Precision machining driving innovation in Automation & Robotics.
±0.005mm Precision for Automation & Robotics Parts
99.9% Consistency in Mass-Produced Automation Parts
Precision Machining for 100+ Automation Projects Annually
All uploads are secure and confidential.* Learn More
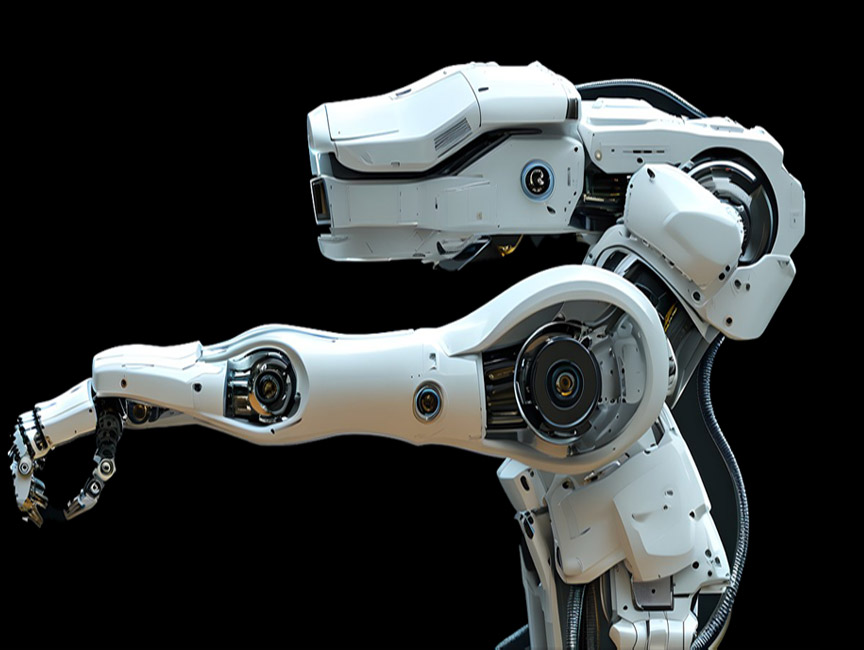
IOS 9001
IOS 14001

About Our Capabilities
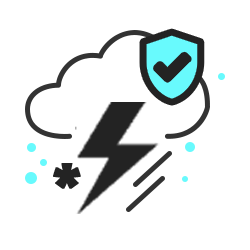
Adaptability to Harsh Environments
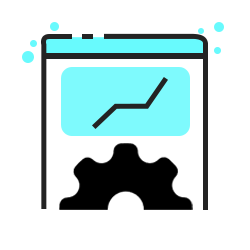
Dynamic Performance Optimization
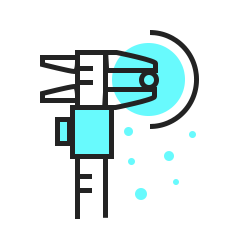
Advanced Quality Management System
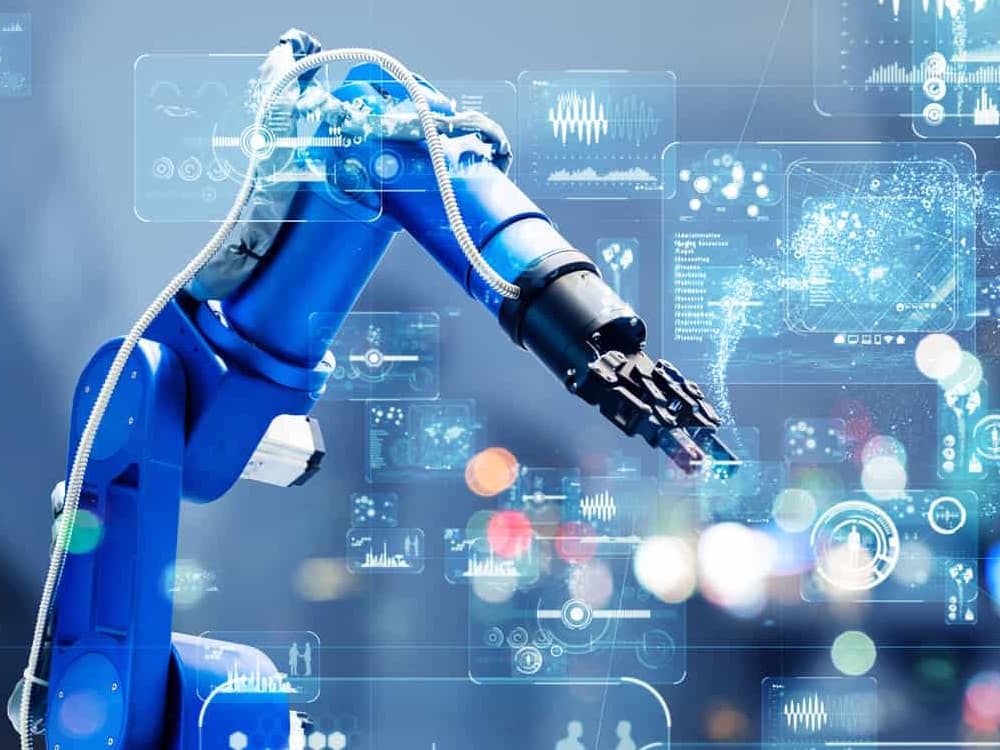
Adaptability to Harsh Environments
Our machining capabilities cover high-temperature, corrosion-resistant, and impact-resistant materials and components, ensuring automated equipment operates reliably in harsh environments for extended periods.
Dynamic Performance Optimization
We focus on machining durable, low-friction components like precision bearings, guides, and transmissions, enhancing the high-speed performance of robotics and automation systems.
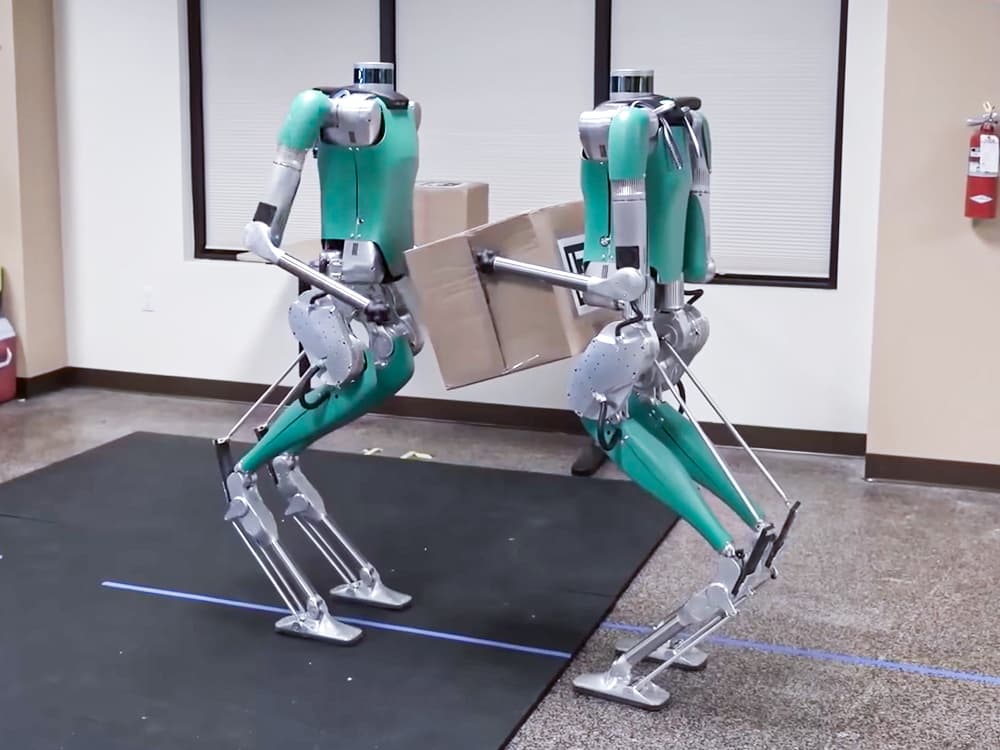
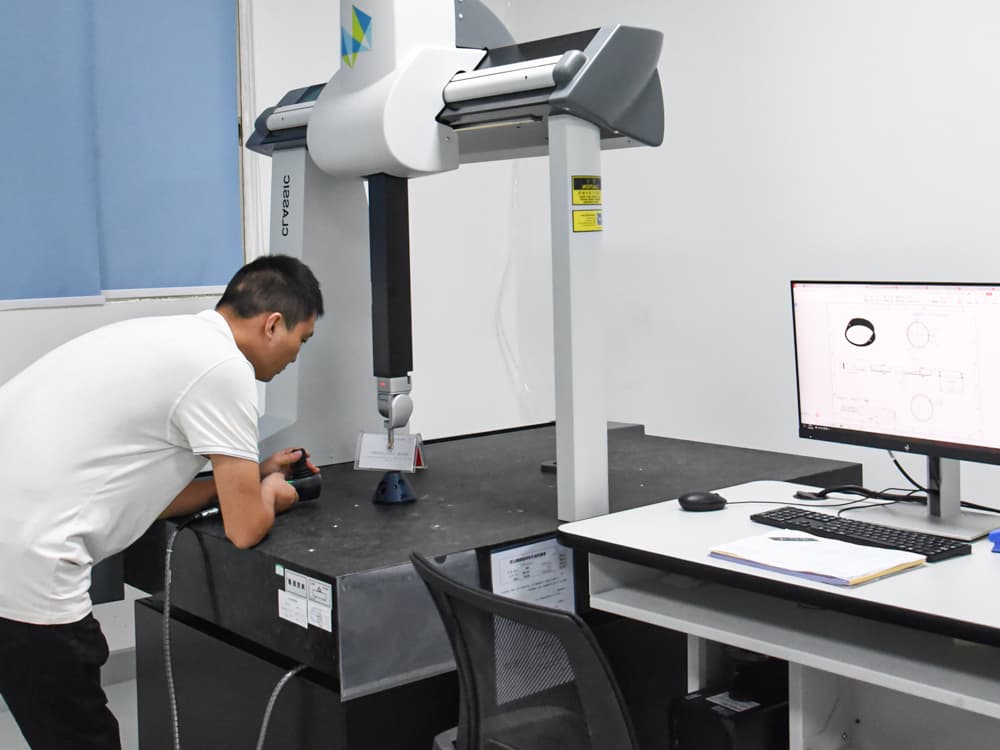
Advanced Quality Management System
With full-process quality traceability and real-time monitoring, we ensure every part meets strict industry standards, achieving an outgoing quality rate of 99.8% or higher.
