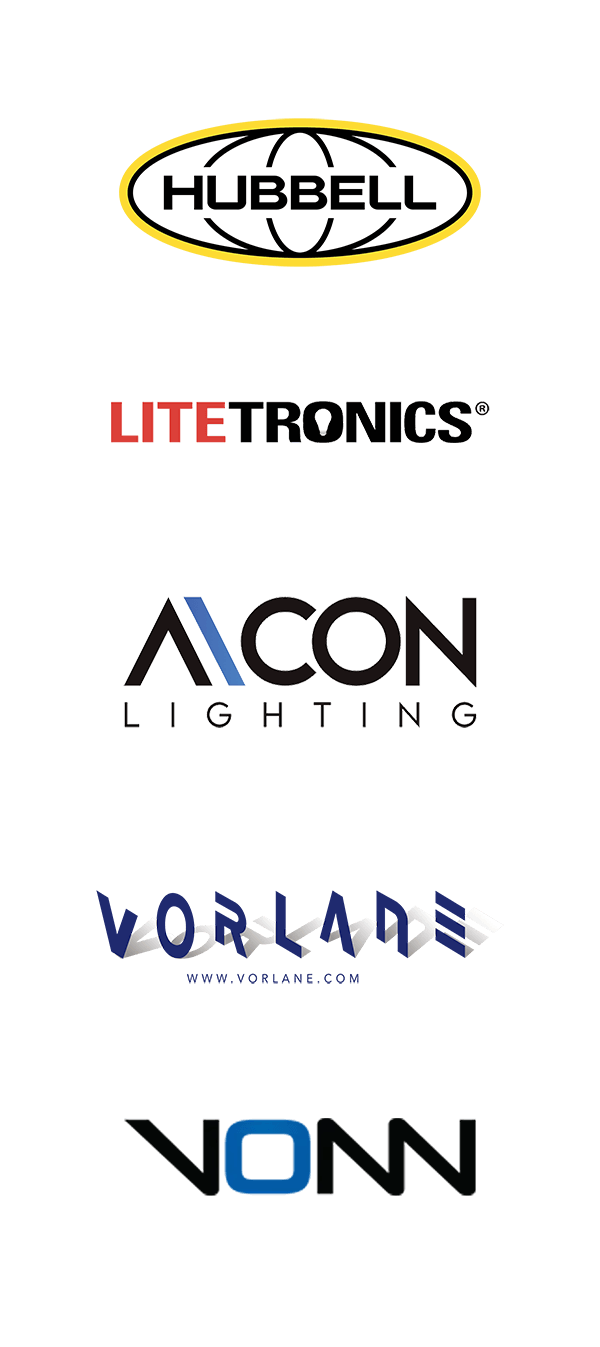
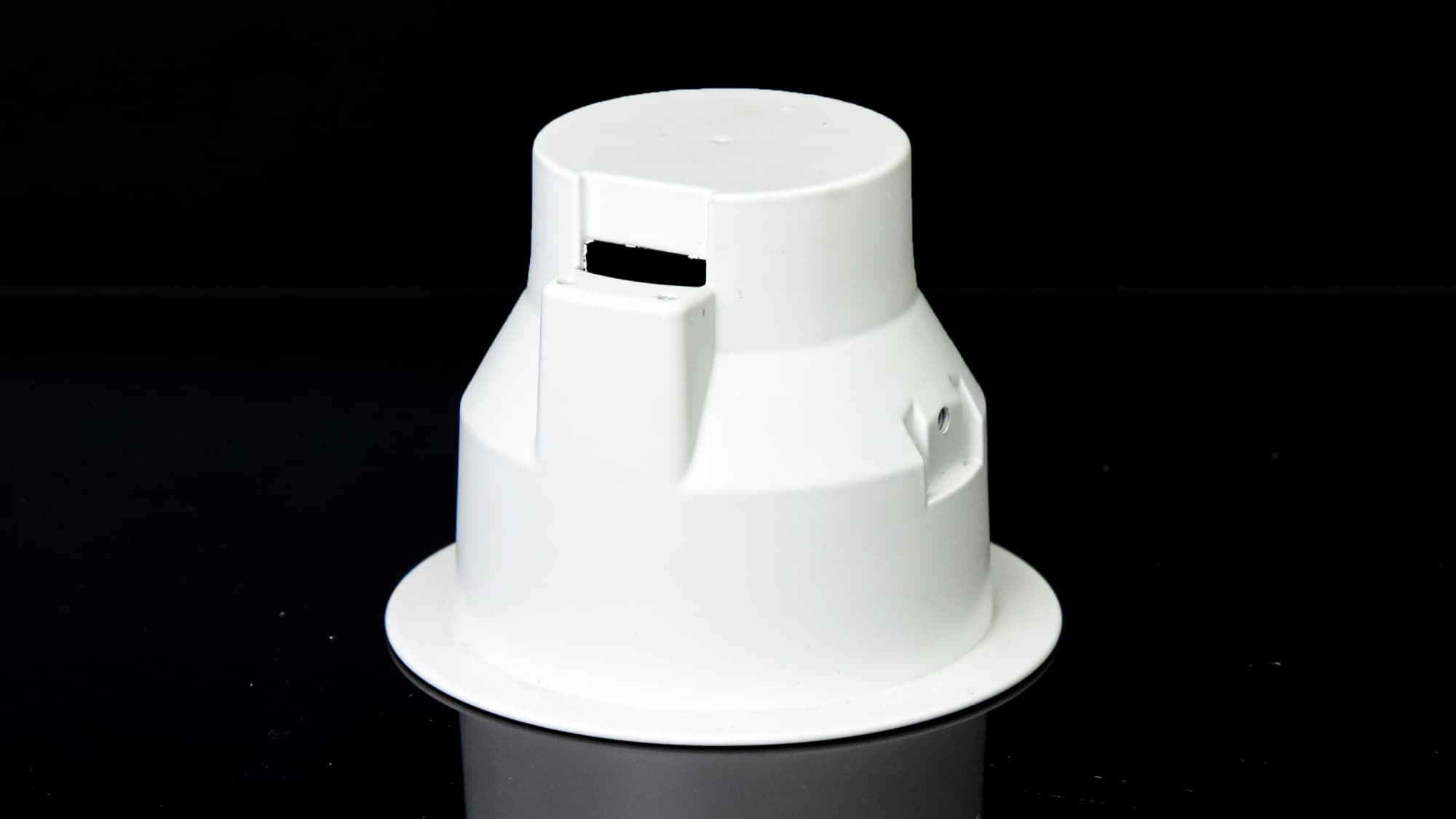
Lighting Industry Engineer Nora from Xielifeng has something to say
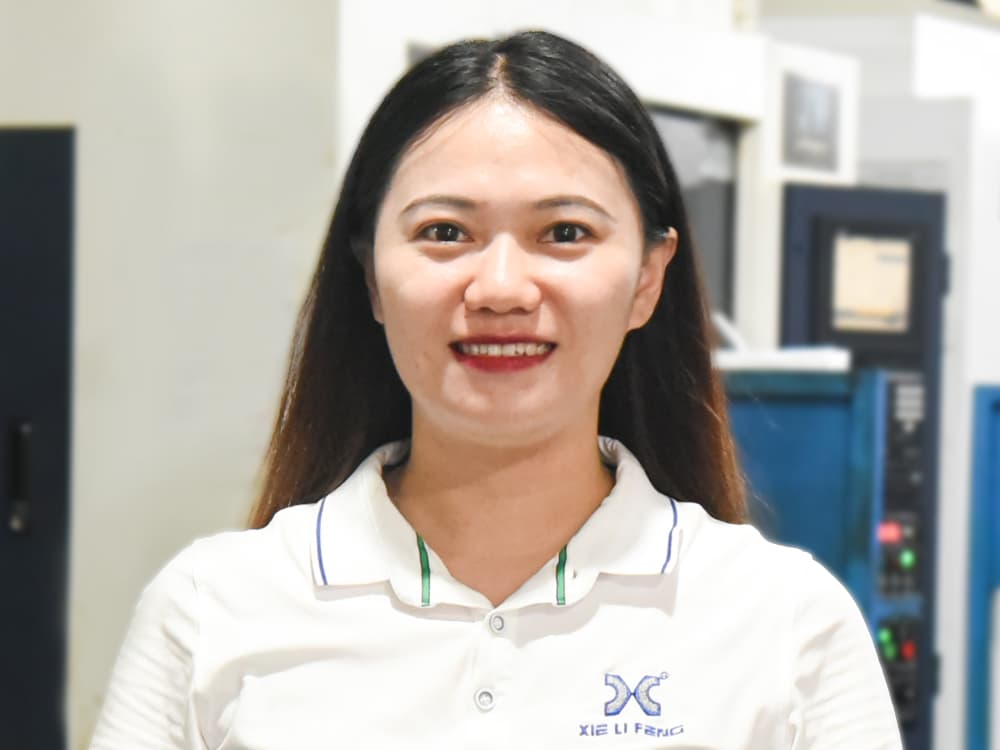
Senior Engineer Nora, 10 years of experience in machining high-value, technically complex parts for the lighting industry. Specialized in heat sinks, reflective housings, and precision connectors, ensuring components meet strict performance, reliability, and aesthetic standards.
