IOS 9001
IOS 14001

Gallery of CNC machined parts
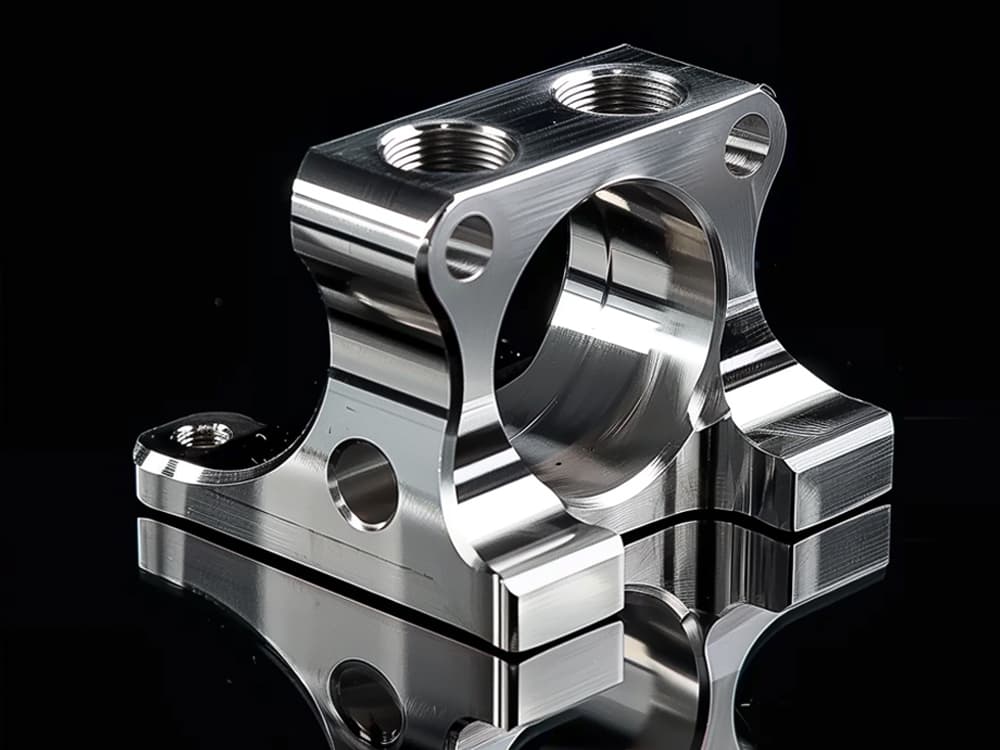
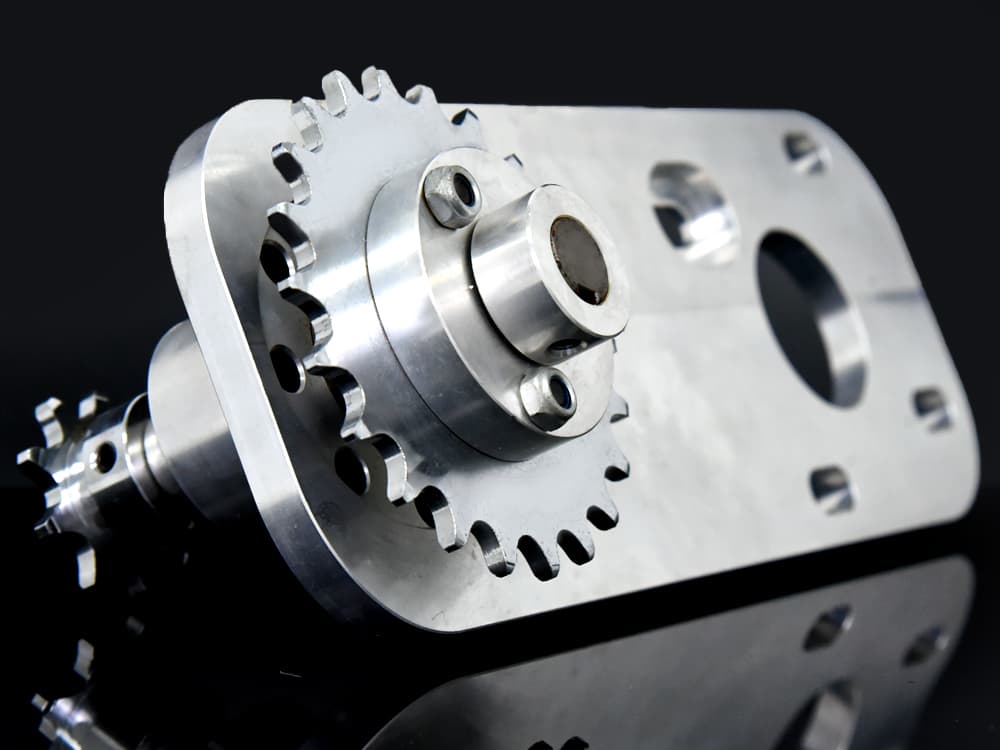
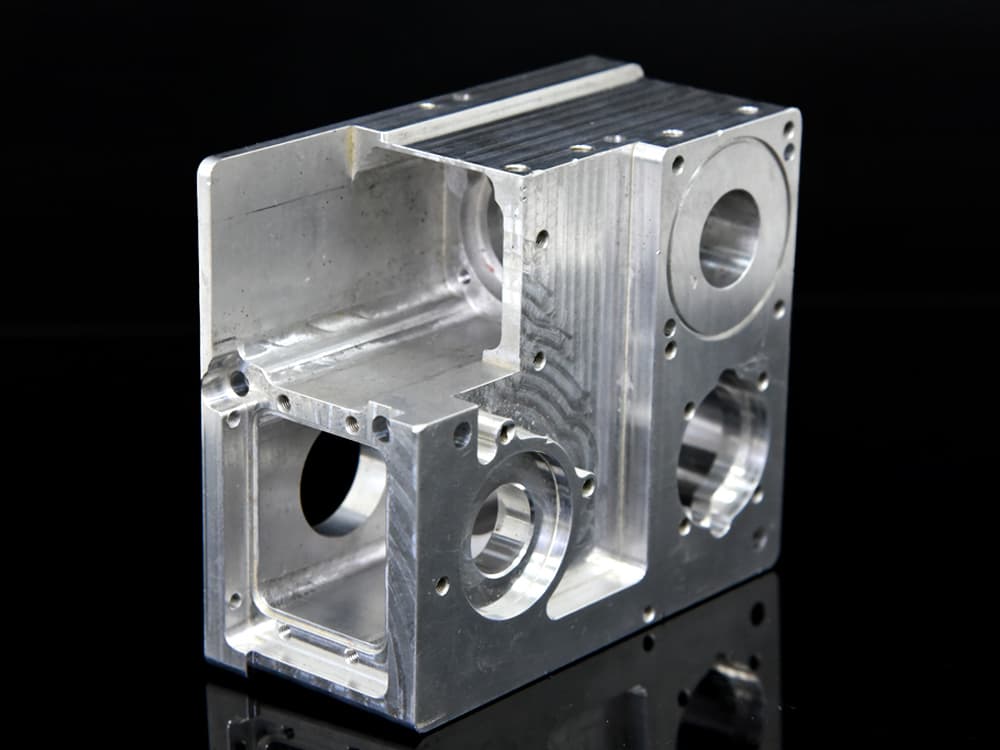
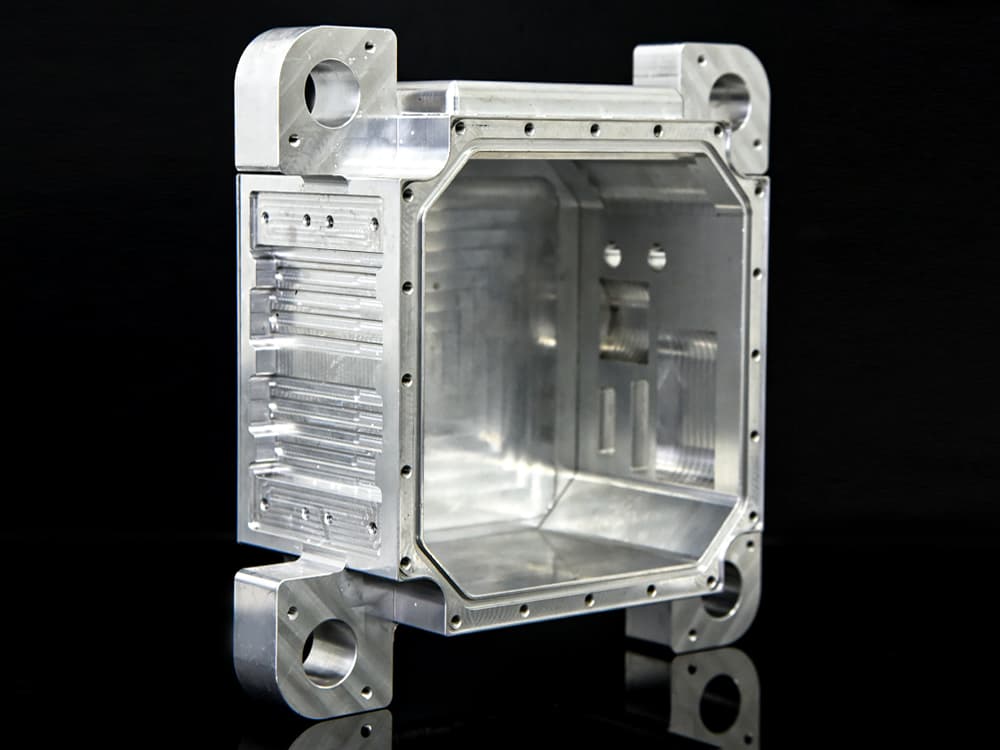
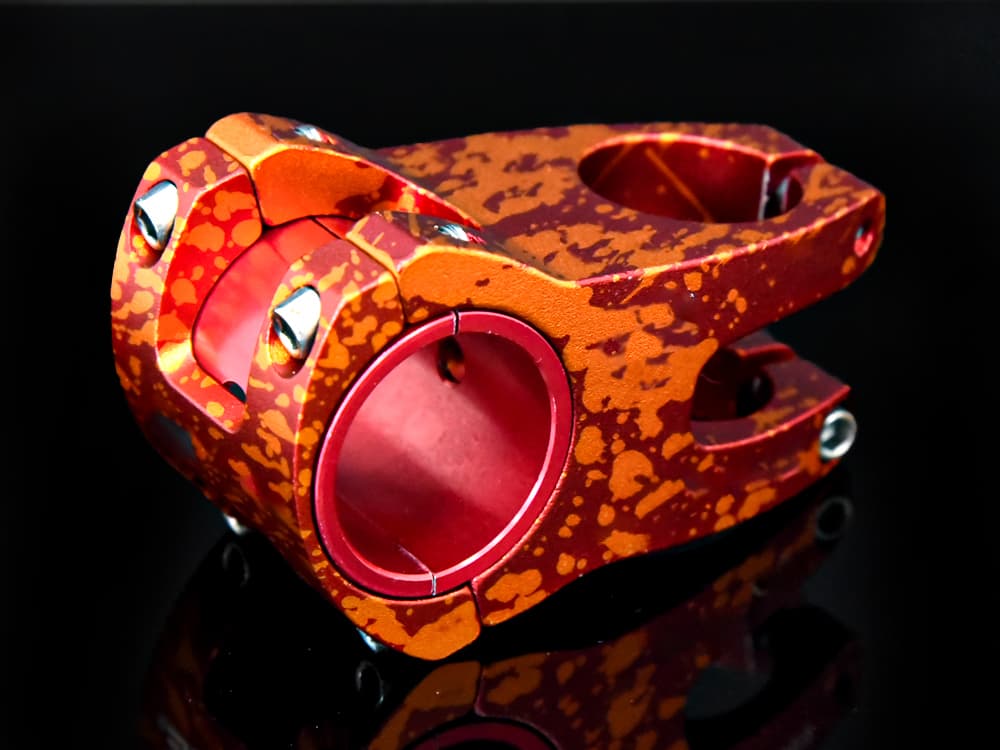
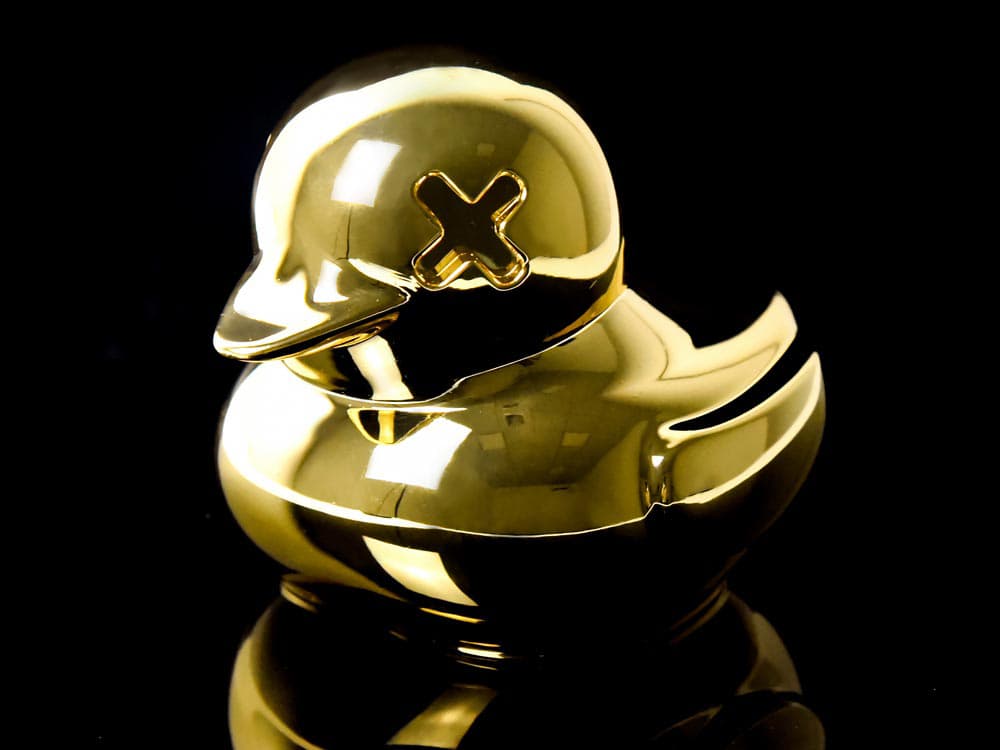
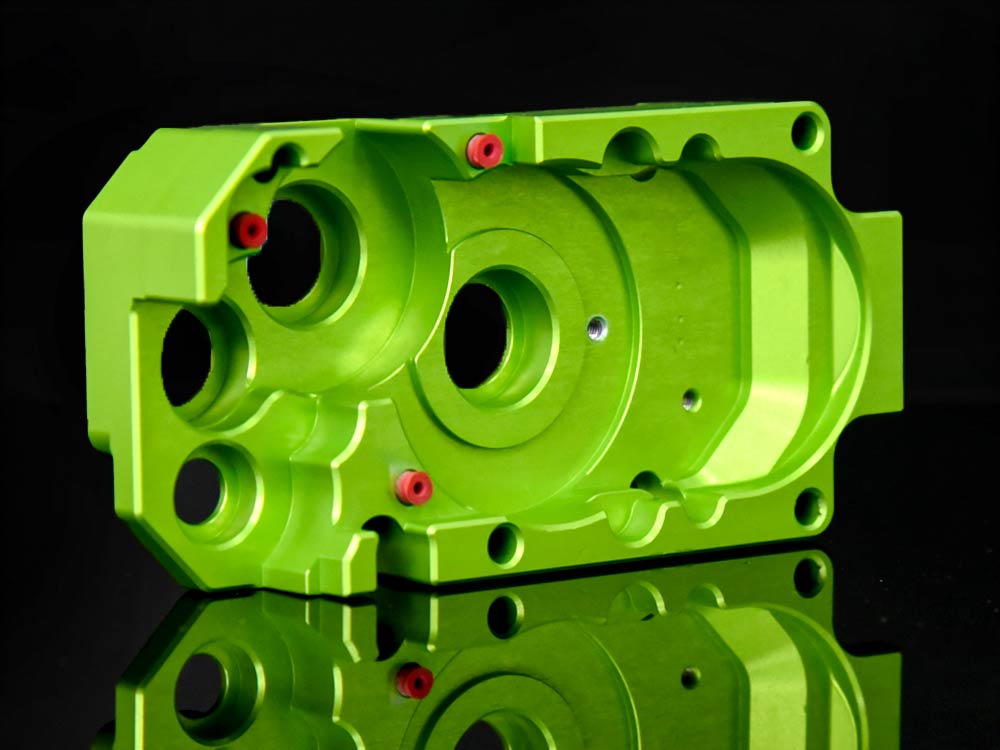
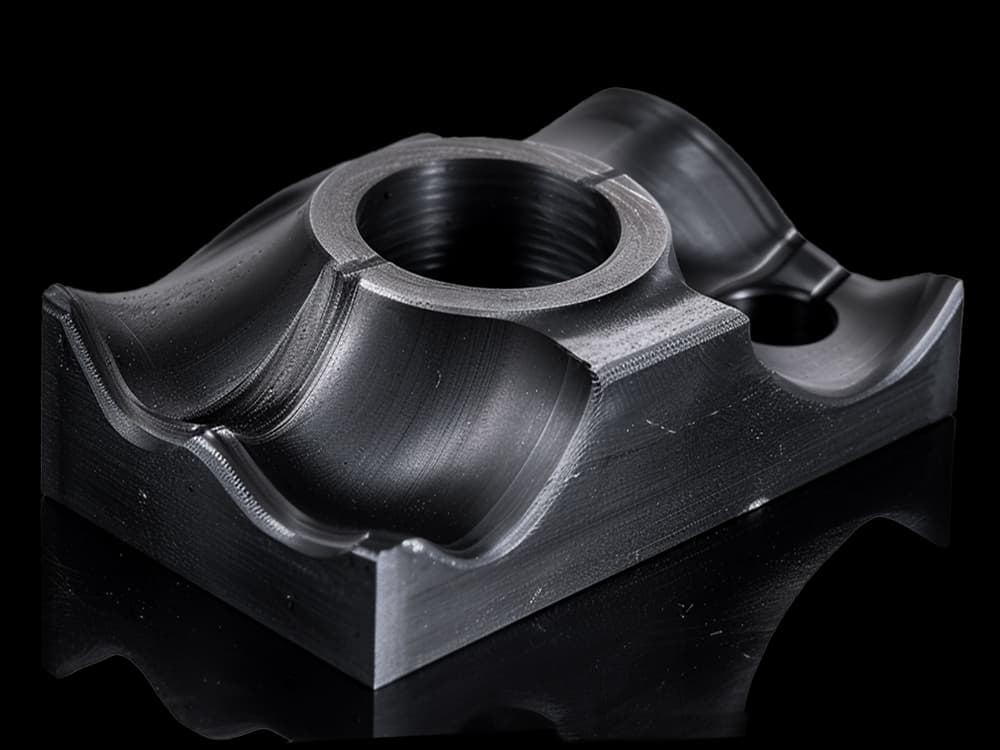
CNC Machining Materials
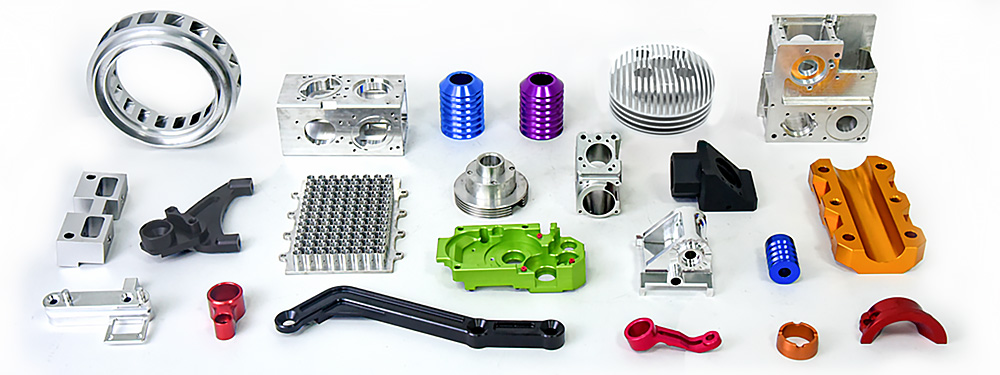
Aluminum is valued for its lightweight, strength, corrosion resistance, and conductivity. Ideal for aerospace, automotive, marine, outdoor equipment, and electronics, it offers durability in harsh environments.
