Die Casting
Aluminum Die Casting
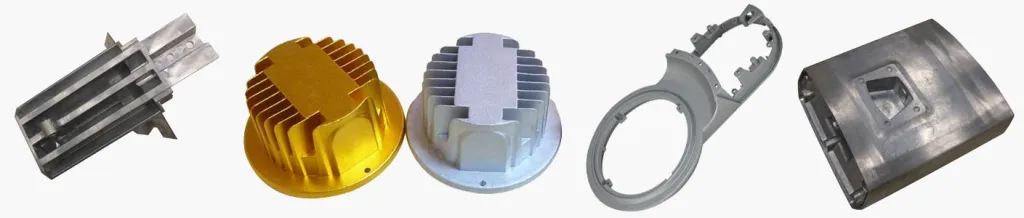
Zinc Die Casting
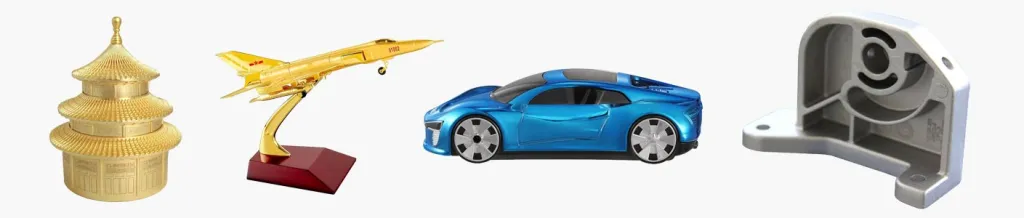
Magnesium die casting
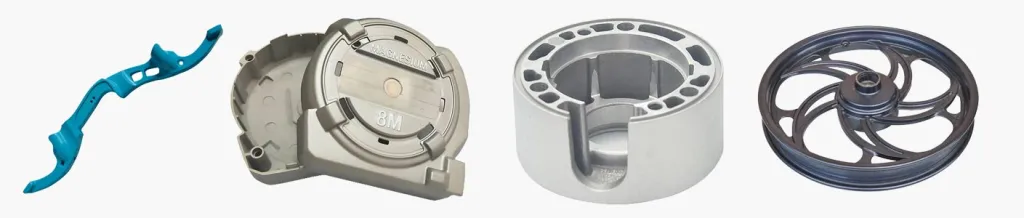
Why Choose Us
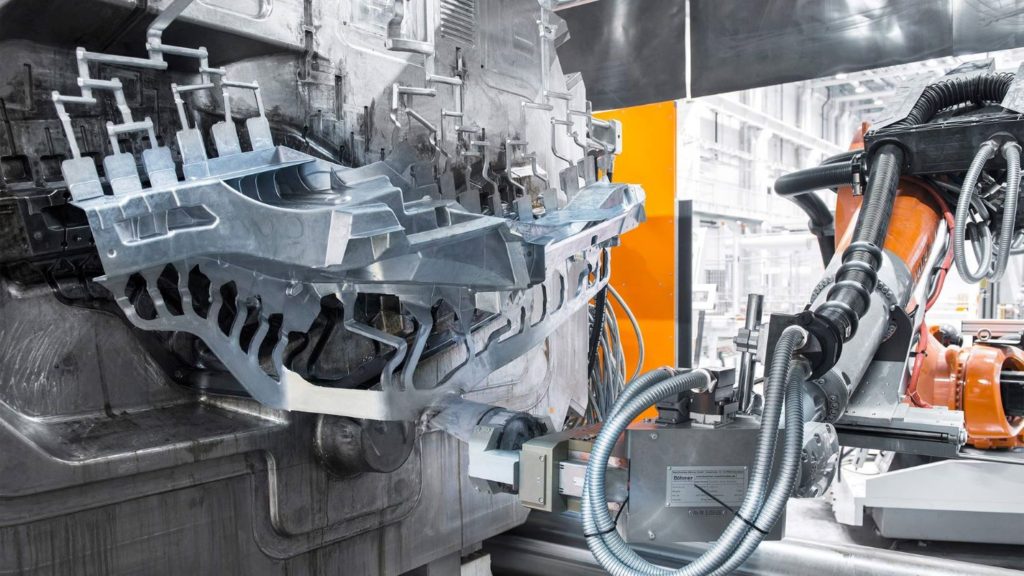
About Die Casting Production
- Automatic production, die casting machine with ABB robot.
- Our engineers have rich mold design and manufacturing experience in diecasting industry.
- Process: high presure/low presure/gravity die casting
- Surface treatment: anodizing, oxidizing, sandblasting,brushing,polishing,plating, powerder coating,PVD/DLC coating, heat-treatment, passivation, QPQ, and so on.
- Tolerance: +/- 0.03-0.05mm avaialble
- Salt spray test :48-720 hours, according to different surface treatment
- Molds belong to customers who pay for it.
About Drawings and Delivery
- 2D and 3D drawings types: JPG,PDF,STP,IGS,DWG,X-T, etc.
- Certificate:SGS,ROHS,IATF16949,etc
- Delivery time:25-45 days for mould , 20-30 for mass production
- 100% inspection before delivery.