Application of parts for Automation & Robotics
Component | Material | Surface Treatment | ||||||||
---|---|---|---|---|---|---|---|---|---|---|
Frames and base plates | Aluminum | Anodizing, Electrophoretic, Powder Coating | ||||||||
Machinery end caps and housings | Aluminum | Anodizing, Painting | ||||||||
Gears and drive shafts | Aluminum | Hardcoat anodizing, Electroplating | ||||||||
Heat sinks and cooling parts | Aluminum | Anodizing | ||||||||
Transmission housings | Stainless Steel | Polishing, Sand blasting | ||||||||
Sturdy tools | Stainless Steel | Nitriding treatment, Chrome Plating | ||||||||
Precision bearing housings | Stainless Steel | Polishing, Nitriding treatment | ||||||||
Custom connectors and fasteners | Steel | Zinc Plating, Nickel Plating | ||||||||
Connectors and joints | Titanium Alloy | Anodizing | ||||||||
Motor housing and brackets | Plastic | Coating, Painting |
CNC Automation & Robotics Parts Case Study
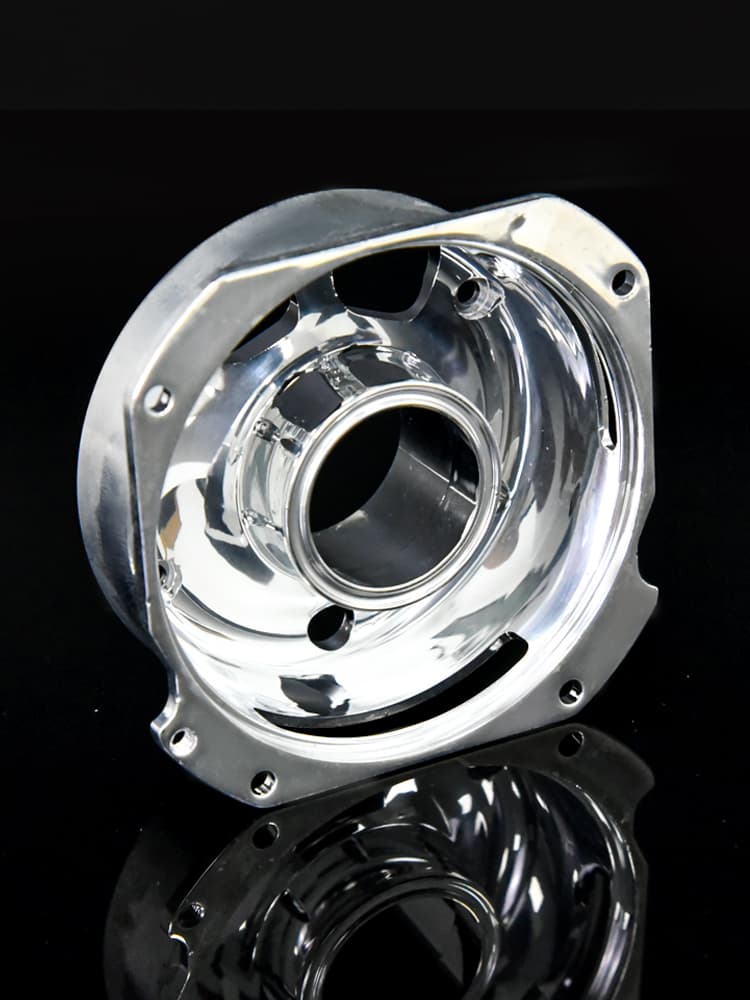
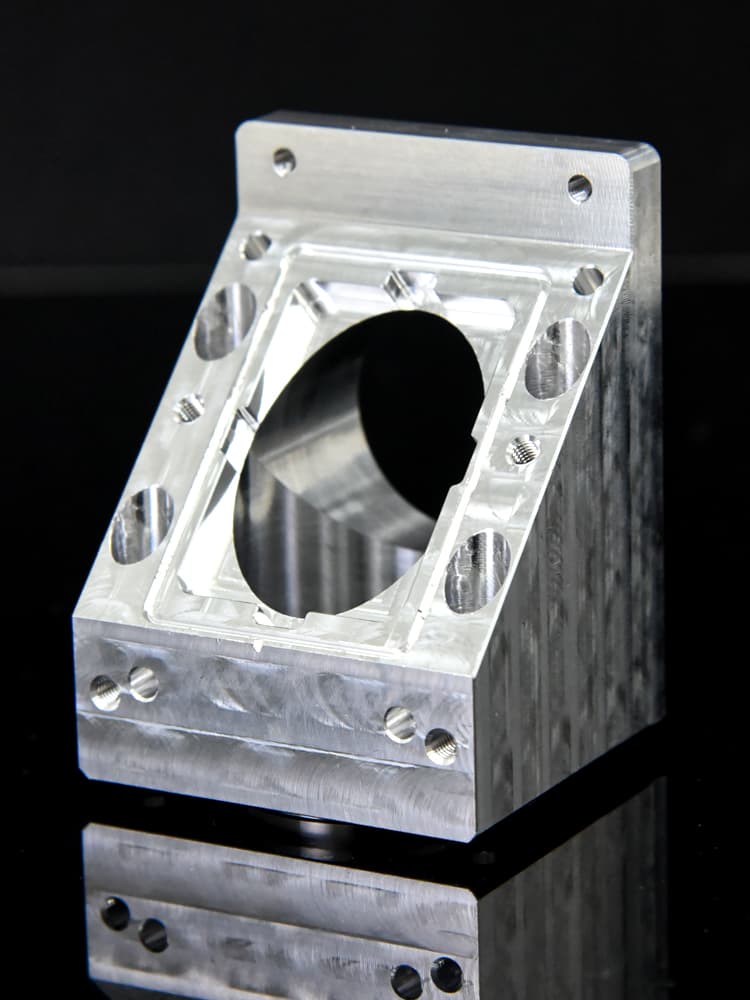
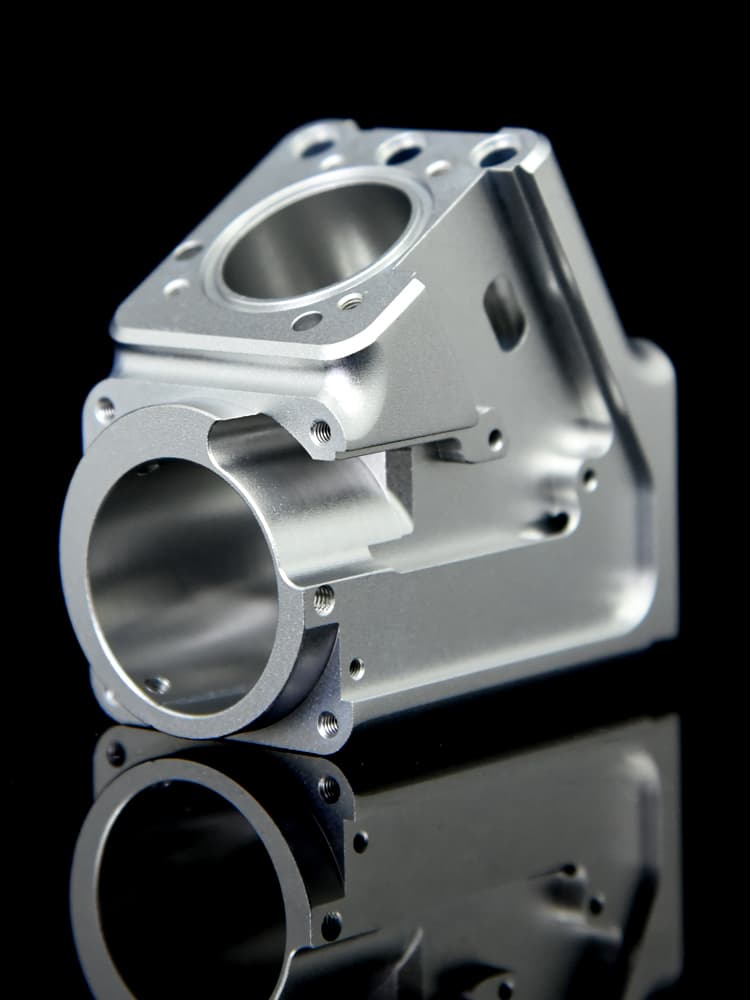
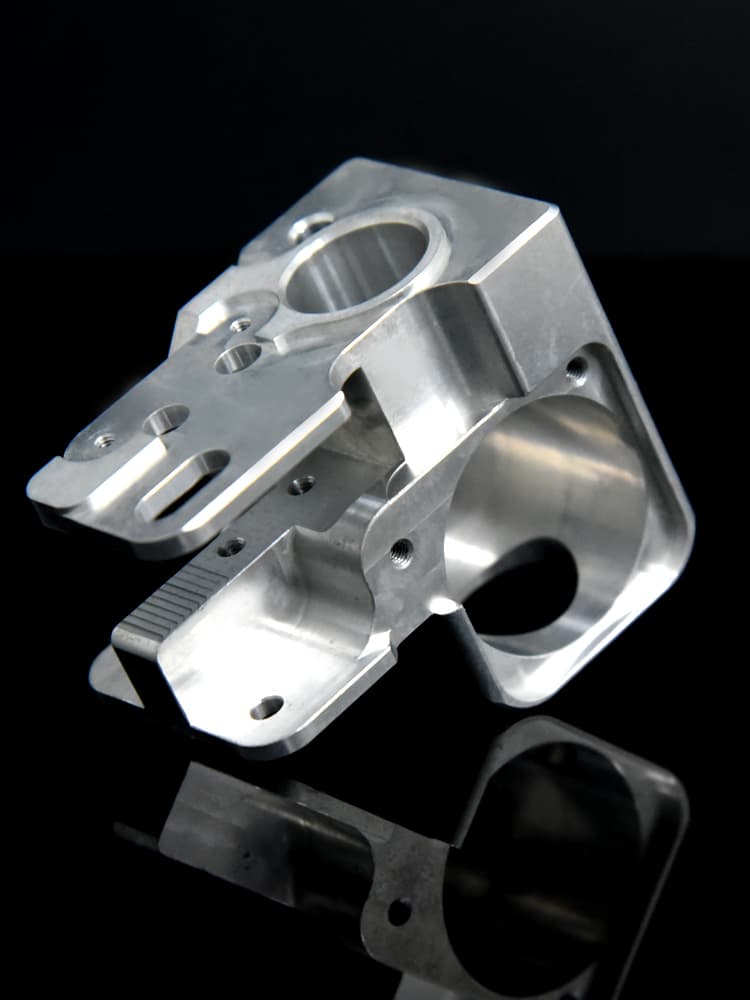
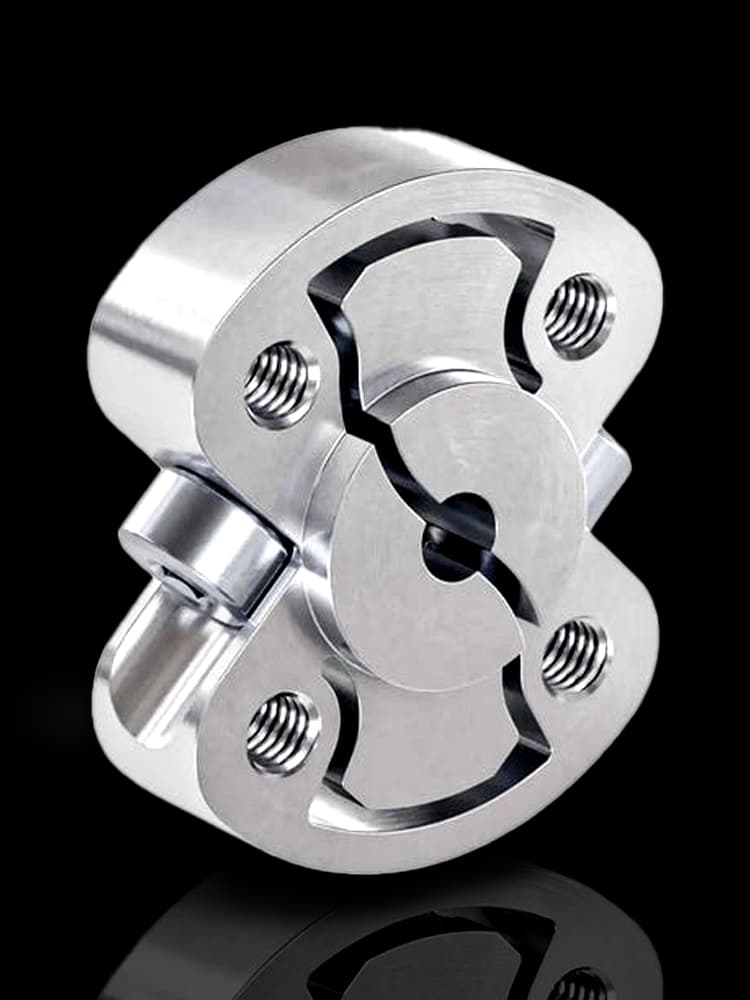
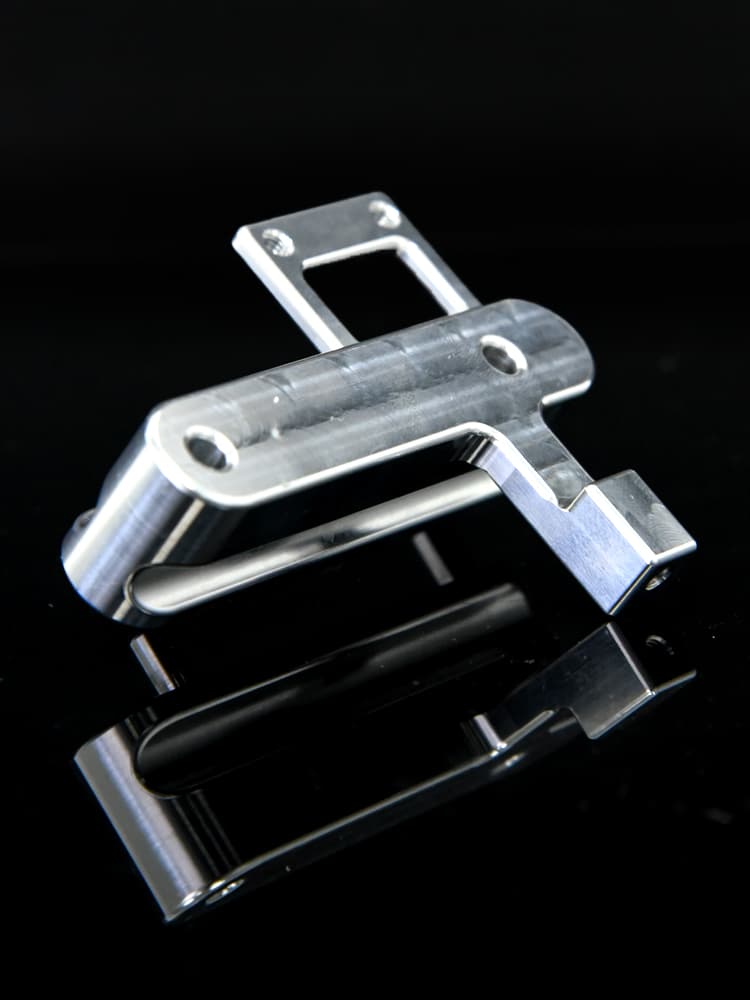
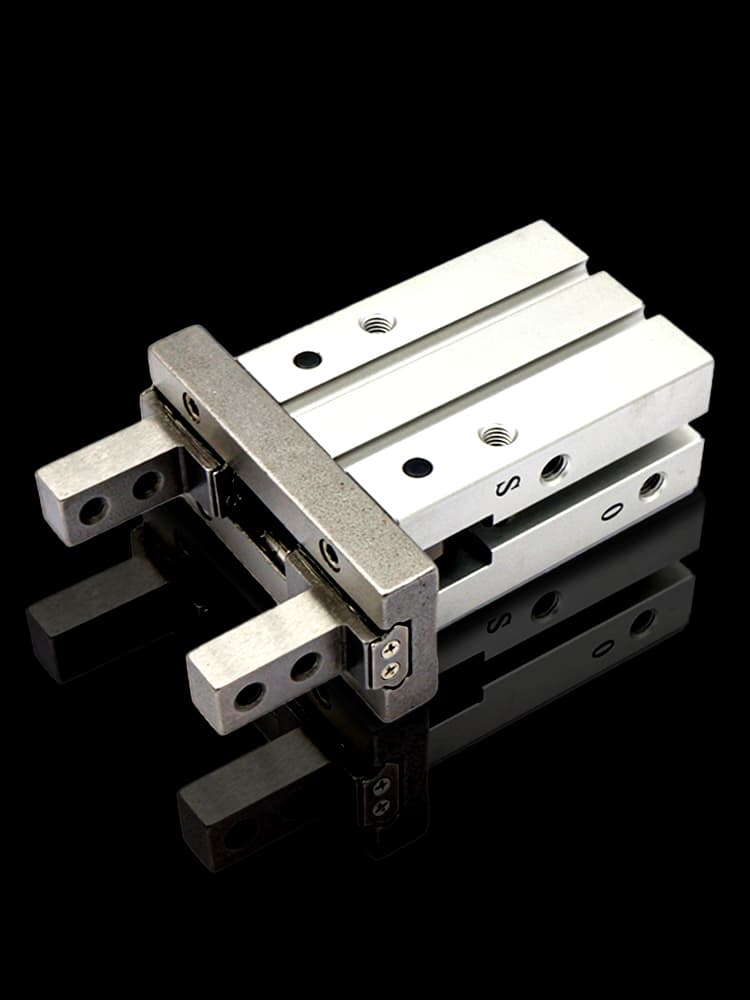
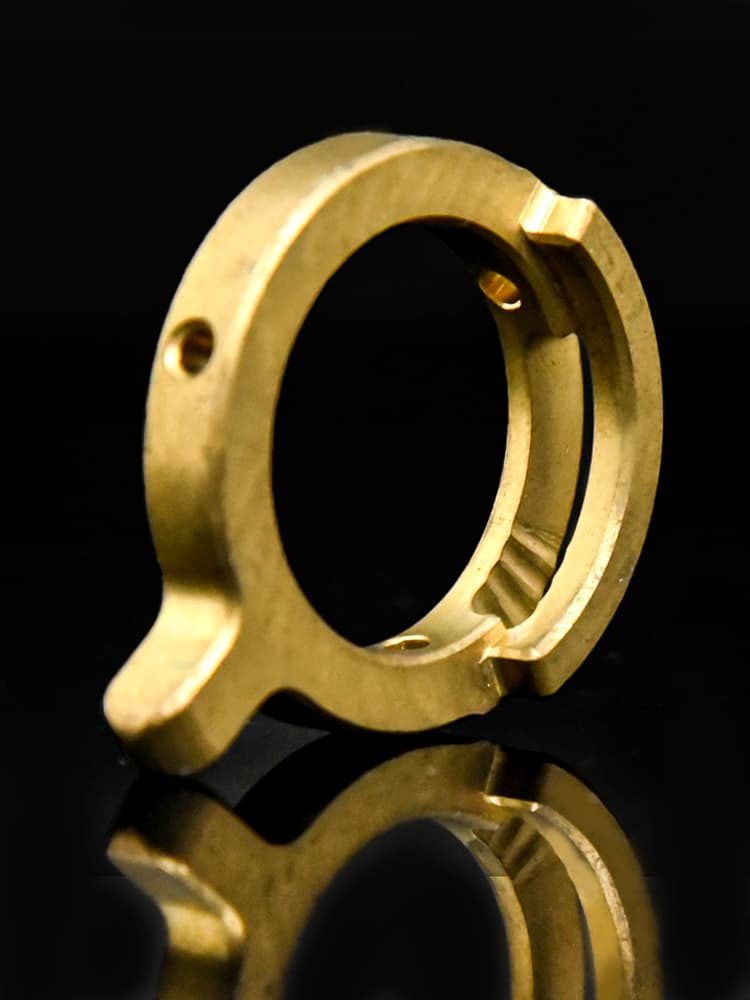
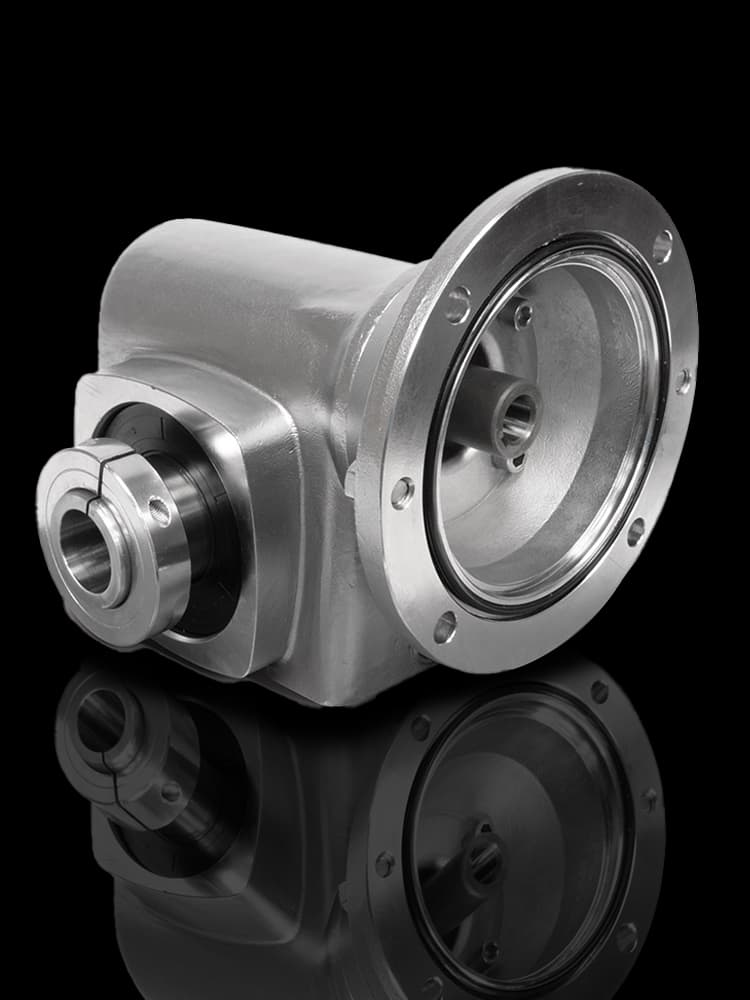
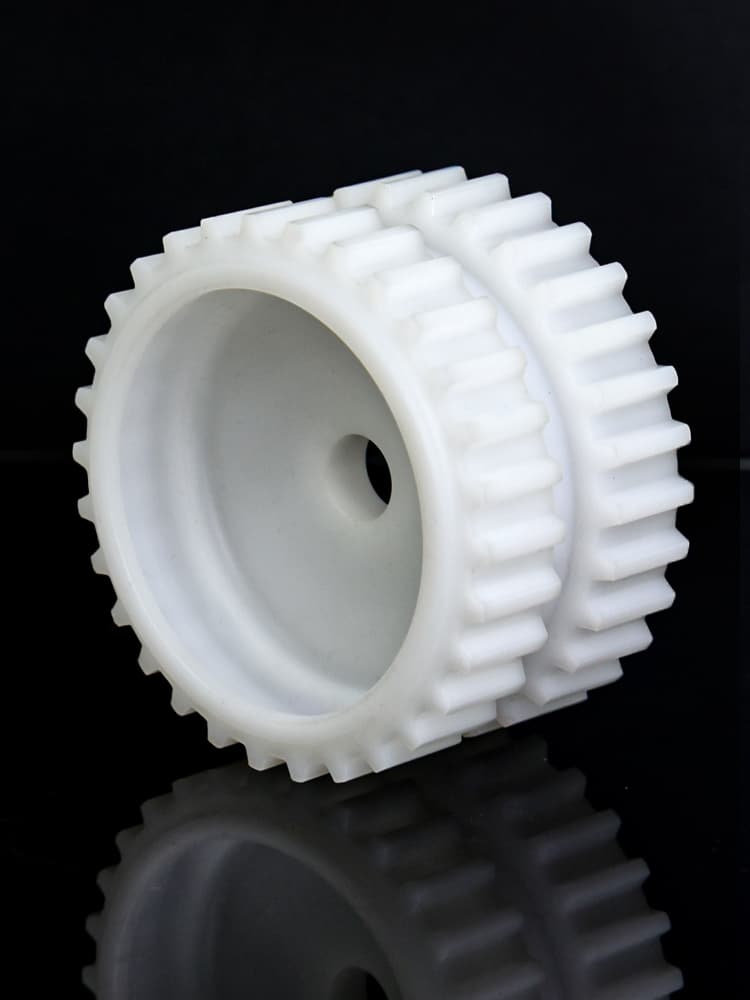
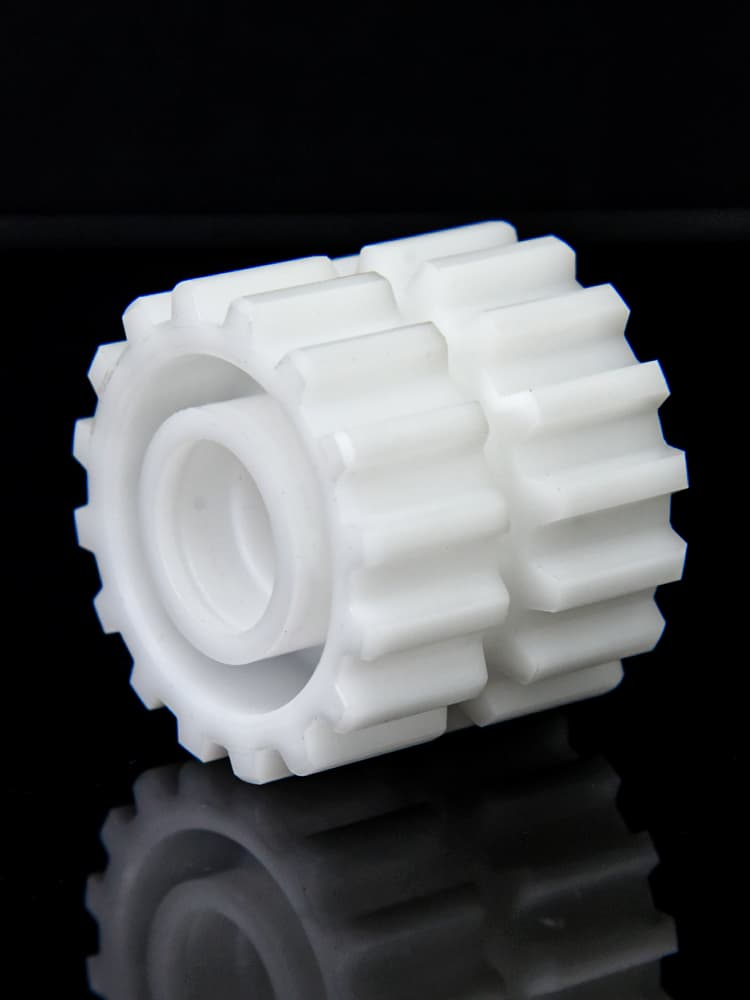
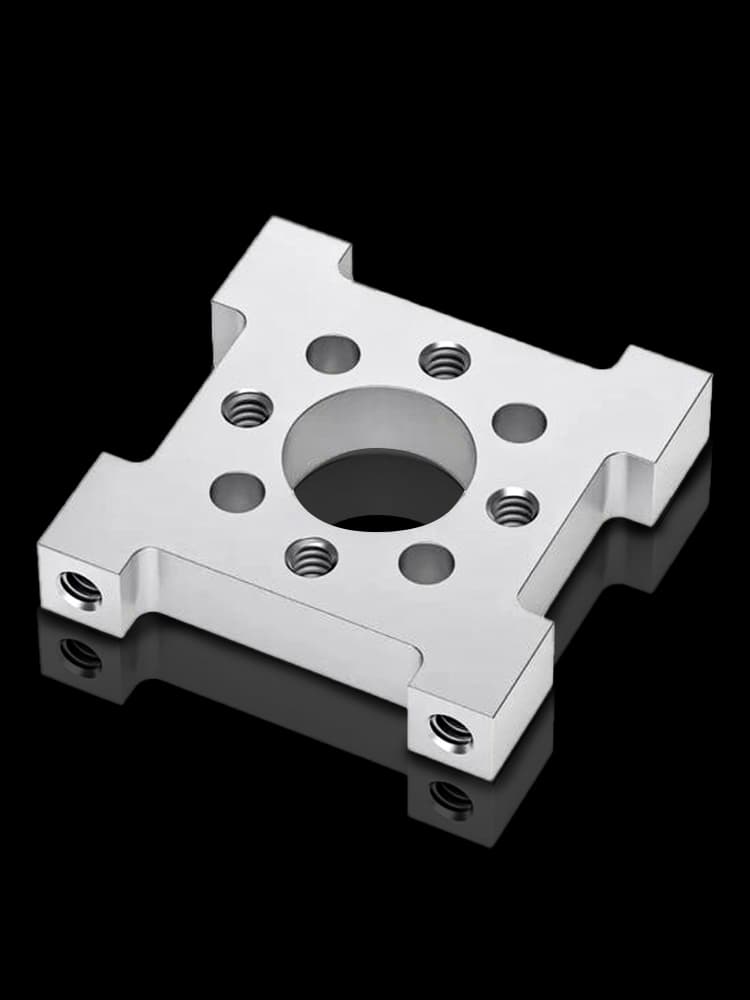
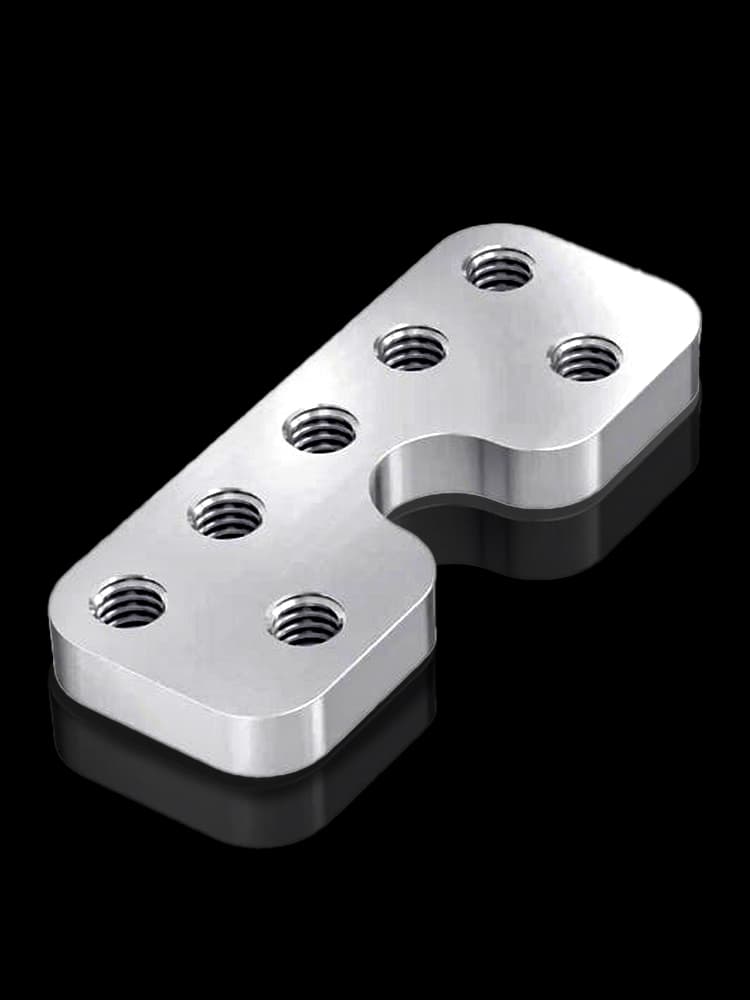
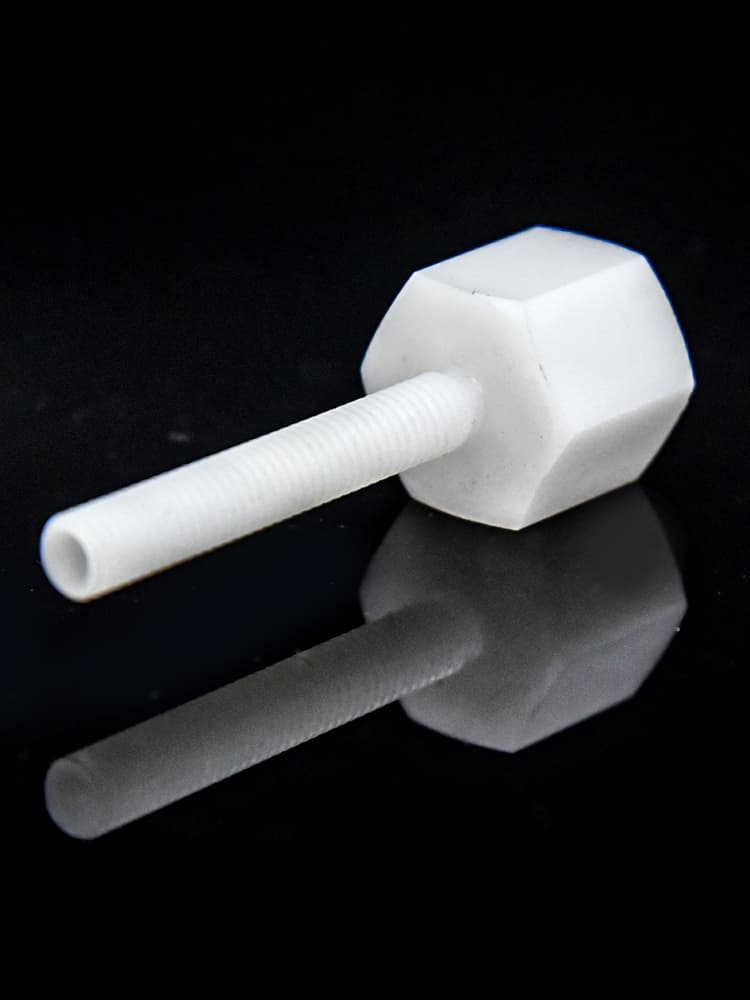
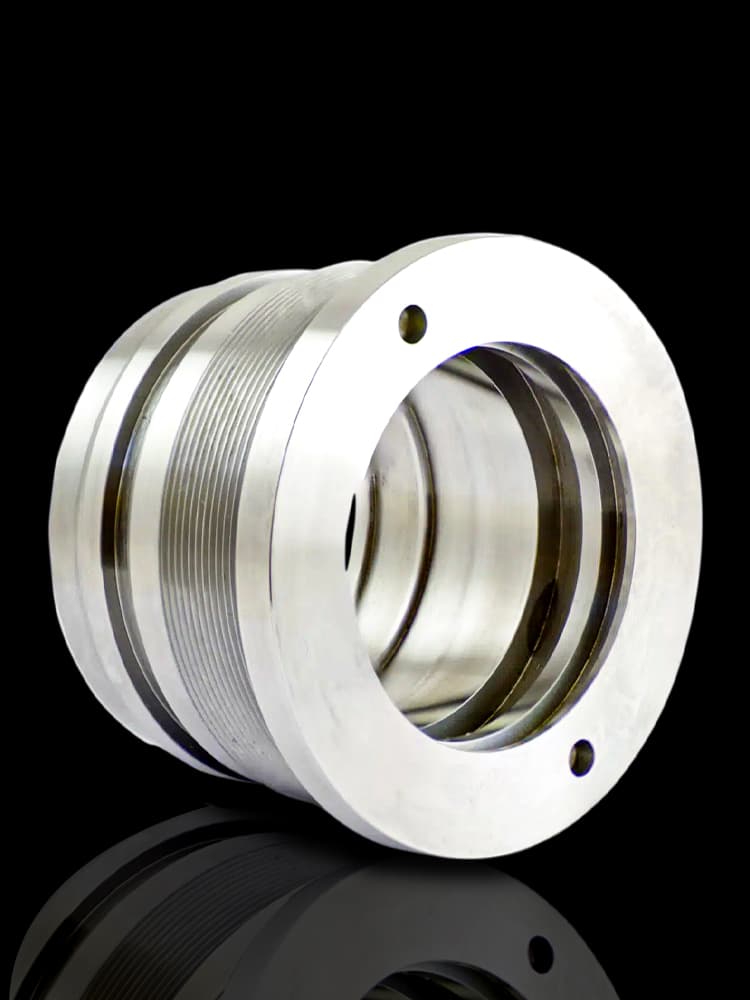
Our Partners
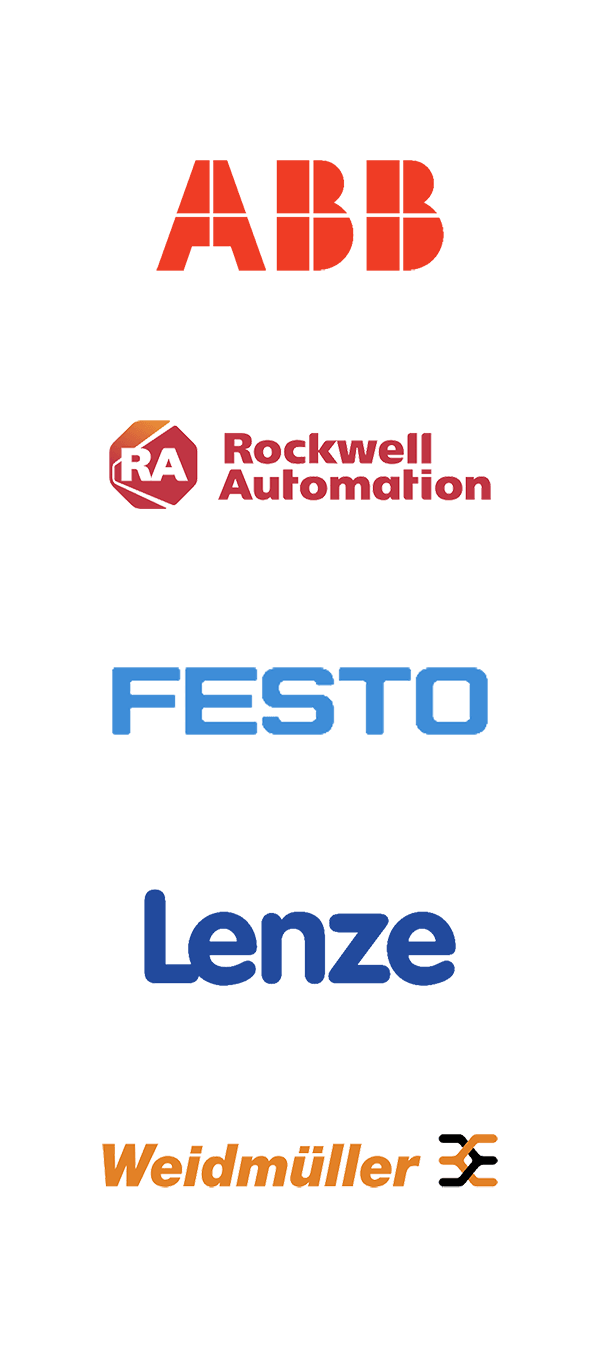