Model: 6061, 7075, 5052, 2024
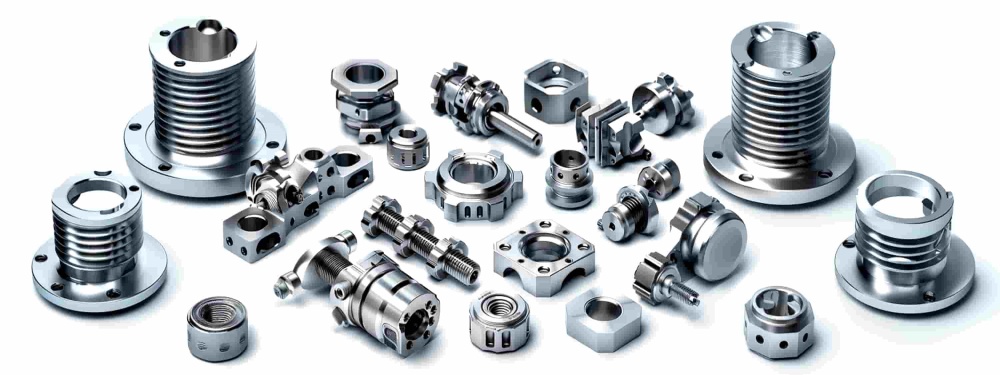
Steel is recognized for its strength, durability, and adaptability. It’s ideal for industrial equipment, automotive parts, construction, and heavy machinery, offering excellent formability and weldability for complex structures.
Model: 1018, 4140, 304, 316
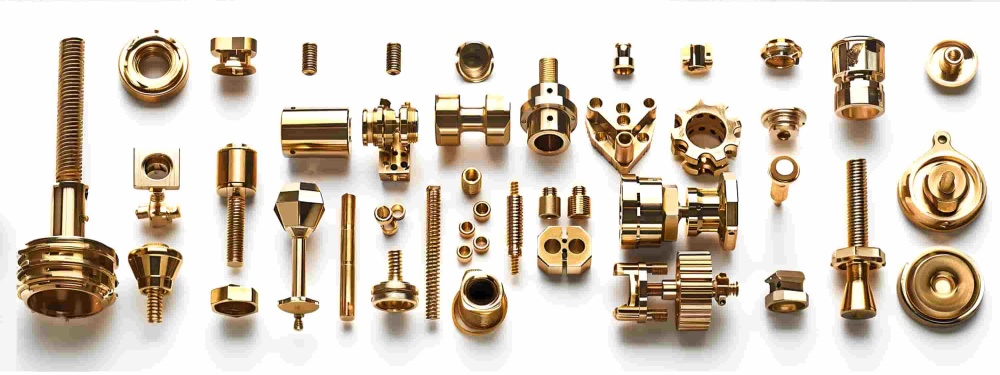
Brass is known for its easy machinability, corrosion resistance, and good conductivity. It’s ideal for electronic components, connectors, plumbing fixtures, and decorative parts, offering precise and reliable performance.
