Surface finishing services
30+ Finishing Options
200+ Available Materials
Consistent Appearance, Corrosion Resistance, and Durability
Compliance with RoHS, REACH, and Other Environmental Standards
All uploads are secure and confidential.* Learn More
| ISO 9001:2015 | ISO 14001:2016
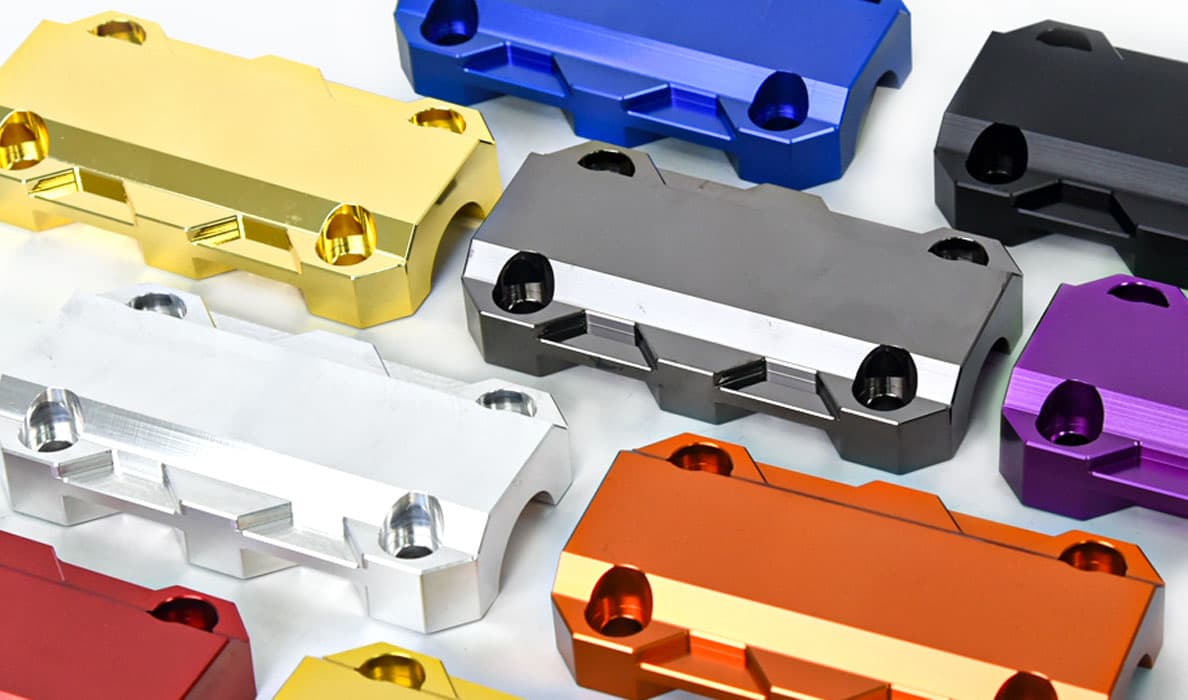
IOS 9001
IOS 14001

Surface Finishing Options
Whether it’s basic treatment, high-end decoration, or functional enhancement, we provide comprehensive surface treatment solutions to meet the needs of various industries and applications.
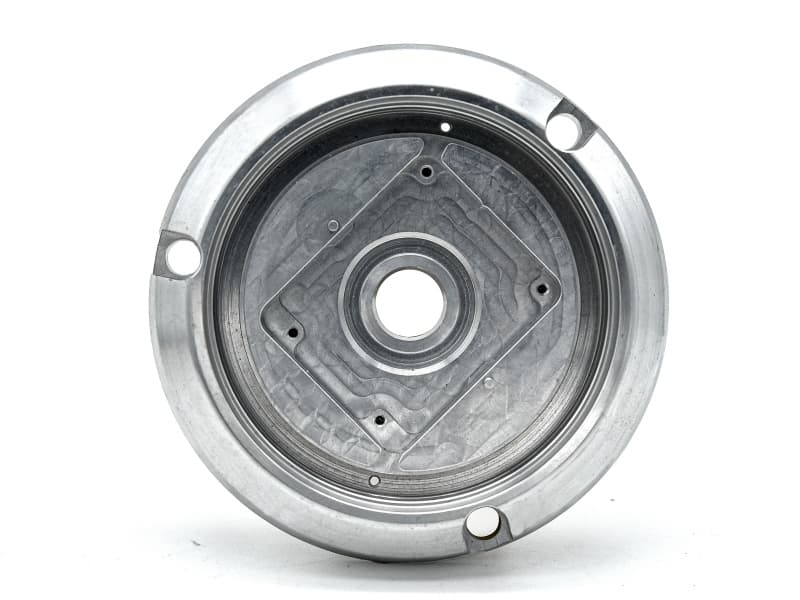
As machined
Color: Varies by material.
Finish Purpose: Creates decorative machining patterns, light surface scratches
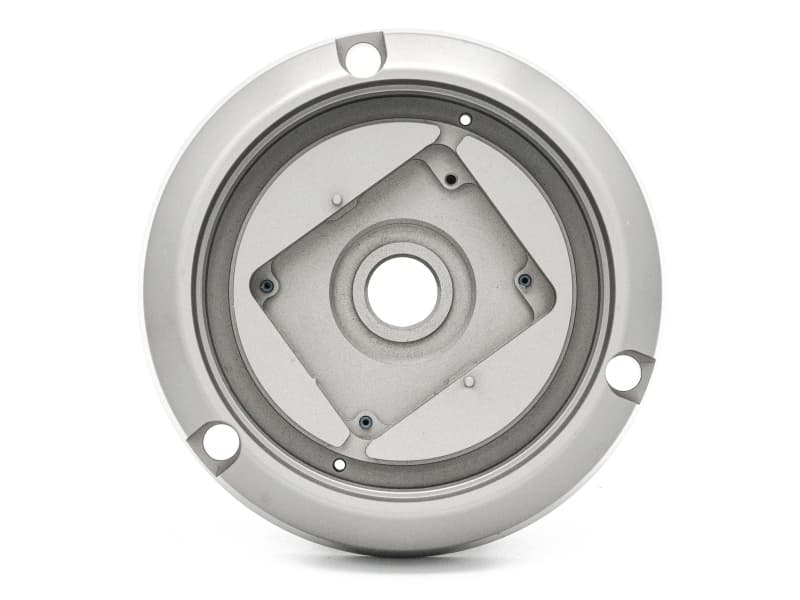
Sand Blasting
Color: None (Textured Surface).
Finish Purpose: Uniform matte finish, enhances surface roughness.
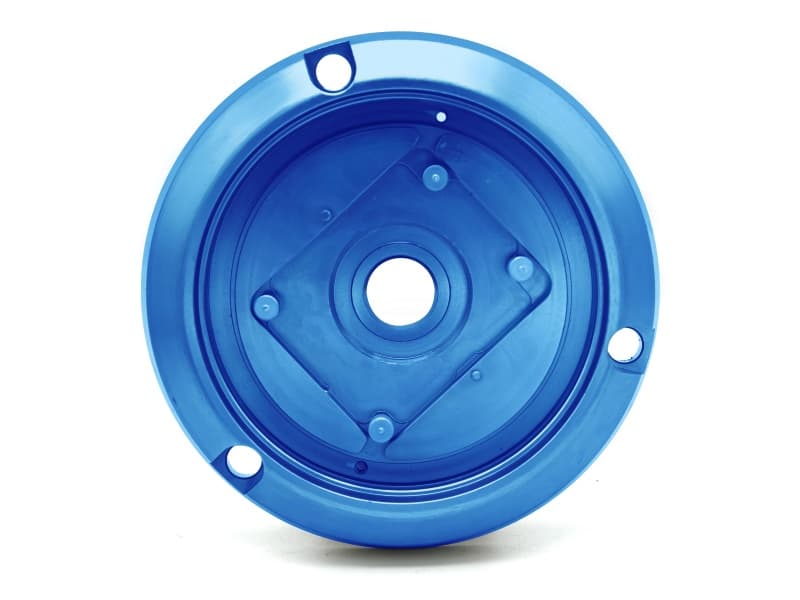
Anodizing
Color: Various, e.g black, red.
Finish Purpose: Improve corrosion resistance, provide decorative effect.
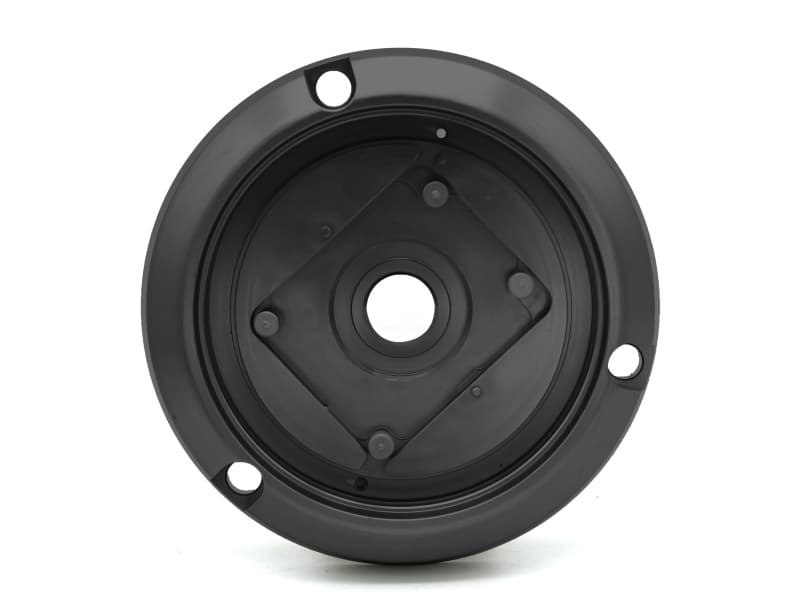
Hardcoat anodizing
Color: Black, Gray.
Finish Purpose: Improve wear resistance and corrosion resistance.
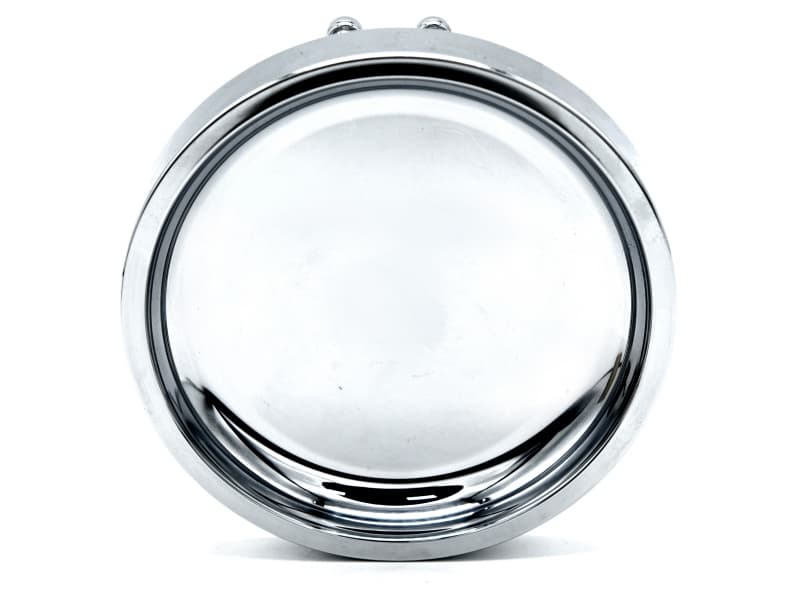
Electroplating
Color: Various, e.g sliver, golden.
Finish Purpose: Improve appearance, increase corrosion resistance and decorativeness.
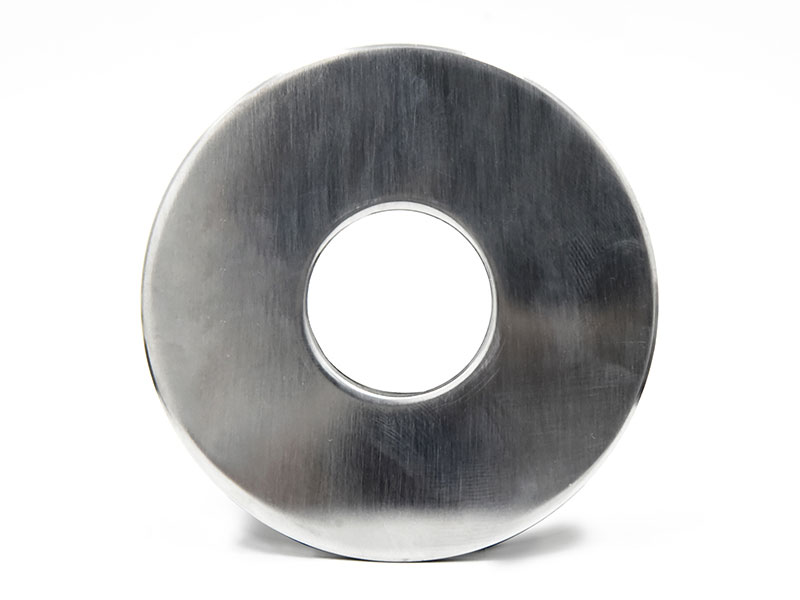
Polishing
Color: depends on material.
Finish Purpose: Improve the smoothness of the workpiece surface.

Brushing
Color: Silver, Matte finish.
Finish Purpose: Create decorative effect, enhance appearance.