The materials suitable for die casting are aluminum, zinc and magnesium. The most common aluminum for die casting are A356, A380, ADC12, and also we can do anodizing aluminum DM3, 6061 etc.
For zinc material, we can make die casted hinges, locks, automobile and motorcycle parts, gearbox, etc.
For magnesium alloy, we can make die casting wheels, brackets, car parts etc.
We can also die cast other metal parts accoding to drawings.
The largest die-casted part we could make is sized by 800mm*800mm, around 40kg. The largest die casting equipment we have is 1200 tons. We also do surface treatment including CNC machining, heat treatment, sandblasting, powder coating etc. We have high technical force and can also machine the part after die casting to make it more precision for assembling.
Get An Instant Online Quote Now
What is die casting?
Die casting is a type of metal casting that uses high pressure to force molten metal into a mold cavity formed by two dies. It shares traits with the plastic manufacturing process of injection molding.
Within the larger metal casting landscape, die casting is one of the most popular techniques due to its accuracy and level of detail. The broader category of metal casting, which has existed for thousands of years, contains many different processes that use a mold to form liquid metal. Historically, such a process usually involved pouring the liquid metal into the mold with the aid of gravity — and many metal casting processes still work this way. Die casting, however, is a relatively new form of metal casting, introduced in the 19th century, and it uses pressure instead of gravity to fill the mold cavity.
Die casting is sometimes called high-pressure die casting, due to the amount of pressure — typically 10–140 megapascals — used to force the metal into the mold cavity. The related process of low-pressure die casting (LPDC) is less common. Die casting typically falls into one of two categories: hot-chamber die casting and cold-chamber die casting, which are suitable for different types of metal. However, there are also other variants of the process, such as semi-solid metal casting (SSM).
Benefits of Die Casting
Die casting is an efficient, economical process capable of producing a broader range of shapes and components than other metal casting or forming techniques. Die cast parts typically have a long service life and generally are designed to complement the surrounding part’s visual appeal. Designers can gain several advantages by using die cast parts, such as:
High-speed production: Die castings can be produced into complex shapes with closer tolerances than most mass production processes. Most of the time, little to no machining is needed, meaning thousands of identical parts can be produced before additional tooling is required.
Dimensional accuracy and stability: Die casting produces durable and dimensionally stable parts while maintaining close tolerances.
EMI and RFI shielding: Die cast parts are also heat and UV resistant and provide EMI and RFI shielding.
Strength and weight: In most cases, die cast parts are stronger than plastic injection moldings and are generally stronger and lighter than parts created from other casting methods.
For your convenience’s sake, please directly forward your RFQ to our support email [email protected], we will give you the quote with 24 hours. It will be better if you send us both 2D and 3D drawings.
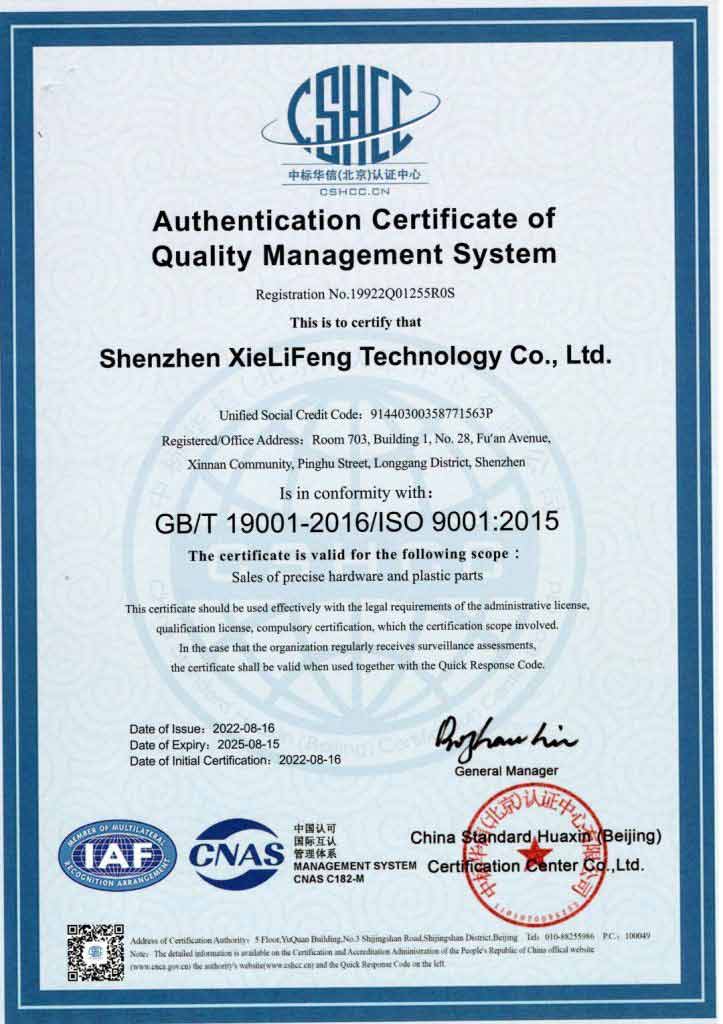