Trust Our QC
Achieve Your Success
5-Step QC Process
97.8% On-Time Delivery Rate
7800+ Global Clients
ISO 9001 & ISO 14001 Certified
All uploads are secure and confidential.* Learn More
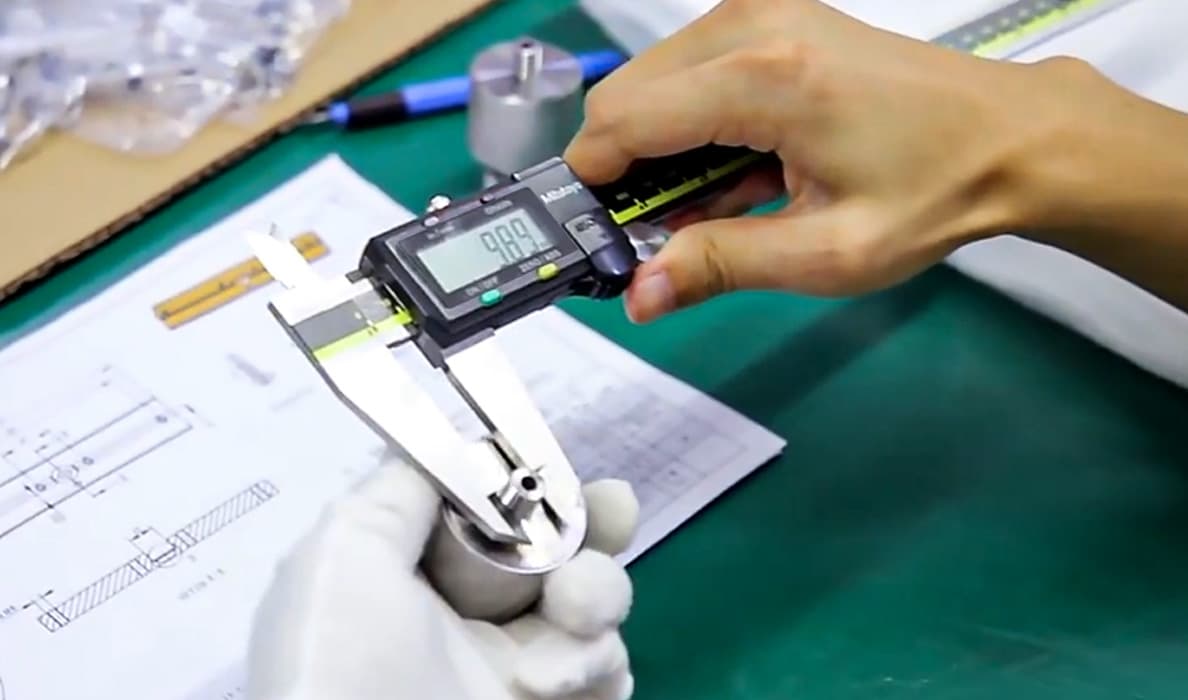
IOS 9001
IOS 14001

Xielifeng Quality Control Team
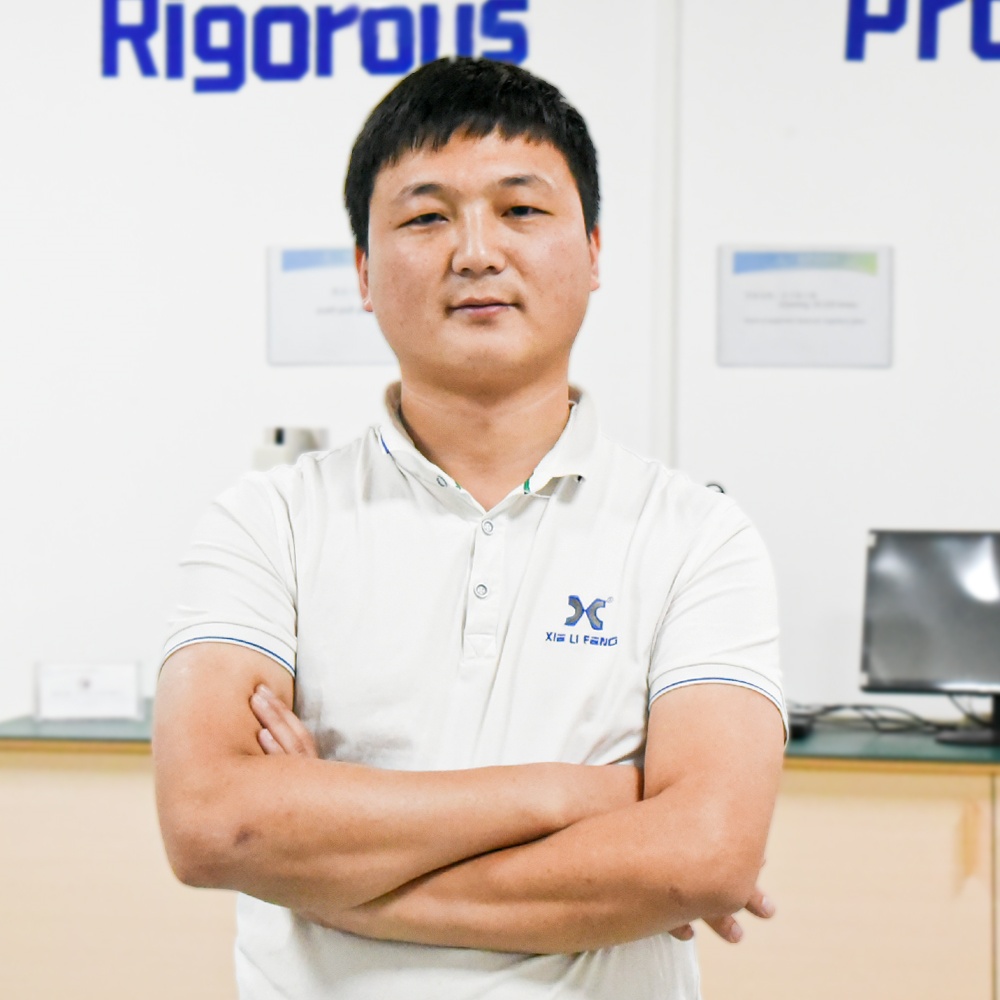
Quality Manager (QM)
Jason Yu
Develop and implement the factory's quality management system.
Oversee and assess QC processes to meet international standards and customer requirements.
Manage and guide the QC team, conducting quality training and performance evaluations.
Handle customer complaints and feedback, driving quality improvement projects.
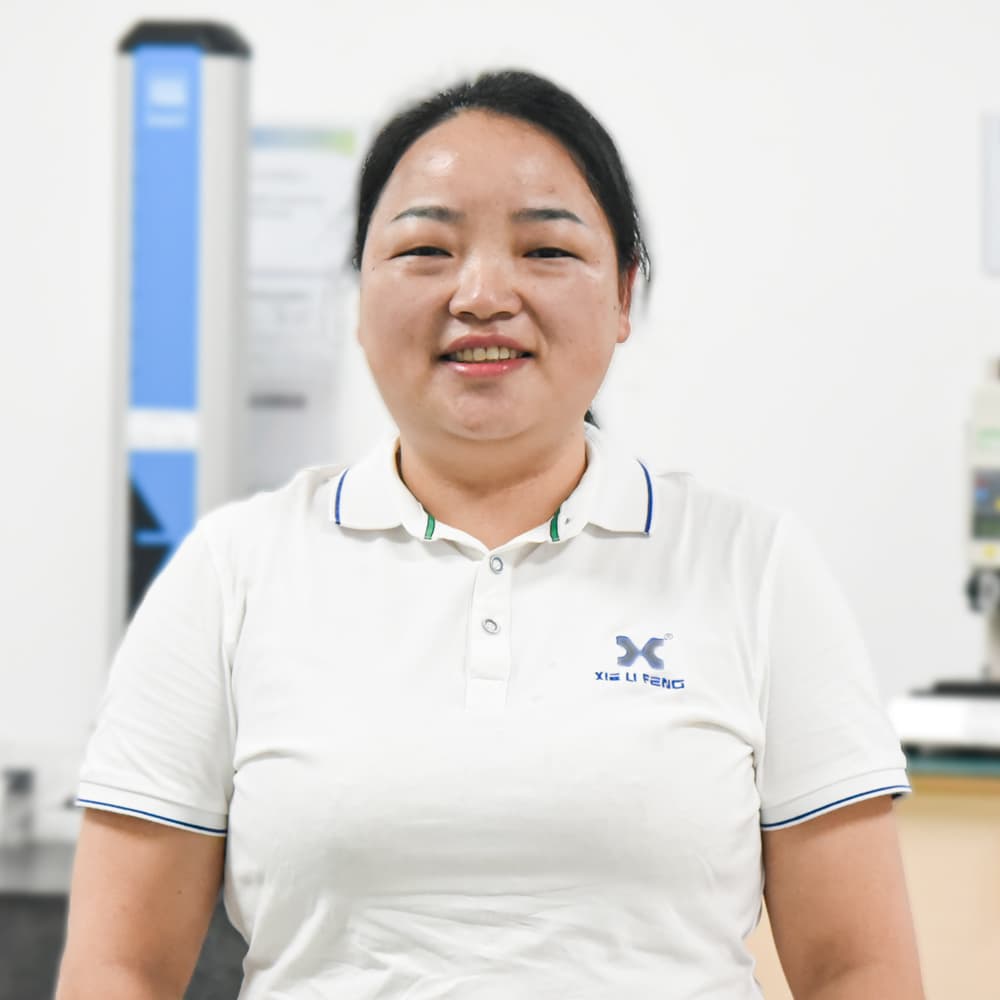
Fiona Lu
Position: SQE
Responsible for maintaining supplier quality relationships, monitoring performance, and assisting in quality improvement.