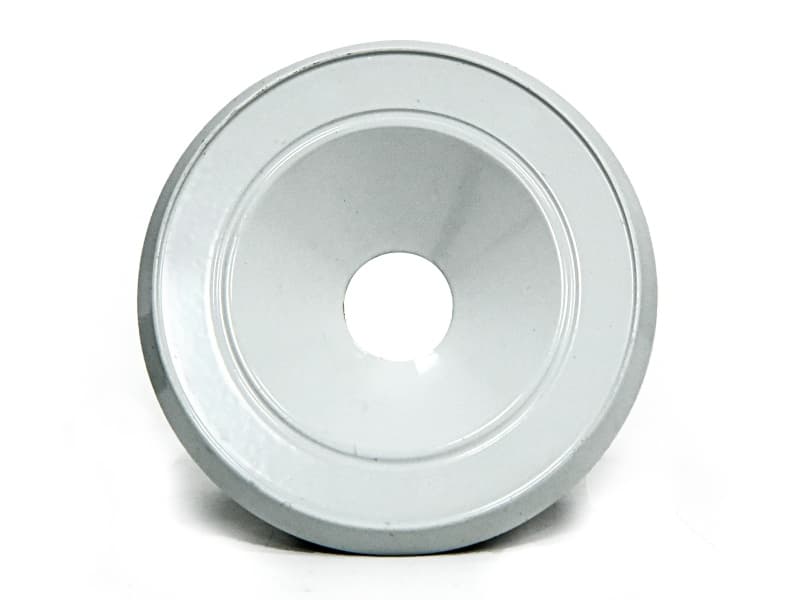
Powder Coating
Color: Various, e.g white, black.
Finish Purpose: Provide protective coating, improve appearance.
Other Surface Finishing Options
Finishes Option | Finishes Description | Application Materials | Finishes Color | Finishes Purpose | Price |
---|---|---|---|---|---|
Default Surface | This is the raw machined surface with tool marks, no post-processing, and a rough finish. | Metals, Plastic | Various (depends on material) | Basic finish, cost-effective | $ |
As machined | Parts are machined, deburred, and chamfered, with visible marks and light scratches. | Metals, Plastic | Various (depends on material) | Machining Decorative Patterns | $$ |
Tumbling | Parts are tumbled with abrasive media to deburr and polish. | Metals, Plastic | None (smooth surface) | Remove burrs, improve smoothness | $ |
Polishing | A process that reduces surface roughness to achieve a shiny, smooth finish. | Metals, Plastic | Various (depends on material) | Improve the smoothness of the workpiece surface | $$ |
Mirror Polishing | A finishing process that uses finer abrasives to create a reflective, mirror-like surface. | Metals, Plastic | Various (depends on material) | Improve material aesthetics, ease of cleaning, corrosion resistance, optical reflectivity | $$$ |
Bead Blasting | A cold working process that enhances fatigue life by blasting the surface with spherical media. | Metals | None (textured surface) | Improve fatigue life, enhance surface strength | $$ |
Sand Blasting | A process that uses compressed air to blast abrasives for cleaning or roughening. | Metals | None (textured surface) | Clean surface, increase roughness | $$ |
Brushing | A machining process where abrasive brushes create fine parallel lines on the surface. | Metals | Silver, Matte finish | Create decorative effect, enhance appearance | $$ |
Anodizing | An electrolytic process that thickens the natural oxide layer on metal parts. | Metals | Various (including clear, black, blue, red, green) | Improve corrosion resistance, provide decorative effect | $$$ |
Hardcoat anodizing | An electrochemical process that forms a hard oxide layer on aluminum to improve durability. | Metals | Black, Gray | Improve wear resistance and corrosion resistance | $$$ |
Black Oxide | A conversion coating process to blacken ferrous metals and provide corrosion resistance. | Metals | Black | Provide decorative effect, enhance corrosion resistance | $$ |
Passivation | A chemical process that removes iron from metal surfaces to enhance corrosion resistance. | Metals | None (smooth surface) | Improve corrosion resistance, increase smoothness | $$ |
Phosphating | A chemical process that enhances corrosion resistance and paint adhesion on steel. | Metals | Gray | Provide protection, promote paint adhesion | $$ |
Electrophoretic | A process that applies an organic or inorganic coating to metal using electrochemistry. | Metals | Various (including black white, red, green, champagne, blue) | Provide decorative effect, improve corrosion resistance | $$$ |
Electroplating | Electrochemical deposition of a metal coating to enhance appearance and corrosion resistance. | Metals | Various (depends on plating material) | Improve appearance, increase corrosion resistance | $$$ |
Electropolishing | Electrochemical polishing to smooth the surface, improving brightness and reducing roughness. | Metals | Mirror finish | Improve smoothness, enhance brightness | $$$ |
Chrome Plating | Applying a layer of chromium to a metal part to increase wear and corrosion resistance. | Metals | Silver | Improve wear and corrosion resistance | $$$$ |
Nickel Plating | Applying a layer of nickel to a metal part to improve corrosion resistance and appearance. | Metals | Silver | Improve corrosion resistance, enhance appearance | $$$ |
Copper Plating | Applying a copper layer to a metal part, often as a base for plating or as a conductive layer. | Metals | Copper Color | Provide base layer for additional plating, improve conductivity | $$$ |
Gold Plating | Applying a gold layer to improve conductivity, corrosion resistance, and decoration. | Metals | Gold | Improve conductivity, enhance corrosion resistance, provide decorative effect | $$$$ |
Silver Plating | Applying a layer of silver to a metal part to improve conductivity and corrosion resistance. | Metals | Silver | Improve conductivity, enhance corrosion resistance | $$$$ |
Tin Plating | Applying a tin layer to a metal part to prevent oxidation and improve solderability. | Metals | Silver | Prevent oxidation, improve solderability | $$ |
Zinc Plating | Applying a layer of zinc to a metal part to improve corrosion resistance. | Metals | Silver | Improve corrosion resistance | $$ |
PVD | A PVD process that creates a thin film on metal to improve wear and corrosion resistance. | Metals, Plastic | Various colors | Improve wear and corrosion resistance | $$$$ |
DLC Coating | Diamond-like carbon (DLC) coating that improves hardness and wear resistance of metal. | Metals | Black | Improve hardness and wear resistance | $$$$ |
Titanium Nitride Coating(PVD) | Applying a titanium nitride coating through PVD to improve wear and corrosion resistance. | Metals, Plastic | Gold, Black | Improve wear and corrosion resistance | $$$$ |
Chrome Nitride Coating(PVD) | Applying a chrome nitride coating through PVD to improve wear and corrosion resistance. | Metals, Plastic | Silver | Improve wear and corrosion resistance | $$$$ |
Powder Coating | Applying a powder coating with electrostatic spray and curing it to form a protective layer. | Metals, Plastic | Various (depends on powder color) | Provide protective coating, improve appearance | $$$ |
Painting | Applying paint in layers to the metal surface for protection and decoration. | Metals, Plastic | Various (depends on paint color) | Provide protective and decorative coating | $$ |
Heat Treatment | Using heat to alter the physical and mechanical properties of the metal. | Metals | None (depends on material) | Improve hardness, strength, and durability | $$ |
Laser Marking | Using a laser to mark the metal surface, providing permanent identification. | Metals, Plastic | Various (depends on material) | Provide permanent identification | $$ |
Cleaning | Using various methods to clean the metal surface, removing contaminants and impurities. | Metals, Plastic | None (depends on material) | Remove contaminants, improve surface quality | $ |
CNC Machined Parts Edge Options
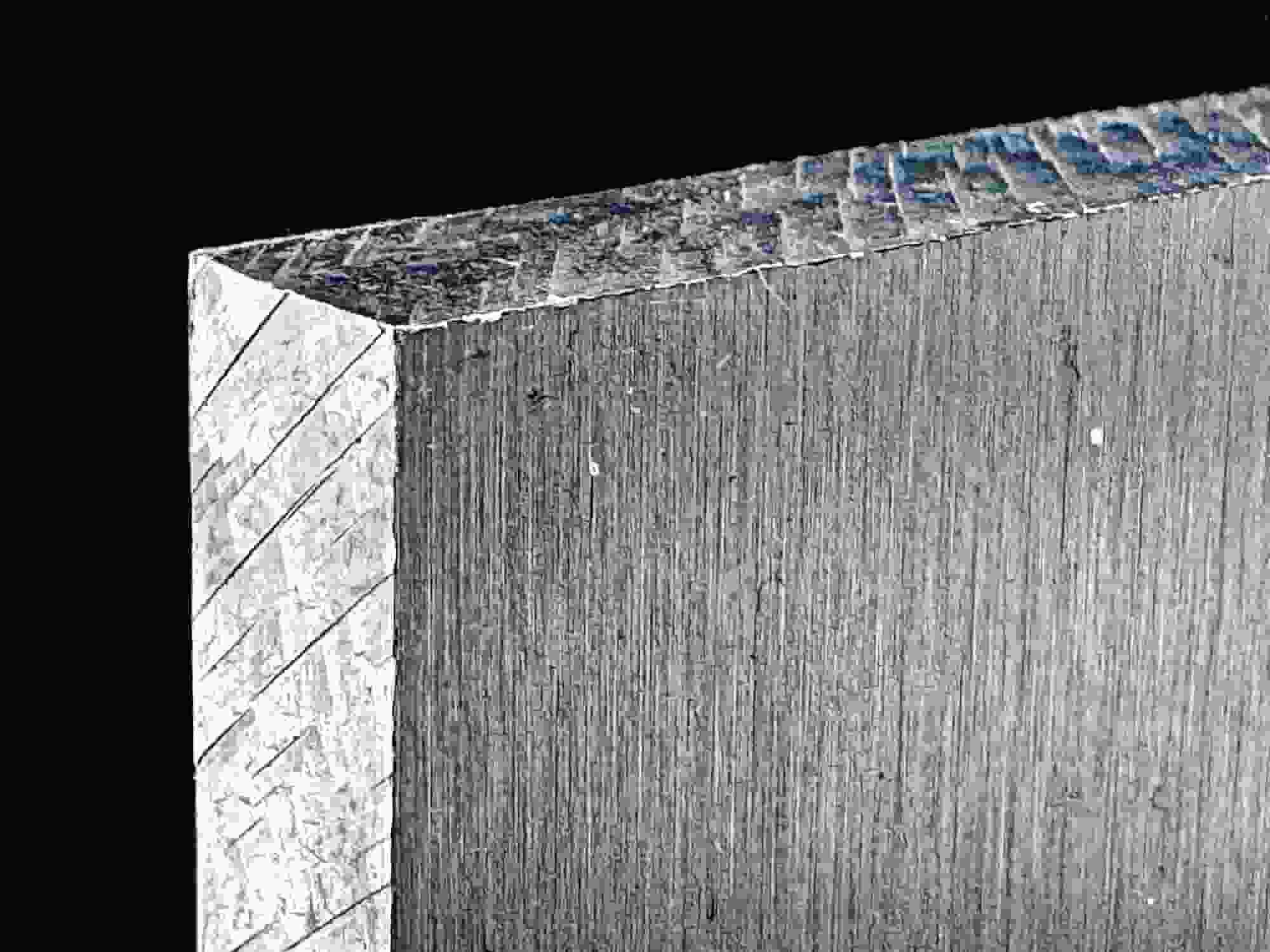
Original Machined Edge
Purpose: Retain original burrs and edges.
Shape: Rough, irregular with burrs and sharp angles.
Application: For parts requiring extra machining or testing.
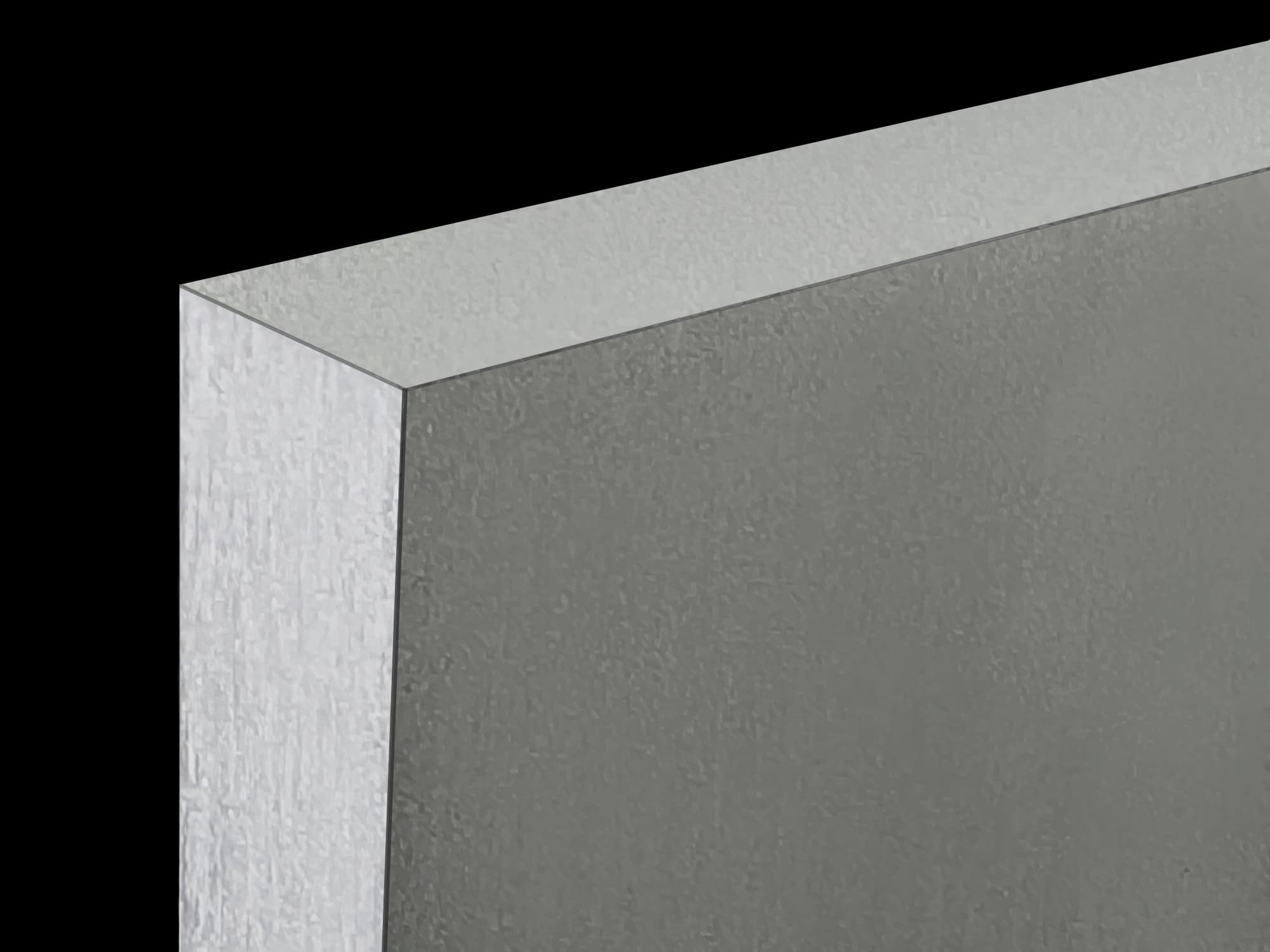
Deburred Edge
Purpose: Remove burrs to ensure smooth and safe edges.
