Xielifeng Precision Machining for Aerospace & Aviation Excellence – Where Safety Meets Innovation.
All uploads are secure and confidential.* Learn More
IOS 9001
IOS 14001

About Our Capabilities
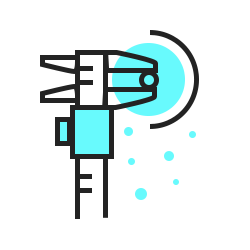
High Precision, Ensuring Flight Safety
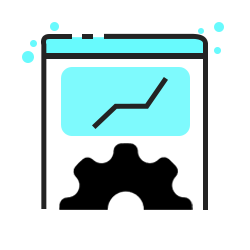
Comprehensive Quality Management

Long-Term Stable Partnerships
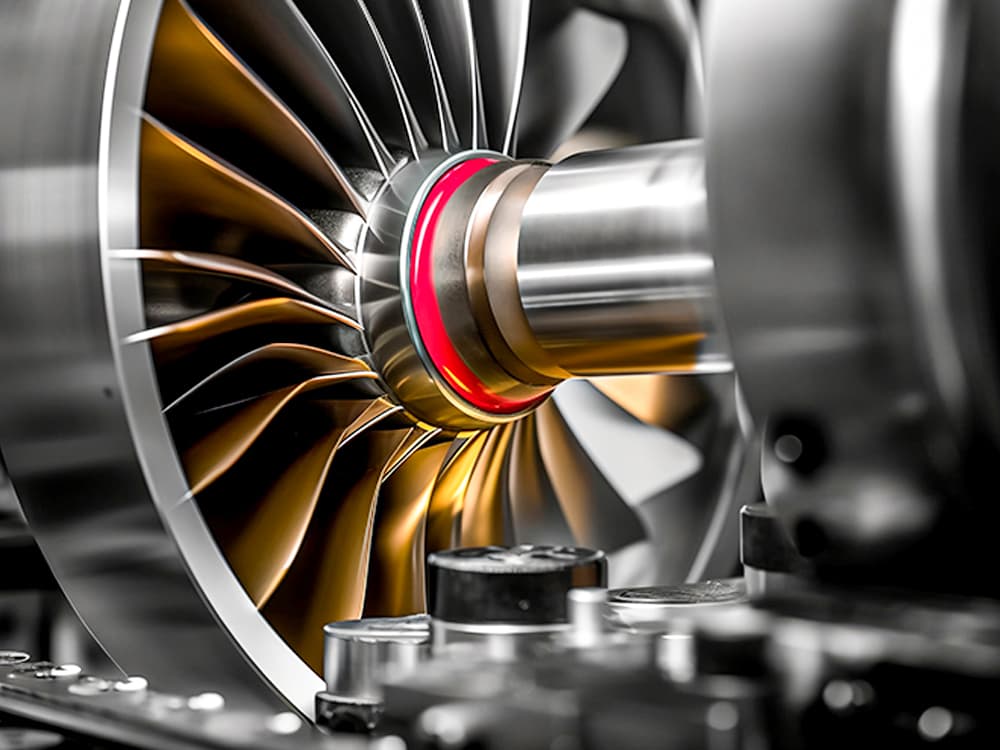
High Precision, Ensuring Flight Safety
We specialize in machining aerospace components with a tolerance of ±0.002mm, such as turbine blades and structural brackets. We ensure safety and stability in critical applications with an annual production of over 50,000 parts.
Comprehensive Quality Management and Zero-Defect Delivery
Through full-process quality traceability and strict inspection standards, our parts achieve a 99.95% pass rate, meeting the most rigorous aerospace certifications and ensuring reliability when it matters most.
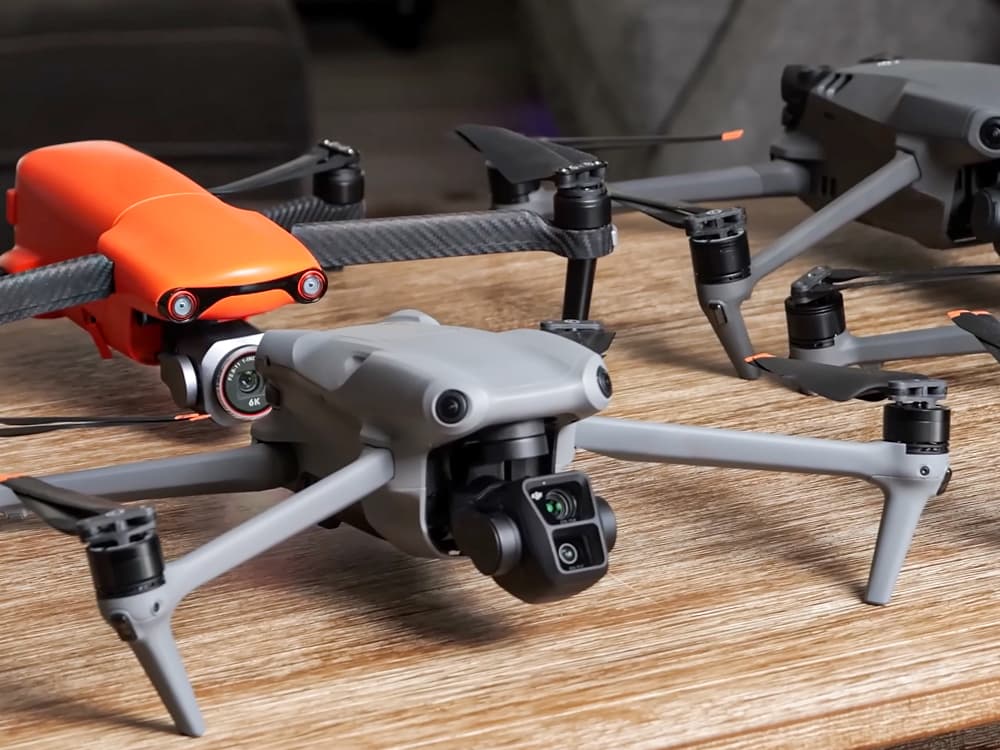
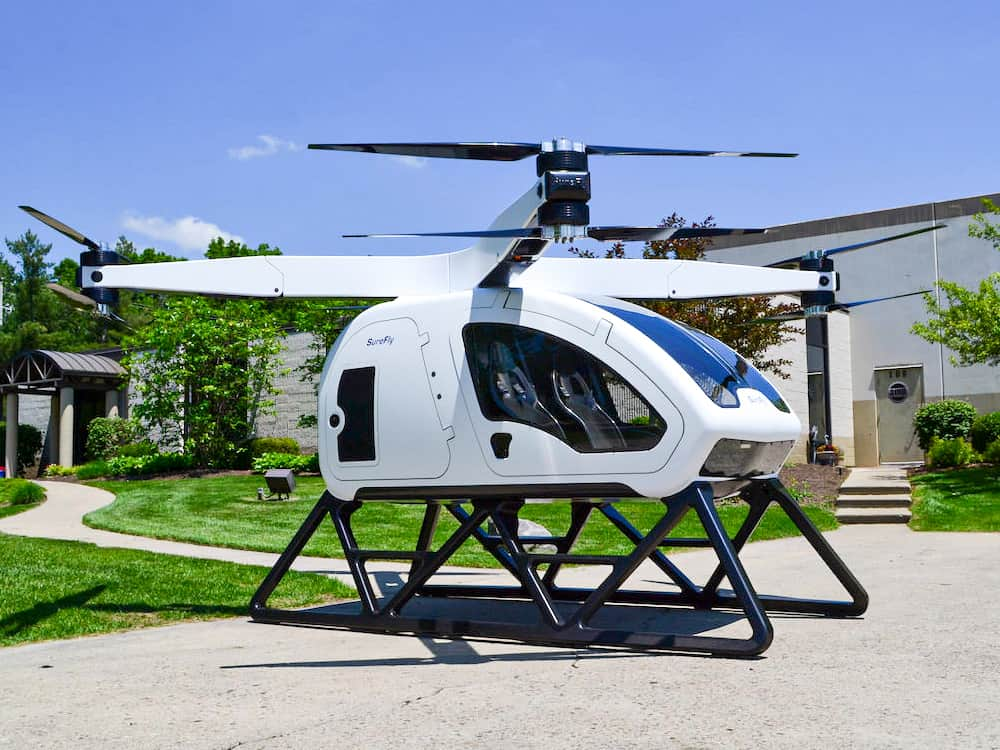
Long-Term Stable Partnerships and Continuous Support
We maintain long-term partnerships with major global aerospace companies, delivering over 100,000 precision parts annually with a 98% on-time delivery rate, supporting our clients’ competitiveness in global markets.