Model: C36000, C37700, C26000, C28000, C27200
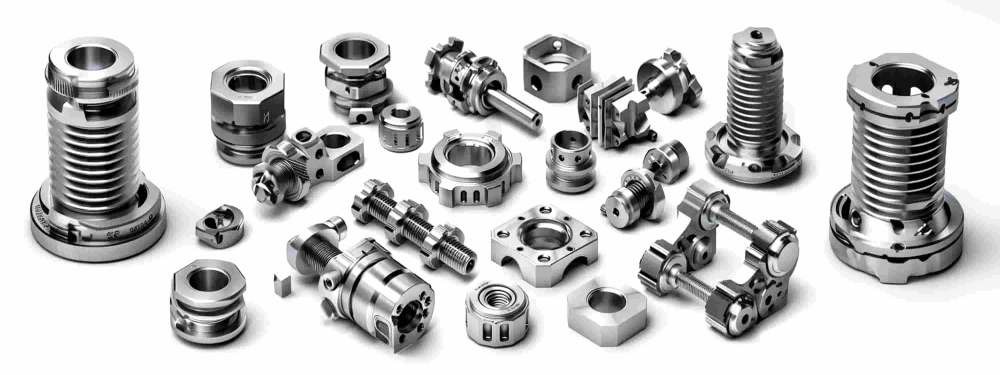
Titanium is prized for its strength, corrosion resistance, and biocompatibility. Perfect for aerospace, medical, marine, and automotive parts, ensuring durability in extreme conditions.
Model: Grade 2, Grade 5, Grade 9, Grade 23, Grade 7
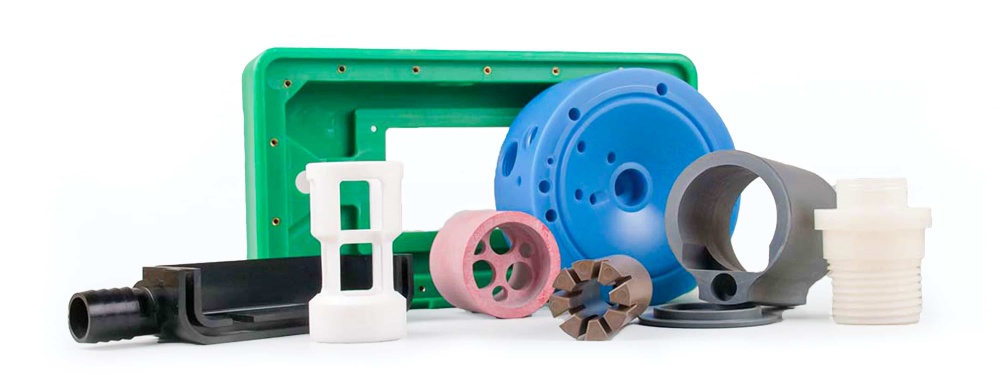
Plastic is valued for its versatility, lightweight, and chemical resistance. It’s ideal for medical devices, electronic housings, automotive components, and industrial parts, offering durability and excellent insulating properties.
Model: POM (Delrin), PEEK, PTFE (Teflon), ABS, Nylon (PA66)
CNC Milled Parts Surface Finishes
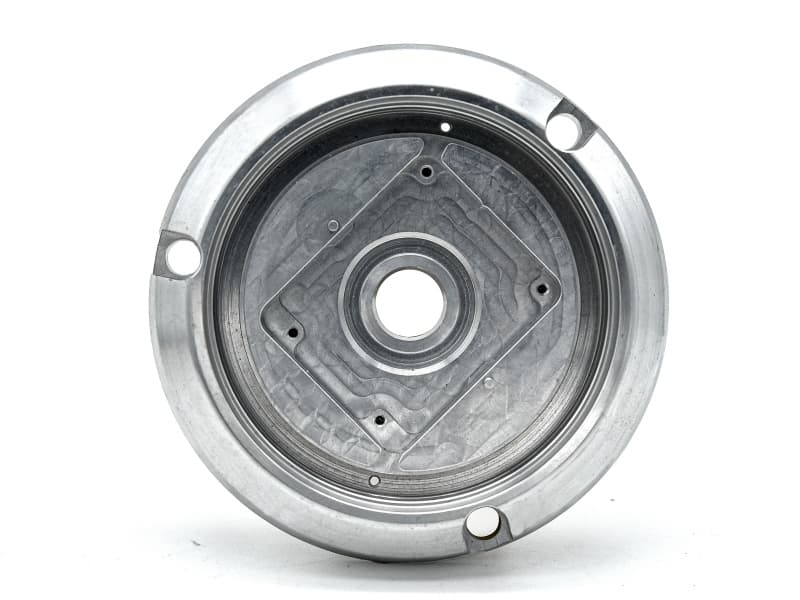
As machined
Color: Varies by material.
Finish Purpose: Creates decorative machining patterns, light surface scratches
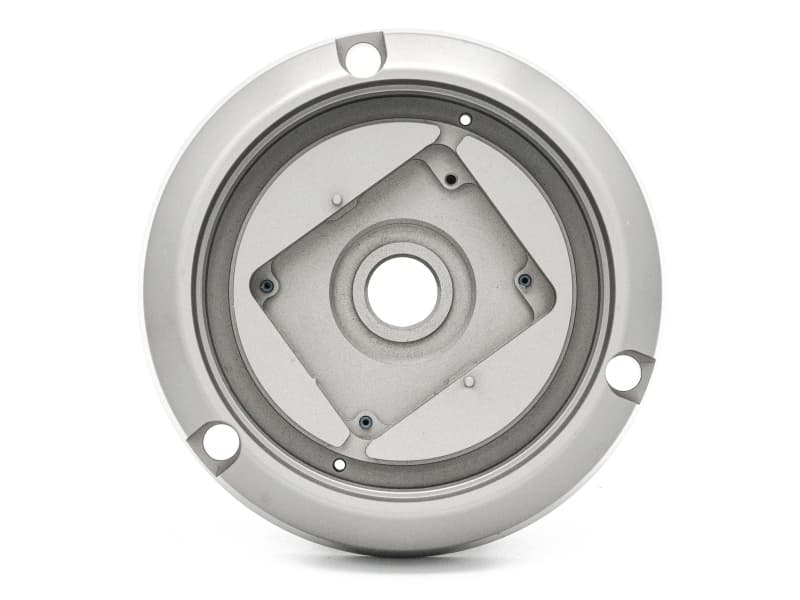
Sand Blasting
Color: None (Textured Surface). Finish Purpose: Uniform matte finish, enhances surface roughness.
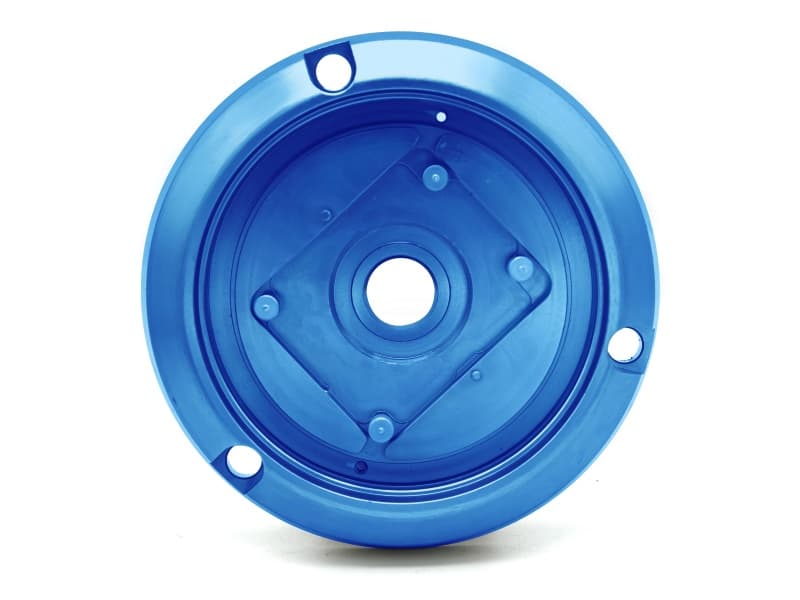
Anodizing
Color: Various, e.g black, red. Finish Purpose: Improve corrosion resistance, provide decorative effect.
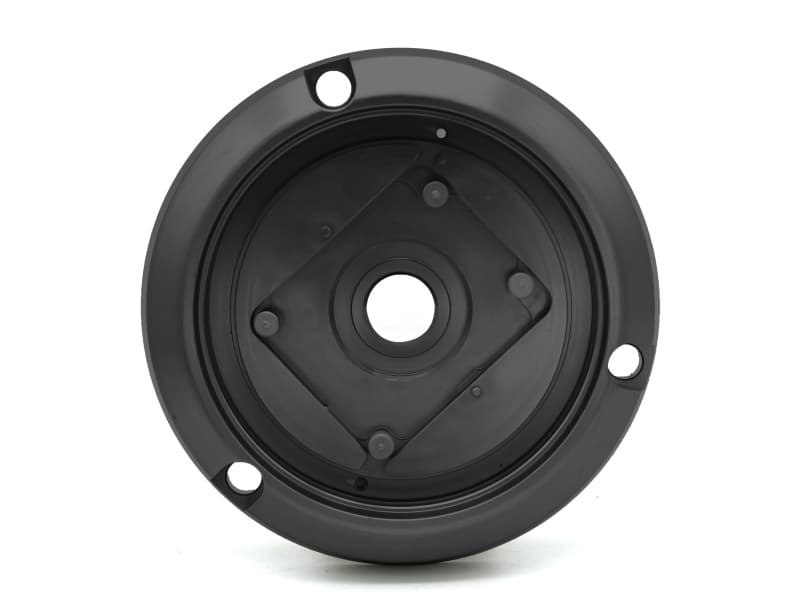
Hardcoat anodizing
Color: Black, Gray.
Finish Purpose: Improve wear resistance and corrosion resistance.
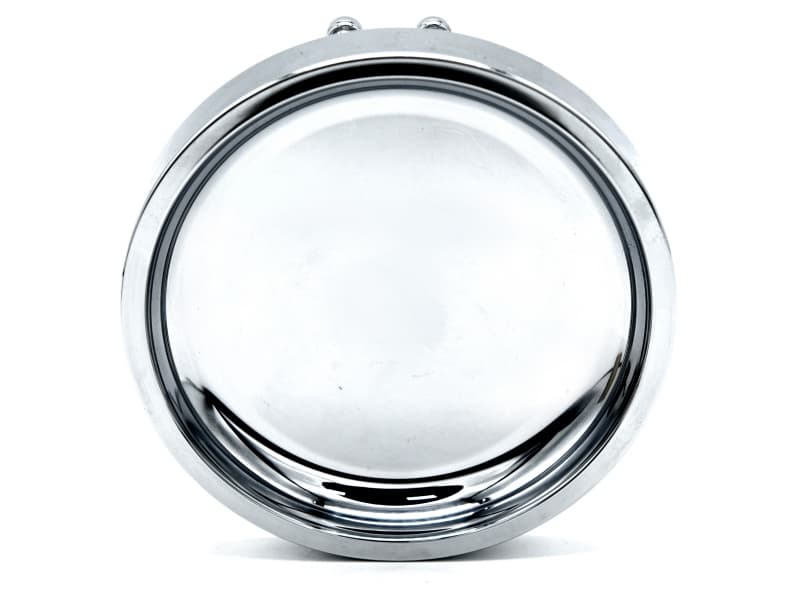
Electroplating
Color: Various, e.g sliver, golden. Finish Purpose: Improve appearance, increase corrosion resistance and decorativeness.
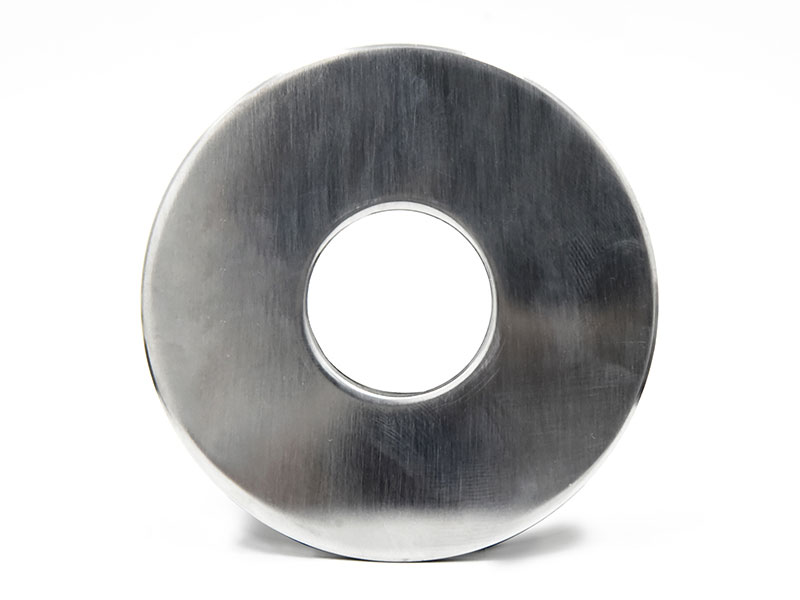
Polishing
Color: depends on material. Finish Purpose: Improve the smoothness of the workpiece surface.