Shape: No fixed shape, eliminates sharp protrusions.
Application: For all parts to ensure safety and functionality.
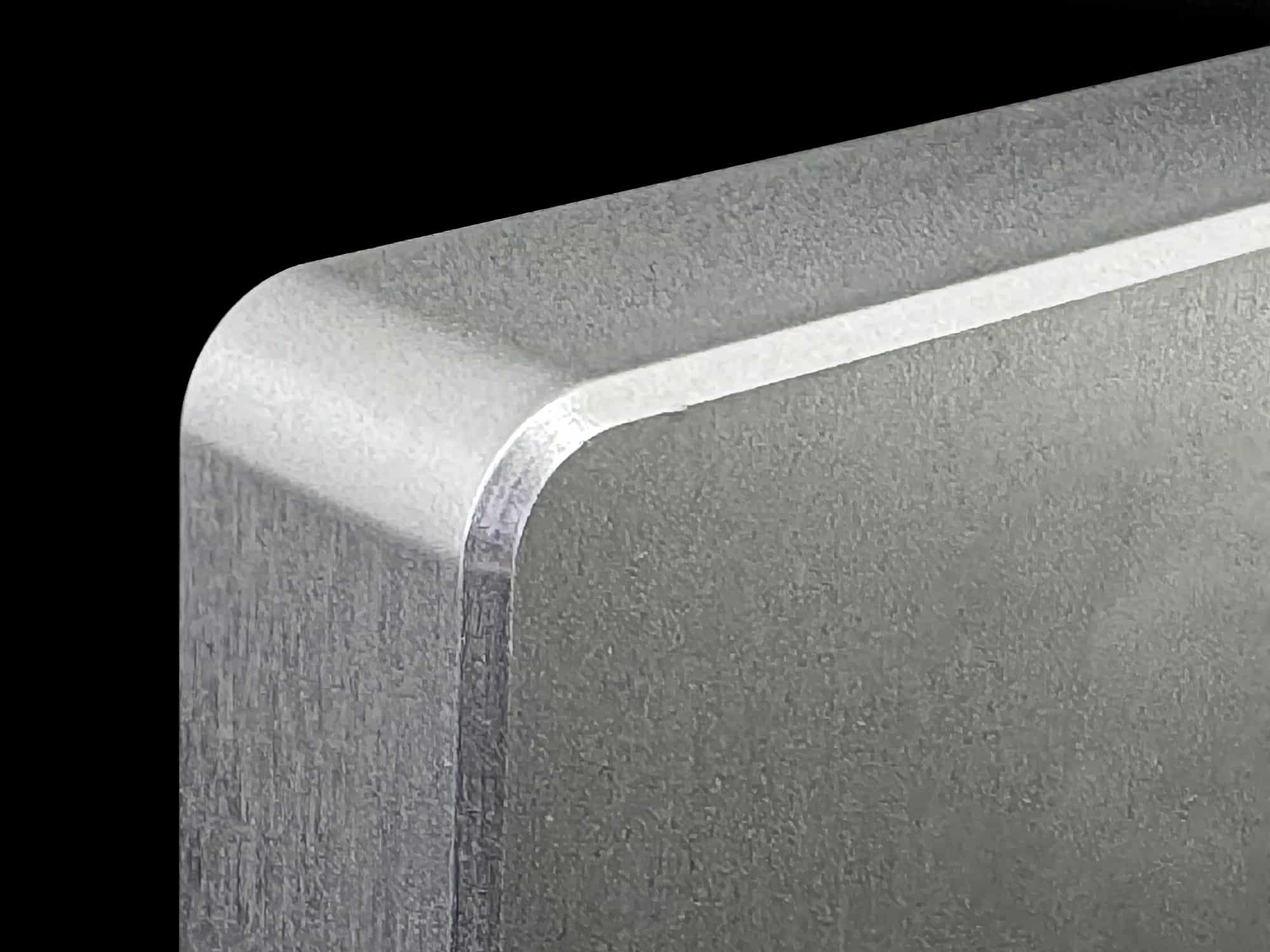
Chamfered Edge
Purpose: Chamfer for precision and edge removal.
Shape: Straight chamfer, typically at a 45-degree angle.
Application: For parts requiring precise angles.
How to Choose the Right Surface Treatment for Your Parts?
Appearance Enhancement
1. Mirror Polishing
Automotive interior parts (such as metal decorative strips)
Electronic device casings (such as mobile phone frames)
2. Brushing
Consumer electronics (such as laptop casings)
Interior decoration parts (metal door handles, lamps)
3. Anodizing
Aluminum alloy casings of mobile phones and laptops
Industrial design products (such as instrument casings)
4. Electroplating
High-end automotive exterior parts (such as door handles, logos)