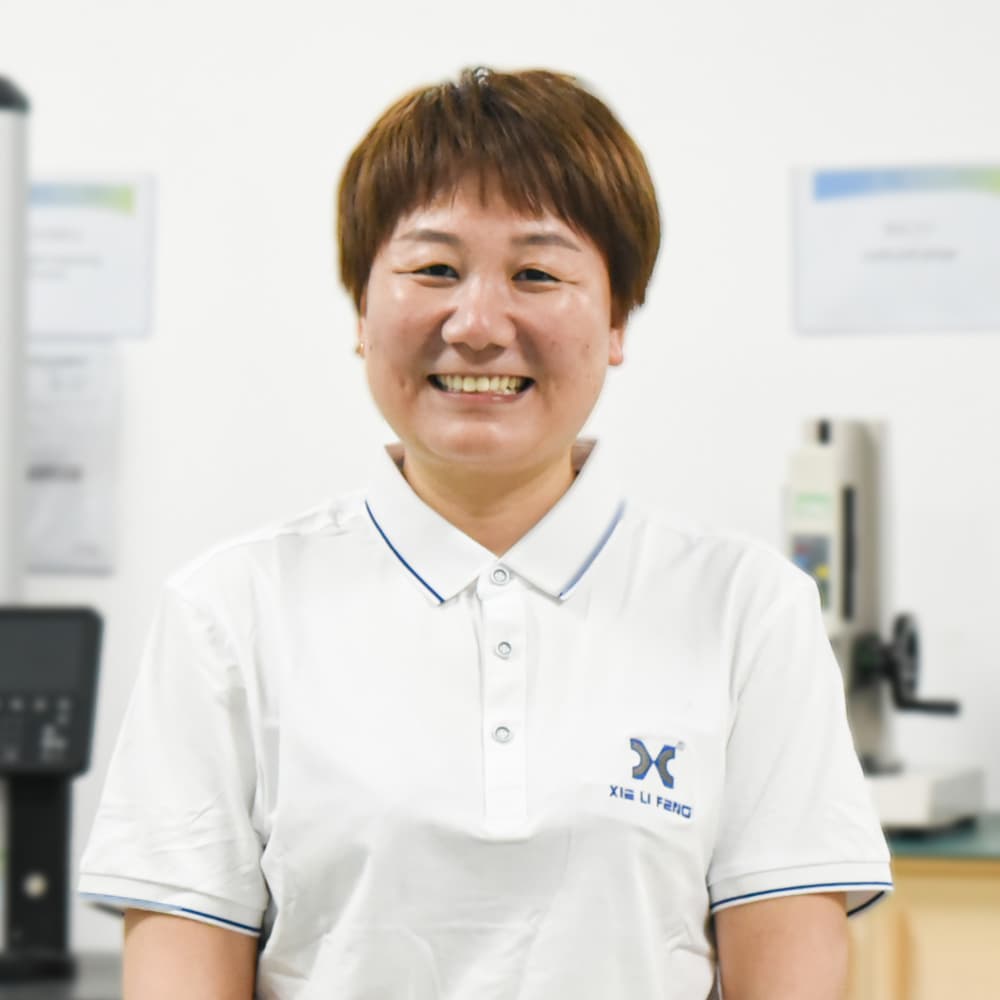
Celine Zhang
Position: QA
Ensure the implementation of the quality management system, conduct regular audits, and provide training support.
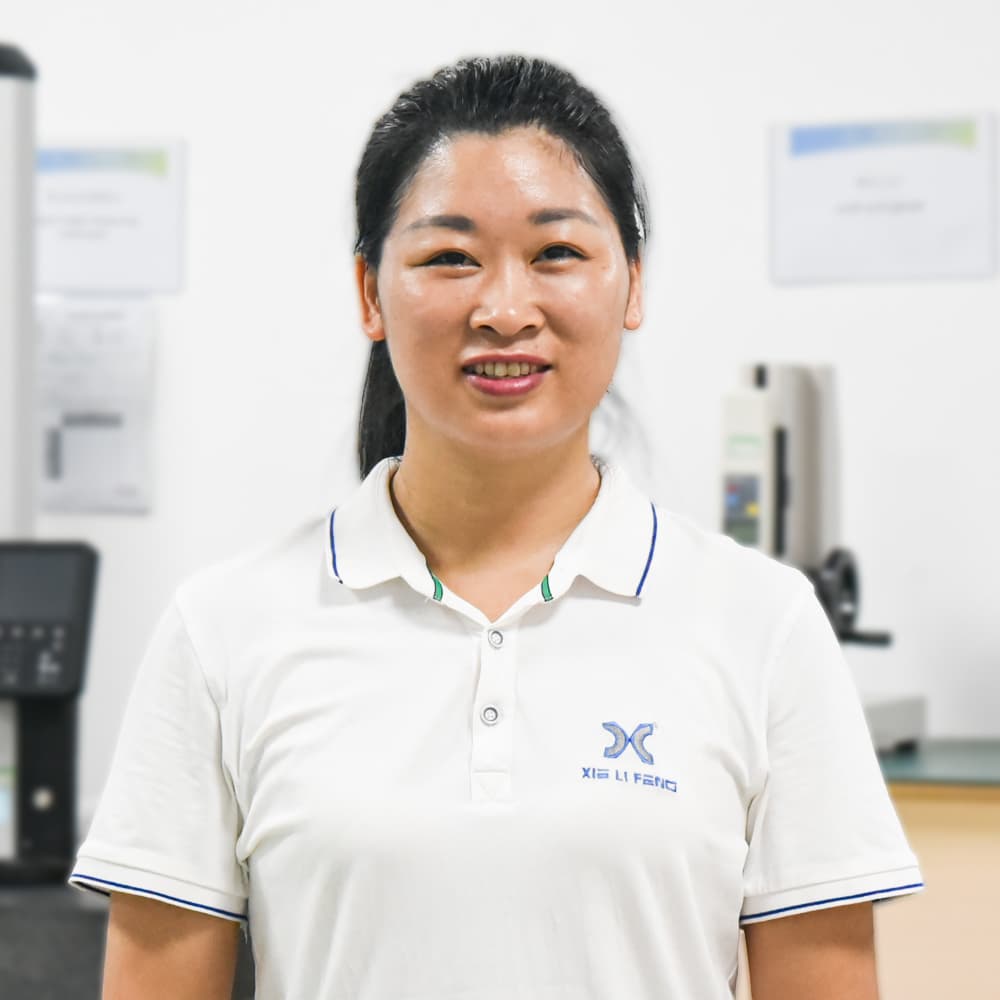
Emma Liu
Position: IQC
Responsible for inspecting and verifying all incoming material quality, ensure it meets requirements, and manage quality records.
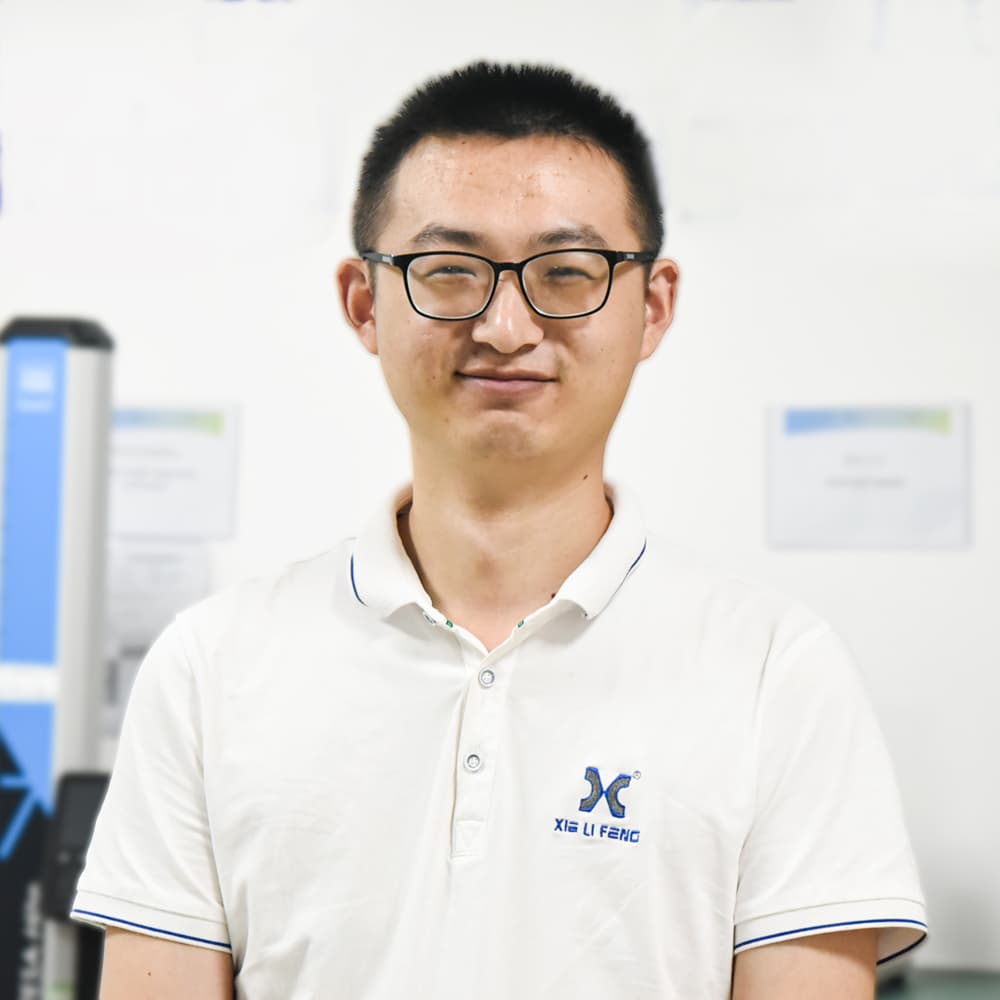
Owen Zhang
Position: IPQC
Conduct real-time inspections during production, ensure quality at each stage, and identify and report any issues.