Brushing
Color: Silver, Matte finish.
Finish Purpose: Create decorative effect, enhance appearance.
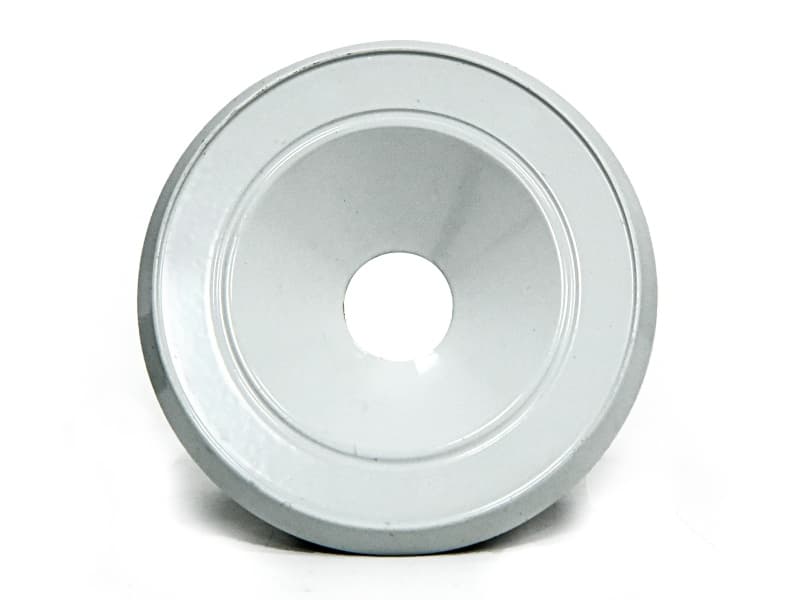
Powder Coating
Color: Various, e.g white, black. Finish Purpose: Provide protective coating, improve appearance.
A Note about Our Customization
Features | CNC Milling Parts | CNC Turning Parts | ||||||||
---|---|---|---|---|---|---|---|---|---|---|
Maximum Part Size | 236" x 118" x 24" (6,000 x 3,000 x 610 mm) | 62" Length x 32" Diameter (1,575 mm Length x 813 mm Diameter) |
||||||||
Minimum Feature Size | 0.020″ (0.50 mm) | 0.020″ (0.50 mm) | ||||||||
Estimated Delivery Time | 3-7 working days | 3-7 working days | ||||||||
Standard Tolerance | ISO 2768 MK | ISO 2768 MK | ||||||||
Precision Tolerance | ±0.0002" (±0.005mm) | ±0.0002" (±0.005mm) | ||||||||
Threads and Threaded Holes | Standard threads and holes available, also customizable. | Standard threads and holes available, also customizable. | ||||||||