Application of parts for Aerospace & Aviation
Application Parts | Material | Surface Treatment | |||||||||
---|---|---|---|---|---|---|---|---|---|---|---|
Body structure | Aluminum | Anodizing | |||||||||
Cradle | Titanium Alloy | Heat Treatment | |||||||||
Turbine blades, compressor blades | Nickel Alloy | Coating (PVD, CVD) | |||||||||
Combustion chamber parts | Titanium Alloy | Heat Treatment | |||||||||
Gears, shafts | Stainless Steel | Chrome Plating | |||||||||
Couplings, connectors | Carbon Steel | Carburizing treatment | |||||||||
Control rods, hydraulic system components | Steel | Nitriding treatment | |||||||||
Sensor housings, electronic equipment housings | Aluminum | Anodizing | |||||||||
Antennas, waveguide components | Brass | Nickel Plating | |||||||||
Seat frames, luggage racks | Composite Materials | None | |||||||||
Fuel system parts, air conditioning system parts | Stainless Steel | Polishing, Nickel Plating | |||||||||
Ground support equipment, jigs | Steel | Heat Treatment |
CNC Aerospace & Aviation Parts Case Study
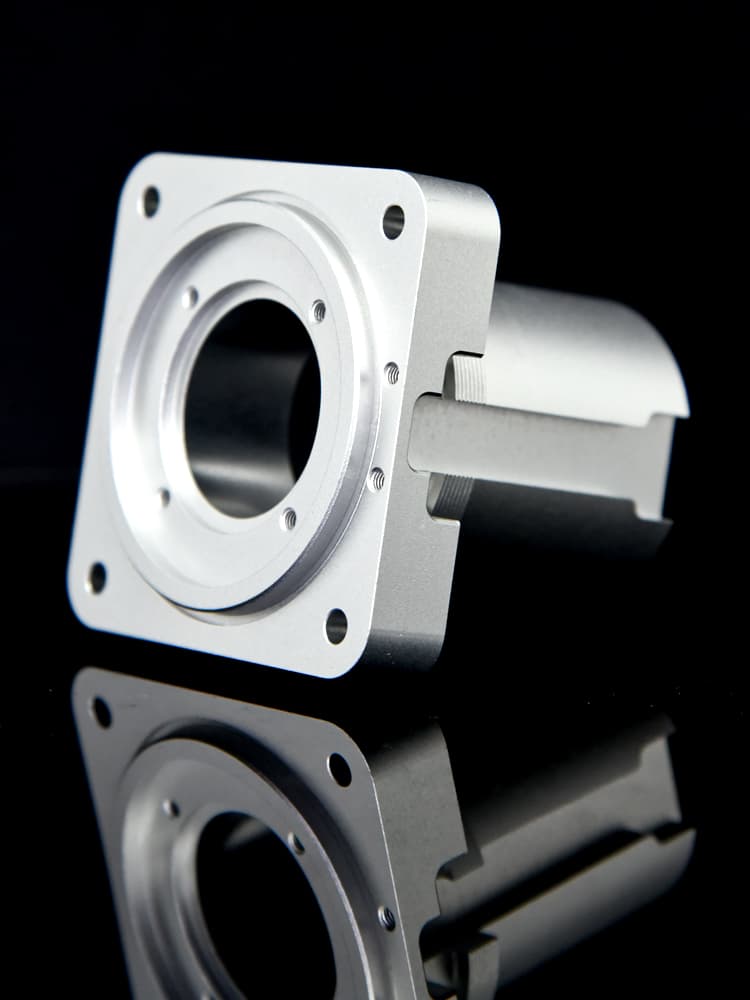
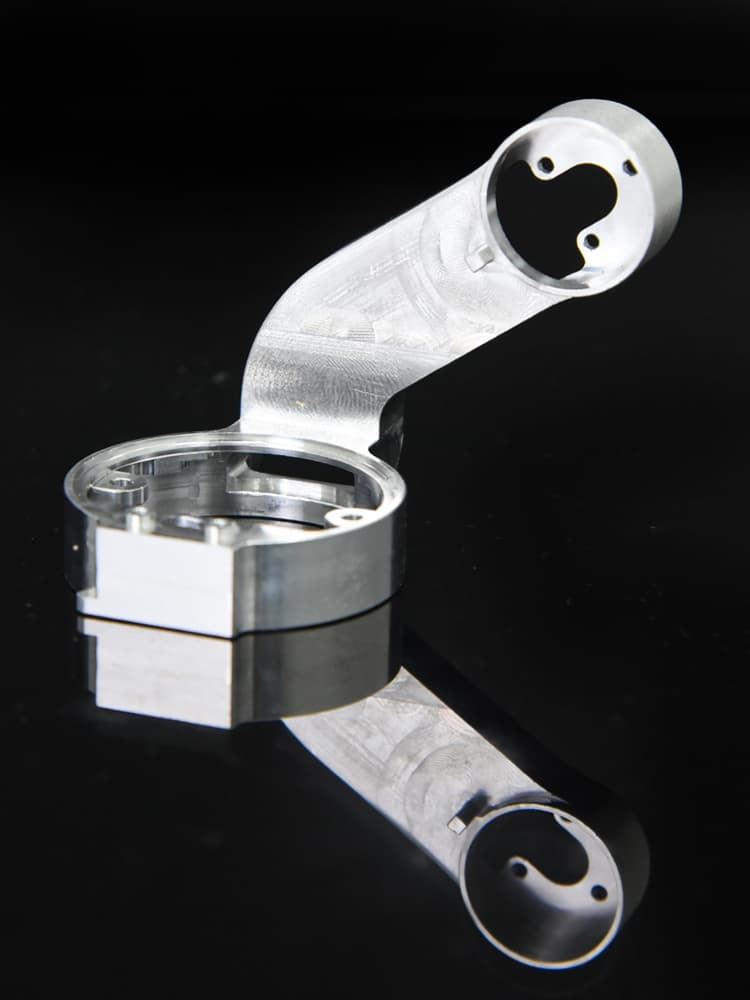
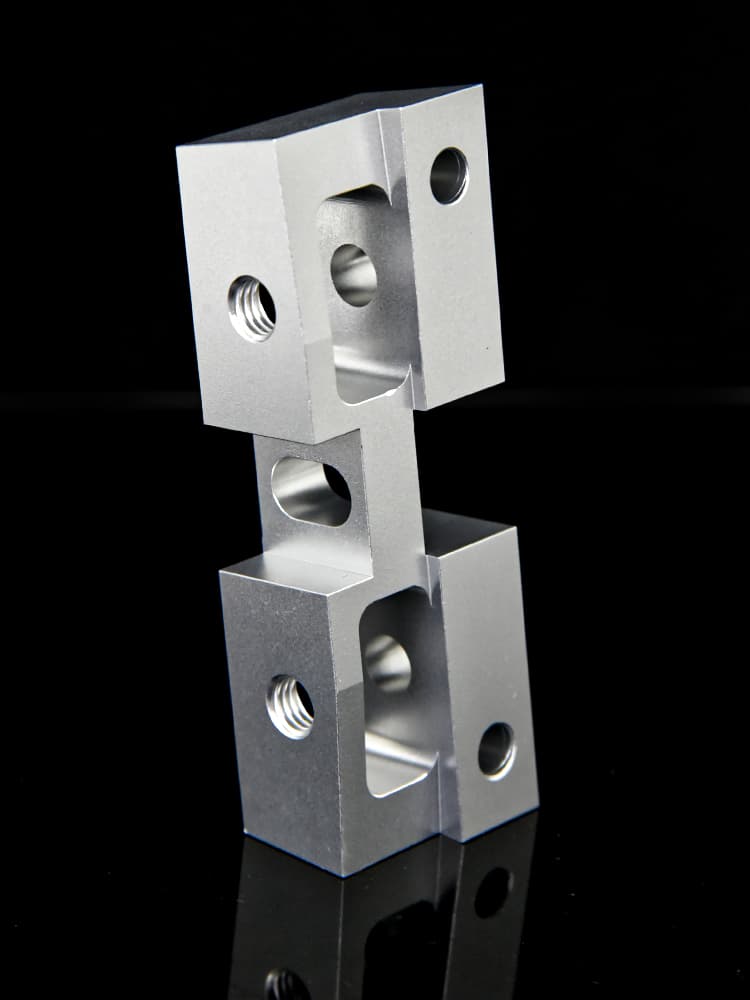
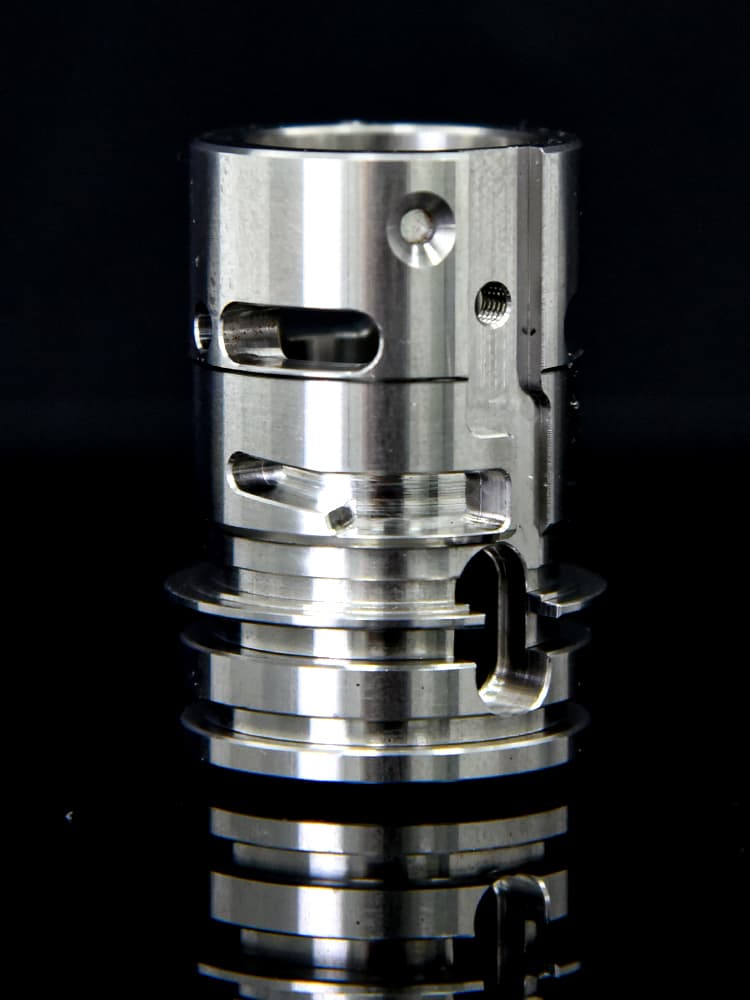
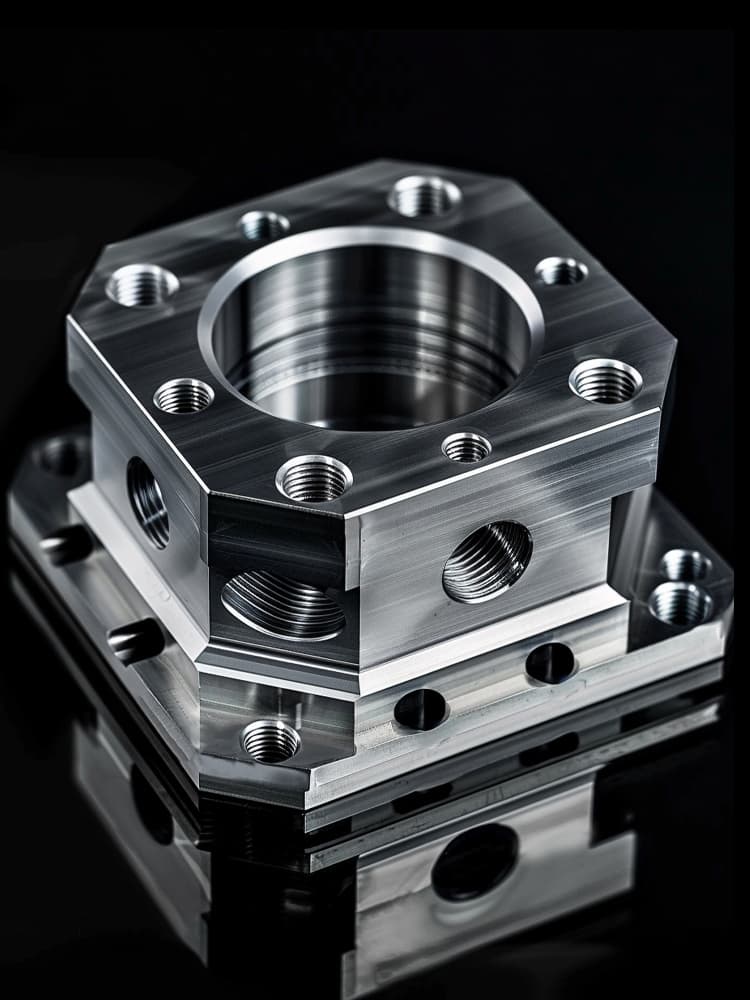
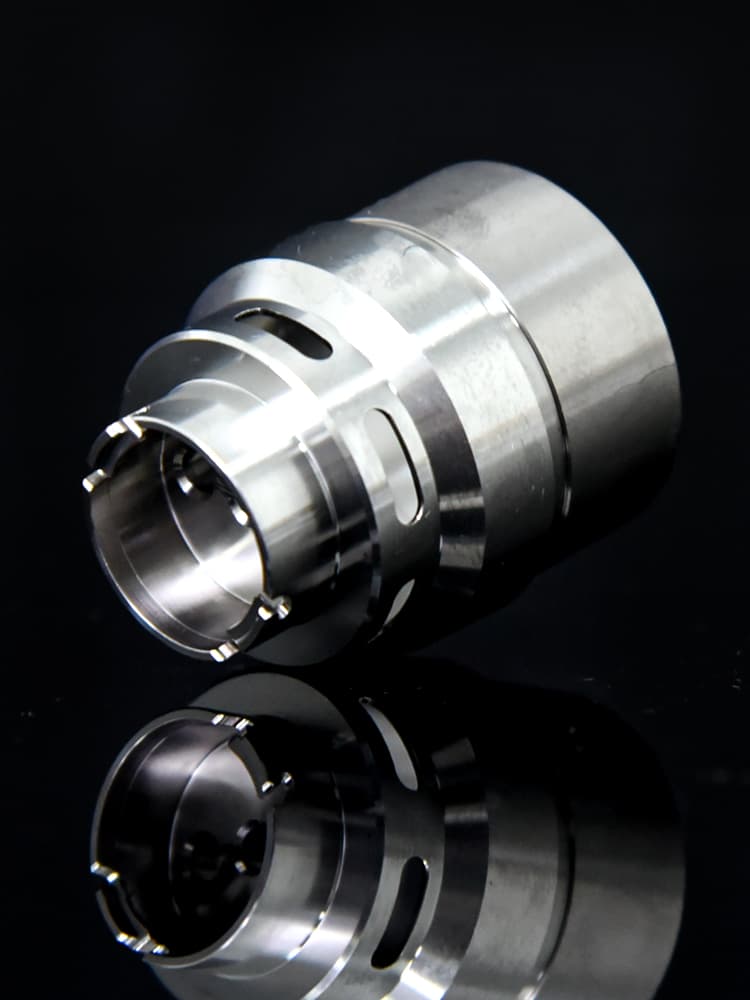
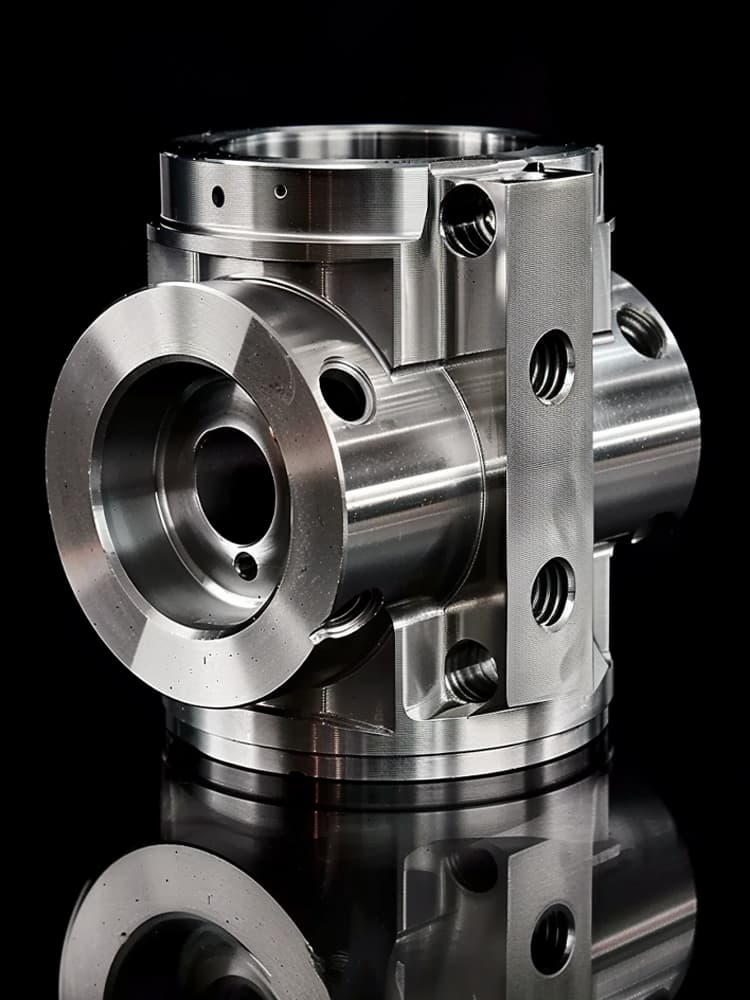
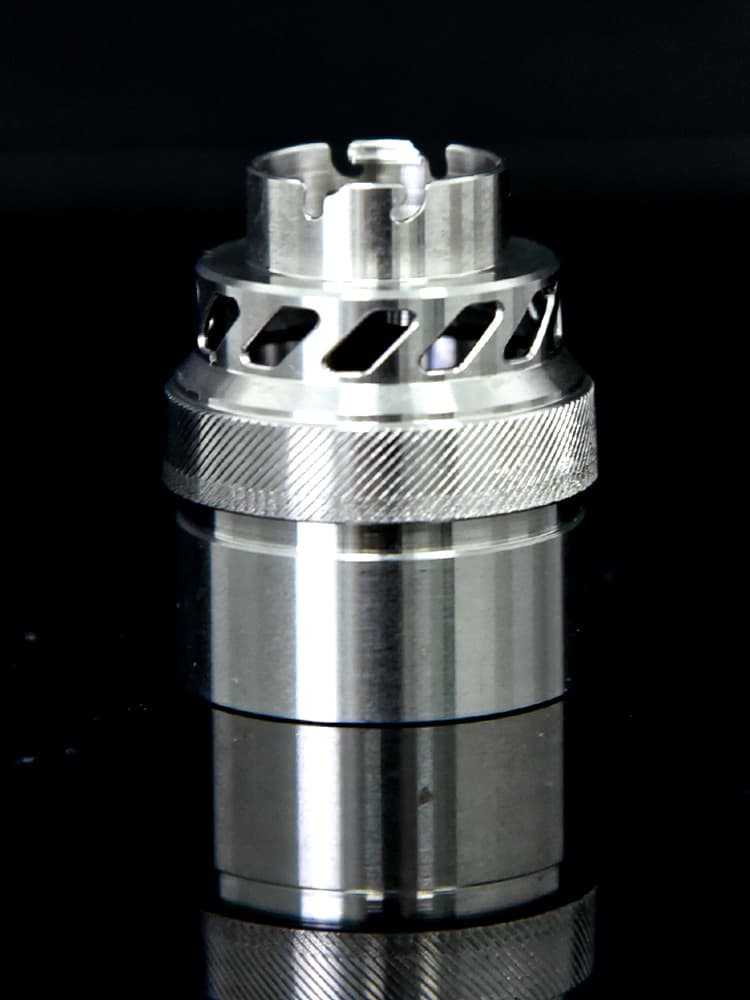
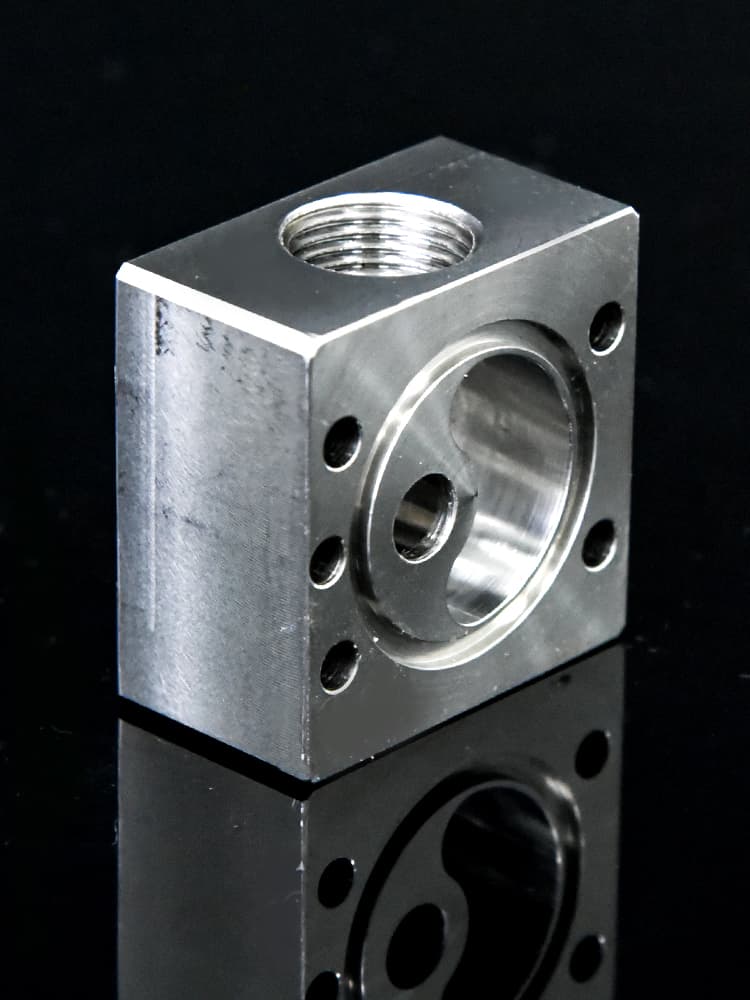
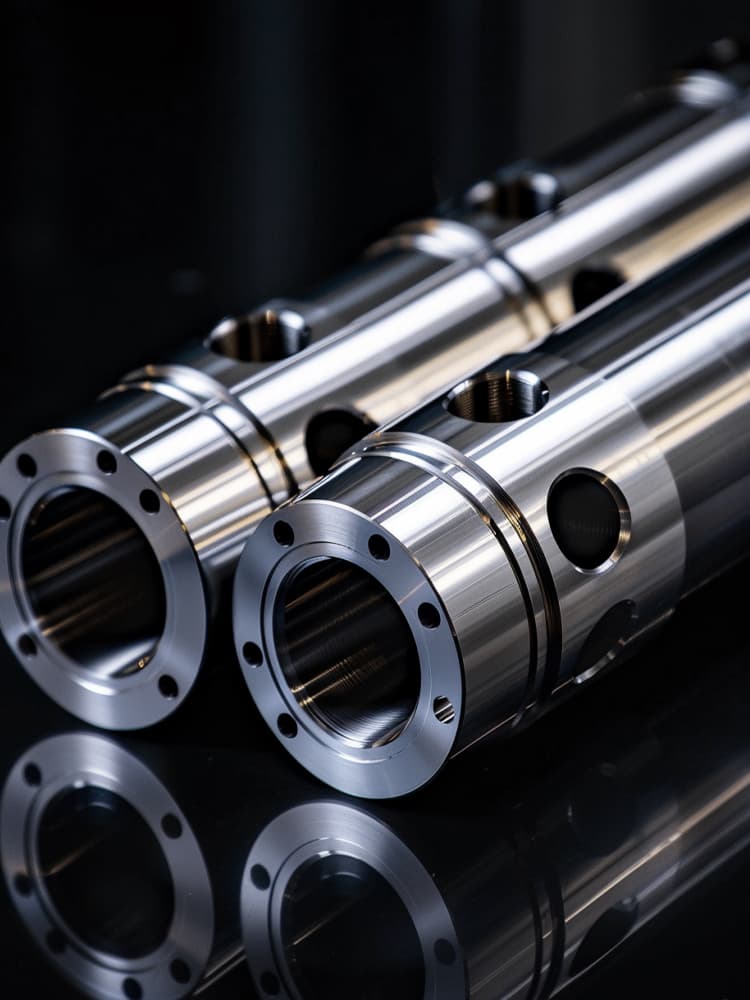
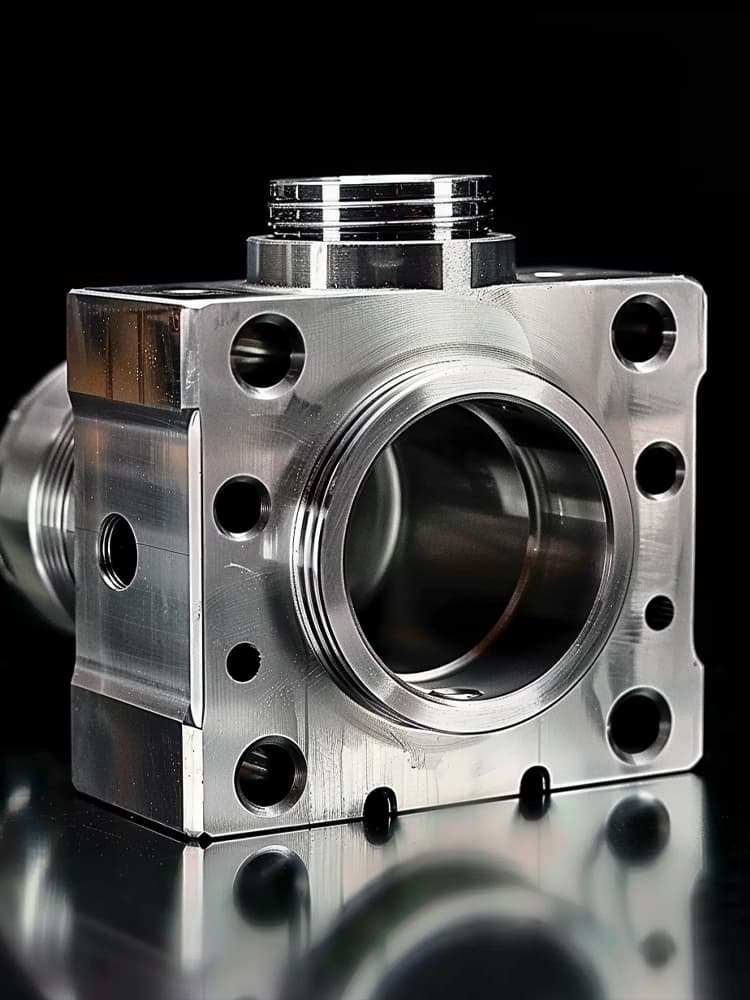
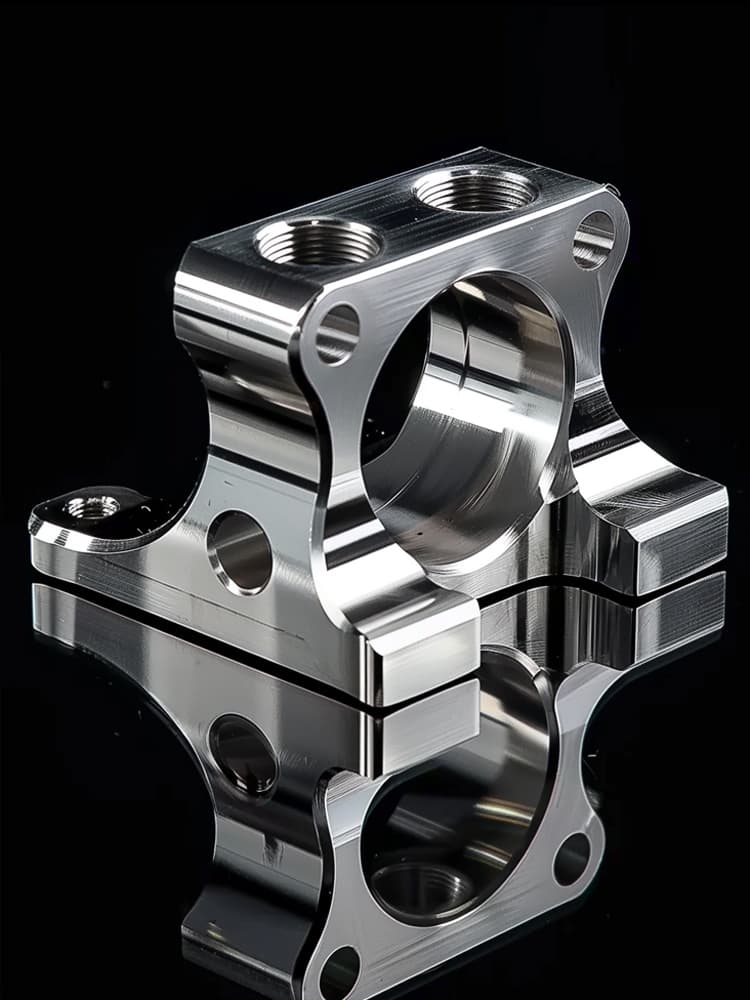
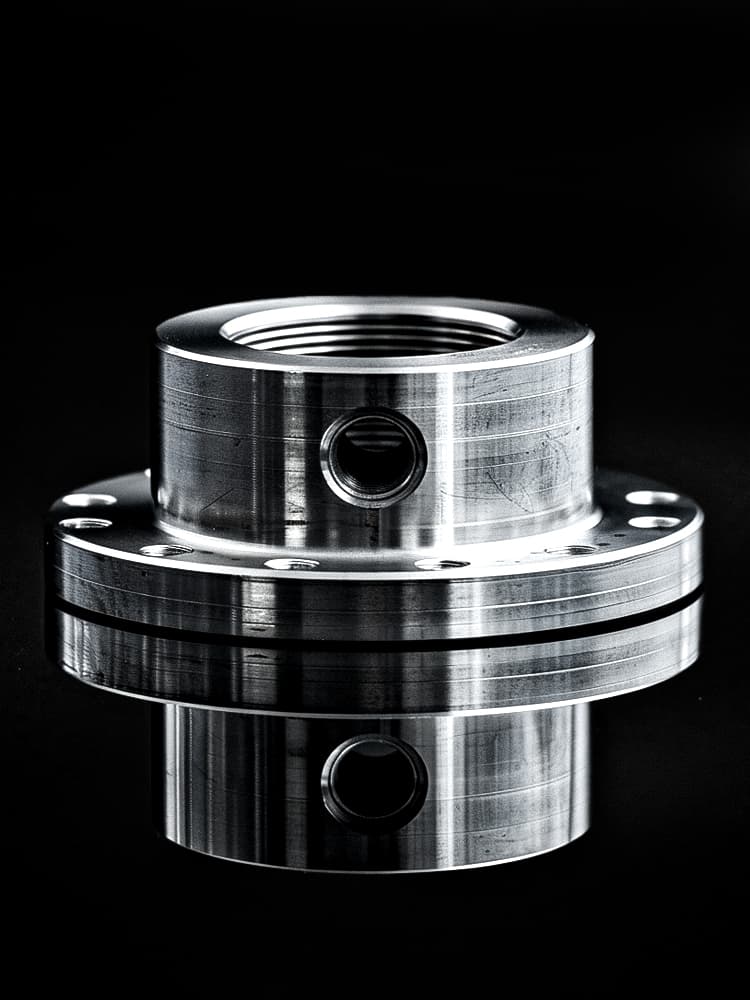
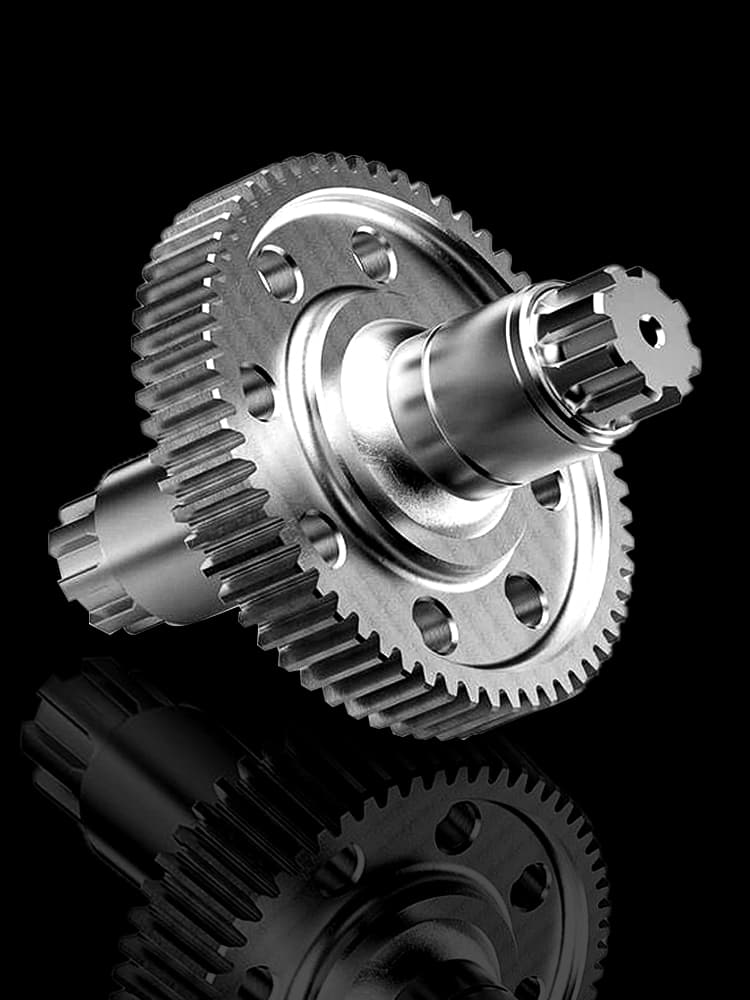
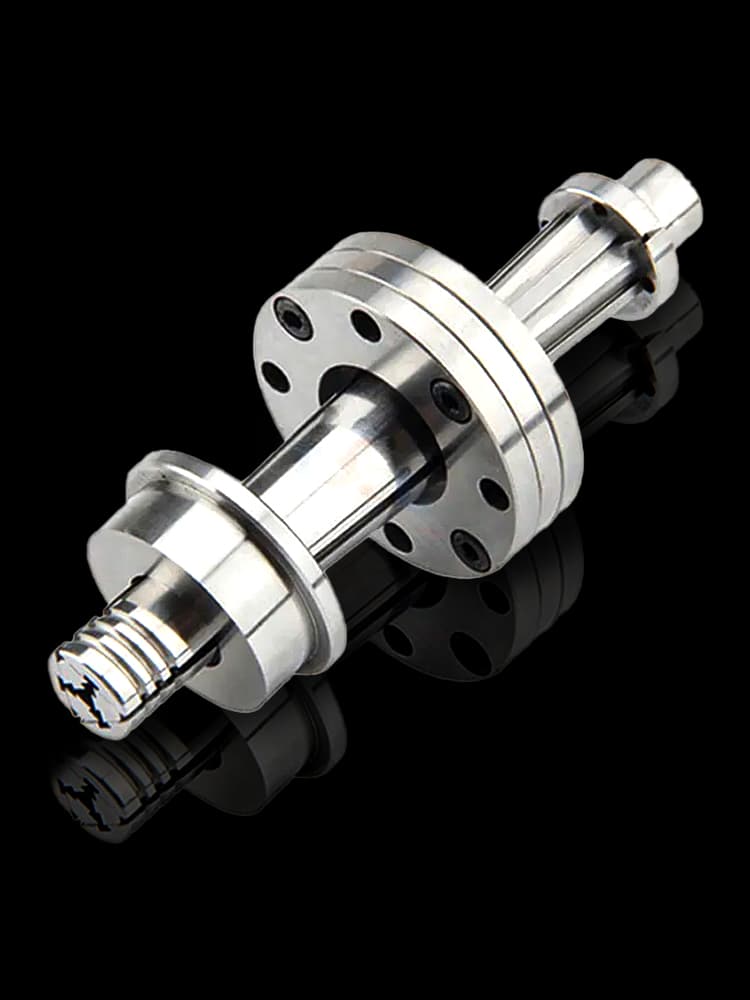
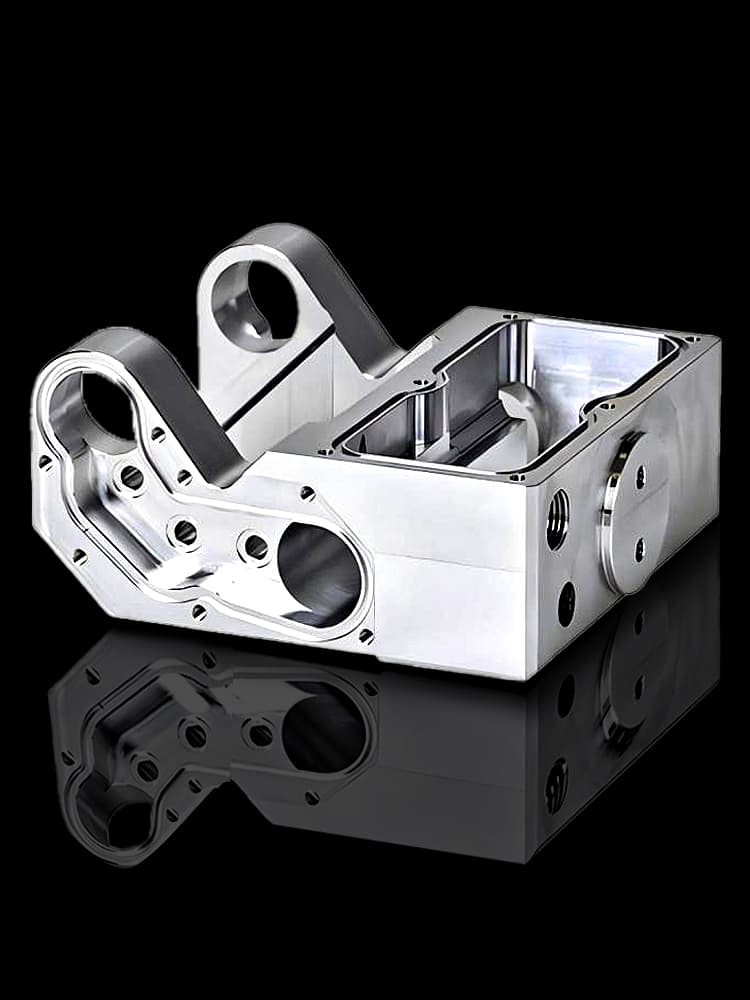
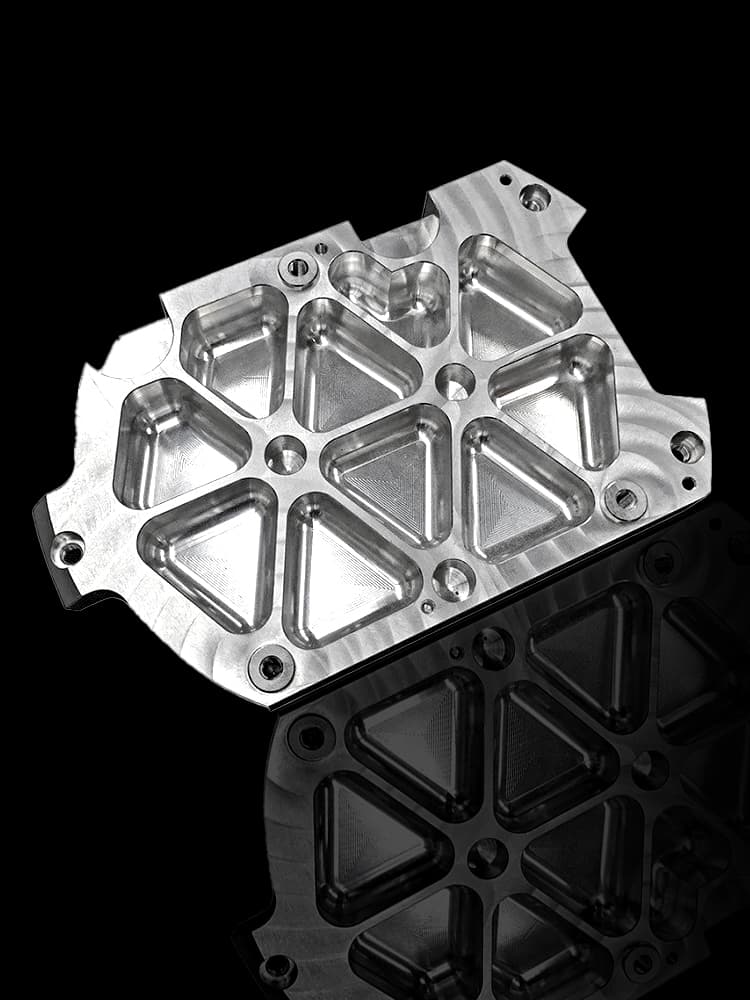