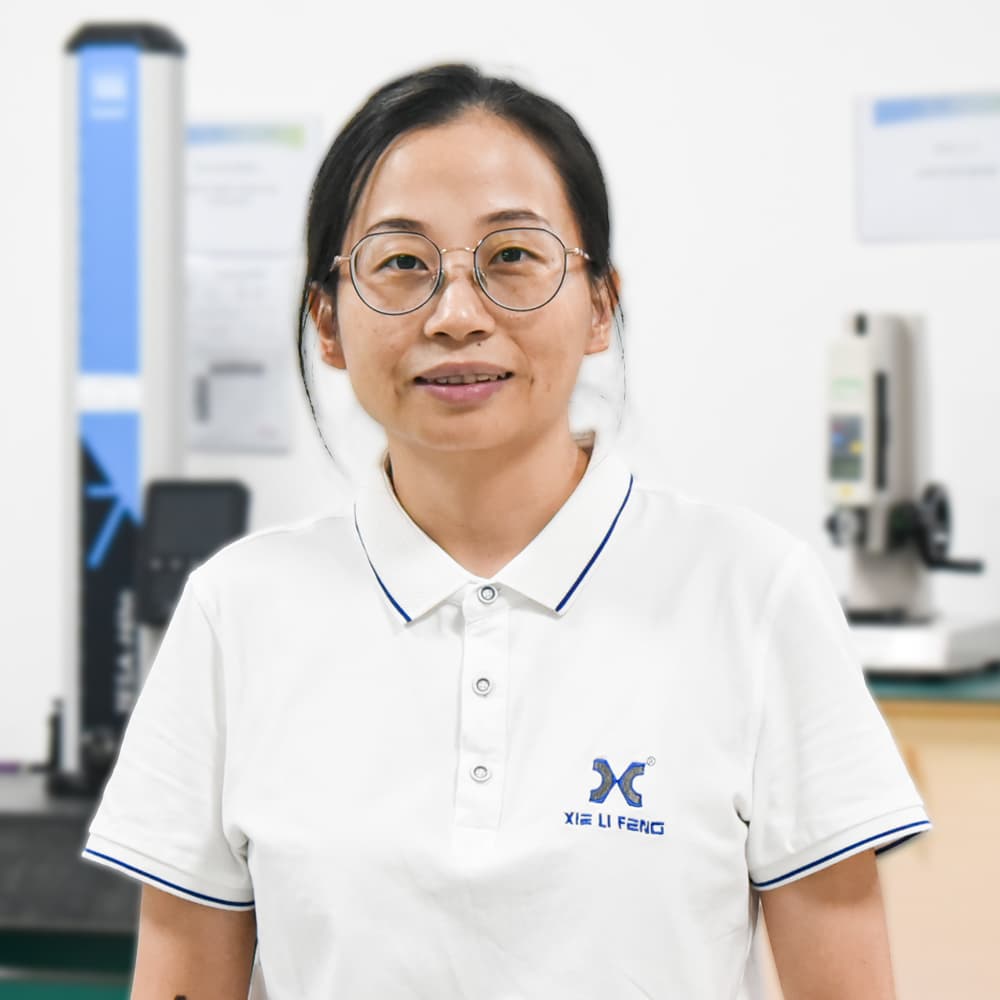
Lana Lu
Position: MQ
Calibrate and maintain inspection equipment, ensure accuracy, and support production and quality control needs.
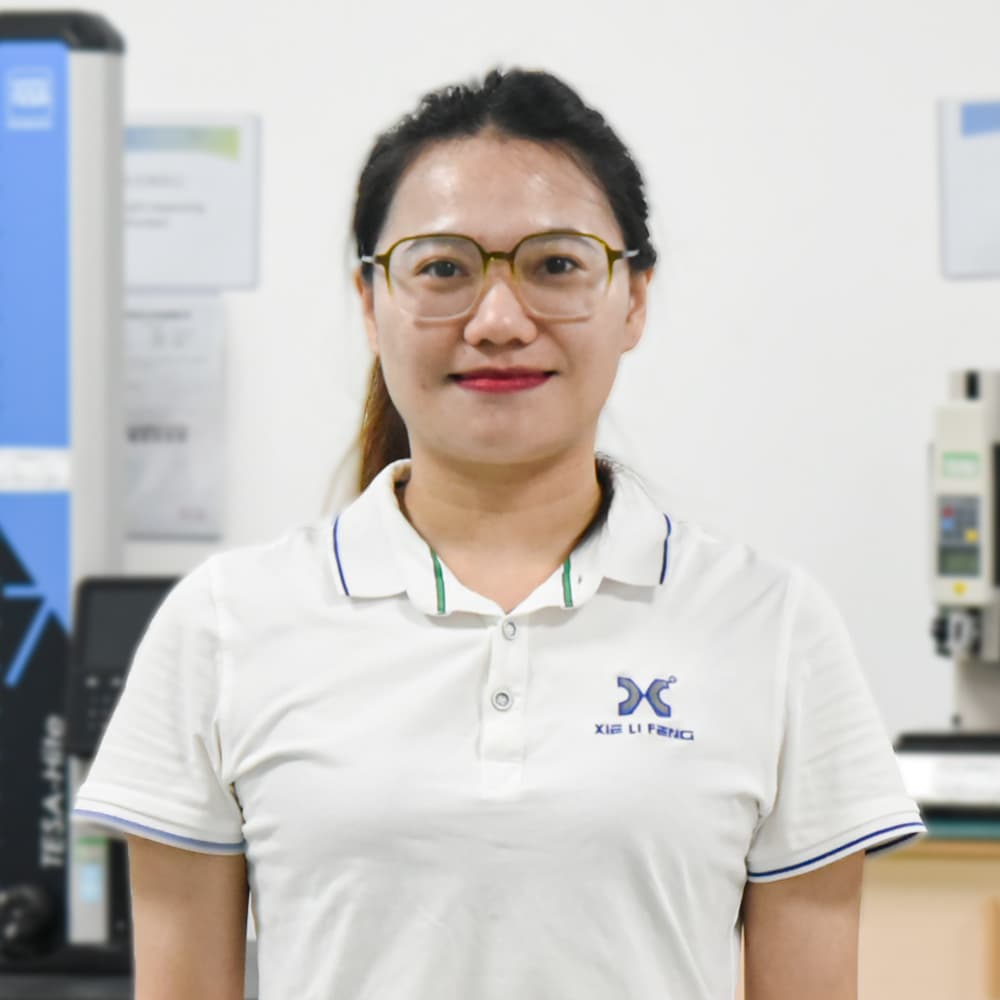
Nicole Xie
Position: QE
Analyze quality data and suggest improvements, handle quality issues and customer complaints, and support production quality control.
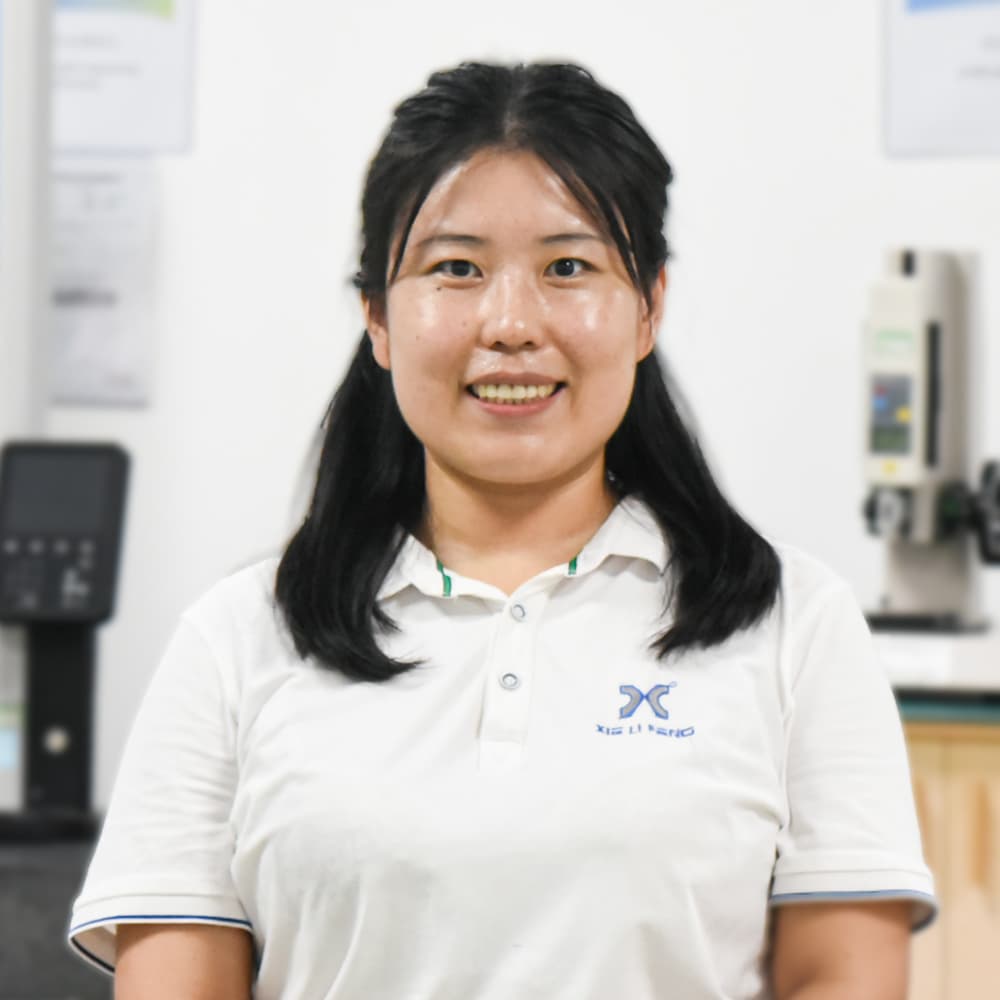
Nadine Wang
Position: FQC
Conduct final inspection of finished products, ensure they meet quality standards, and issue the final quality report.