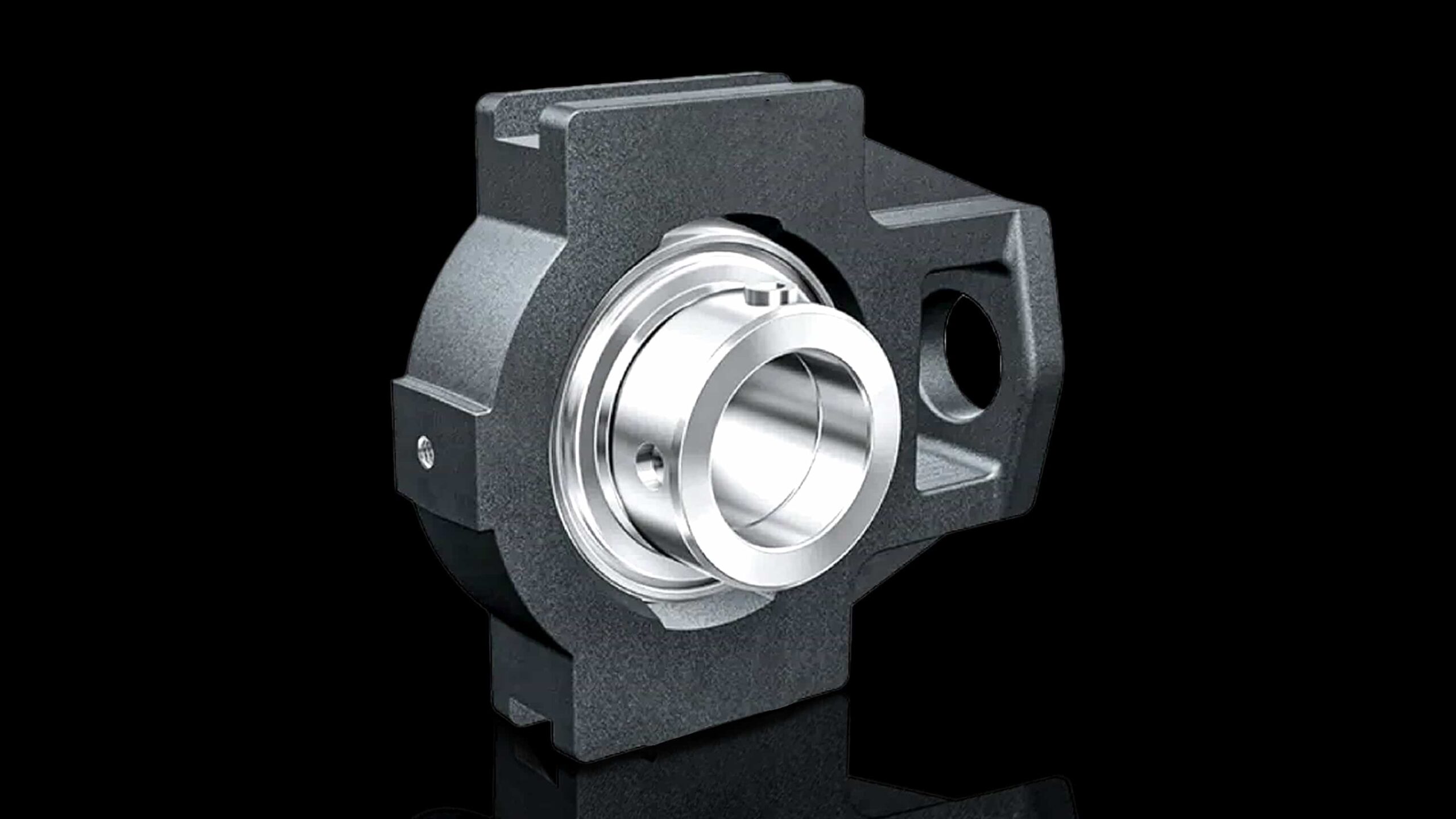
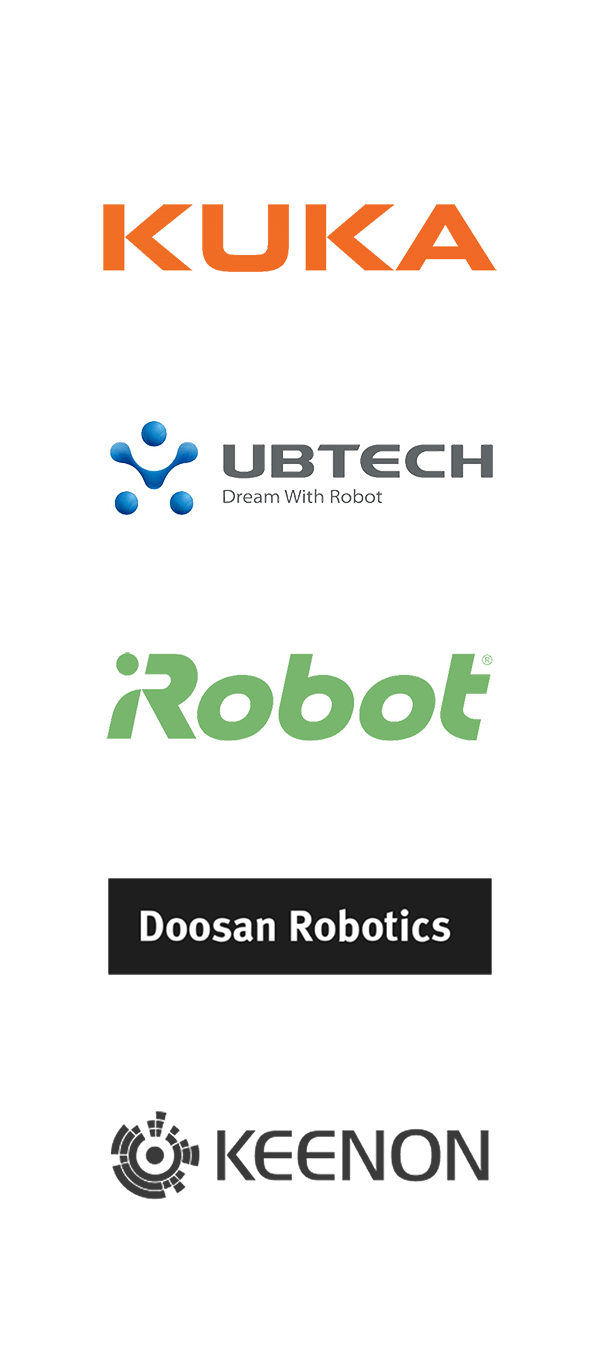
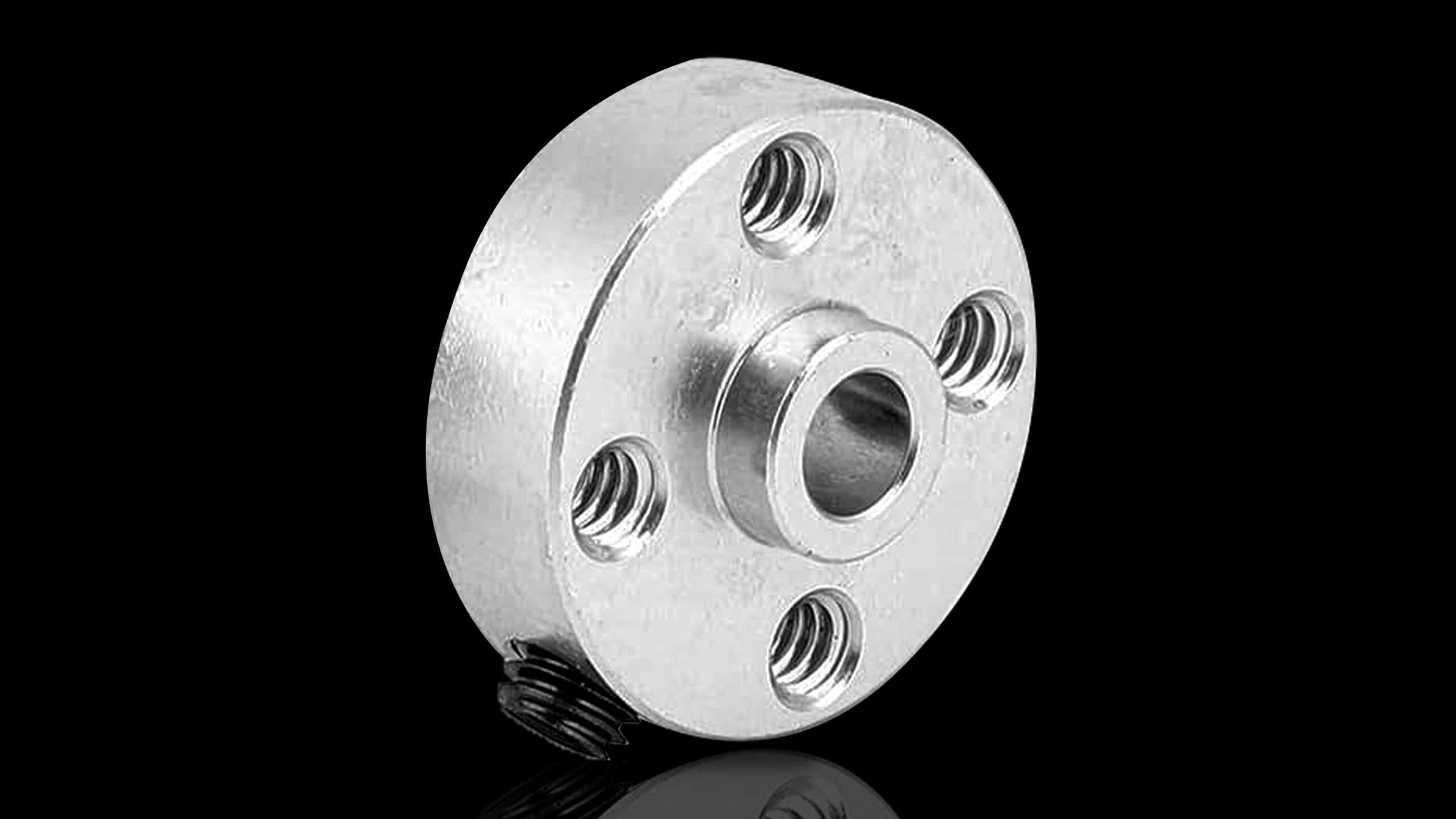
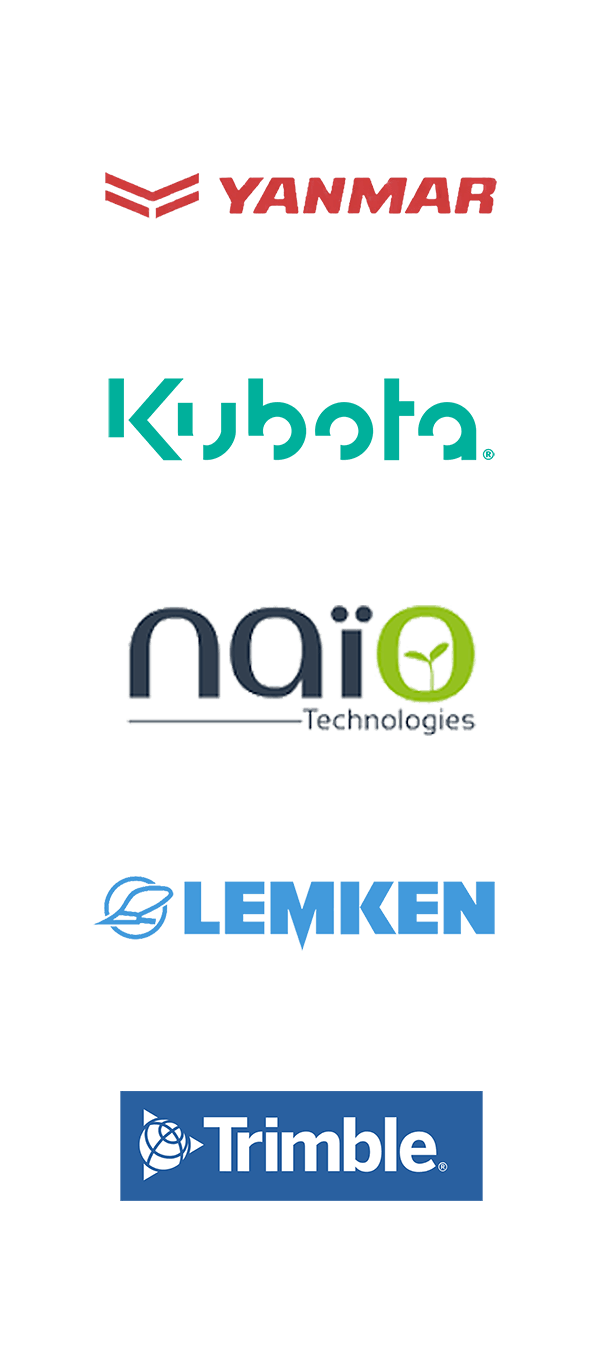
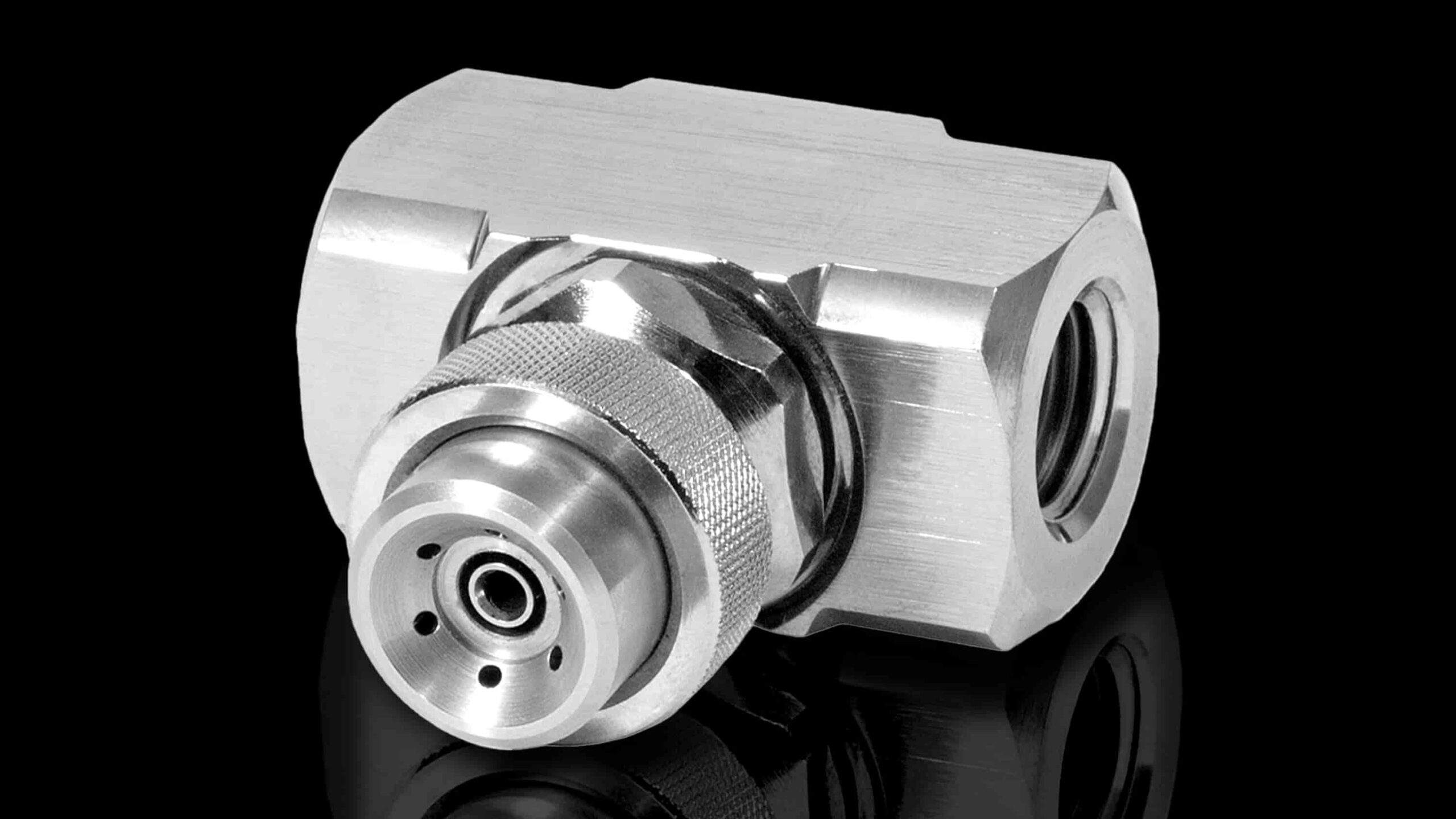
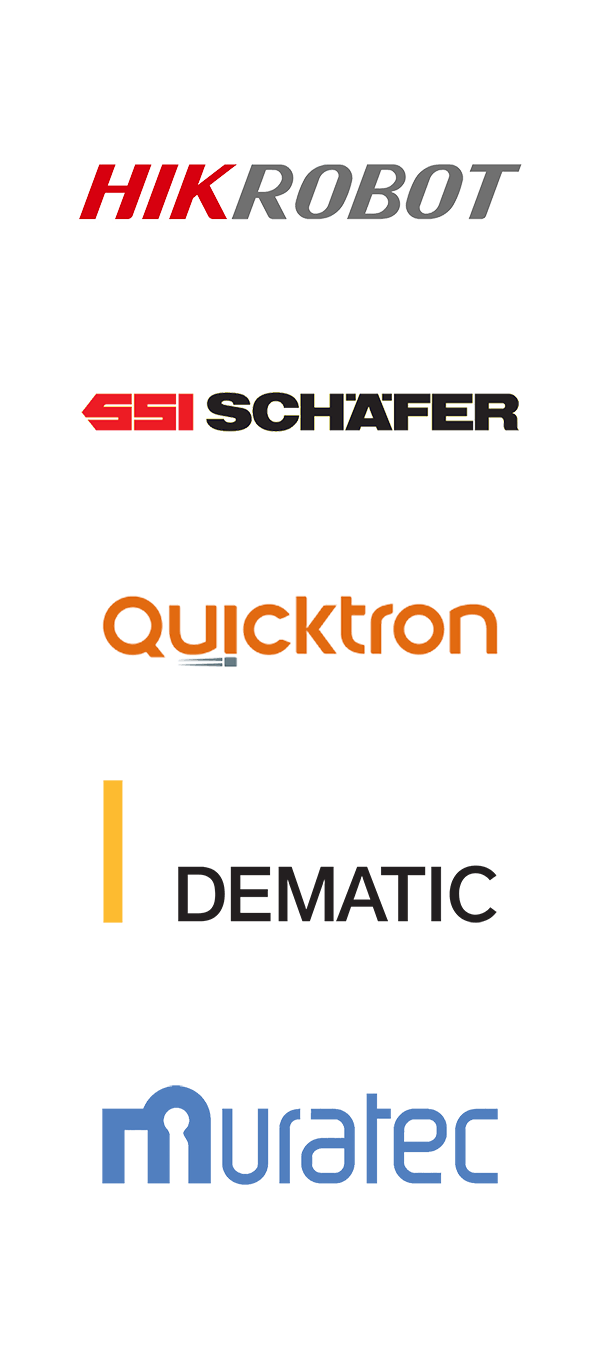
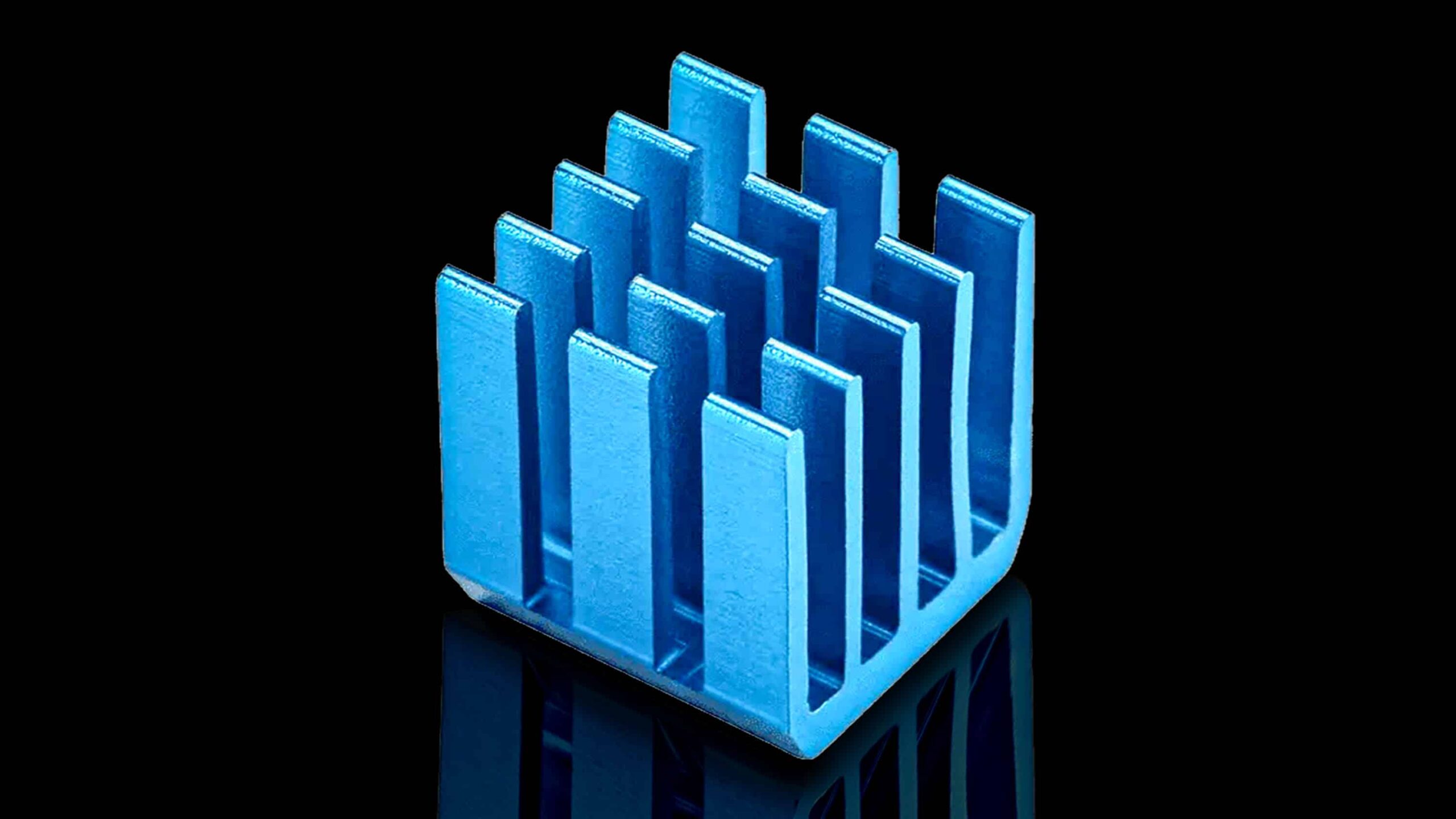
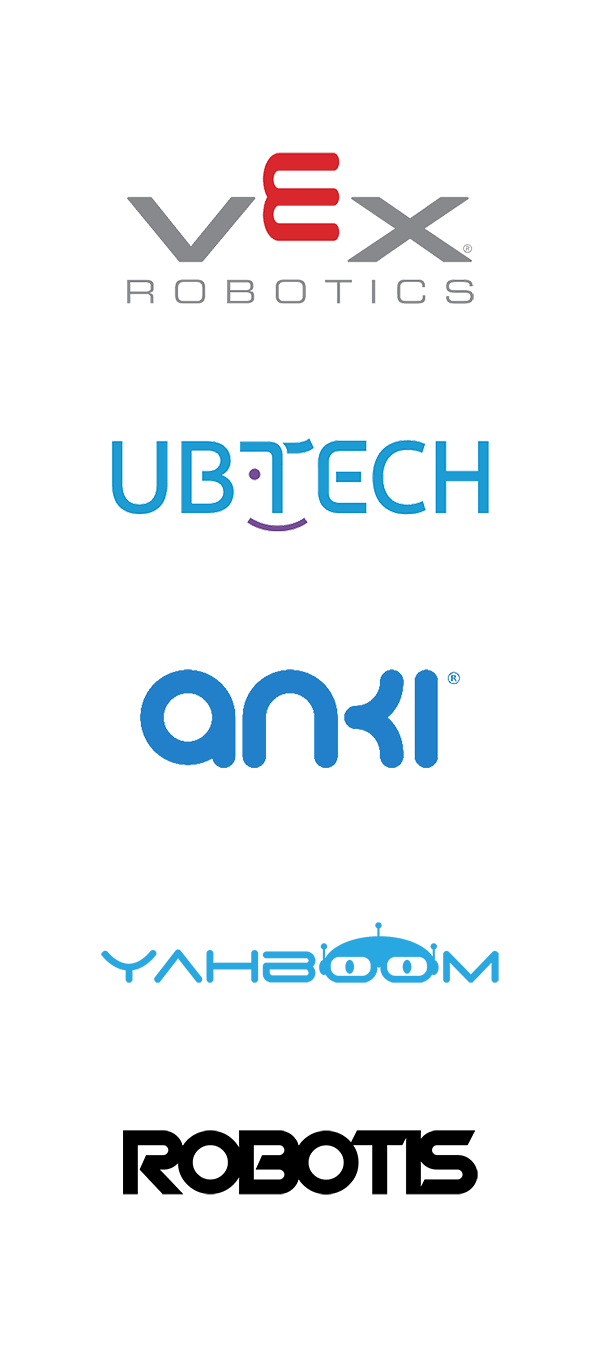
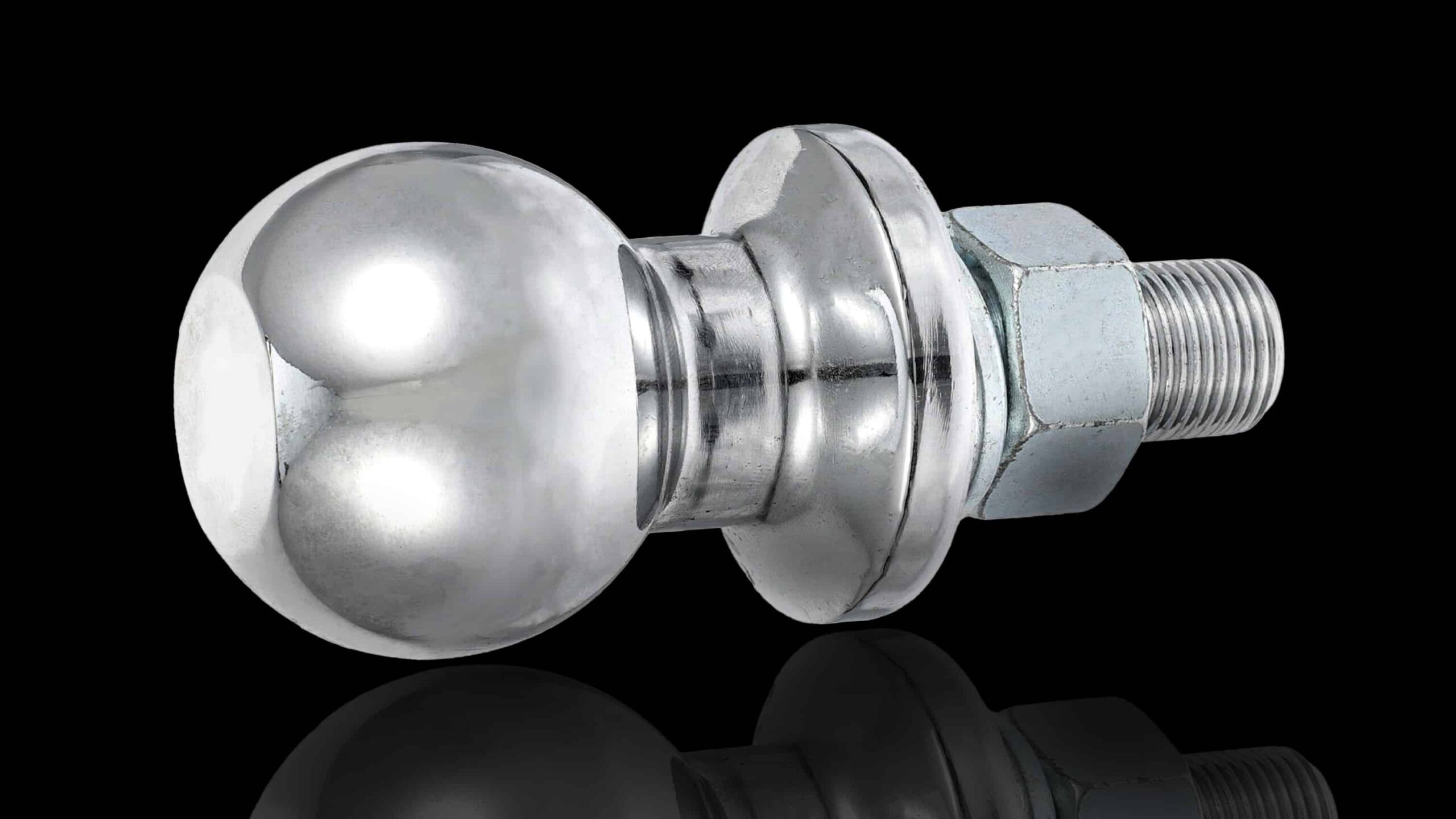
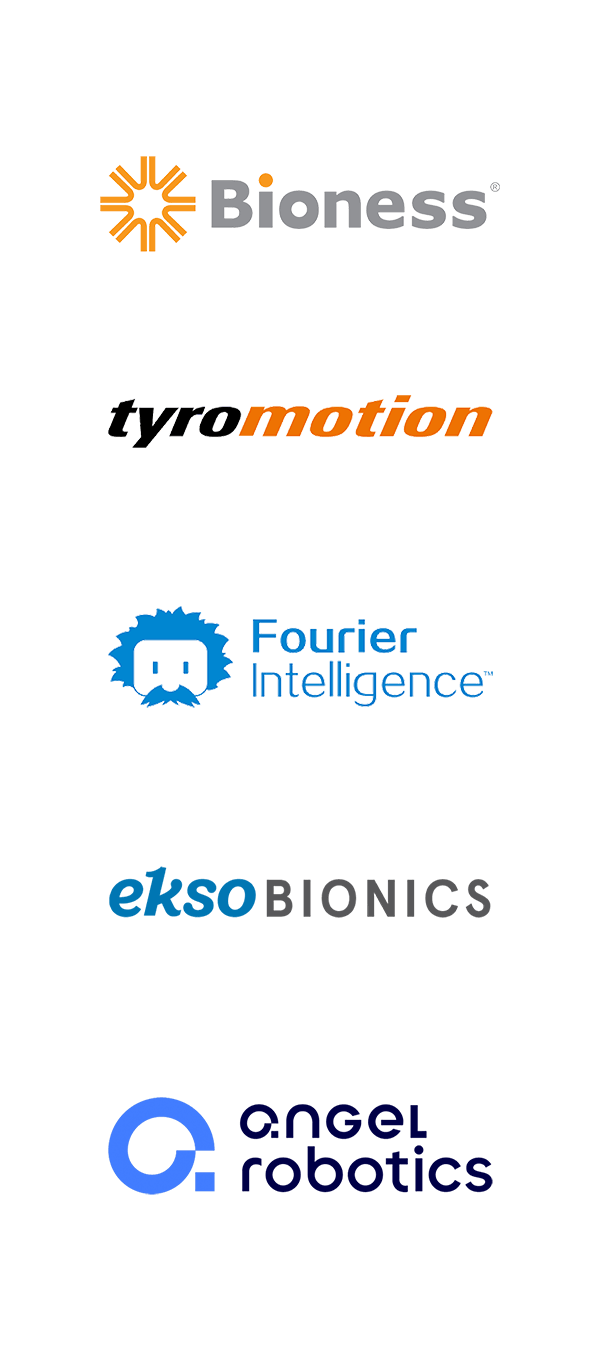
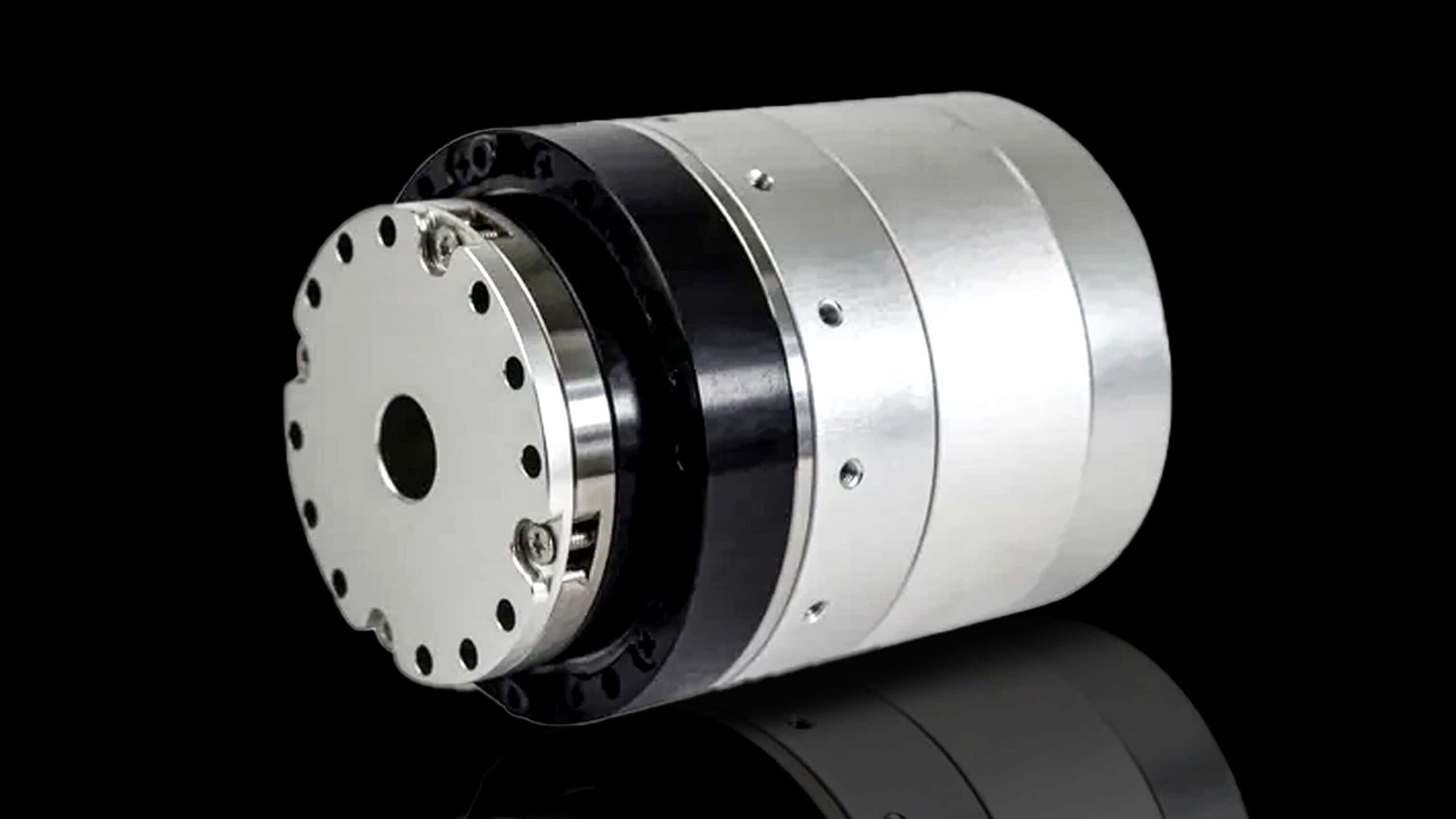
Automation & Robotics Industry Engineer Bella from Xielifeng has something to say
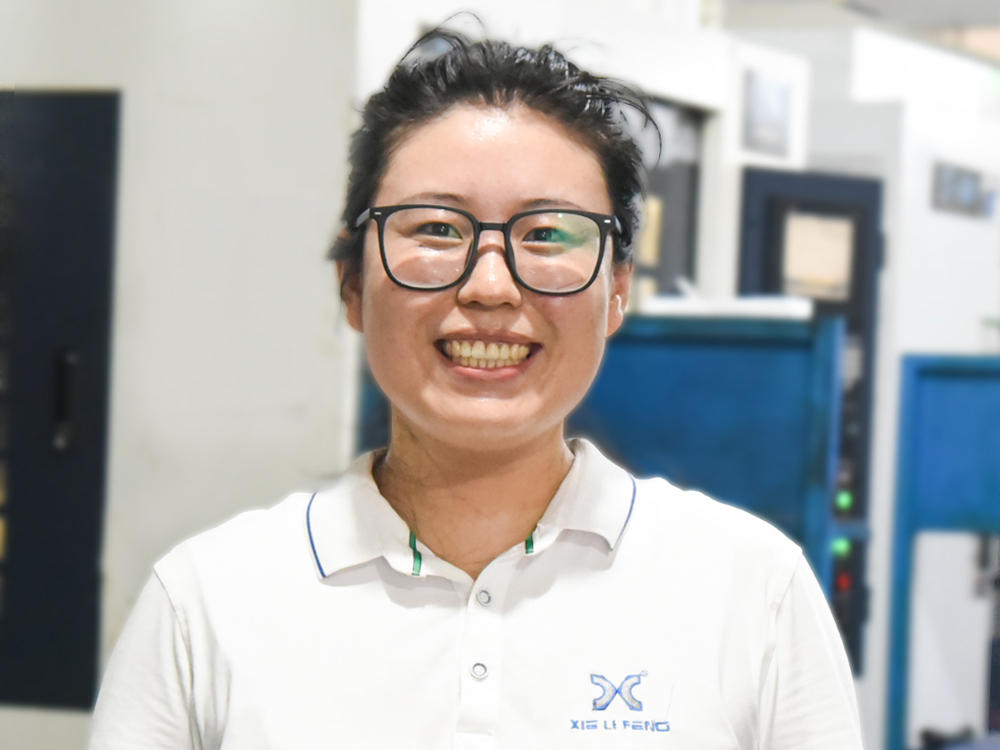
Senior Engineer Bella, 9 years of experience in machining precision components for automation systems and robotics. Specialized in robotic arms, precision gears, and motor shafts, ensuring high reliability and smooth movement in complex automation systems.