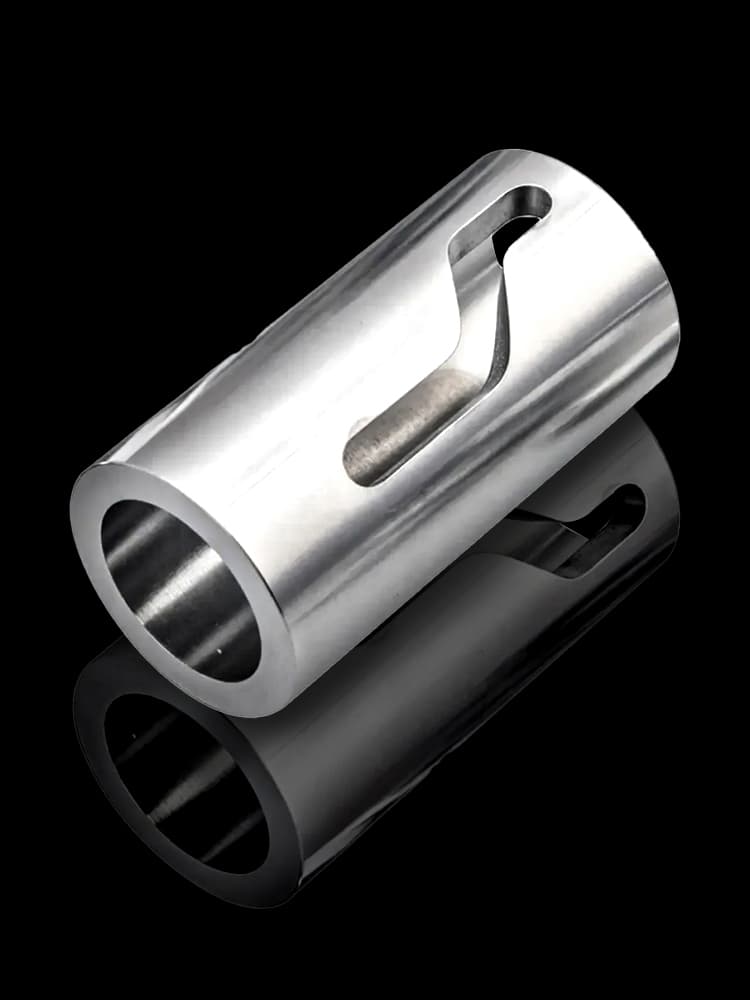
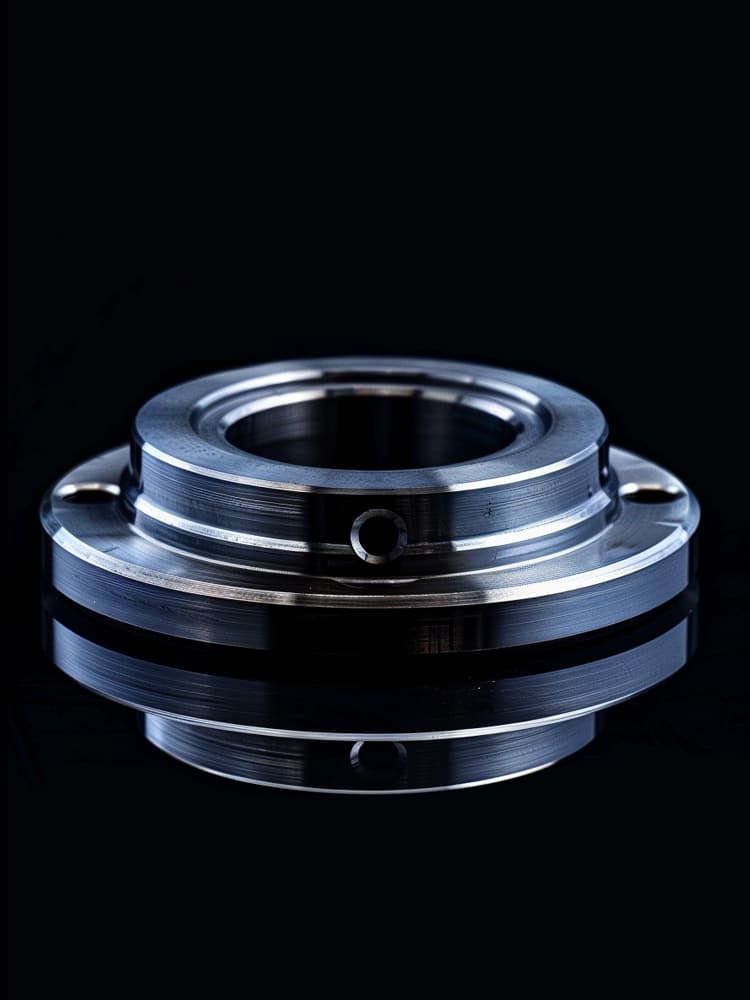
About the Parts We've Made
Aerospace components require high precision, reliability, durability, and the ability to withstand extreme environmental conditions. We have extensive experience in both material selection and machining processes.
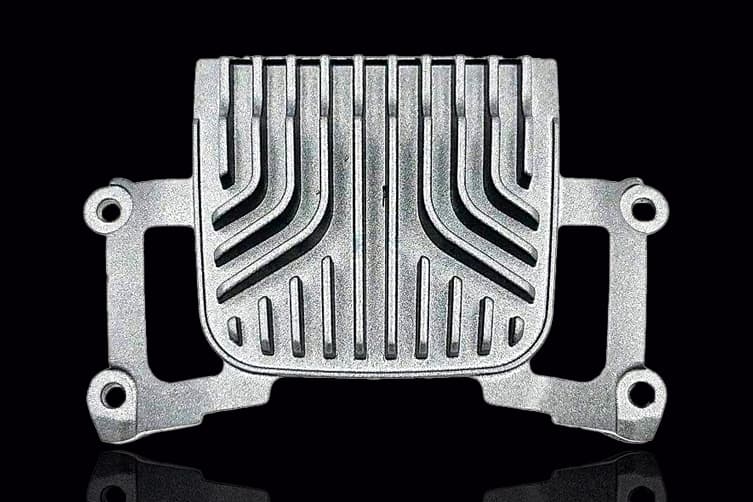
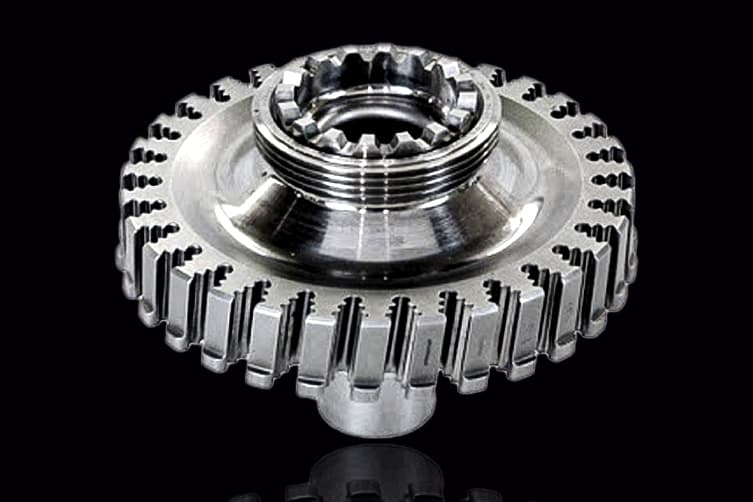
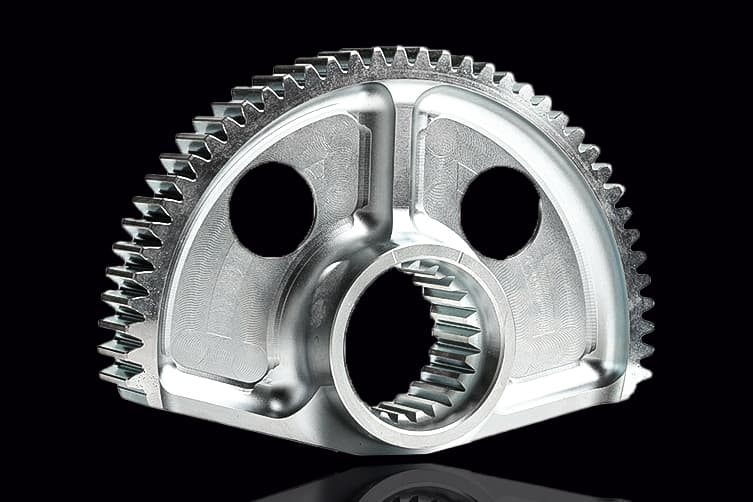
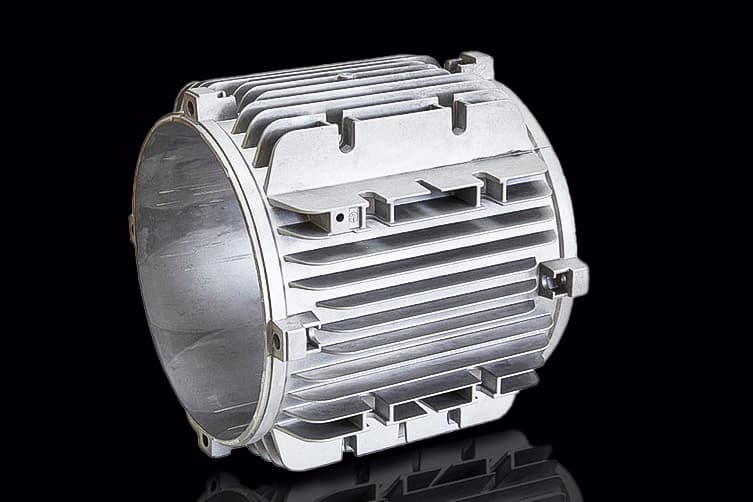
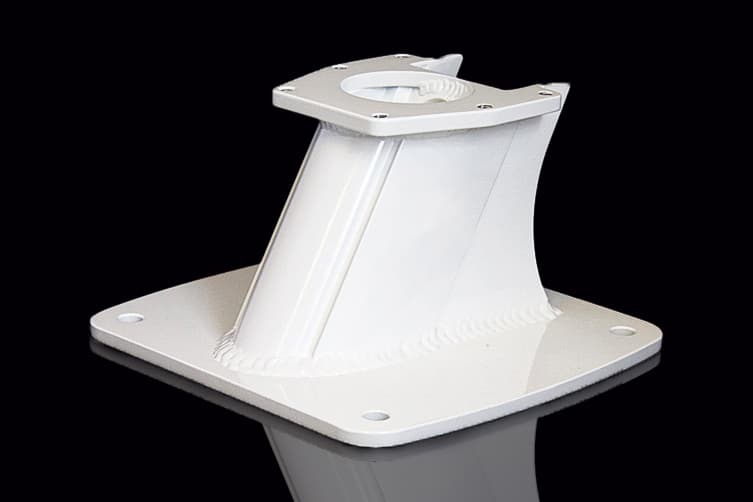
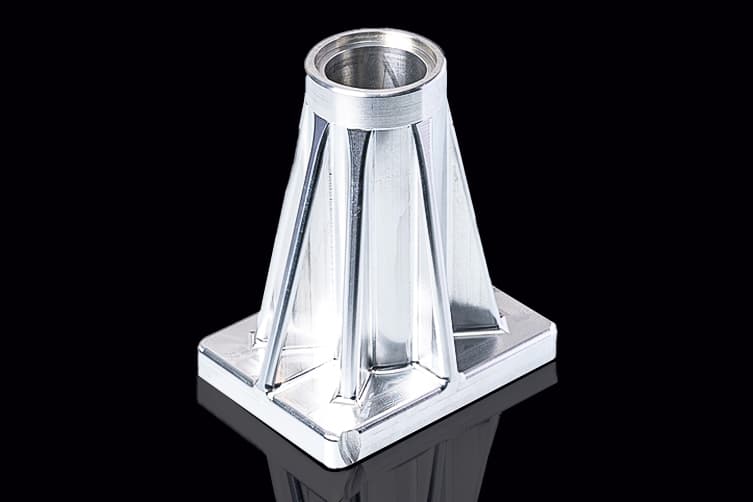
Aerospace & Aviation Industry Engineer James from Xielifeng has something to say

Senior Engineer James, 15 years of experience in machining high-precision, high-demand aerospace components, specializing in parts for aircraft engines, structural components, and control systems. Proficient in meeting the stringent standards required by the aerospace industry, including AS9100 certification.