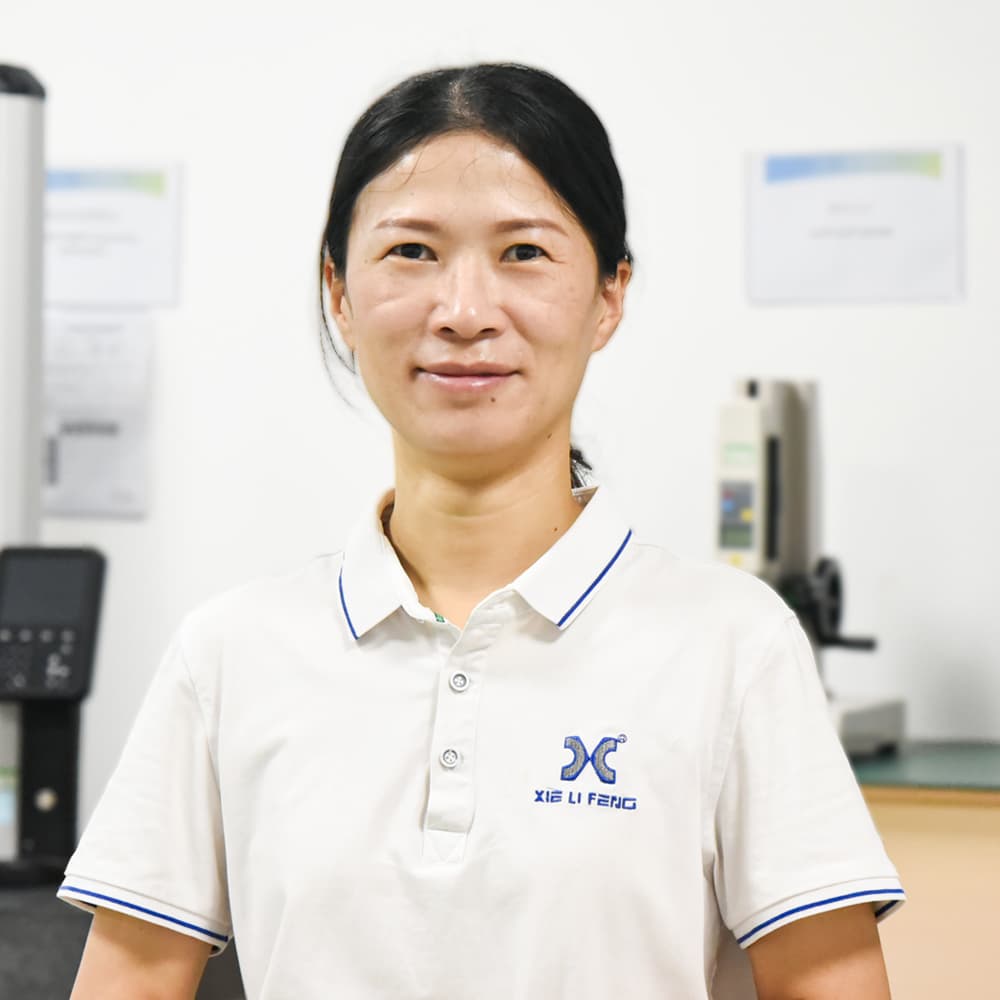
Kayla Wang
Position: OQC
Inspect finished product quality, ensure shipments meet customer requirements, and address any pre-shipment quality issues.
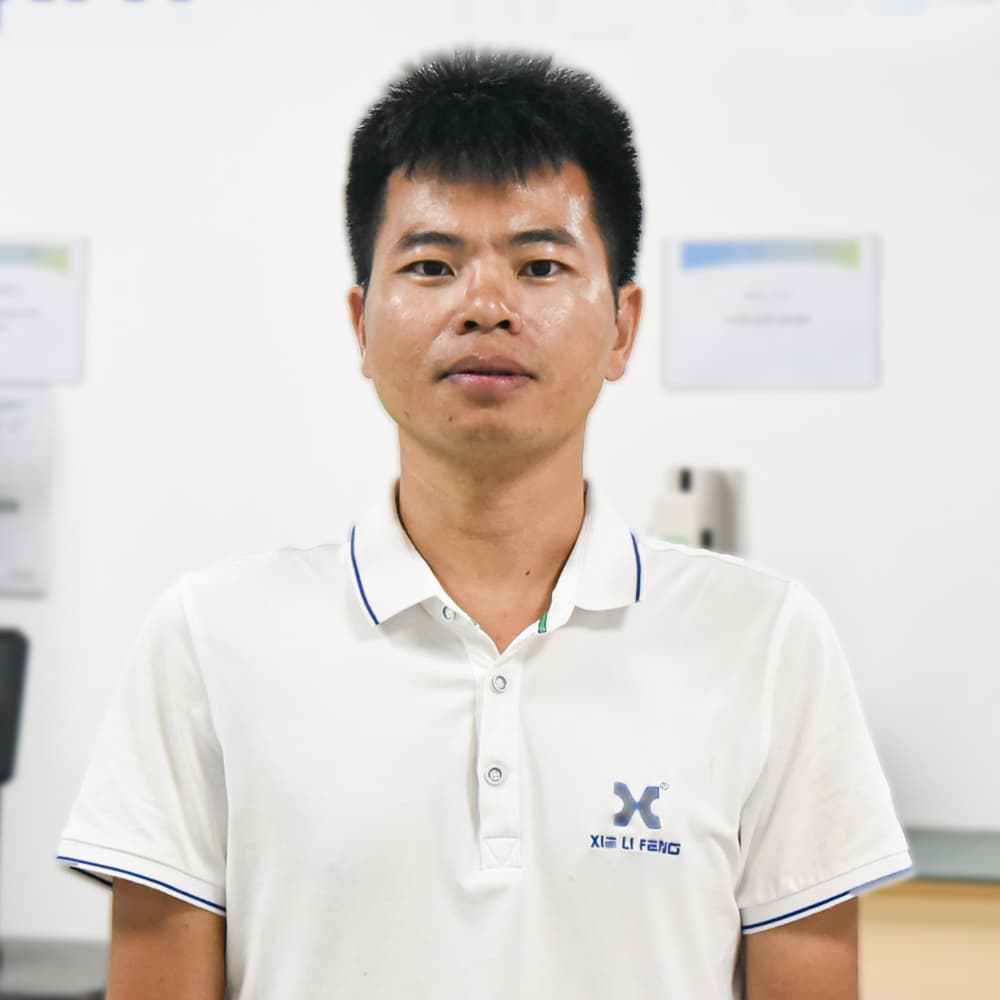
Jacob Huang
Position: PQC
Develop packaging standards, supervise the process, test strength, and resolve packaging issues for improvement.
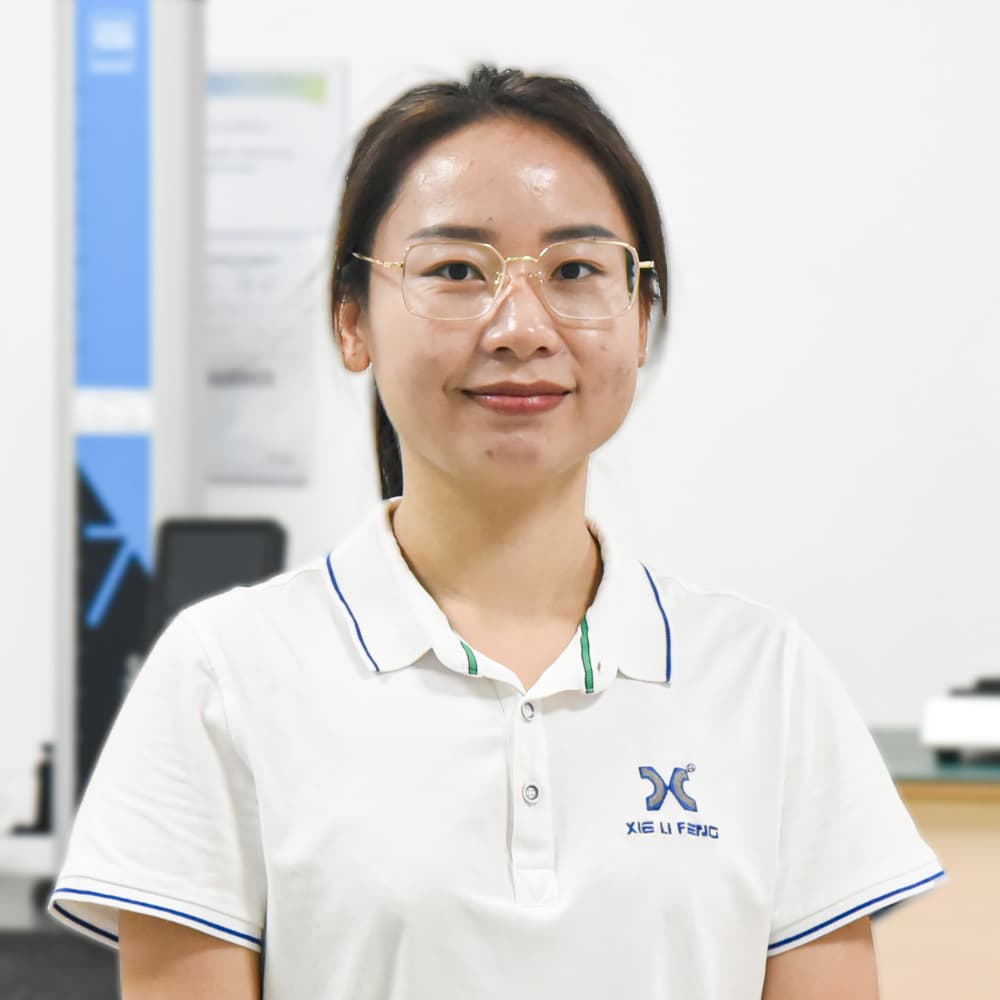
Eileen Qin
Position: CA
Handle customer inquiries, complaints, and feedback, provide solutions and after-sales support, and maintain customer relationships.