What materials do you recommend for robotic components requiring durability and lightweight properties?
We recommend aluminum alloys for their excellent strength-to-weight ratio, ideal for robotic arms and frames. Stainless steel is often used for gears and joints due to its wear resistance. For applications requiring flexibility and low friction, engineering plastics like POM and PTFE are ideal choices.
How do you maintain precision for complex robotic gears and joints?
We use 5-axis CNC machines to achieve complex geometries with tolerances as tight as ±0.01 mm. To prevent backlash in robotic joints, we carefully control gear meshing and use post-assembly alignment checks. Our inspection team performs CMM-based dimensional checks to ensure every part meets precise specifications.
What are the main challenges in machining robotic end effectors?
The primary challenge is balancing strength and dexterity. End effectors, such as grippers, require both precision and lightweight materials to ensure fast and accurate movements. We use light alloys and composites to reduce weight and apply surface treatments to enhance grip and wear resistance.
How do you ensure smooth operation and minimize wear in moving parts?
We machine components to tight tolerances to ensure proper alignment and smooth movement. For rotating parts, we recommend using low-friction materials such as POM or PTFE. Additionally, we apply lubrication channels during machining and conduct wear testing to validate the component’s longevity.
How do you ensure precision in machining robotic parts that involve complex motion, such as joints and actuators?