High-end bathroom accessories (such as faucets, showers),
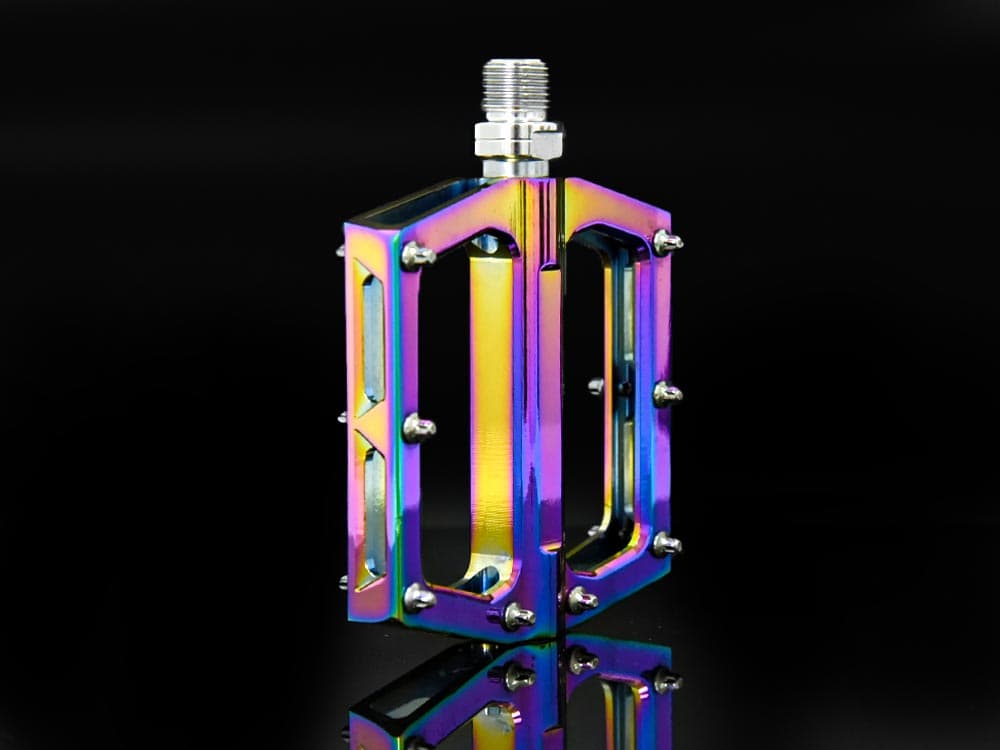
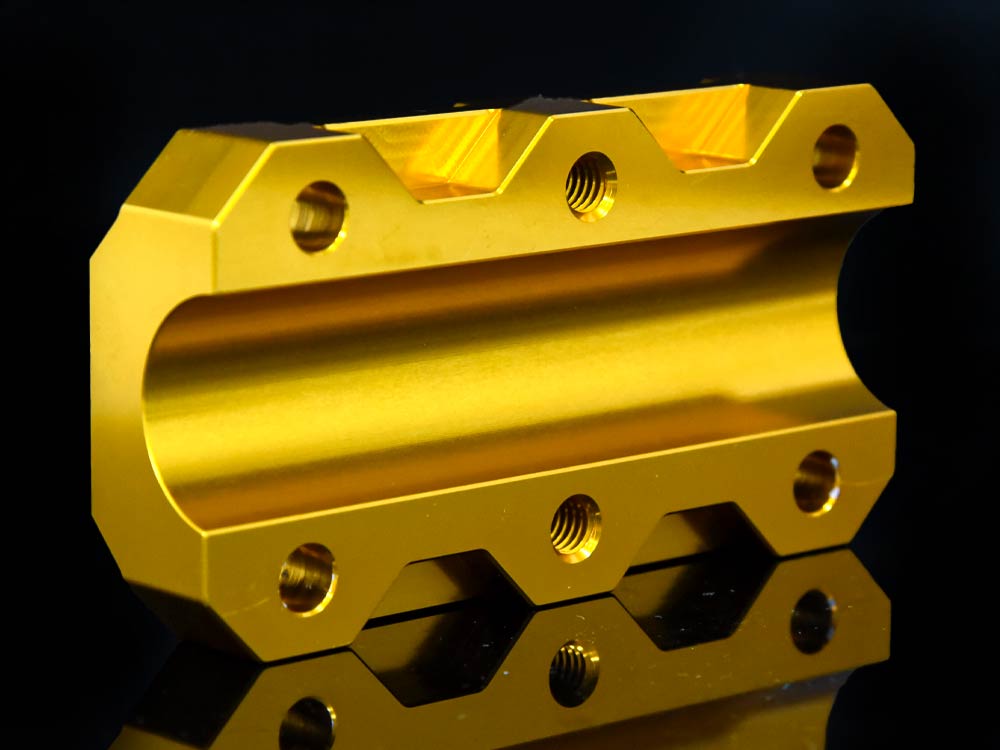
Corrosion Resistance Enhancement
1. Hardcoat Anodizing
Aerospace parts (such as fuselage structural parts, brackets)
Industrial machinery parts (such as hydraulic cylinders, valve bodies)
2. Anodizing
Automotive decorative parts (such as door handles, roof racks)
Sports equipment (such as bicycle frames, fitness equipment)
3. Powder Coating
Automotive chassis and accessories (such as wheels, bumpers)
Industrial equipment housing (such as machine guards, electrical control cabinets)
4. Passivation
Medical equipment (such as surgical tools, implants)
Electronic components (such as connectors, screws)
Wear Resistance Enhancement
1. DLC Coating