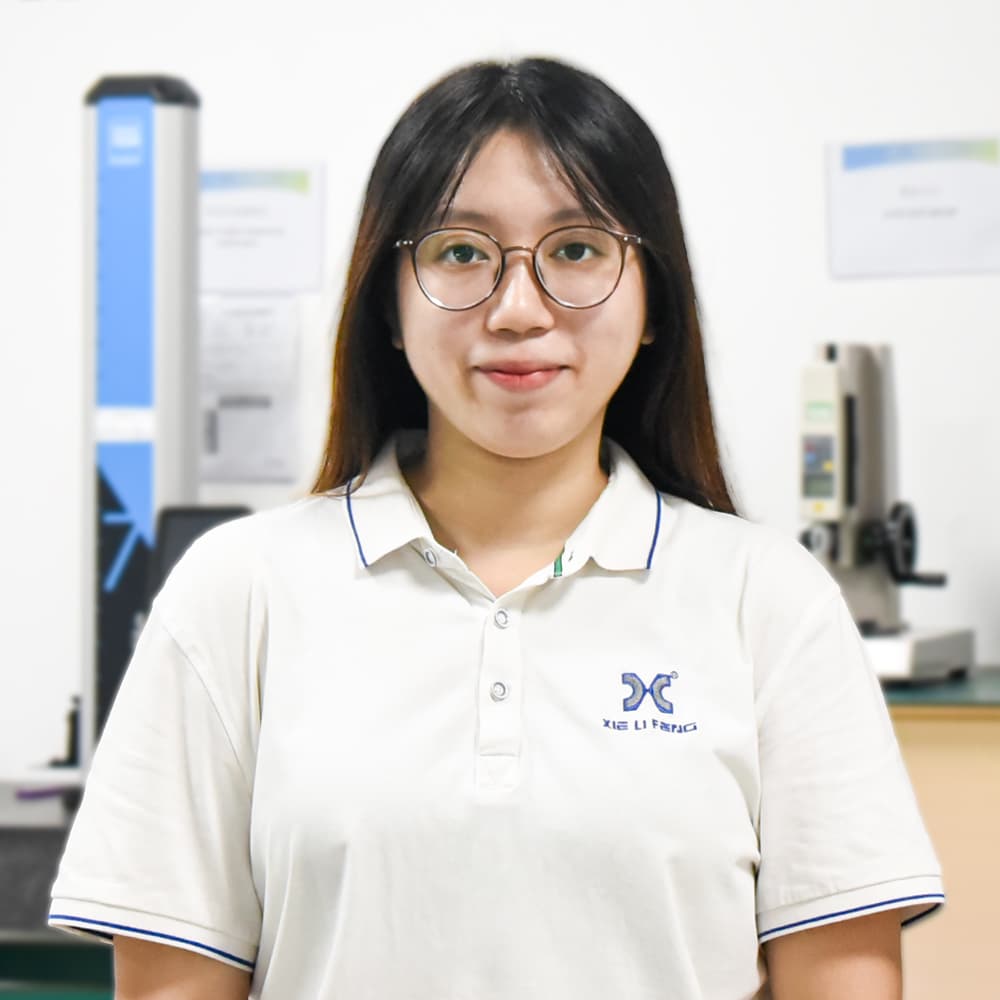
Camila Huang
Position: DCC
Manage quality documents, ensure accuracy and timely updates, and support the document needs of the quality control team.
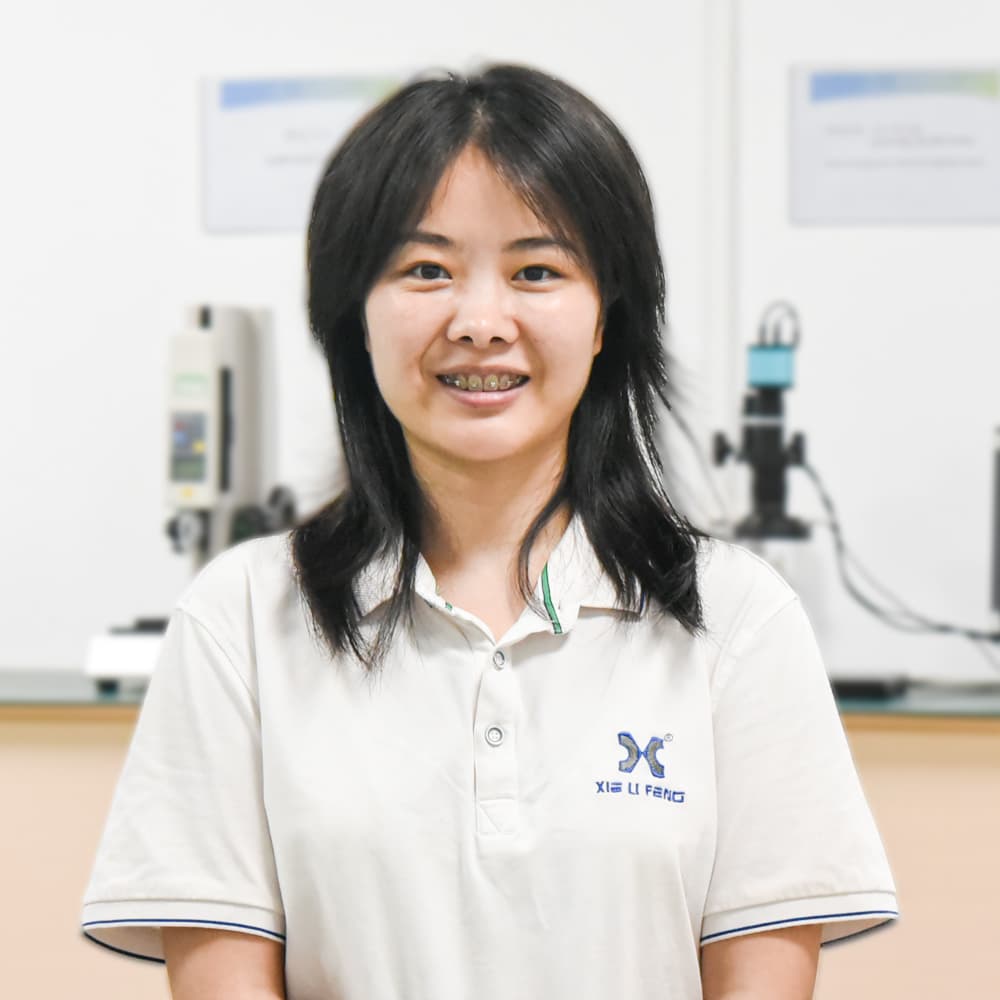
Estelle Luo
Position: CIM
Develop training plans to enhance skills, organize training for continuous learning, and evaluate and adjust content to ensure quality.
CNC Machined Parts Quality Control Process
QC process covers every step from order placement to delivery, ensuring each part meets the highest quality standards
01 Order Confirmation
Customer Requirement Confirmation:
Discuss requirements and quality standards, ensuring every detail is considered.
Technical Evaluation and Confirmation:
Evaluate drawings and technical requirements, confirm feasibility, and develop a quality control plan.
02 Incoming Inspection
Supplier Selection and Evaluation:
Choose qualified raw material suppliers to ensure supply chain stability and material quality.
Incoming Material Inspection:
Strictly test the chemical composition and mechanical properties of raw materials to meet standards.
03 In-Process Control
Process Planning and First Part Inspection:
Develop process flow and thoroughly inspect the first article’s dimensions, shape, surface, and performance.
Process Monitoring and Statistical Process Control:
Monitor production data in real-time, implement SPC, and ensure production stability and quality consistency.
04 Final Inspection
Final inspection:
Final inspection of finished products to ensure that the size and performance meet the standards.
Packaging and compliance inspection:
Develop and implement packaging specifications to ensure transportation safety.
05 Delivery
Pre-shipment Inspection:
The quality technician performs random checks to ensure high product quality.
Shipping Preparation:
Customer representative confirms shipping details to ensure timely and safe delivery.
06 Continuous Improvement
Customer Feedback Handling:
Collect and address customer feedback and complaints.
Quality Improvement:
Analyze feedback and data, implement improvements, and enhance quality and satisfaction.
Xielifeng Quality Inspection Equipment
Xielifeng’s quality inspection team is composed of experienced professionals with deep industry expertise and rigorous quality standards. We employ state-of-the-art inspection equipment to ensure every product meets the highest quality requirements.