Edge Conditions | Deburring by default. | Deburring by default. | ||||||||
Surface Smooth | Ra 0.4 - 1.6μm | Ra 0.4 - 1.6μm | ||||||||
How Xielifeng Works
From quotation to delivery, we provide efficient and high-quality services, making manufacturing more convenient.
01
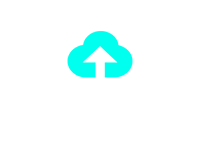
Upload drawing
CAD files: 2D: DXF | DWG | PDF 3D: STP | STEP |IGS | IGES| X_T | SLDPRT
02
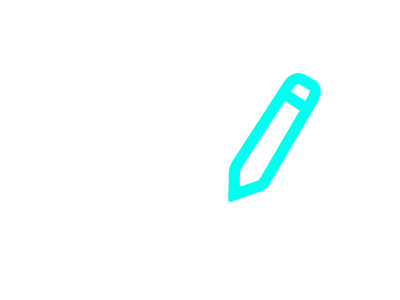
DFM Evaluation & Quote
- Drawing review
- Process analysis
- Material inspection
- Feasibility proposal
- Cost estimation
03
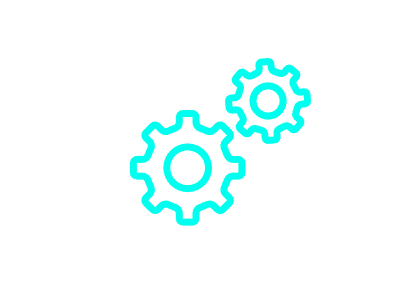
Order Confirmtion & Production
- Sample processing
- Sample quality inspection
- Customer confirmation
- Mass production plan
04
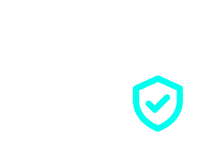
Quality Inspection & Delivery
- Raw material inspection
- First piece inspection
- Process inspection
- Final inspection
- Inspection report
Xielifeng Professional Engineer Team