High-performance engine parts (such as piston rings, camshafts)
Precision mechanical parts (such as rolling bearings, gears)
2. Titanium Nitride Coating (PVD)
Mold parts (such as injection molds, stamping molds)
Precision mechanical parts (such as valves, bearings)
3. Hardcoat Anodizing
Industrial machinery parts (such as hydraulic cylinders, gears)
Outdoor sports equipment (such as bicycle frames, mountaineering tools)
4. Chrome Plating
Automotive parts (such as piston rods, steering columns)
Household hardware (such as faucets, door handles)
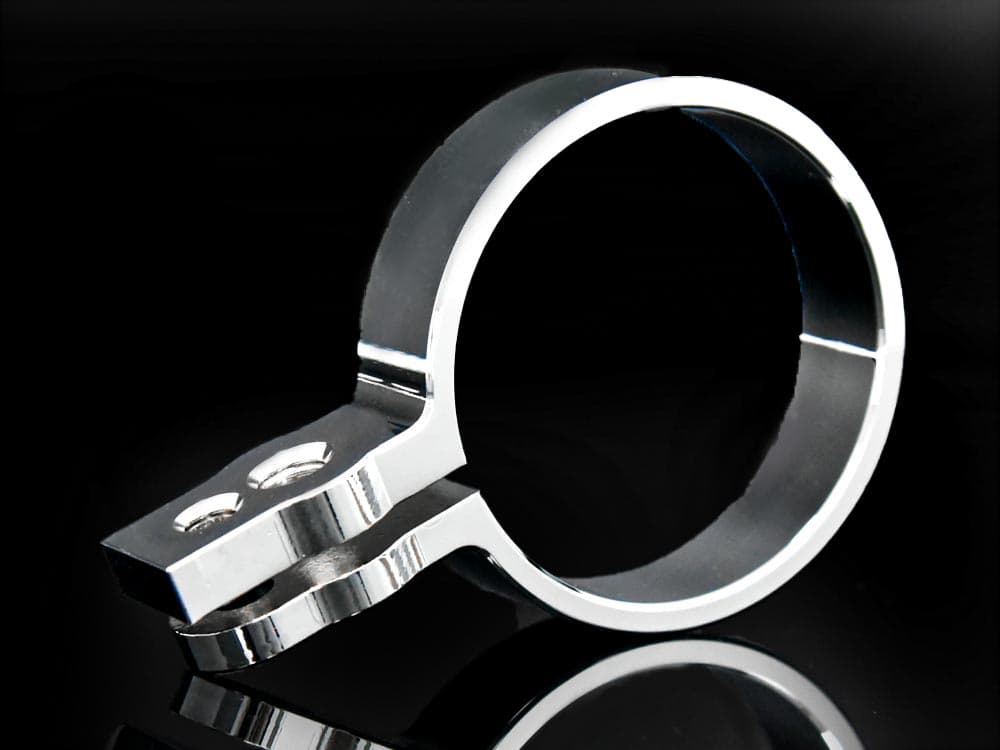
Xielifeng Finishinig Services Case Studies
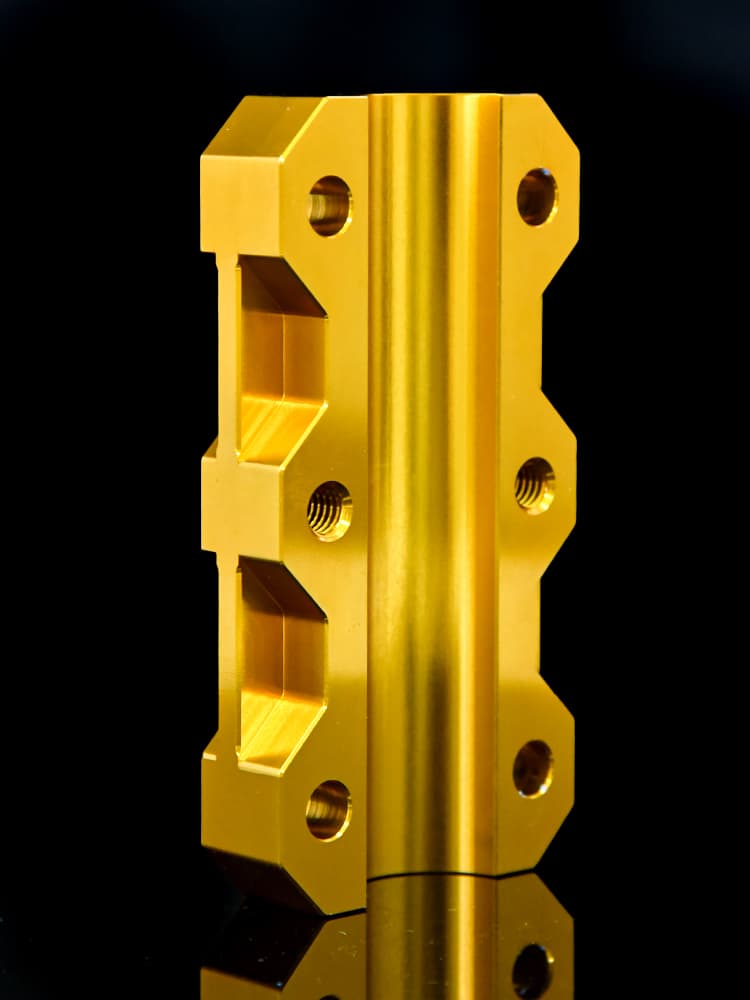
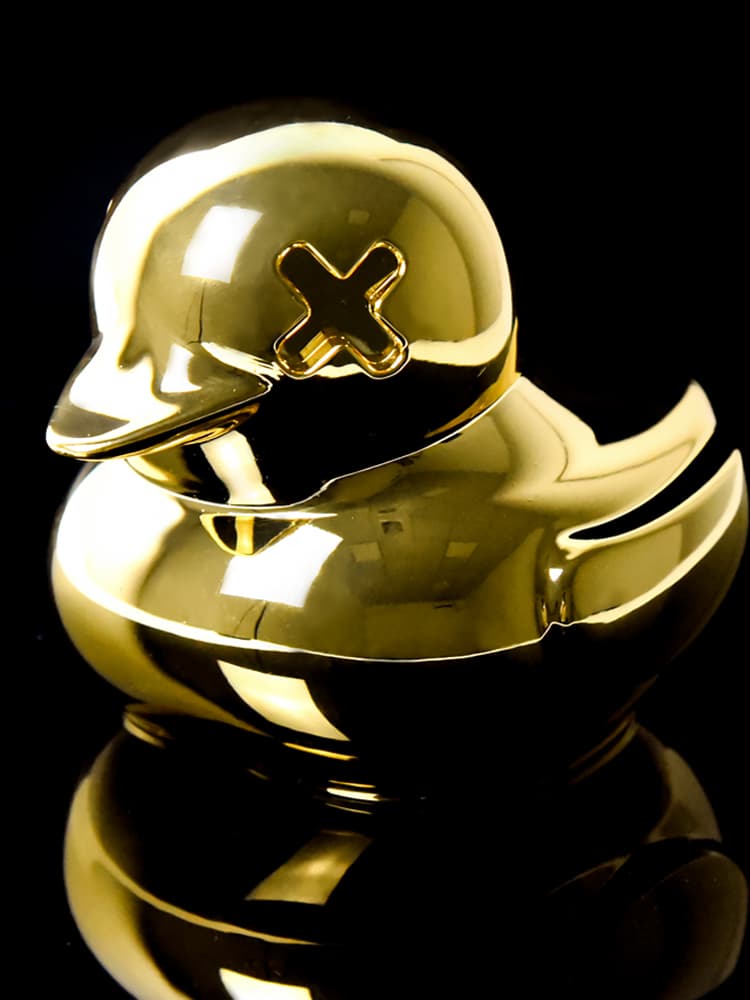
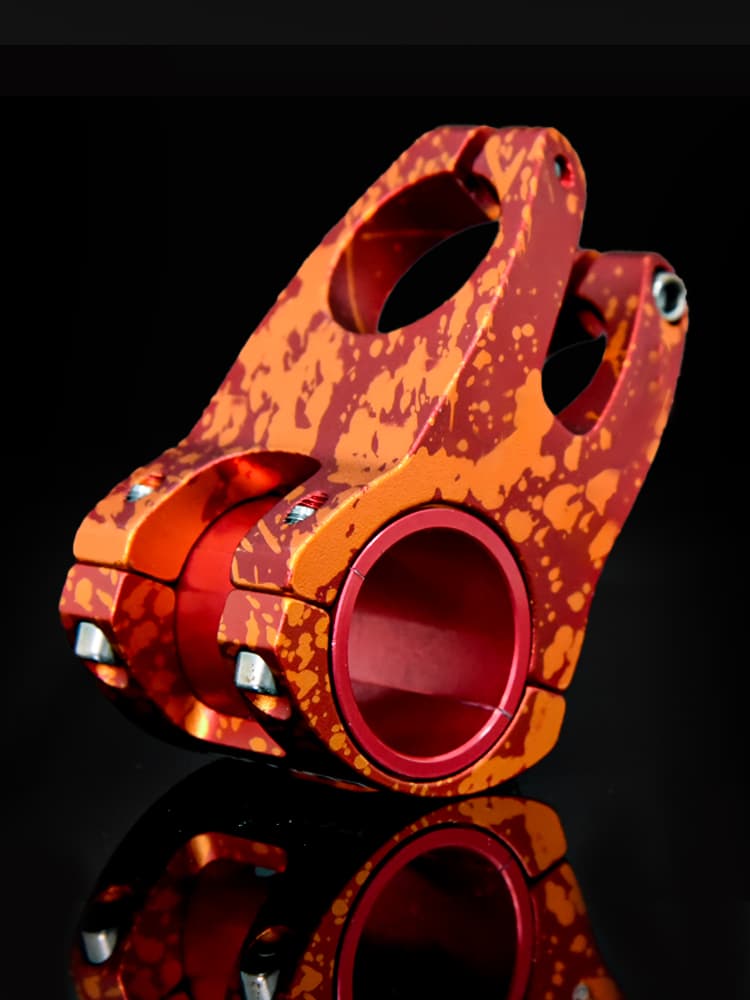
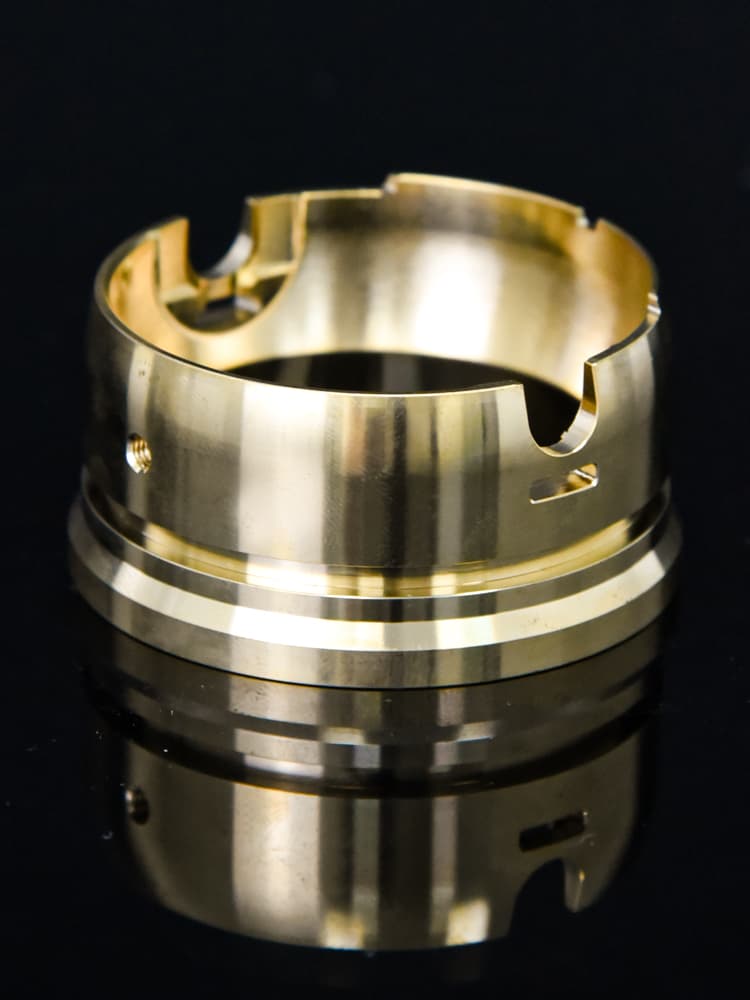
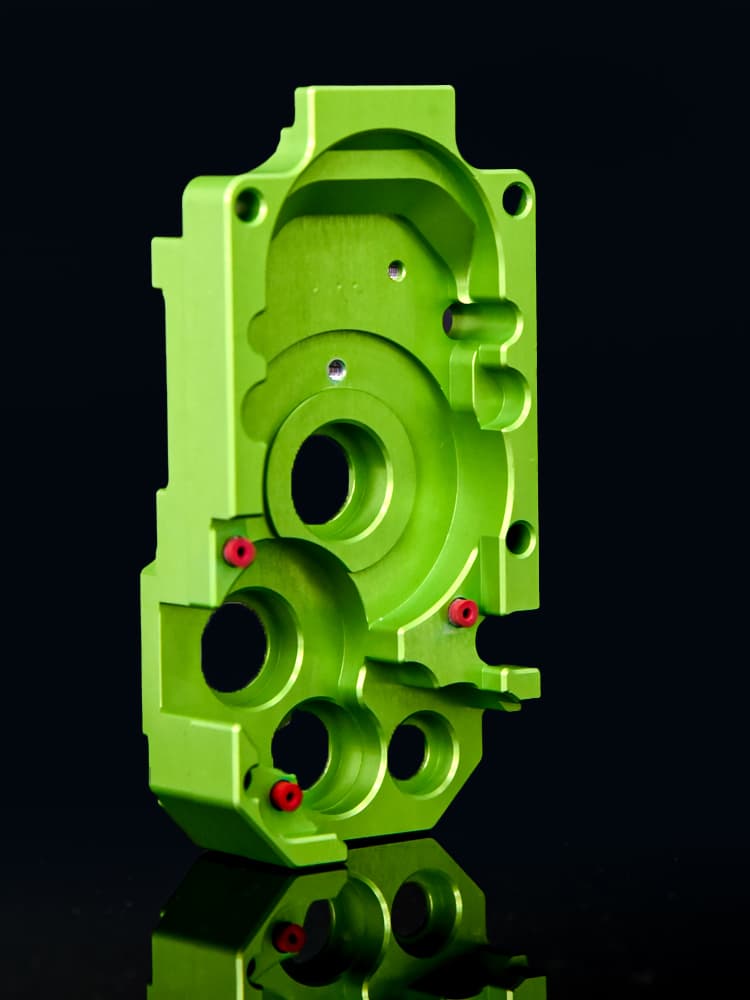