We achieve precision through multi-axis CNC machining and custom toolpaths designed specifically for intricate components. For joints and actuators, we ensure perfect concentricity and alignment to avoid binding or excessive friction during movement. Our engineers also conduct dynamic testing on prototypes to simulate real-world operations, verifying smooth performance before full production.
How do you ensure long-term reliability for components used in robotics?
We conduct extensive durability testing, including fatigue tests and life cycle analysis, to ensure that components can withstand repeated use. We also apply protective coatings to prevent corrosion and wear, particularly for outdoor or industrial environments. Regular quality checks throughout production ensure that every component meets strict reliability standards.
How Xielifeng Works
From quotation to delivery, we provide efficient, high-quality services, making manufacturing more convenient.
01
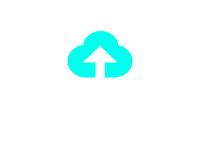
Upload drawing
CAD files: 2D: DXF | DWG | PDF 3D: STP | STEP |IGS | IGES| X_T | SLDPRT
02
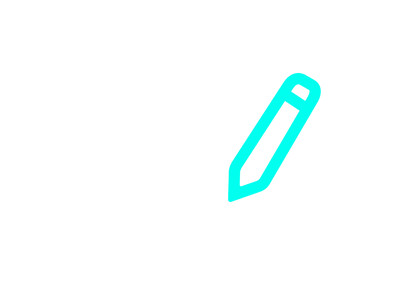
DFM Evaluation & Quote
- Drawing review
- Process analysis
- Material inspection
- Feasibility proposal
- Cost estimation
03
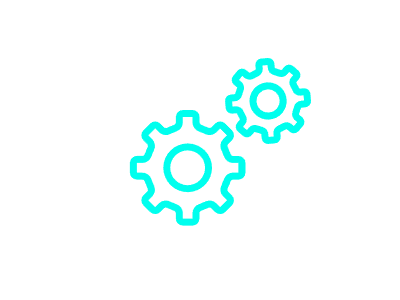
Order Confirmtion & Production
- Sample processing
- Sample quality inspection
- Customer confirmation
- Mass production plan
04

Quality Inspection & Delivery
- Raw material inspection
- First piece inspection
- Process inspection
- Final inspection
- Inspection report