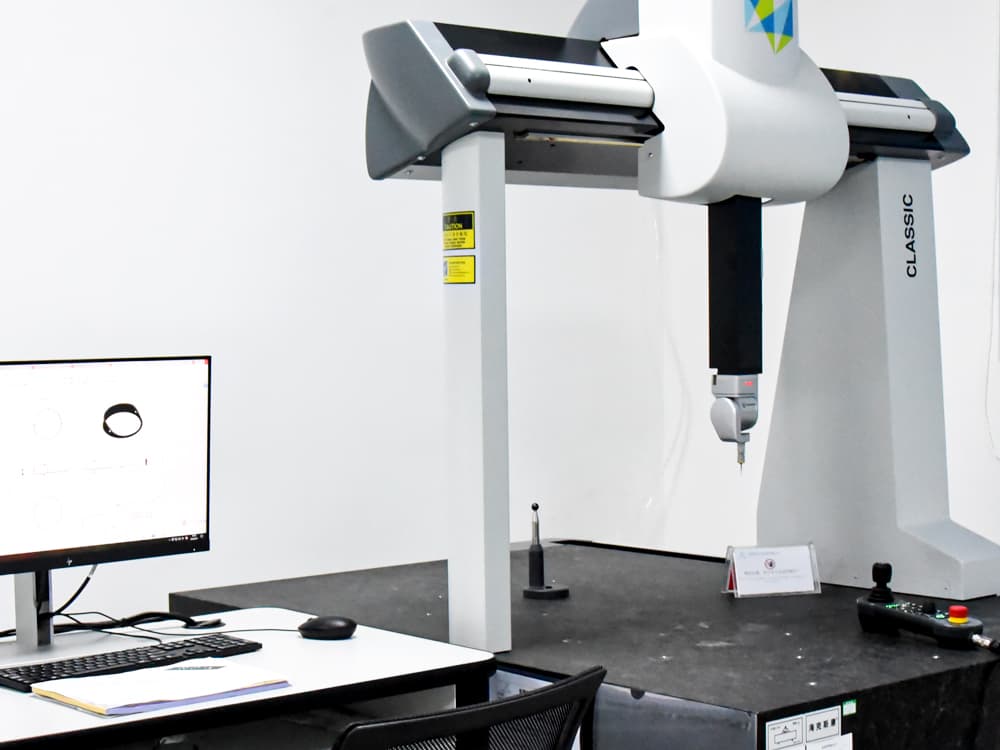
Coordinate Measuring Machine
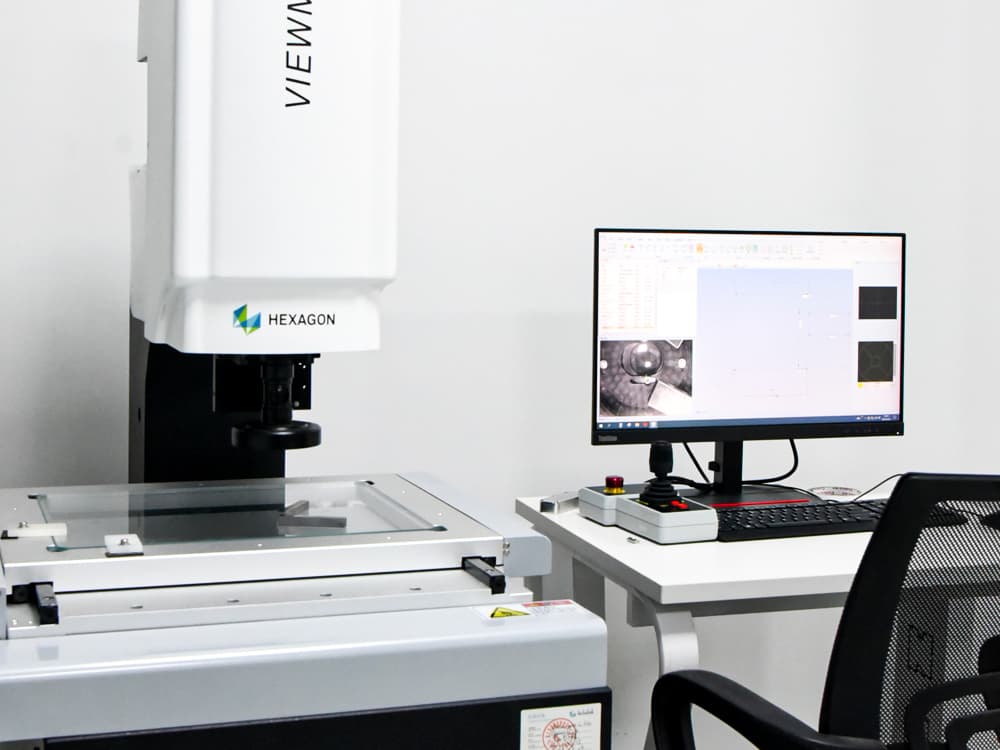
Quadratic Element Measuring
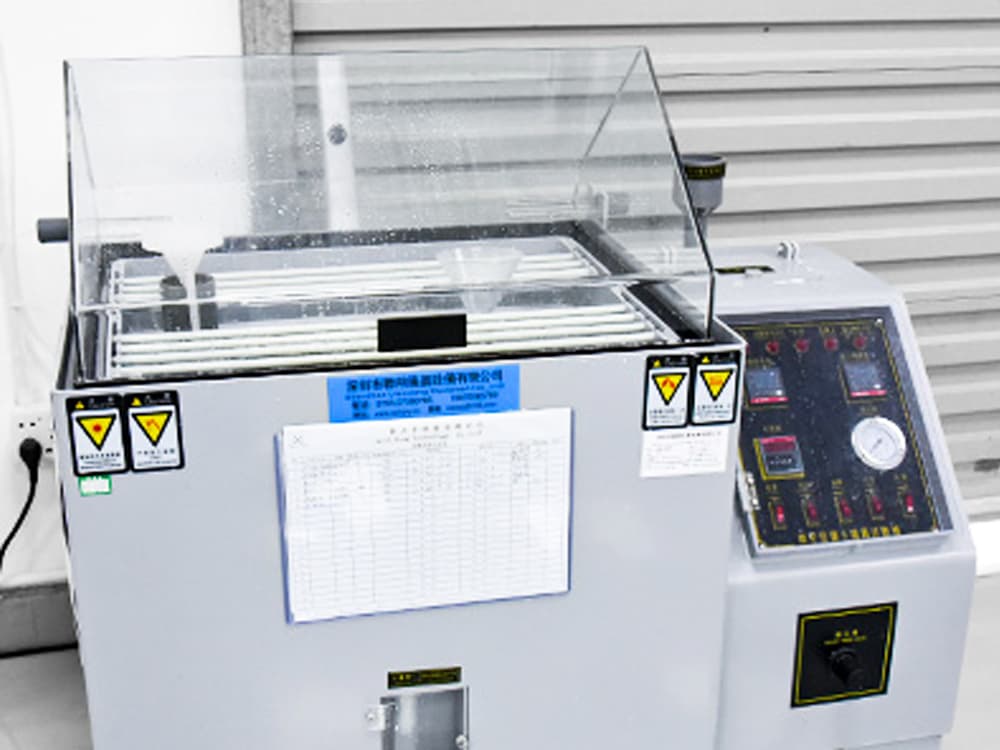
Salt Spray Tester

UV Aging Test Machine
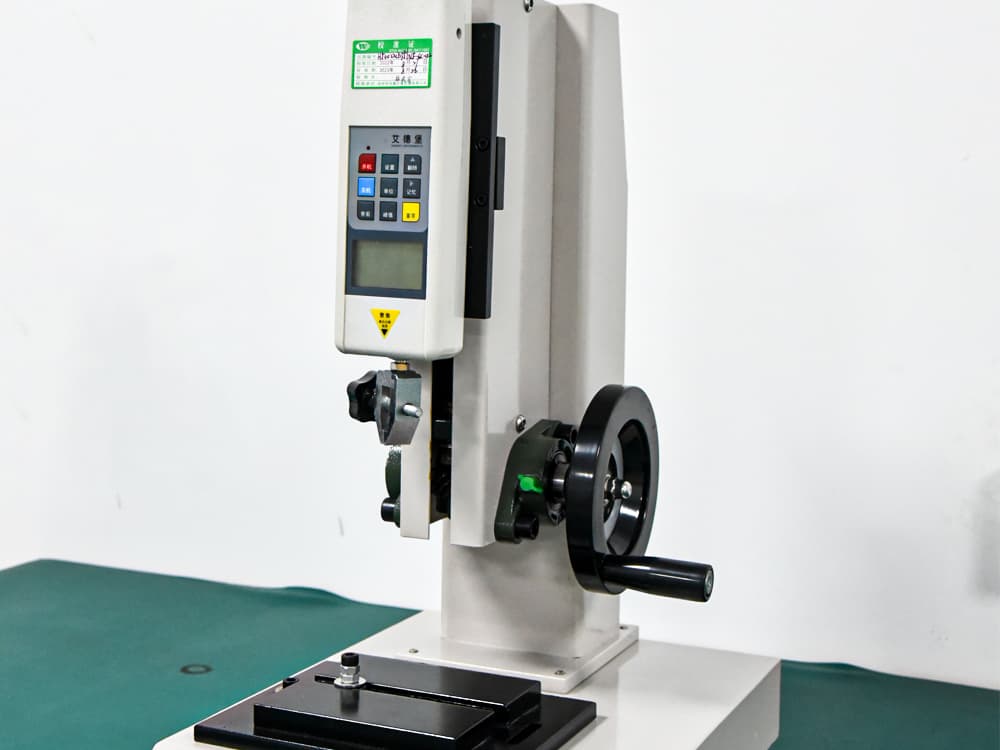
Push-pull Gauge
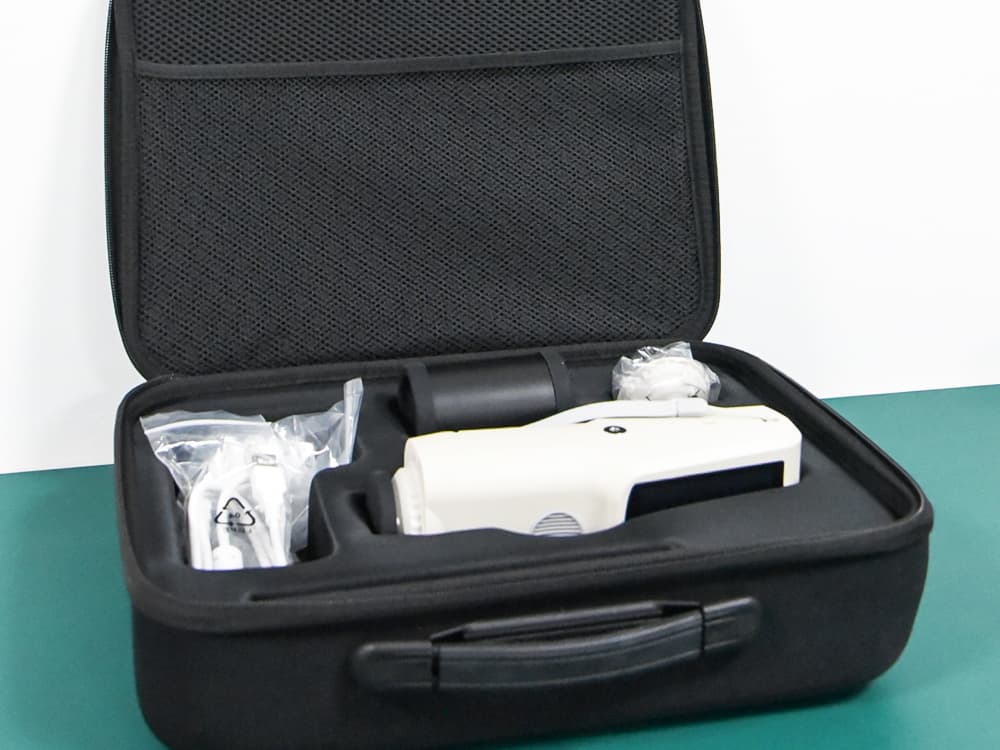
Color Tester
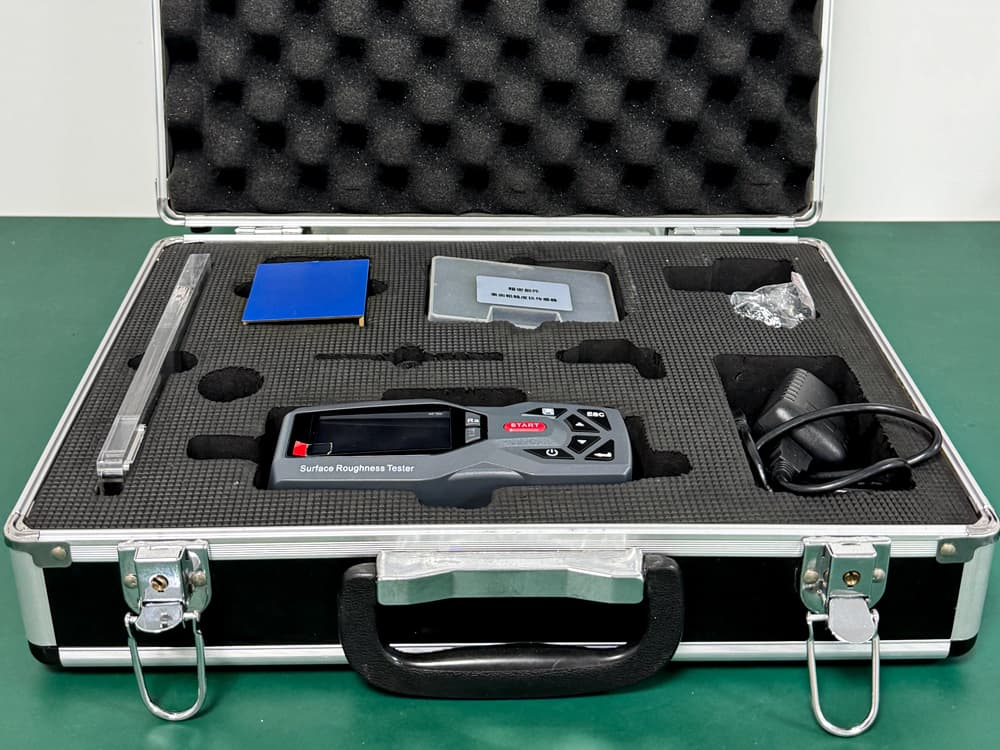
Digital Roughness Tester
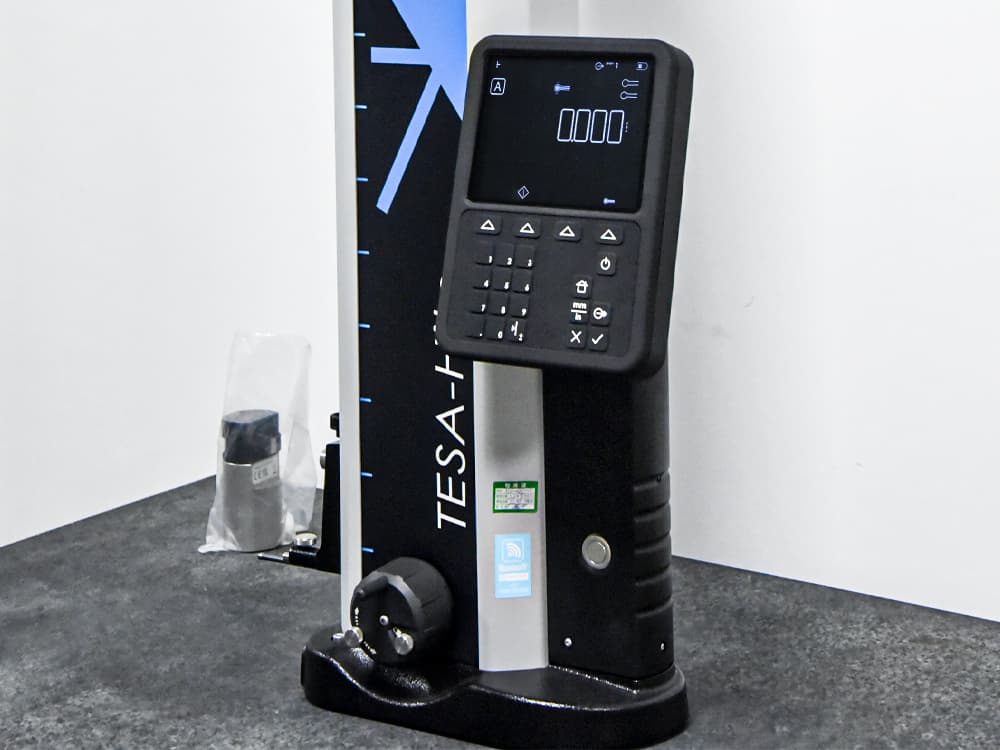
Digital Height Instrument
Quality Certificate & Test Report
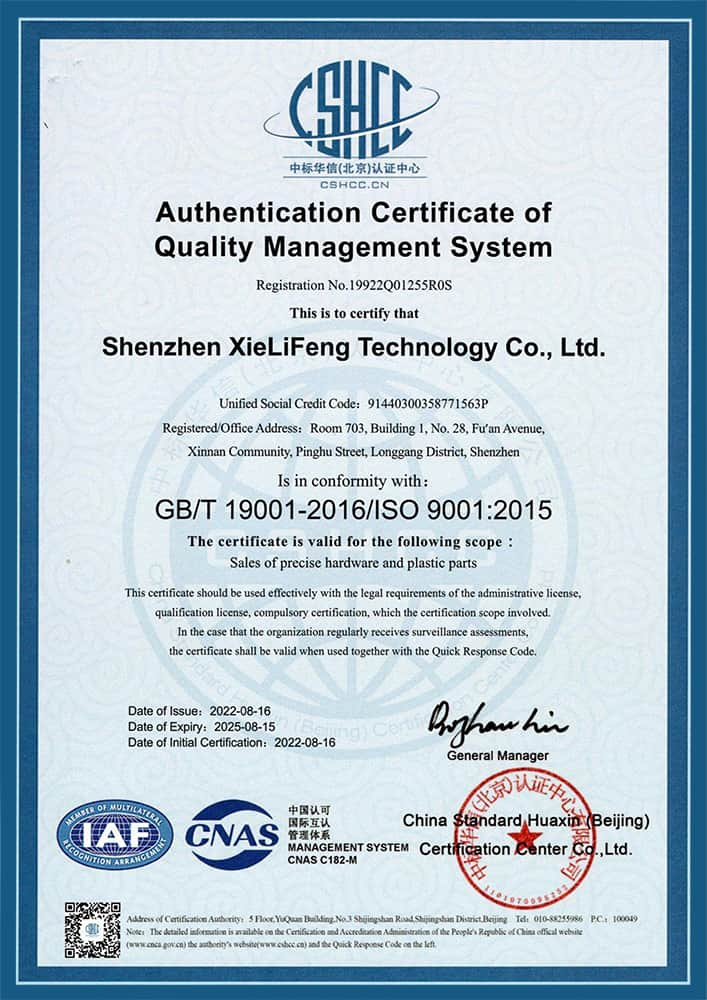
ISO 9001
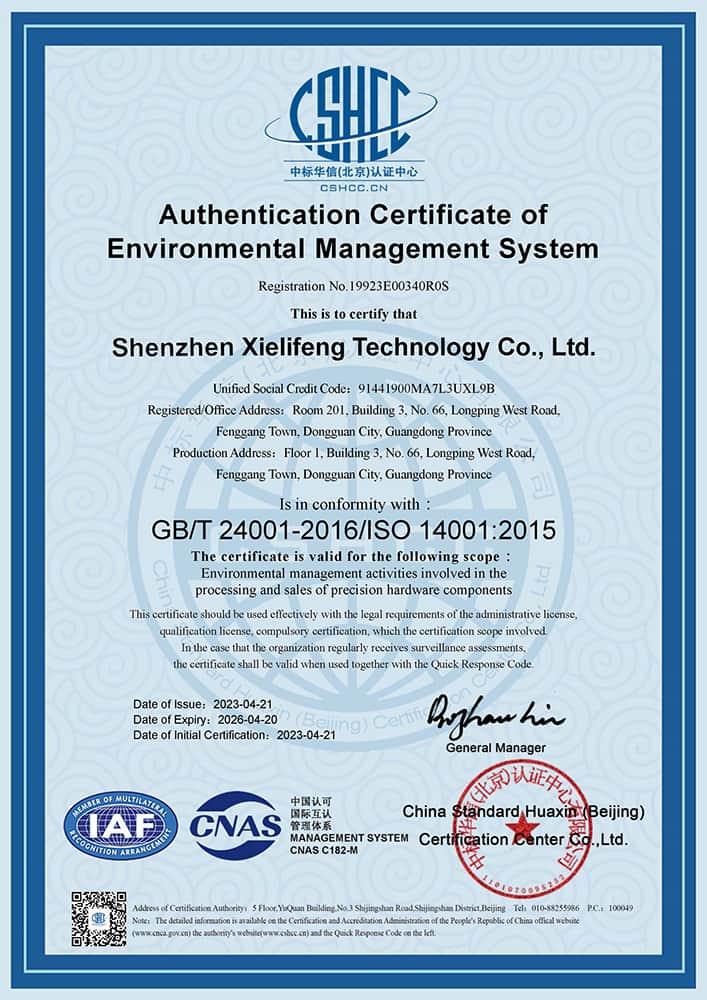
ISO 14001
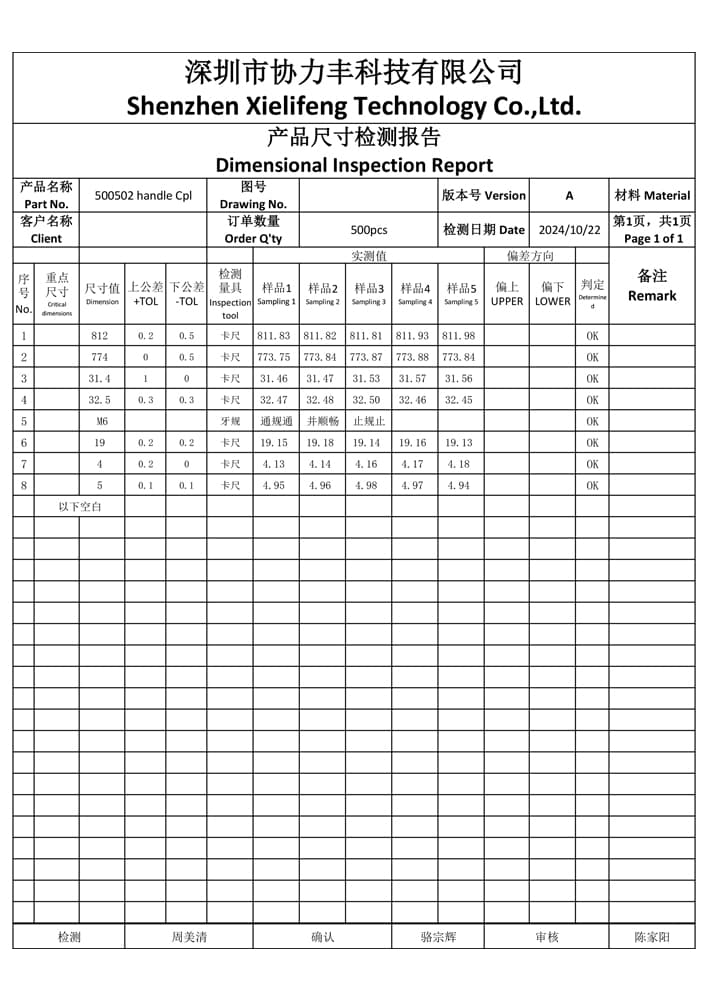
Product Size Inspection Report
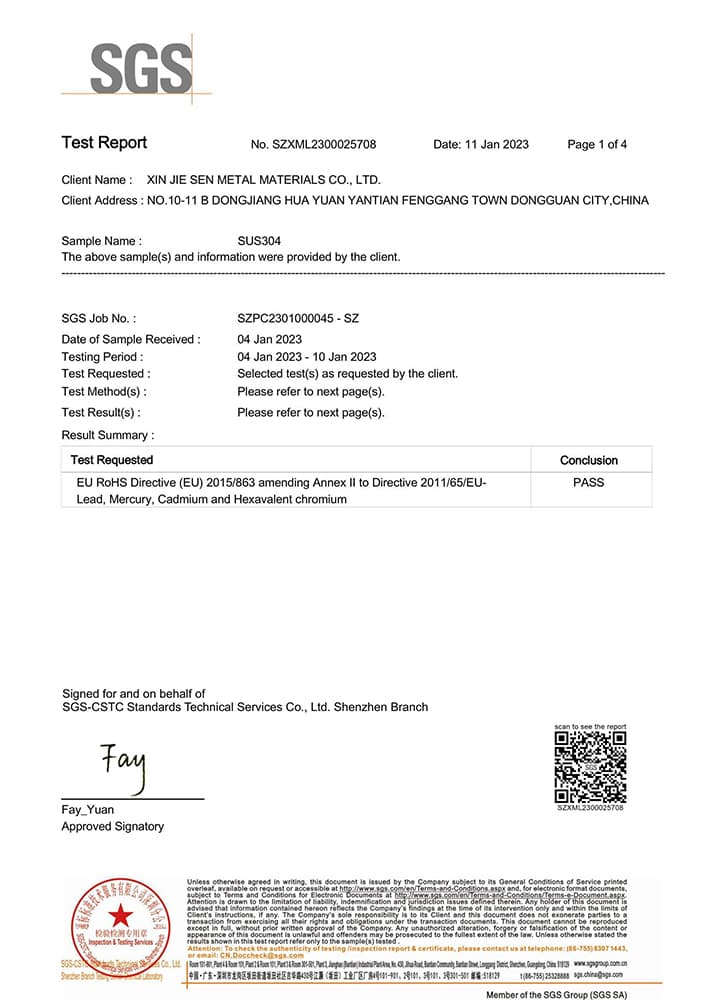
Reach
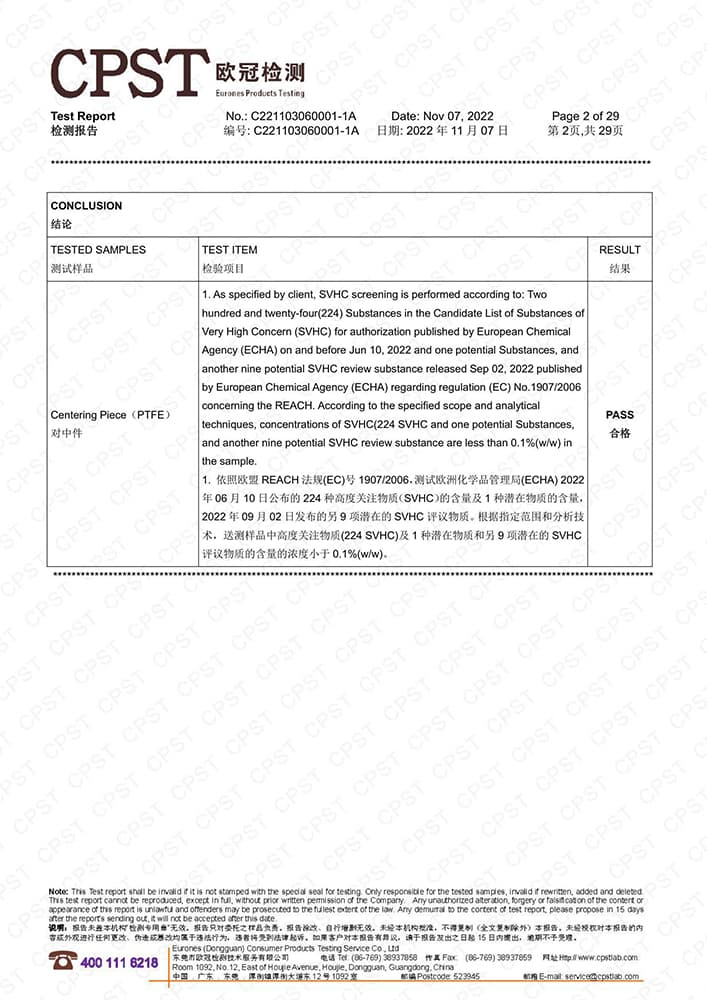
RoHs
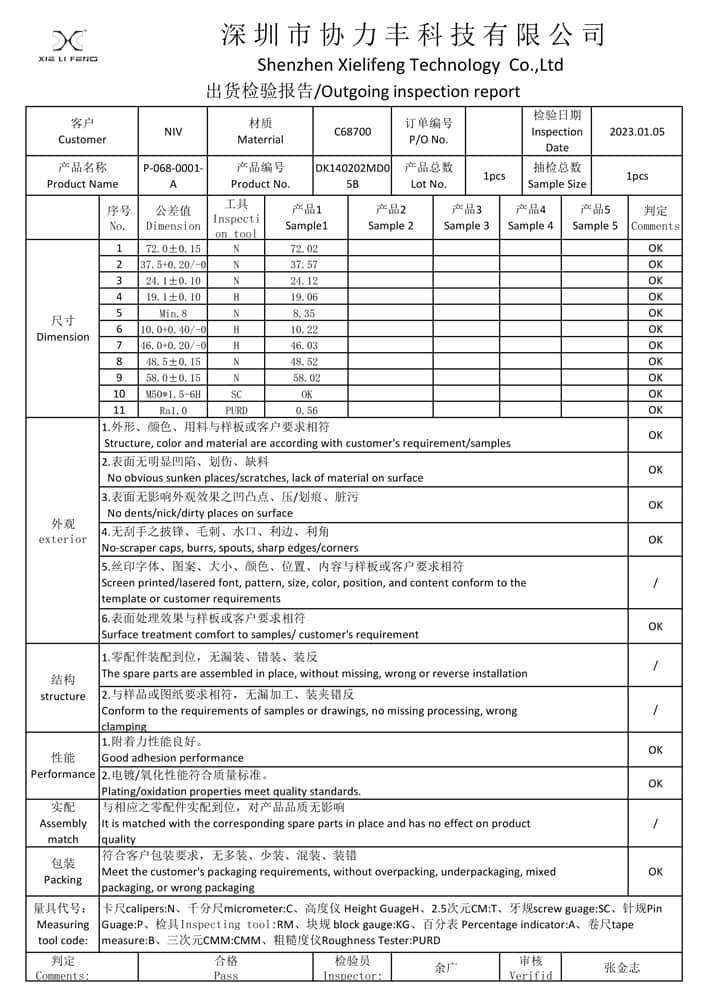
Shipment Inspection Report
Voices from Xielifeng's Partners