Our engineering team has extensive experience and expertise, specializing in precision machining, material processing, and innovative manufacturing. They are committed to delivering top-quality results for every project, whether it’s aerospace components, automotive parts, or motorcycle accessories, ensuring every detail meets the highest standards.
View More About Our Engineering Team>>
Daniel
Senior Engineer of Medical Equipment Parts
Nora
Senior Engineer of Lighting Parts
Benjamin
Senior Engineer of Firefighting Parts
Lucy
Senior Engineer of Communication Equipment Parts
Bella
Senior Engineer of Industrial Equipment Parts
James
Senior Engineer of Aerospace Parts
Grace
Senior Engineer of Consumer Electronics Parts
Henry
Senior Engineer of Automotive Parts
Julia
Senior Engineer of New Energy Parts
Andrew
Senior Engineer of Household Appliance Parts
Quality Control
Our dedicated quality control team and advanced inspection equipment ensure every part meets the highest standards. From start to finish, we guarantee precision, reliability, and consistency in every component.
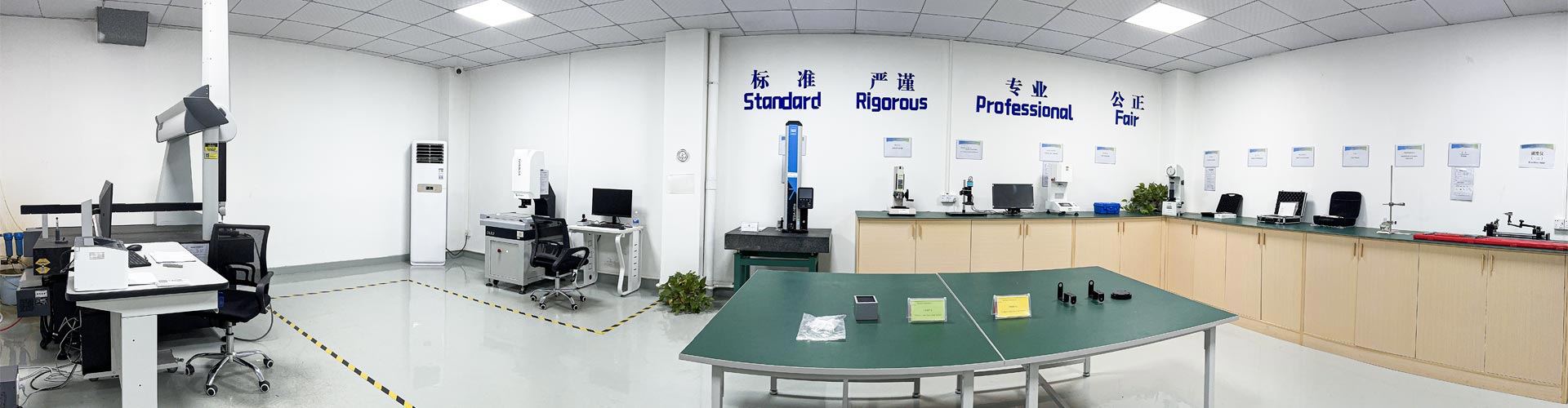
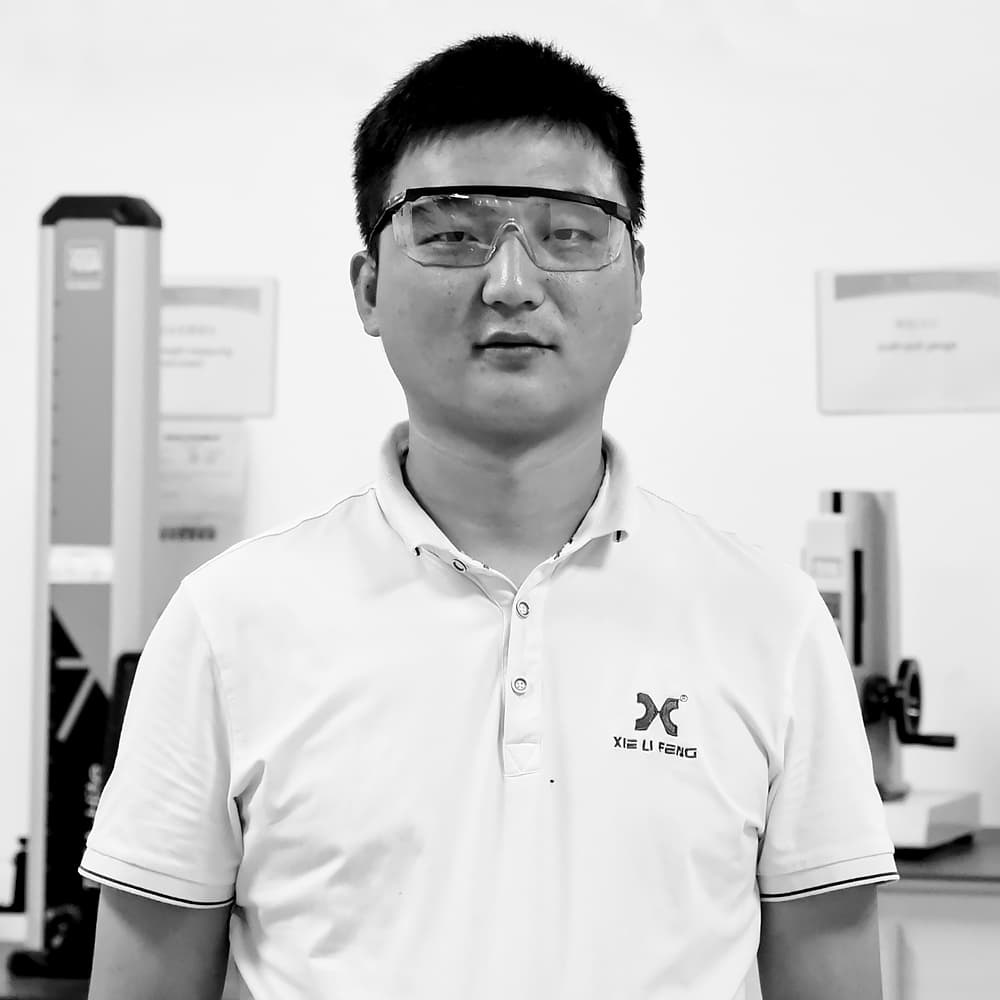
Jason
QM
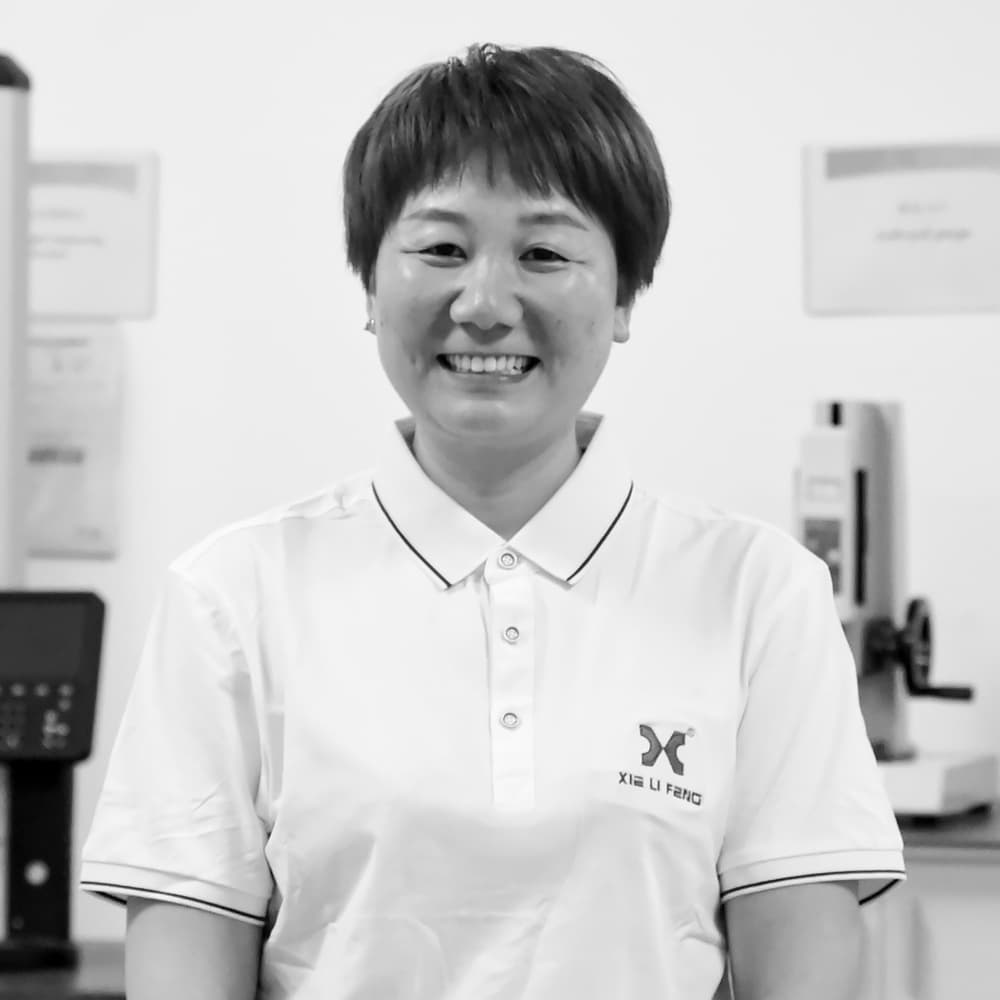
Celine
QA

Emma
IQC
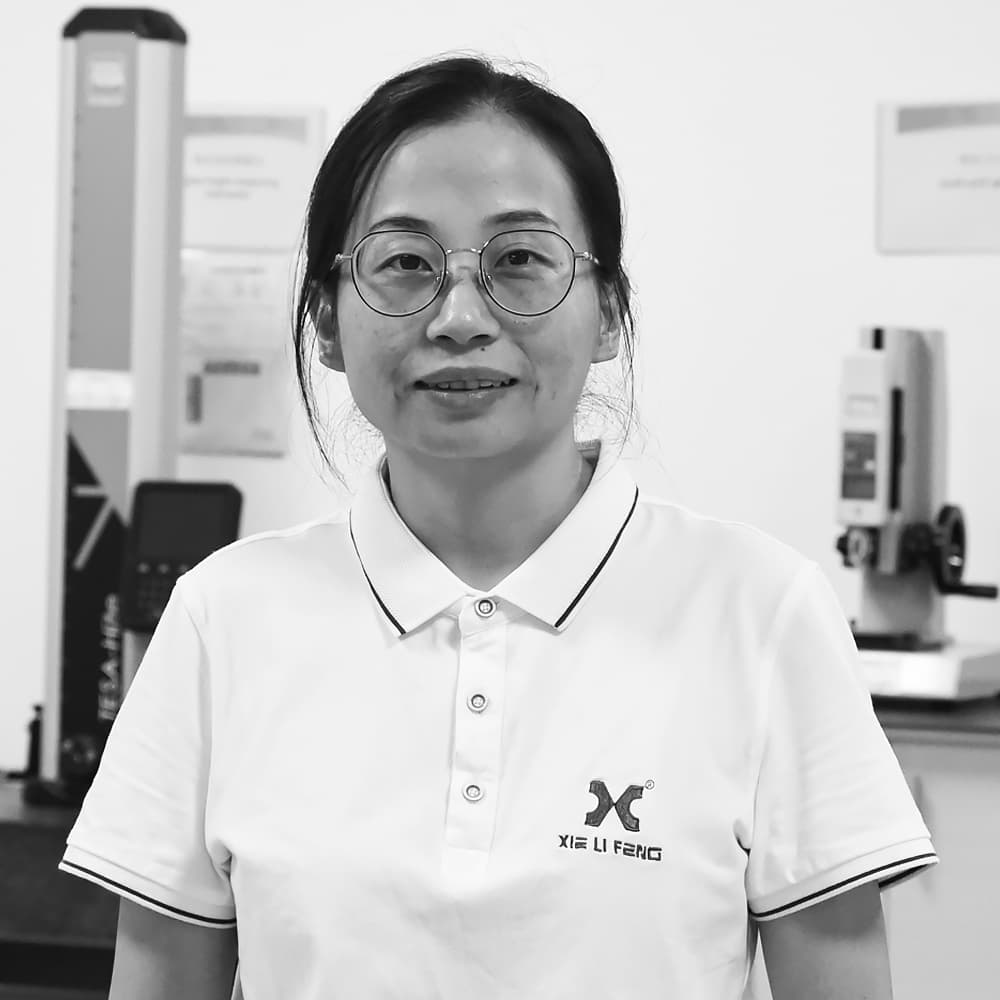
Lana
MQ
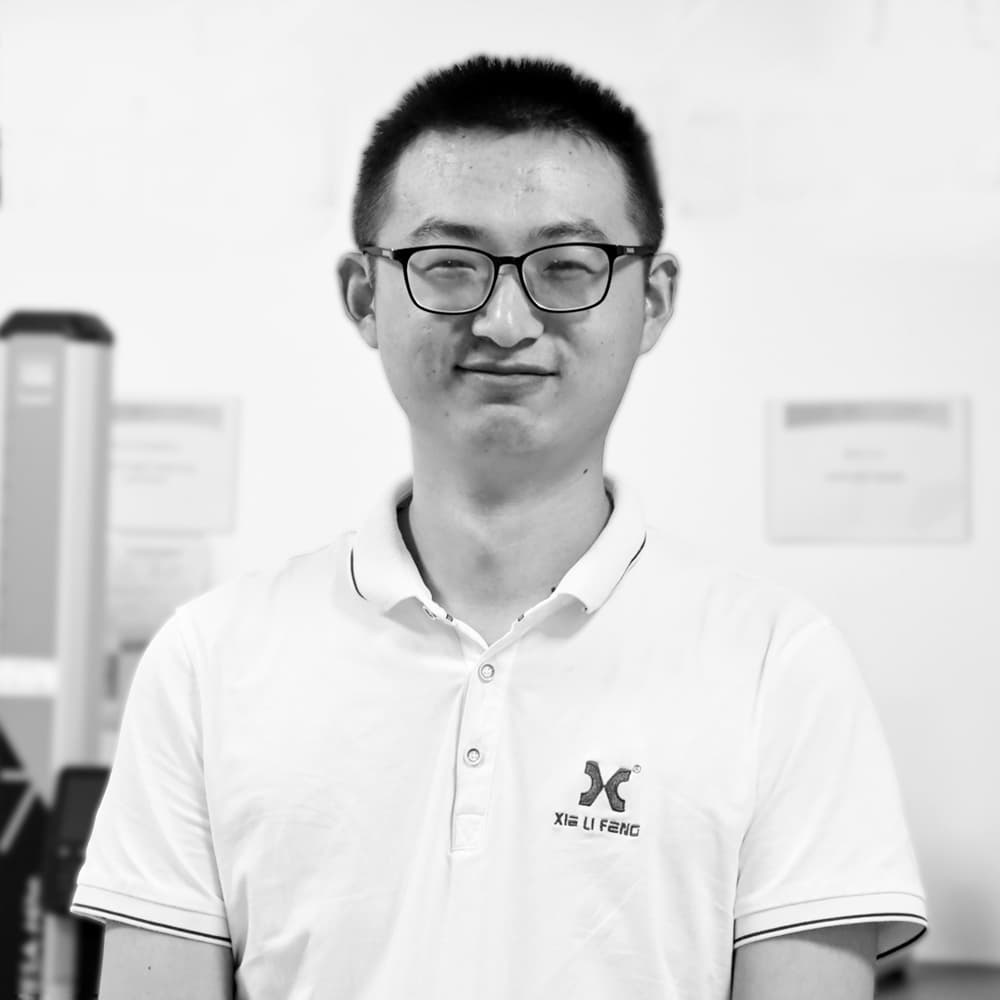
Owen
IPQC
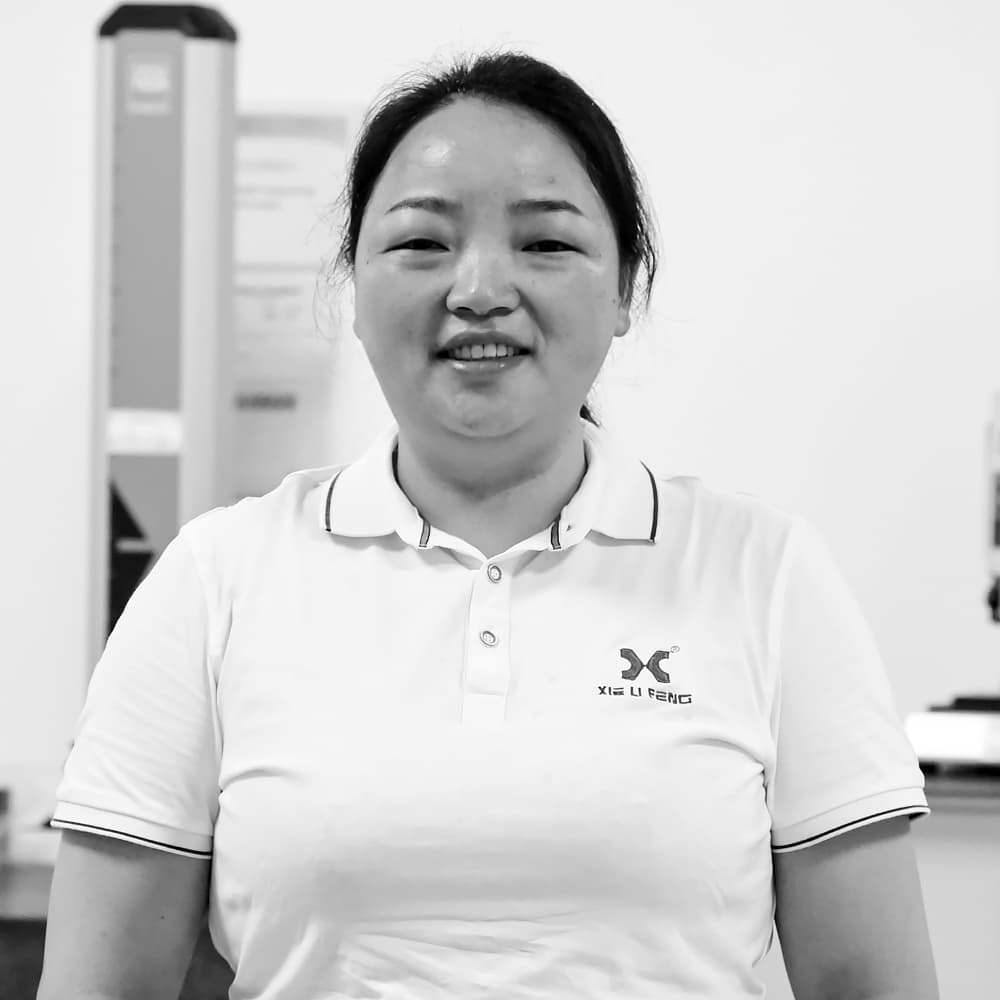
Fiona
SQE
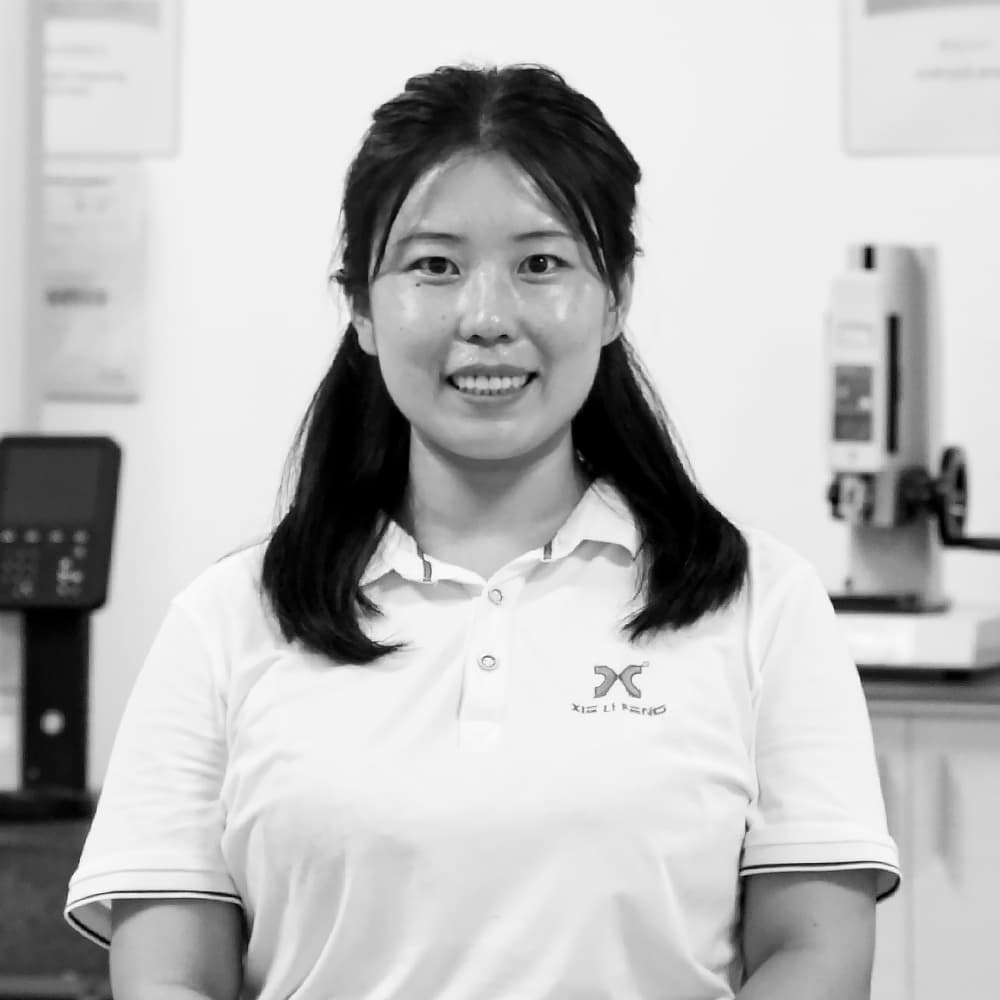
Nadine
FQC
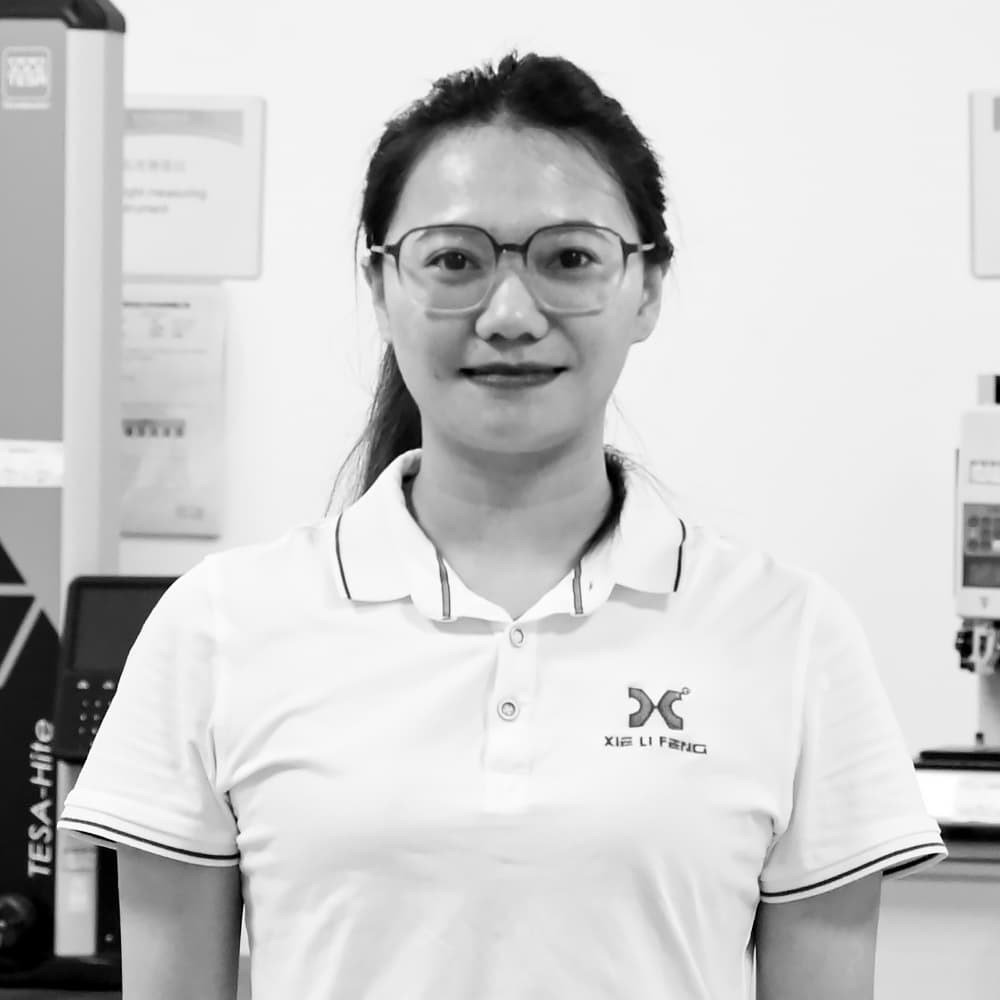
Nicole
QE
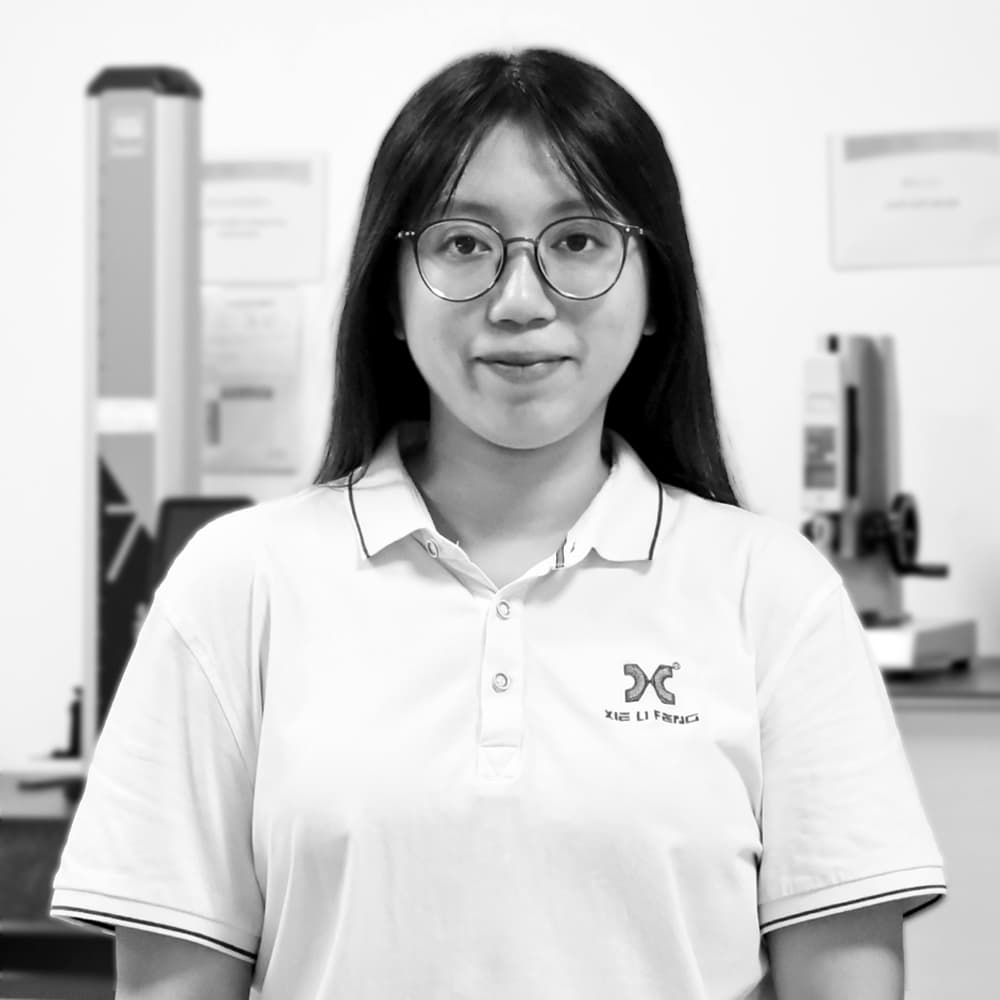
Camila
DDC
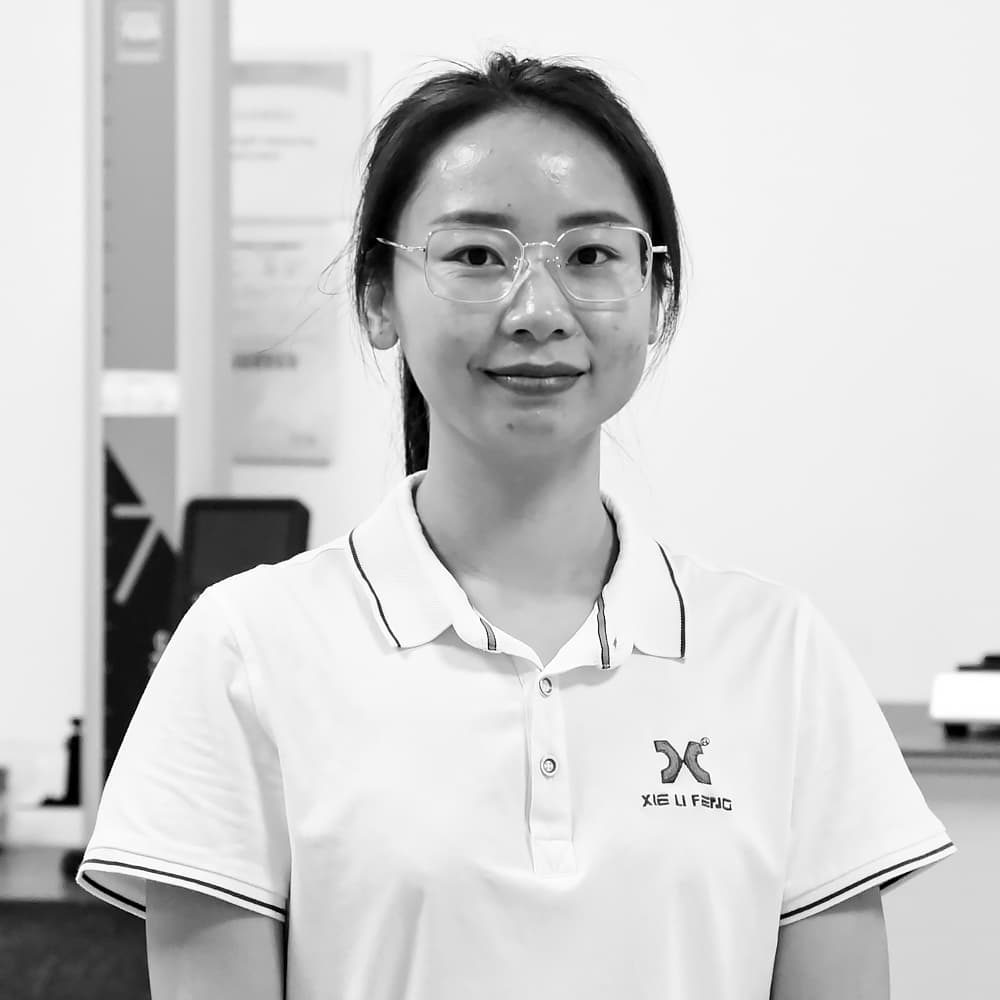
Eileen
CA
Quality Inspection Equipment
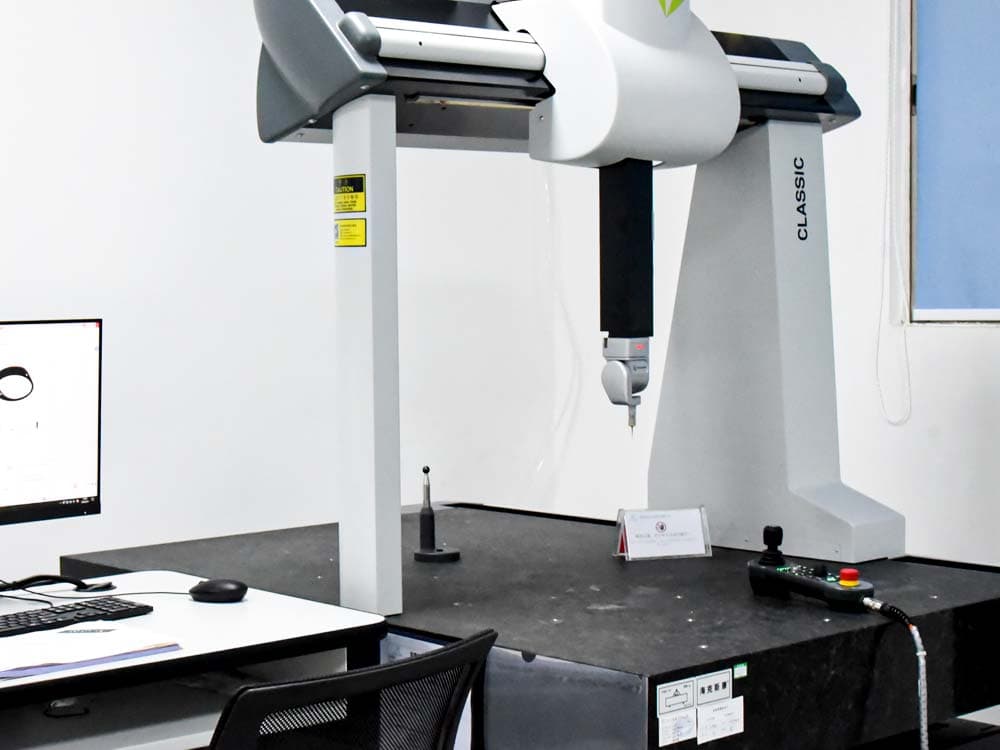
CMM
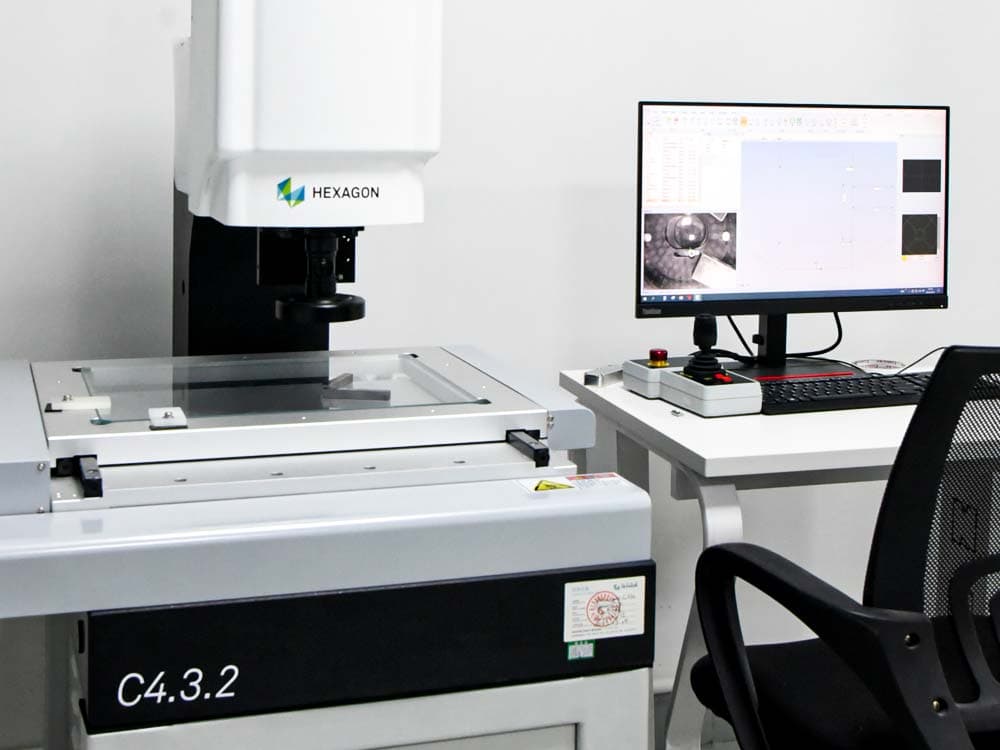
Quadratic Element Measuring instrument
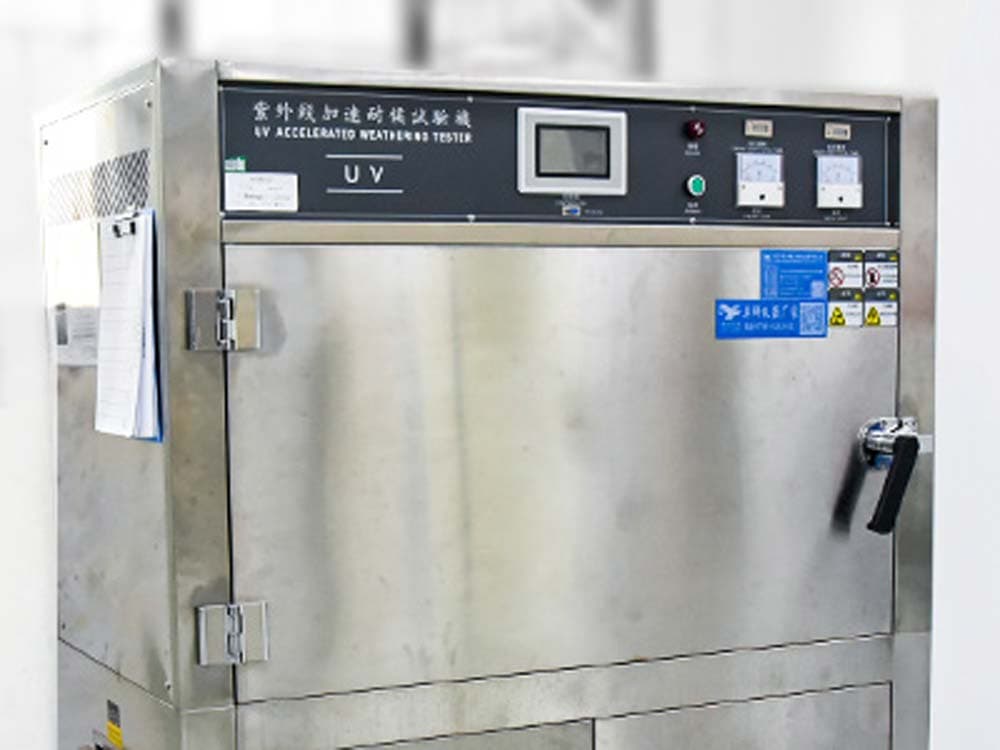
UV
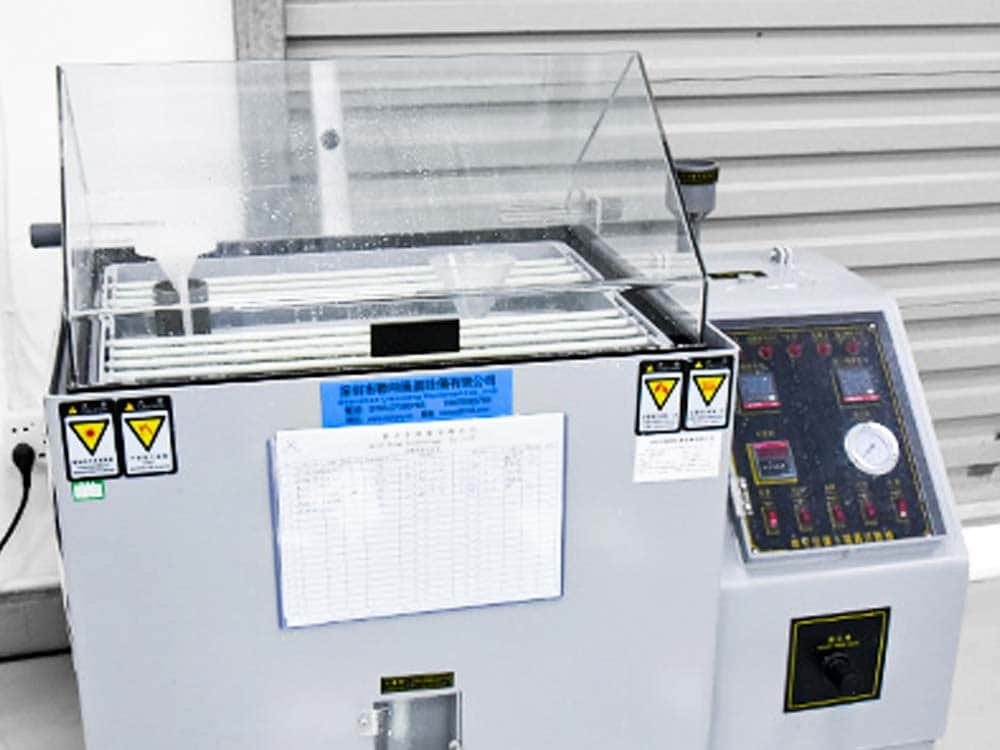
Salt Spray Test
Xielifeng CNC machinng Factory
We provide you with a variety of processing methods. We have a variety of advanced processing equipment to complete customized processing with high efficiency and quality.