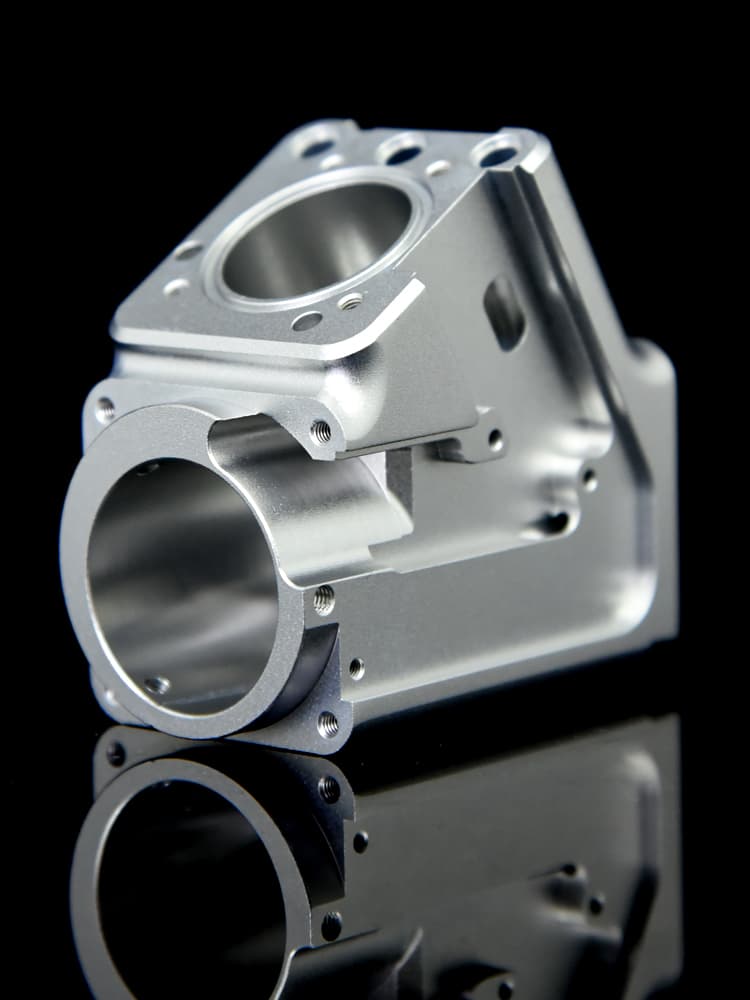
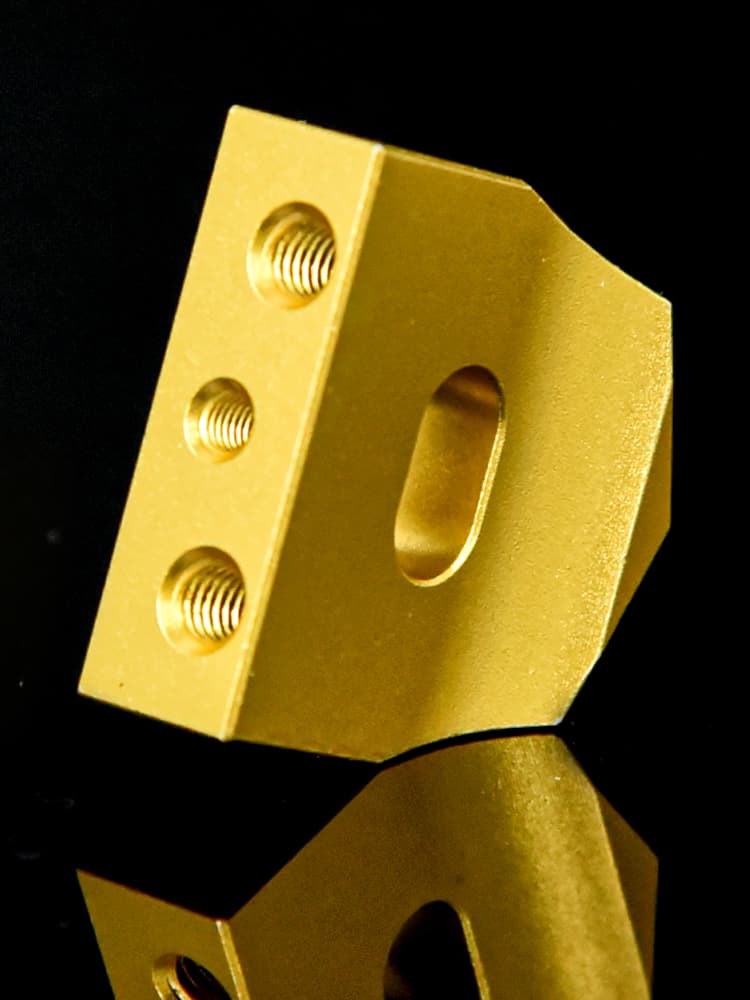
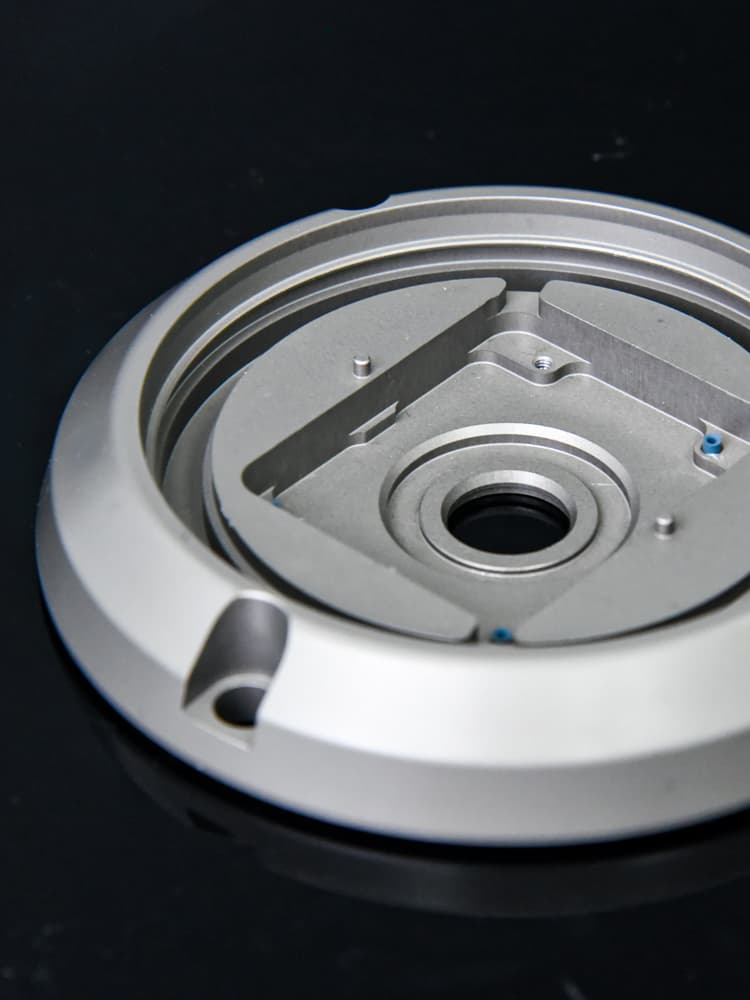
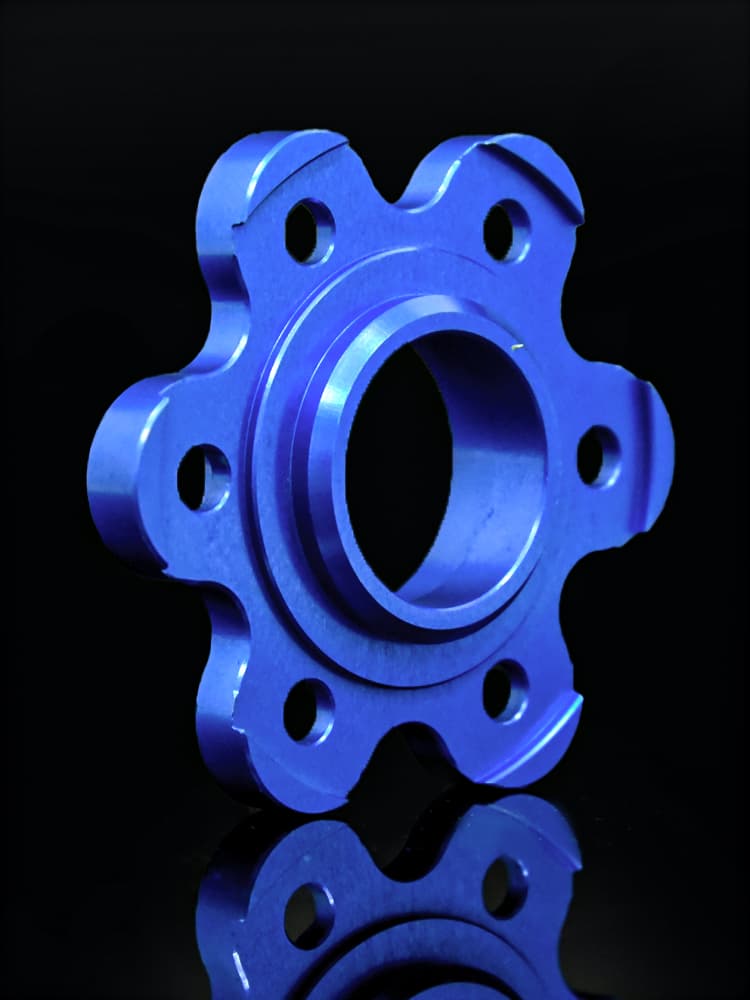
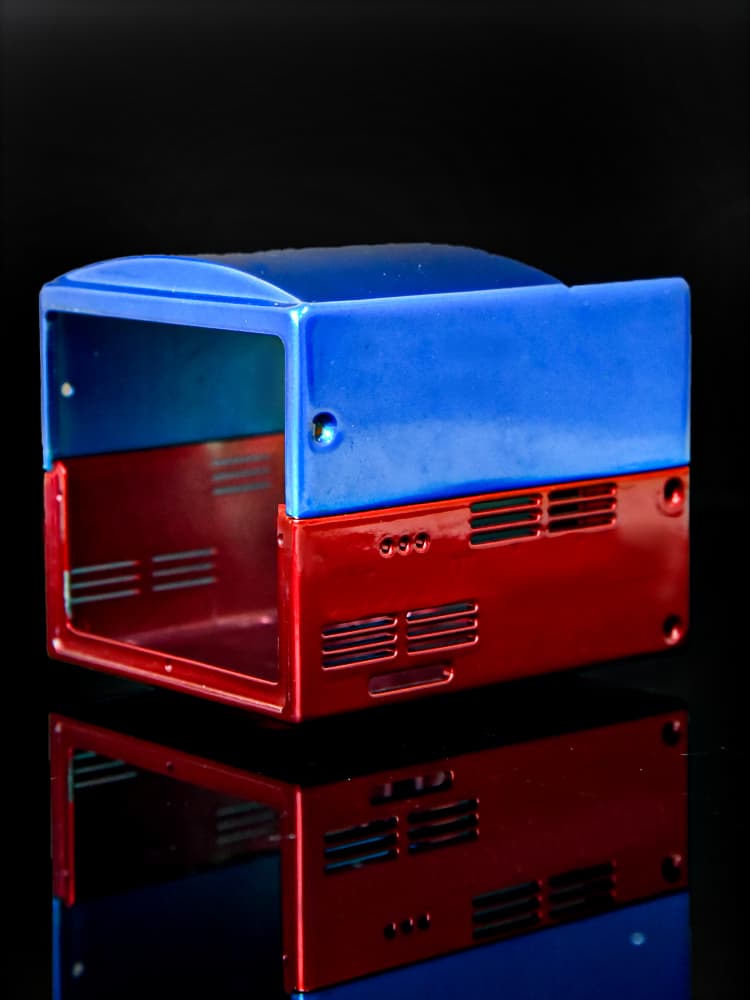
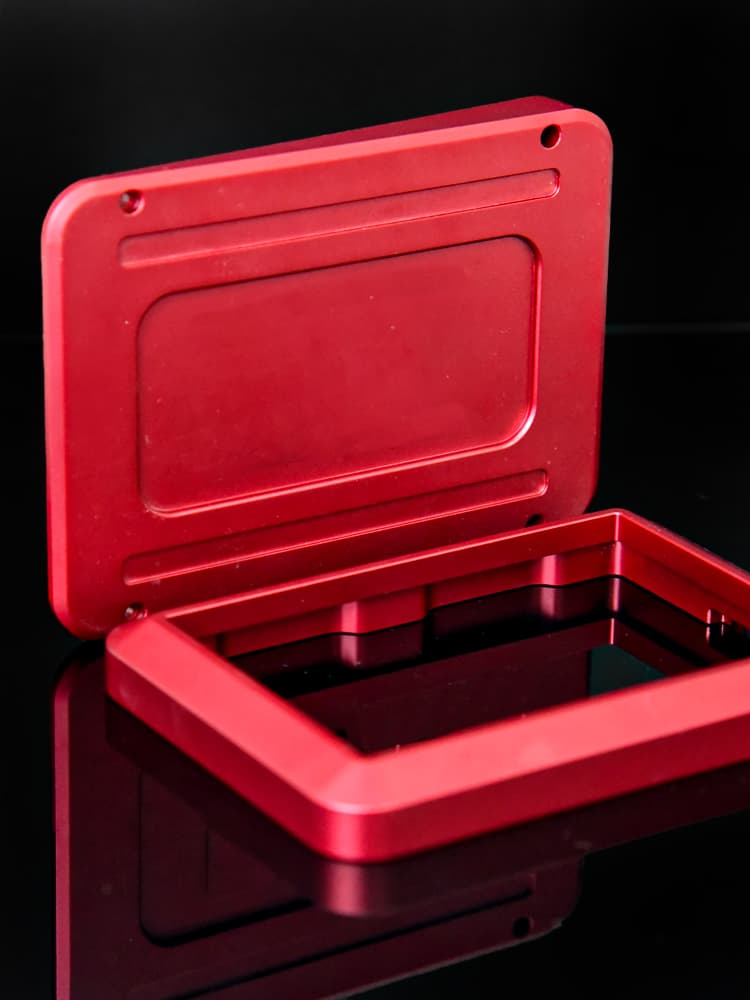
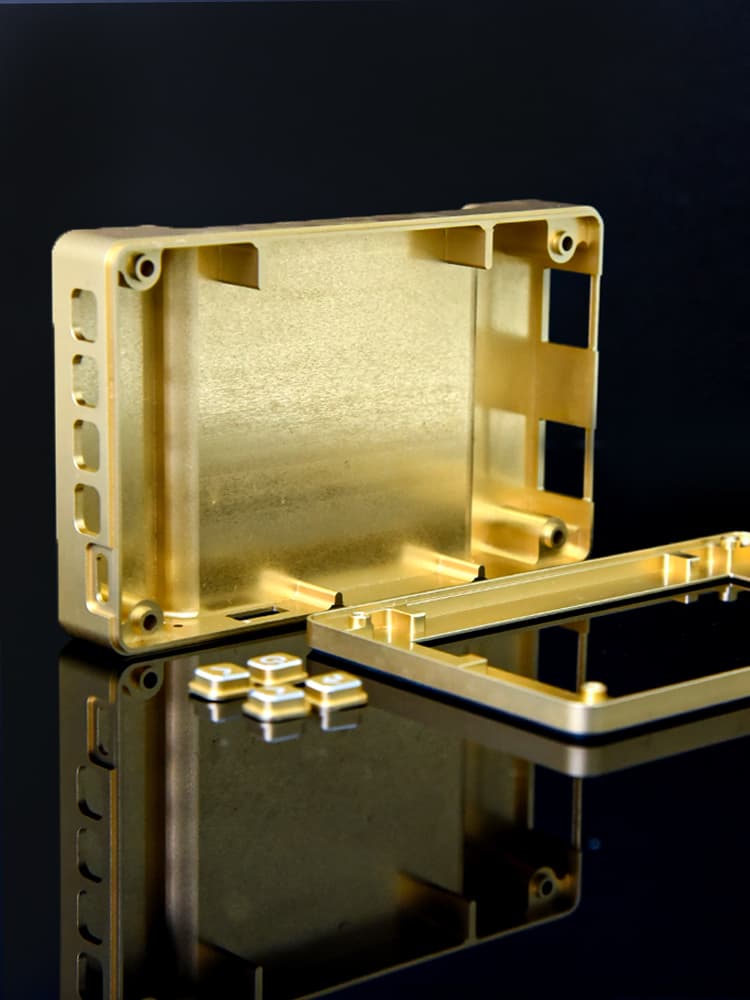
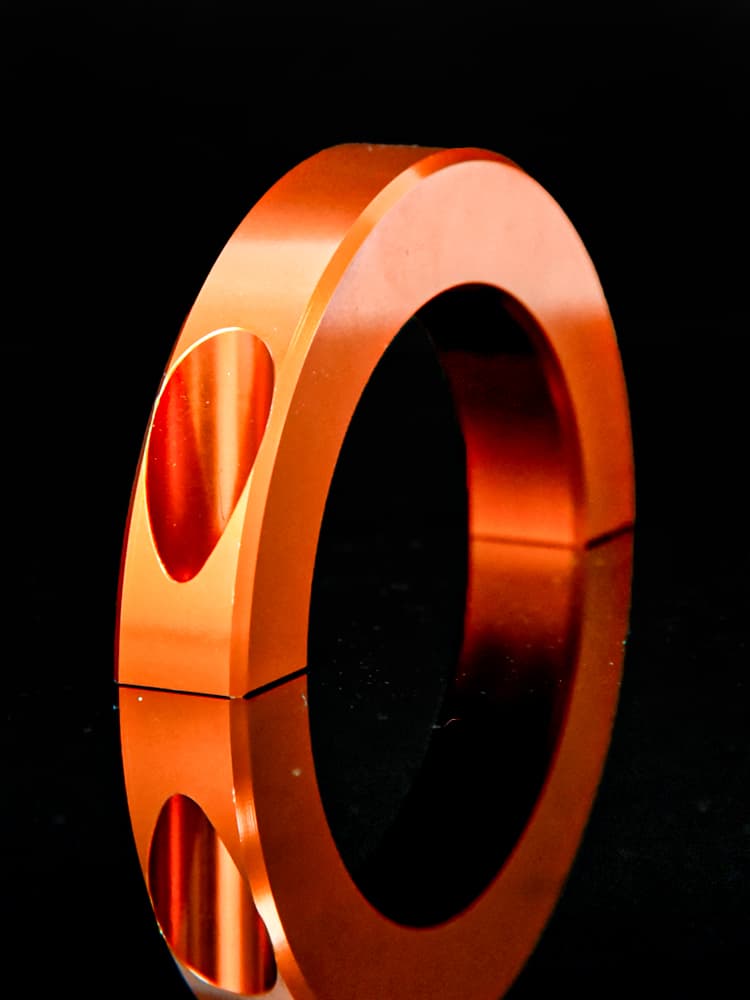
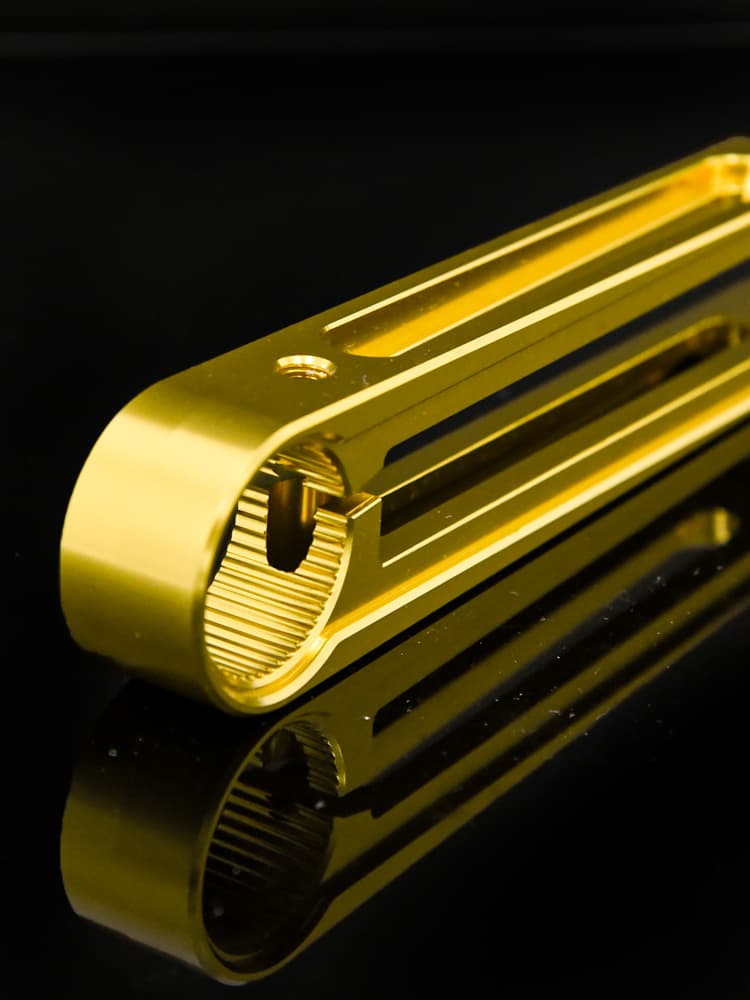
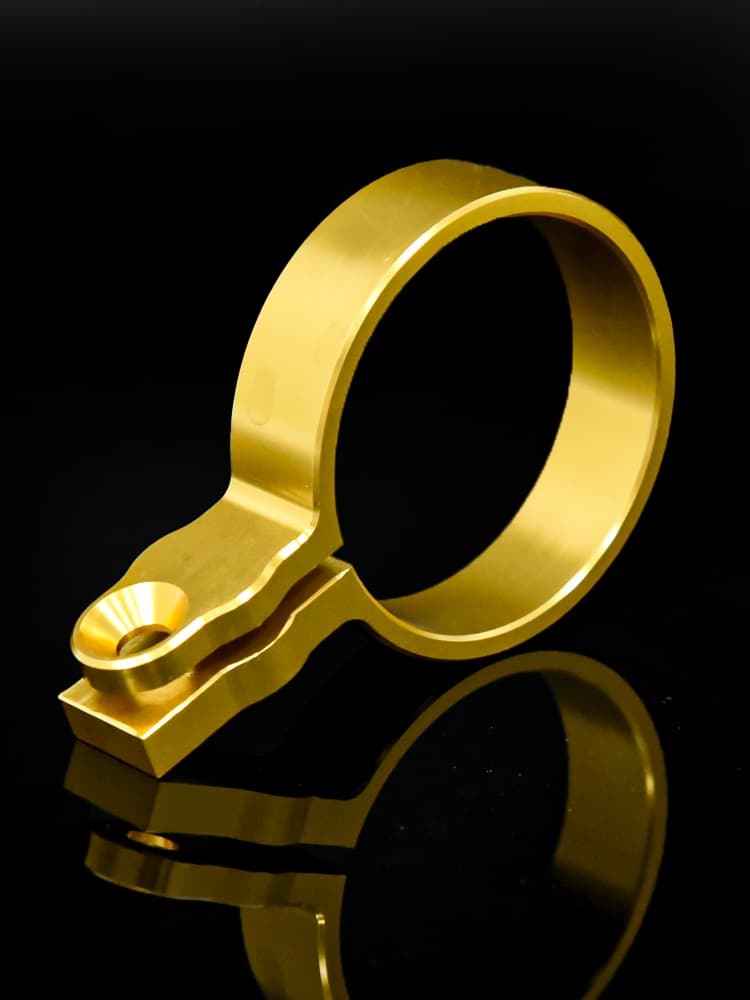
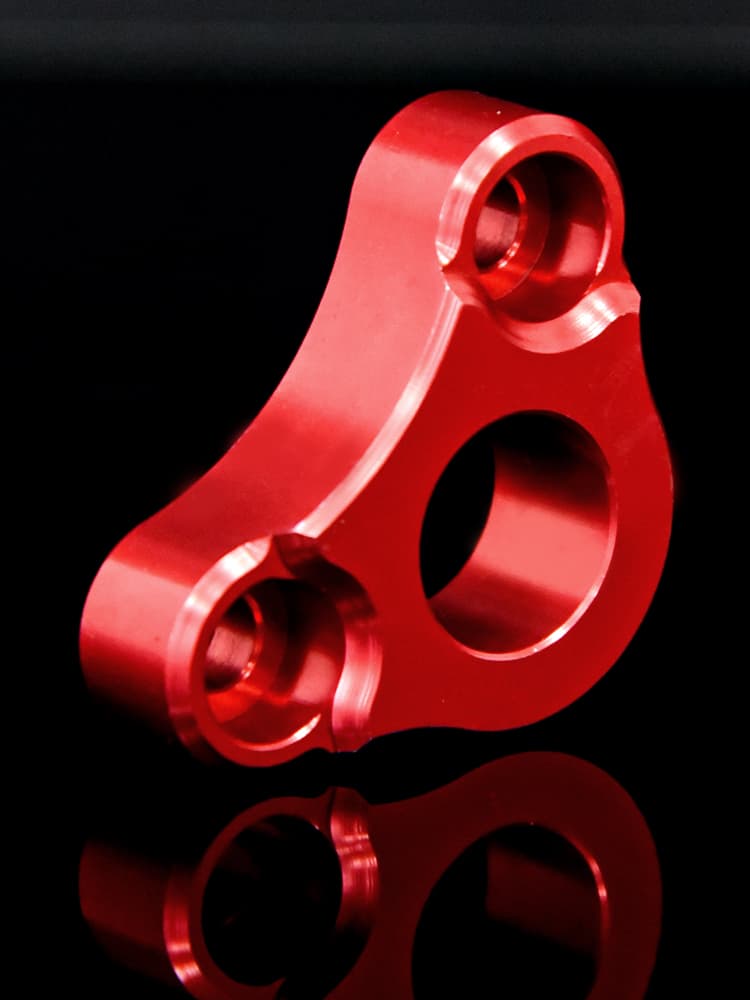
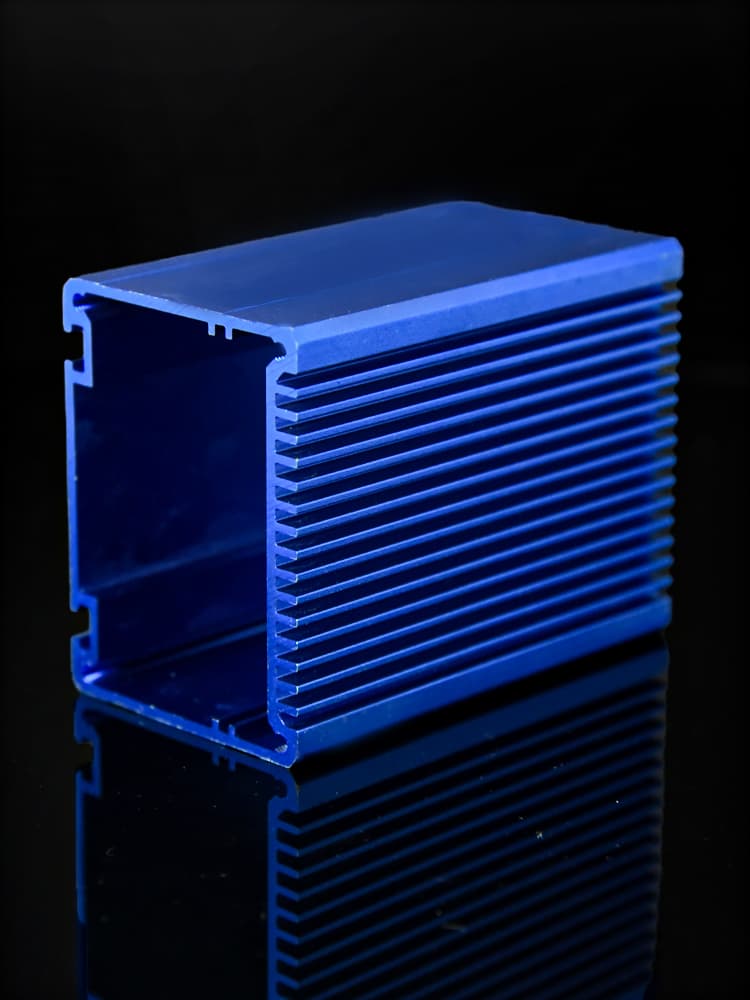
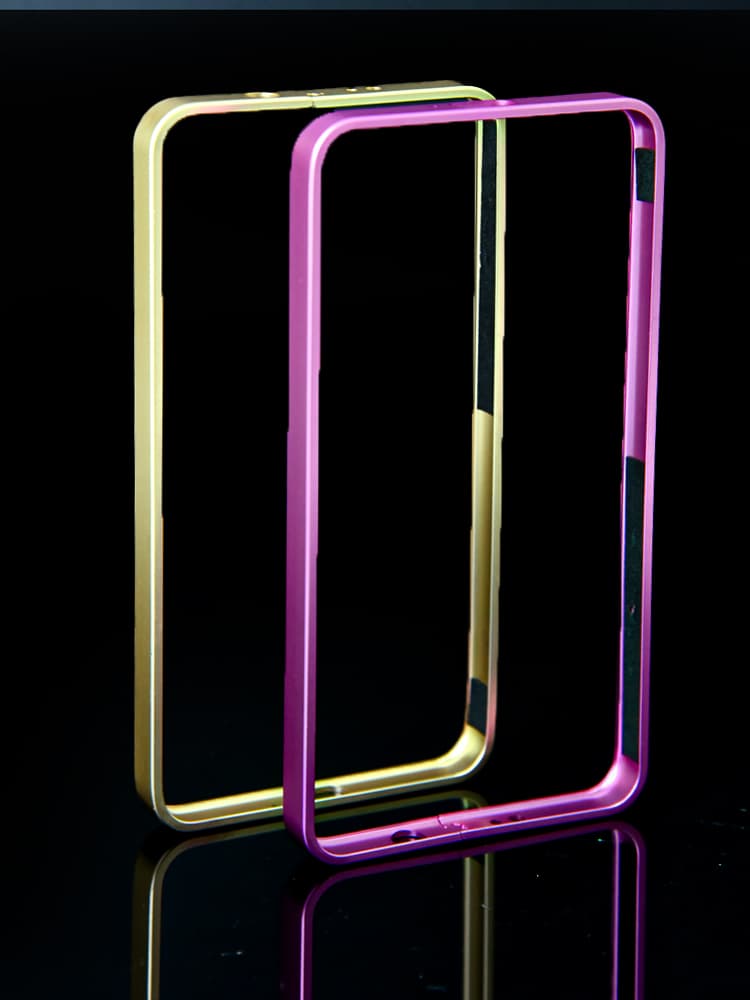
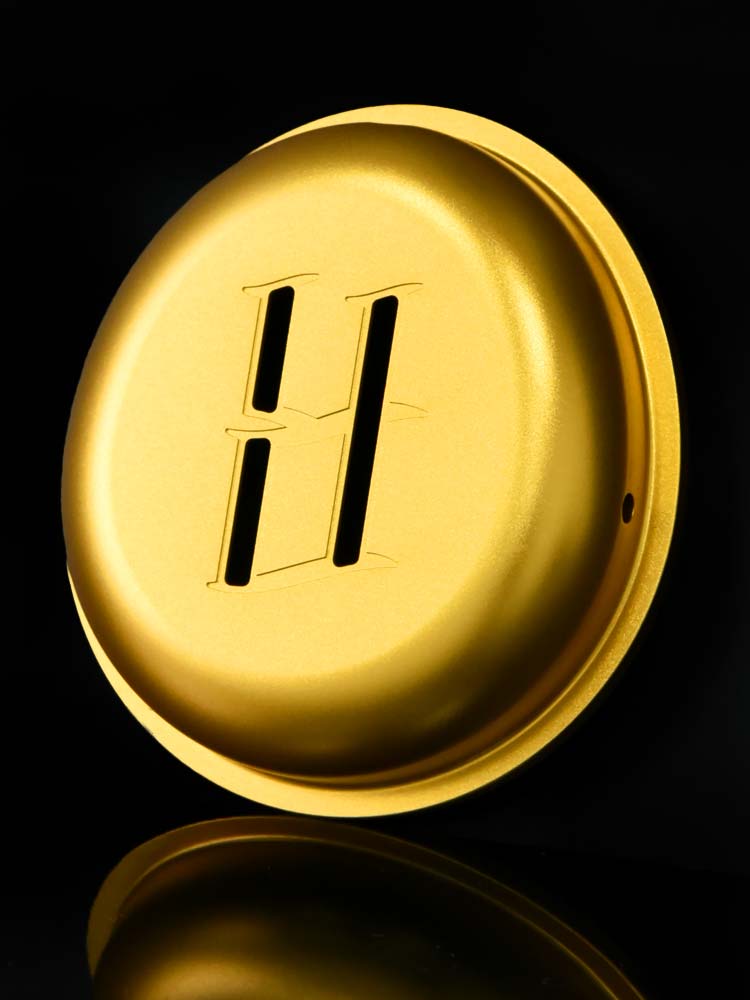
Why Xielifeng is Your First Choice?
At Xielifeng, we offer high-quality machining and premium surface treatments.
With advanced inspections and strict quality control, every part meets top standards. Choose us for quality and trust.
We look forward to creating value together.