What materials are best suited for aerospace components to ensure both strength and weight reduction?
We recommend titanium alloys and aluminum-lithium alloys for their excellent strength-to-weight ratios and corrosion resistance. Carbon fiber composites are also widely used for structural components to further reduce weight. These materials meet the rigorous demands of the aerospace industry, where every gram counts.
How do you ensure dimensional accuracy in machining aerospace components?
We use 5-axis CNC machines to achieve complex geometries with tolerances as tight as ±0.005 mm. Our inspection team employs coordinate measuring machines (CMMs) for precise measurements, and every part undergoes first-article inspection (FAI) to ensure compliance with aerospace standards before mass production.
How do you address thermal expansion in aerospace components that operate under extreme conditions?
We select materials with low thermal expansion coefficients, such as Inconel and titanium, for components exposed to extreme temperatures. We also conduct thermal stress testing to simulate operating conditions, ensuring that parts maintain their integrity and precision. Additionally, thermal coatings can be applied to enhance heat resistance.
How do you ensure the reliability of aerospace parts that require both high strength and low weight?
We balance strength and weight by using titanium and advanced composites, which maintain durability without compromising weight limits. Our production process includes fatigue testing and non-destructive testing (NDT) to verify the long-term reliability of each component. Additionally, real-time monitoring during machining helps us detect any deviations immediately.