What materials do you recommend for lighting components to ensure durability and heat dissipation?
We recommend aluminum alloys, such as 6061 and 6063, due to their excellent thermal conductivity and lightweight properties. For connectors, brass provides good electrical conductivity and durability. In applications requiring high reflectivity, anodized aluminum or stainless steel ensures lasting performance.
How do you ensure dimensional precision when machining reflective housings?
We use 5-axis CNC machines to produce reflective housings with complex geometries and tight tolerances. By closely monitoring cutting parameters and minimizing tool wear, we ensure consistency across batches. We also perform post-machining dimensional inspections to verify that all parts meet the required specifications for seamless assembly.
How do you ensure corrosion resistance and durability of marine lighting components?
Marine environments present unique challenges, including exposure to saltwater and humidity. We use marine-grade stainless steel and brass for components exposed to these harsh conditions. Additionally, we apply anodizing and anti-corrosion coatings to protect aluminum parts. Each part undergoes salt spray testing to ensure it can withstand long-term exposure to maritime environments.
How do you ensure corrosion resistance for outdoor lighting components?
We apply anodizing or powder coating to aluminum components for enhanced corrosion resistance. For connectors or exposed metal surfaces, we use stainless steel or brass to prevent rust and oxidation. Each part undergoes corrosion-resistance inspections to ensure it meets industry requirements for outdoor use.
How do you meet high-volume production requirements while maintaining quality?
We use automated CNC machining to ensure consistency and efficiency in high-volume production. Our team performs first-article inspections (FAI) at the beginning of each production run to validate the setup. We also implement statistical process control (SPC) to monitor quality in real-time and make adjustments when necessary, minimizing the chance of defects.
How do you ensure consistency in the surface finish across multiple lighting components?
We standardize our surface finishing processes, such as anodizing and powder coating, to ensure uniformity. Our team performs color and texture checks on each batch to guarantee consistency. Additionally, we work closely with clients to align the surface finish with their design specifications, ensuring all components fit seamlessly within the overall product design.
How Xielifeng Works in Machined Lighting Parts
From quotation to delivery, we provide efficient, high-quality services, making manufacturing more convenient.
01
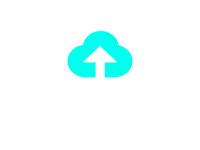
Upload drawing
CAD files: 2D: DXF | DWG | PDF 3D: STP | STEP |IGS | IGES| X_T | SLDPRT
02
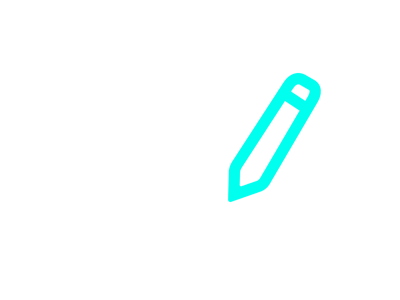
DFM Evaluation & Quote
- Drawing review
- Process analysis
- Material inspection
- Feasibility proposal
- Cost estimation
03
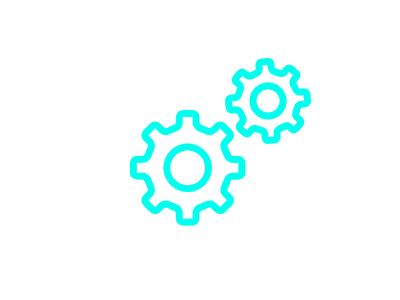
Order Confirmtion & Production
- Sample processing
- Sample quality inspection
- Customer confirmation
- Mass production plan
04
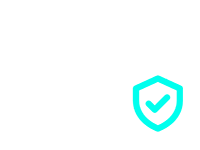
Quality Inspection & Delivery
- Raw material inspection
- First piece inspection
- Process inspection
- Final inspection
- Inspection report