Customer-Tested, Worry-Free Choice
Our partners praise our precision, reliability, and flexibility.
Contact us and join our satisfied clients!
Parts are consistently high-quality and delivered on time, helping us complete multiple projects. I look forward to continued collaboration.
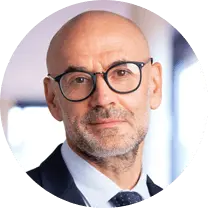
John Stevens
Parts are exceptional, meeting our precision and reliability standards. We are satisfied with your strict quality control and high standards.
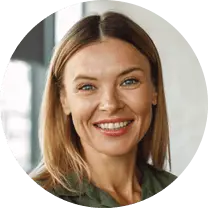
Sarah Mitchell
Your precise and reliable parts make our products popular. We are very satisfied with your professional quality control and service.
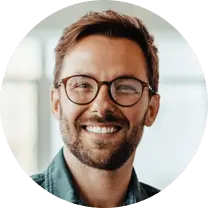
James Walker
Your medical device parts passed stringent biocompatibility and sterility tests, fully meeting the high standards of the medical industry.
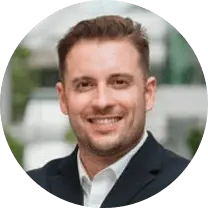
Ethan Thompson
Your after-sales service is very prompt, always responding quickly and resolving issues whenever needed. We are very satisfied with your customer service.
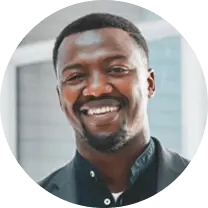
Alex Johnson
Xielifeng’s production efficiency is excellent, and it quickly responds to our urgent orders. We highly appreciate your flexibility and efficient operations.
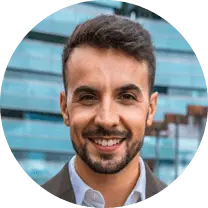
Benjamin Clark
Xielifeng focus on environmental protection and sustainability is commendable. Collaboration has been very pleasant.
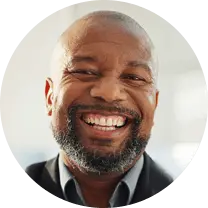
Robert Green
Your strong innovation consistently delivers high-precision and complex parts. We highly appreciate your technical development capabilities.
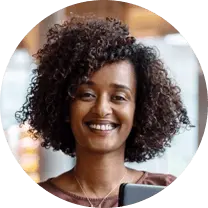