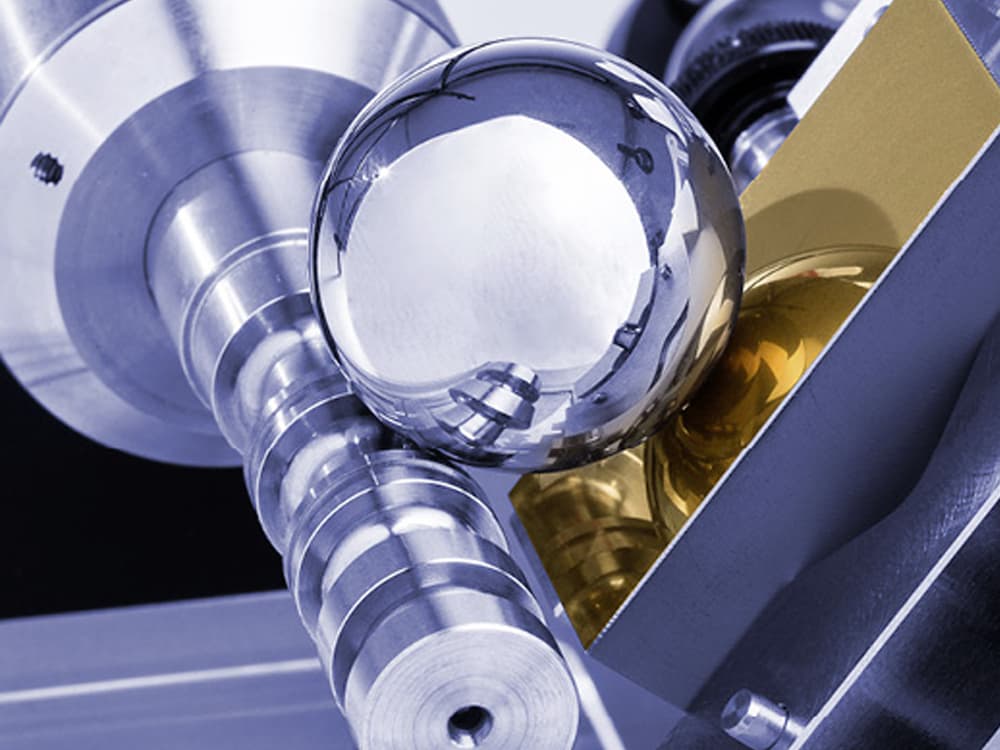
01
Coating Thickness Testing
We use XRF spectrometers, eddy currents, and magnetic thickness gauges to control coating thickness precisely. Rigorous testing ensures ideal protection without compromising part tolerance or performance.
02
Coating Hardness Testing
We use Vickers, Rockwell, and microhardness testers to measure precise coating hardness. Whether enhancing wear resistance or surface hardness, our equipment ensures coatings meet design requirements and extend part lifespan.
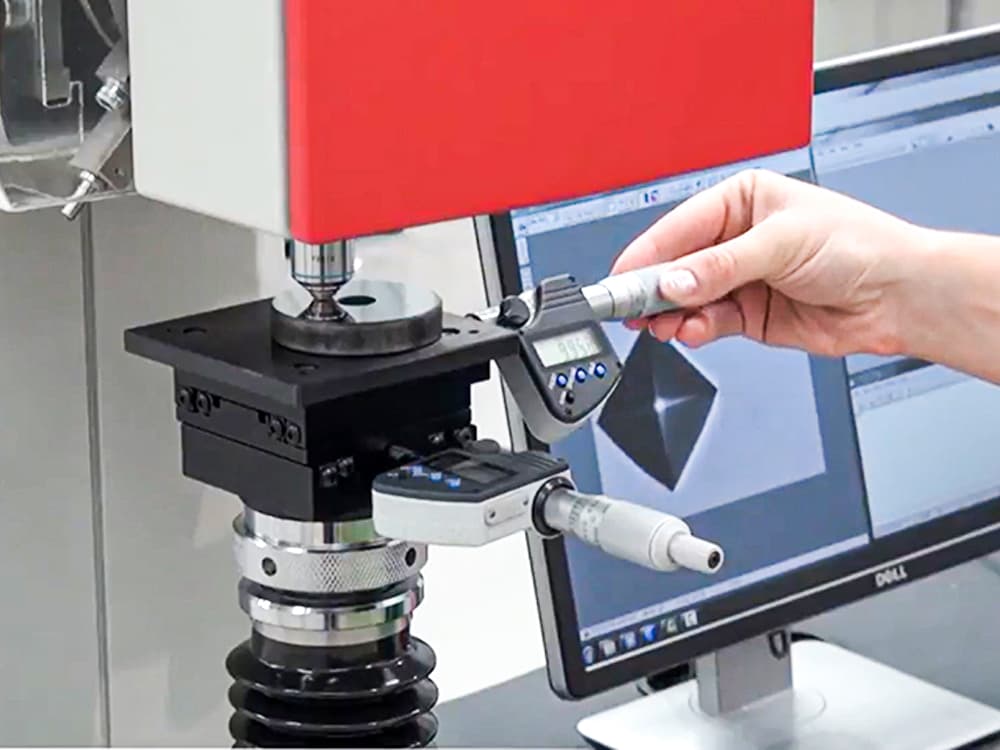
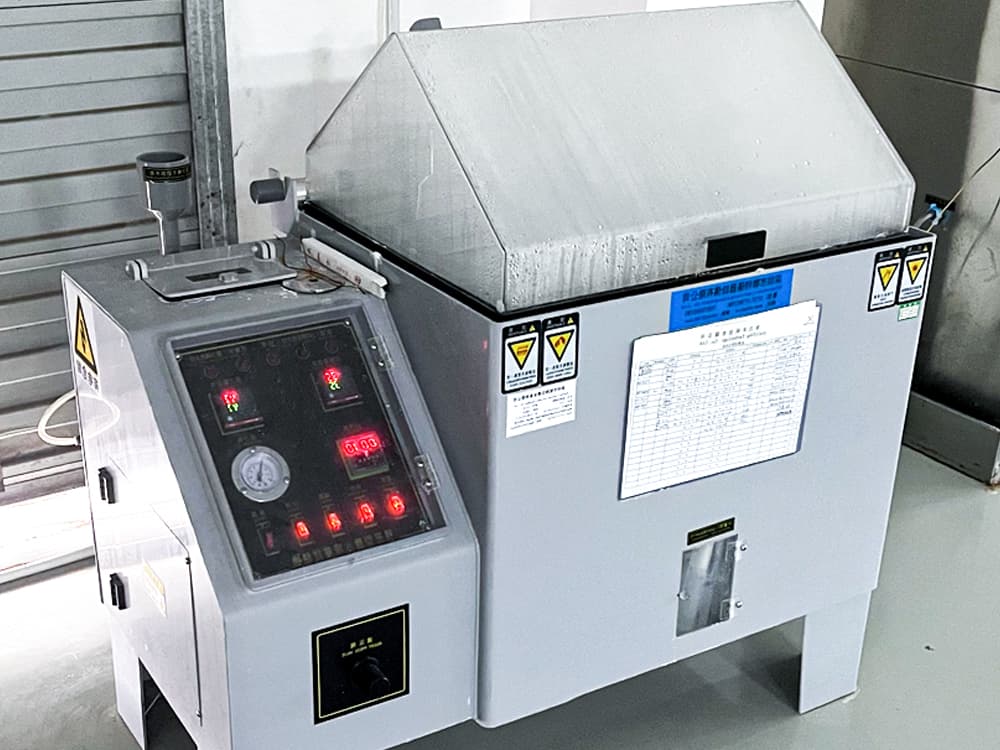
03
Coating Corrosion Resistance Testing
Our salt spray tester simulates harsh conditions to evaluate coating corrosion resistance, ensuring every part resists long-term corrosion while maintaining top performance and appearance.