How do you handle customized aerospace component designs with complex geometries?
We collaborate closely with clients during the design phase to develop custom machining strategies. Using CAD/CAM software, we generate optimized toolpaths to achieve the desired geometries. Prototypes are created for validation, and any adjustments are made before full production. This approach ensures that we meet both the functional and performance requirements of aerospace applications.
How do you manage traceability for aerospace components to meet regulatory requirements?
We implement a comprehensive traceability system, assigning each part a unique serial number. This allows us to track every component from raw material procurement to final delivery, including all testing and inspection results. Our documentation process complies with AS9100 and FAA requirements, ensuring full accountability and transparency throughout production.
How Xielifeng Works
From quotation to delivery, we provide efficient, high-quality services, making manufacturing more convenient.
01
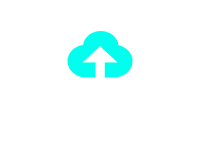
Upload drawing
CAD files: 2D: DXF | DWG | PDF 3D: STP | STEP |IGS | IGES| X_T | SLDPRT
02
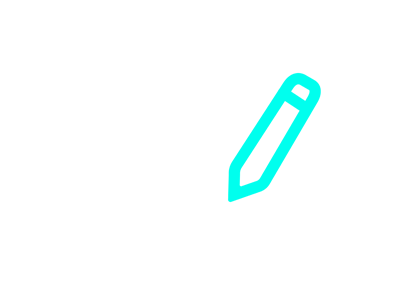
DFM Evaluation & Quote
- Drawing review
- Process analysis
- Material inspection
- Feasibility proposal
- Cost estimation
03
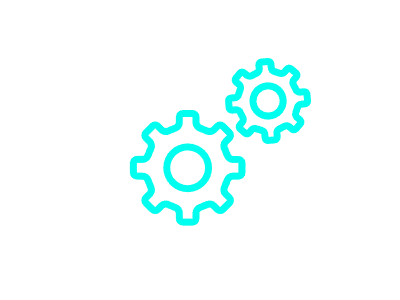
Order Confirmtion & Production
- Sample processing
- Sample quality inspection
- Customer confirmation
- Mass production plan
04
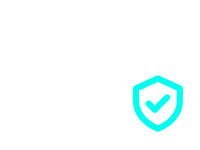
Quality Inspection & Delivery
- Raw material inspection
- First piece inspection
- Process inspection
- Final inspection
- Inspection report