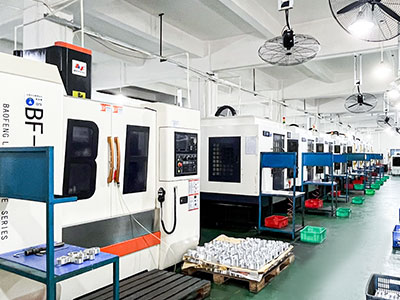
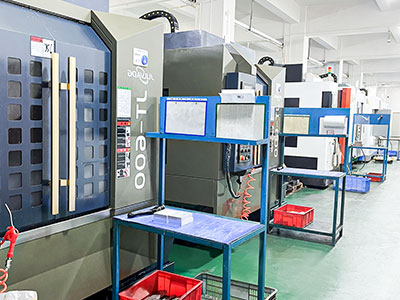
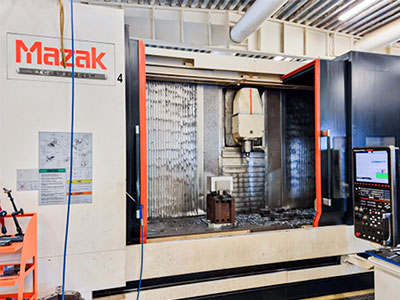
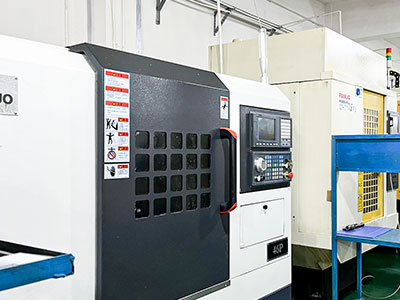
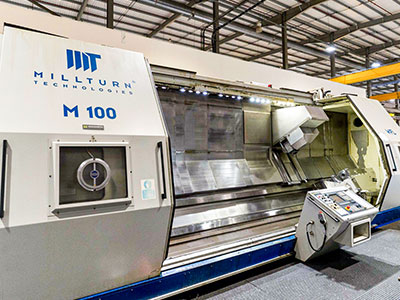
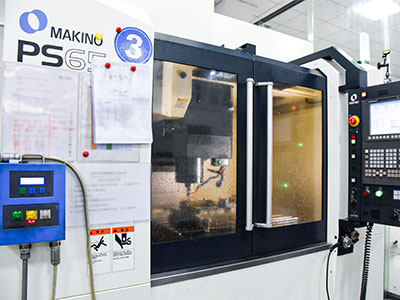
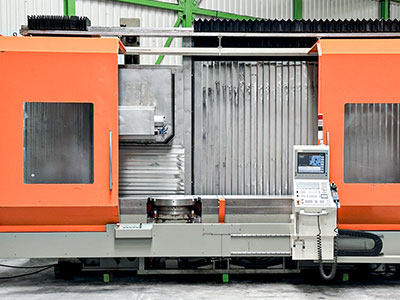
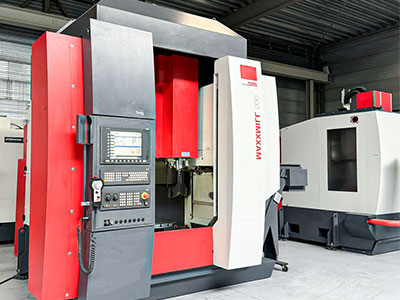
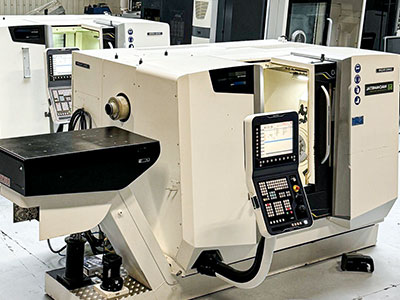
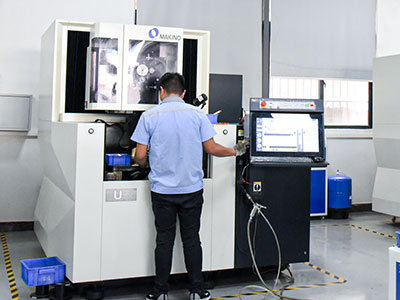
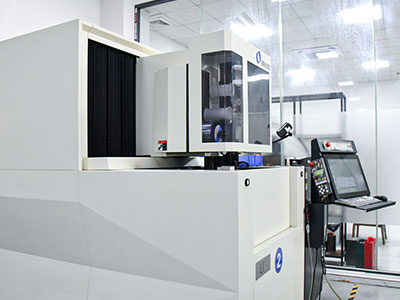
Precision Machined Parts Case Study
With extensive experience in parts machining, we serve multiple industries. Our years of expertise and advanced CNC technology make us a trusted partner worldwide.
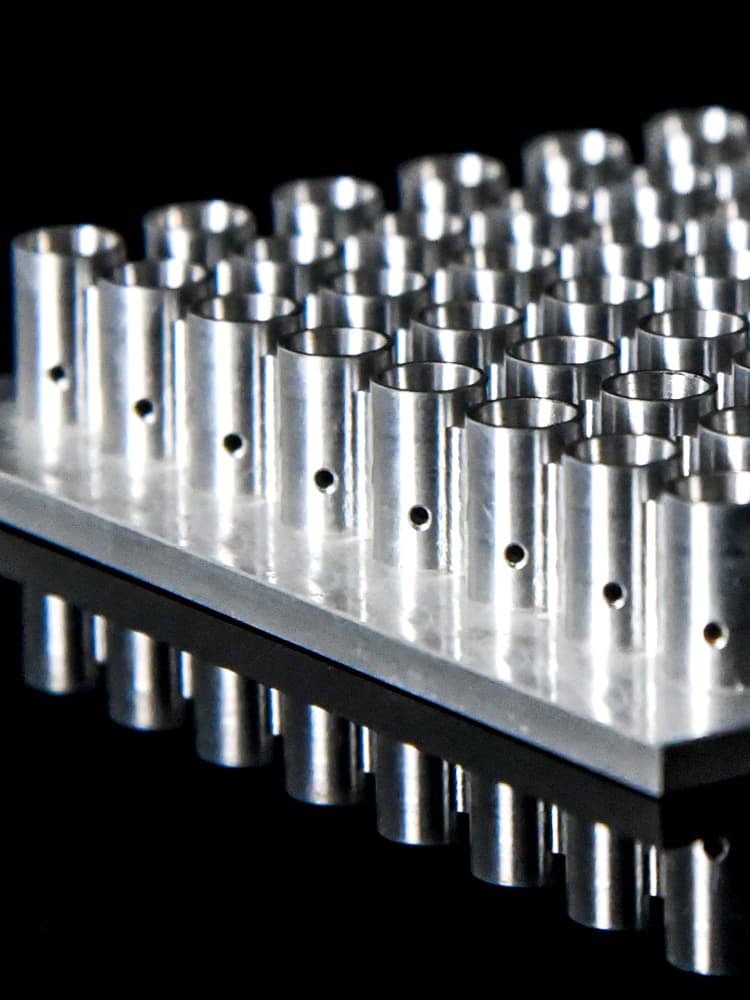
Processing Challenges
Hole Diameter and Depth Precision (1.0mm, Depth 96mm)
The part requires a hole diameter of 1.0mm and a depth of 96mm, which presents a high challenge in precision and deep hole processing, particularly in maintaining consistency between hole diameter and depth.
Concentricity Control (within 0.02mm)
The concentricity of the holes must be controlled within 0.02mm, ensuring precise relative positioning of multiple holes in space, which is critical for the part’s assembly and function.
Hole Alignment Requirement
The holes must align in a straight line in each direction, requiring extremely precise hole placement to ensure the overall structure’s function and performance.
We use high-precision CNC equipment and deep hole machining technology, ensuring that the hole diameter and depth meet design specifications, maintaining concentricity within 0.02mm, and making fine adjustments to align the holes in each direction in a straight line, ensuring both the accuracy and functionality of the part.
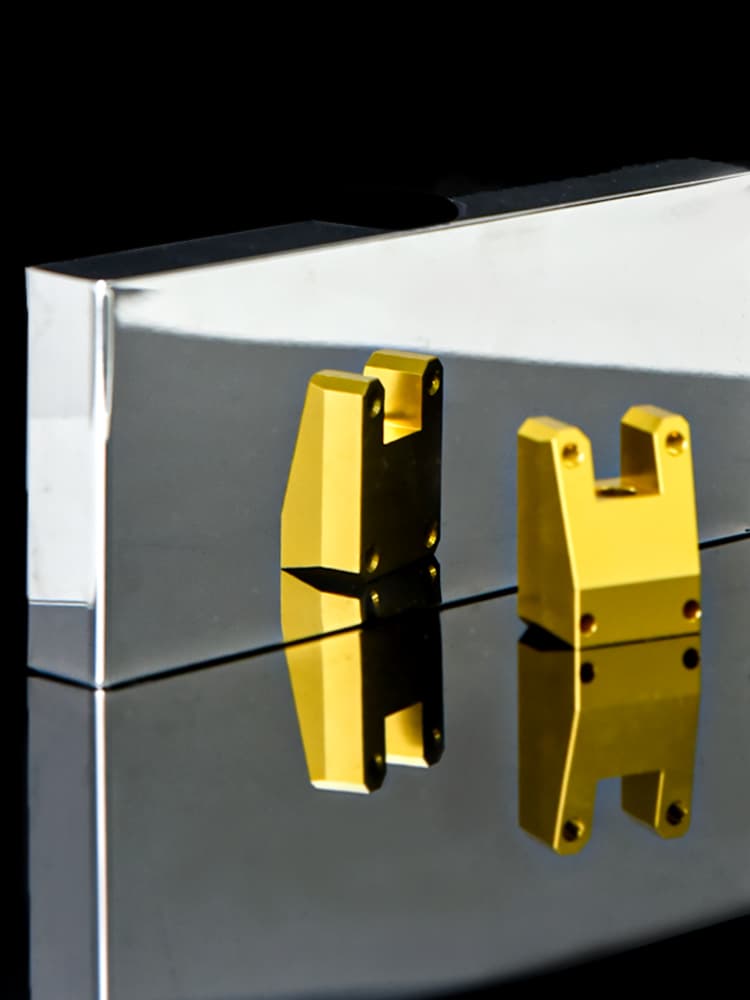
Processing Challenges
The part is prone to deformation during processing due to temperature and mechanical factors.
High Surface Roughness Requirement:
The surface roughness needs to be below Ra0.2, with a smooth and flawless finish.
Strict Flatness Requirement:
The flatness must be controlled within 0.01mm, requiring extremely high precision.
No Image Distortion:
The part must have no image distortion within 1 meter, demanding exceptional geometric accuracy.
We have successfully addressed the processing challenges of part deformation, surface roughness, flatness, and image distortion through precise process control, high-precision equipment, and rigorous measurement techniques, ensuring high precision and quality of the product.
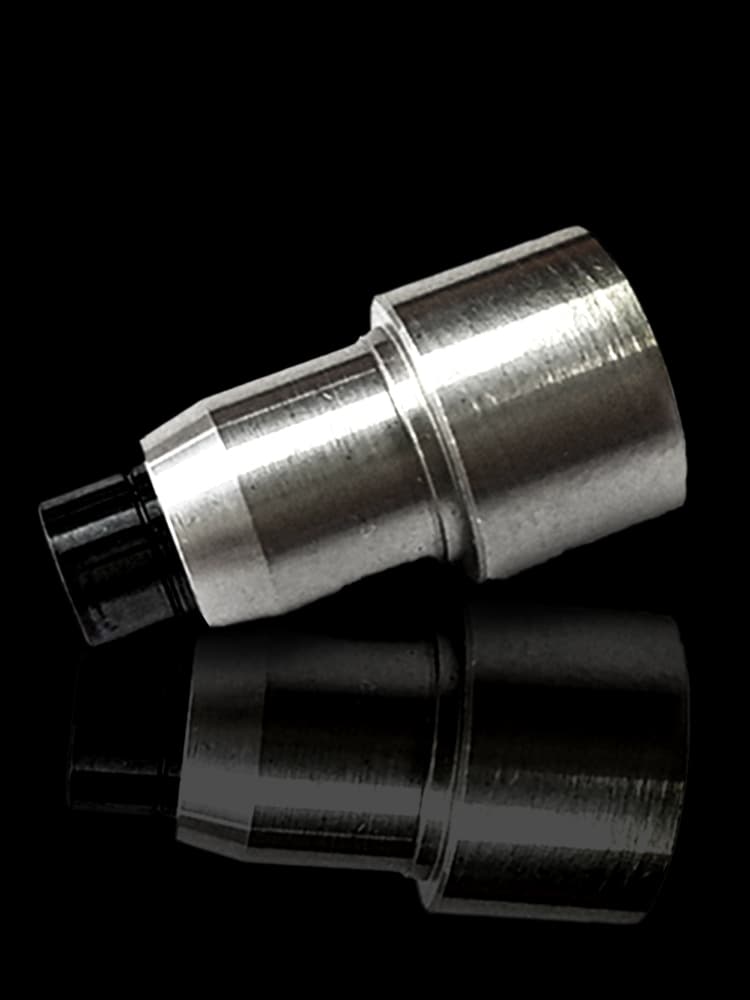
Processing Challenges
High Precision Tolerance Requirement (0.003mm)
The part’s tolerance requirement is 0.003mm, and any small deviation could affect its functionality, making the machining process highly challenging.
Strict Surface Roughness Requirement (Ra0.3)
The surface roughness must be controlled to Ra0.3, ensuring the part’s surface is smooth and flawless, meeting both appearance and performance requirements.
Tolerance Control After DLC Coating (0.004mm)
The tolerance after DLC coating must be controlled within 0.004mm, requiring precise coating processes to ensure uniformity and adhesion of the coating.
We successfully addressed the challenges of high-precision tolerance, surface roughness, and DLC coating tolerance control by using precision machining, strict measurement, advanced grinding techniques, and accurate coating control, ensuring the part’s precision