04
Coating Adhesion Testing
We accurately assess coating adhesion using scratch testers, tensile testers, and cross-cut testers. We ensure the coating is firmly bonded to the substrate, preventing peeling or detachment, thus enhancing part reliability and durability.
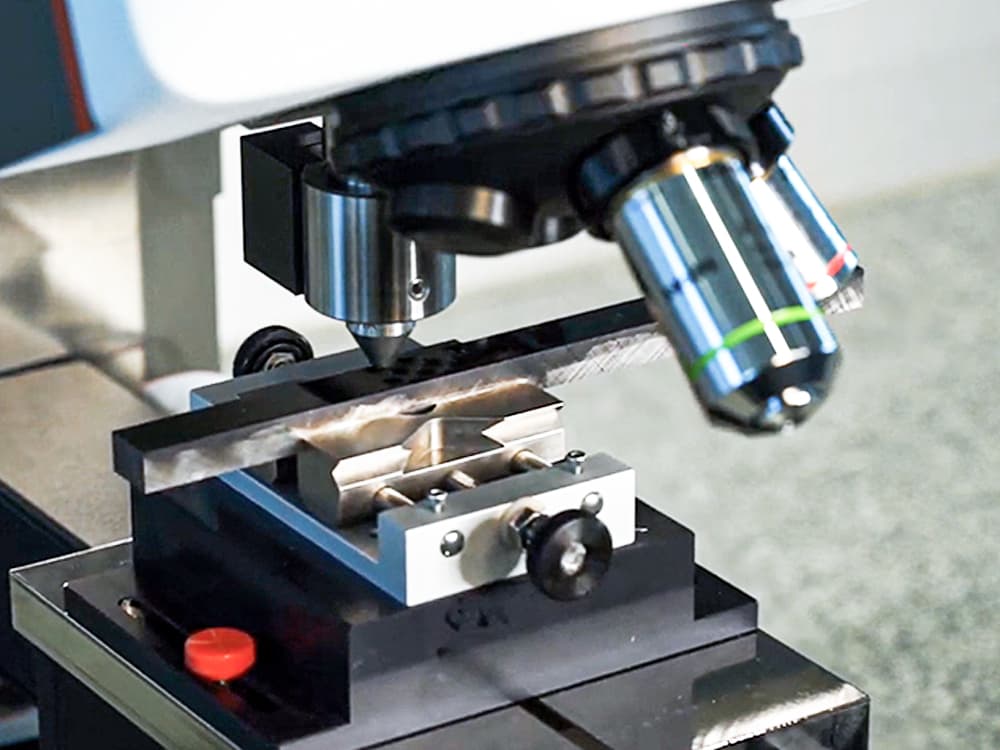
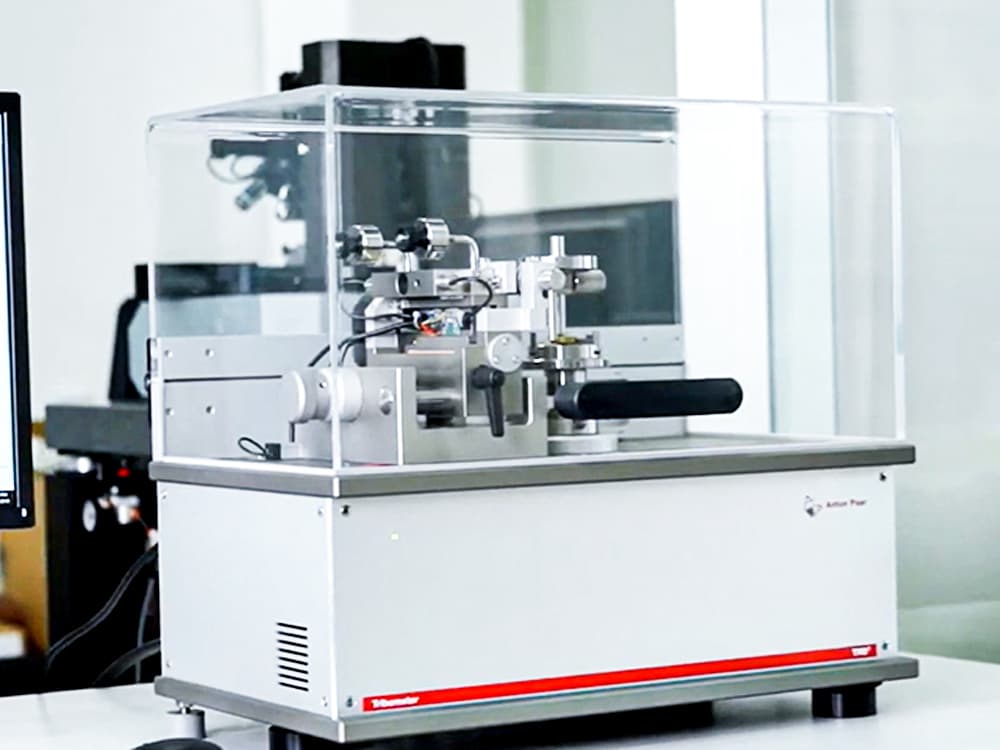
05
Coating Wear Resistance Testing
Using a Taber Abraser and friction tester, we evaluate the wear resistance of coatings. Whether in high-friction environments or in daily use, our coatings maintain excellent durability, extending the lifespan of the parts.
06
Coating Microscopy and Imaging Analysis
We are equipped with a scanning electron microscope (SEM) and optical microscope to examine the microstructure and surface morphology of coatings closely. This enables us to identify and resolve minor defects, ensuring flawless coating quality in every layer.
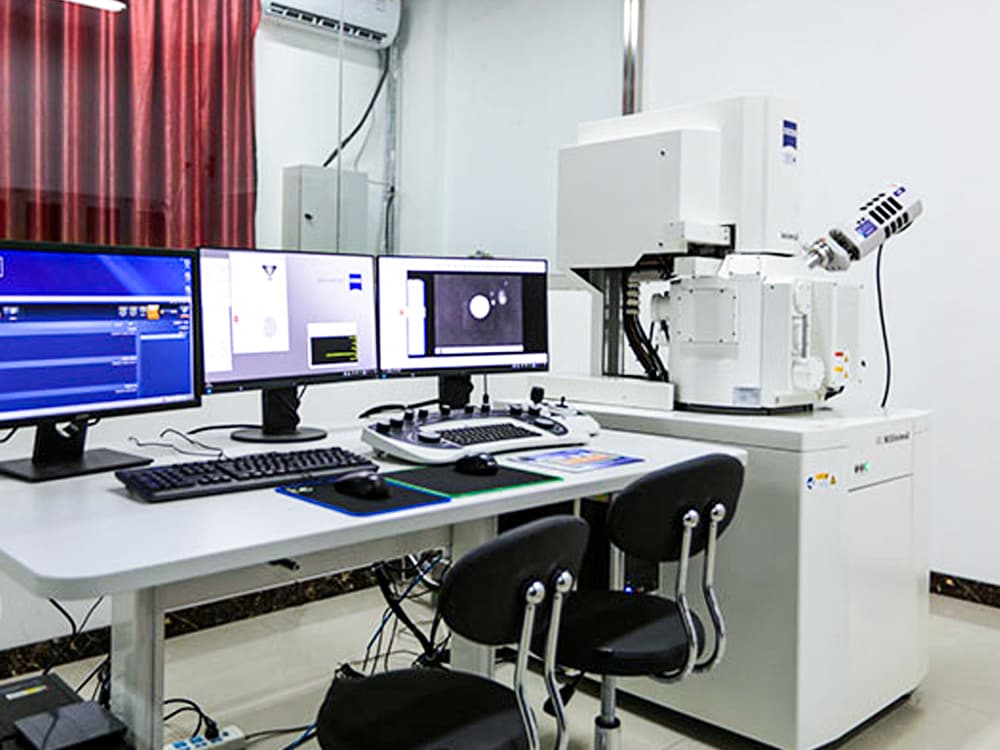
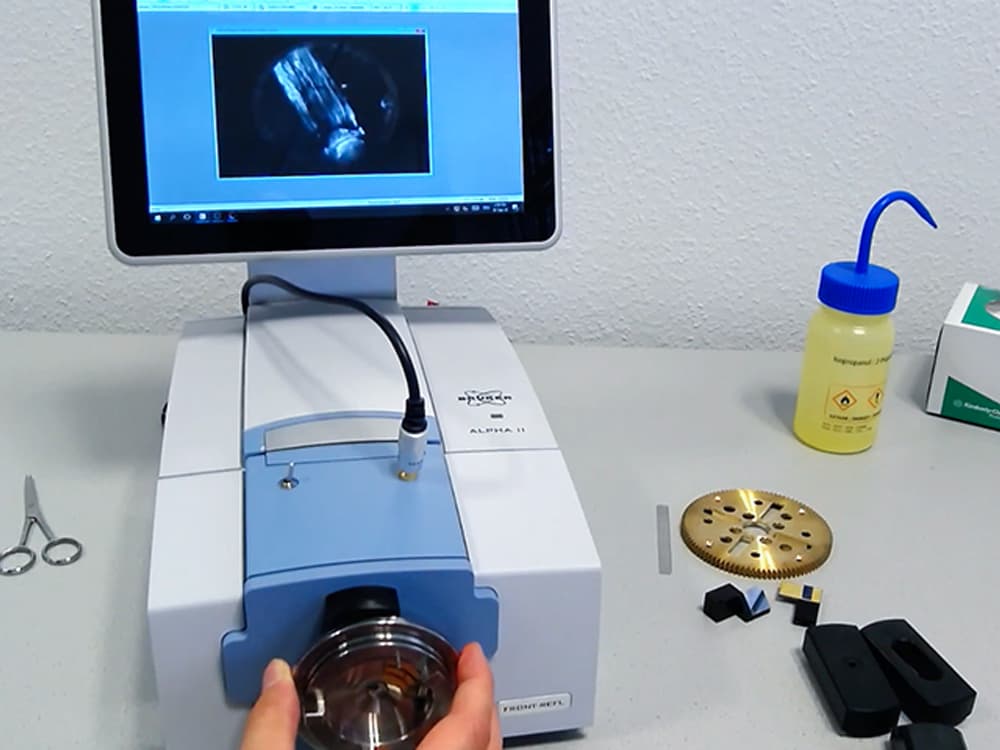
07
Coating Chemical Analysis
We conduct an in-depth analysis of the coating’s chemical composition and electrochemical properties using an electrochemical workstation and FTIR. This ensures the coating’s chemical stability and protective performance meet various specialized application requirements.
08
Coating Color and Appearance Testing
Our colorimeter and visual inspection tools precisely measure coating color consistency and appearance quality. No matter the customer’s demands, we rigorously test to deliver products that exceed expectations.
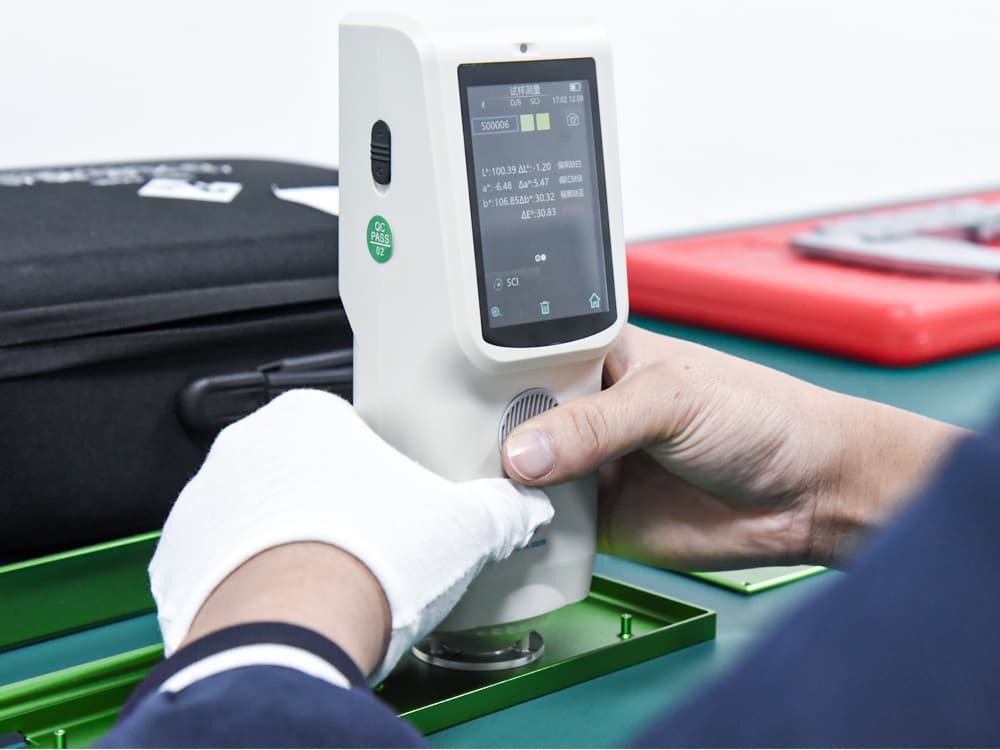