Stainless Steel CNC Machining
Pofessional and fast machining stainless steel 303, 304,316, etc. with tight tolerance and fine workmanship.
- No MOQ is requited
- Quote as fast as one day
- Sample can be make in 3 days
- Bulk order can be finished within 15 days
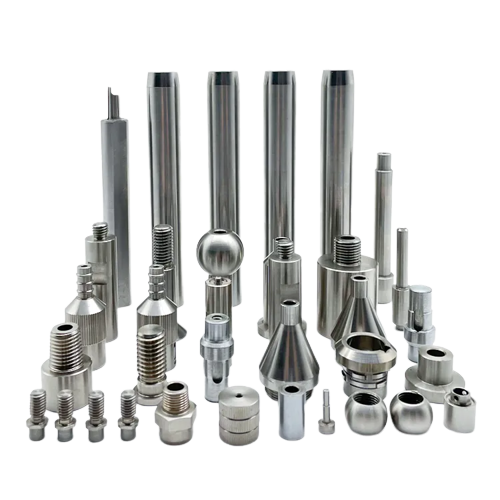
Features of Stainless Steel
- Weldability
- Corrosion resistance
- Polishing performance
- Heat resistance
Applications of Stainless Steel
CNC machining of stainless steel is used to produce a wide range of parts for the medical industry, robotics, food and beverage industry, aerospace, and any industry that requires high-strength applications. Stainless steel is ideal for the following applications:
- Medical instruments
- Mechanical Parts
- Gear
- Tractor parts
- Heavy construction equipment
- Vacuum and Pressure Vessels
Stainless steel has excellent machinability, excellent uniformity, corrosion and oxidation resistance, resulting in longer product life and lower overall cost of machined parts.
CNC Machining Stainless Steel Guide
CNC machining stainless steel is a common manufacturing process used to create precise and intricate parts from stainless steel materials. Stainless steel is a challenging material to machine due to its hardness, toughness, and tendency to work harden during machining. However, with the right tools, techniques, and parameters, CNC machining can be effectively used to work with stainless steel. Here are some important considerations:
Tooling: Use high-quality carbide or ceramic cutting tools specifically designed for stainless steel machining. These tools are able to withstand the high temperatures generated during machining and can provide longer tool life.
Cutting Speeds and Feeds: Stainless steel requires lower cutting speeds compared to softer materials to prevent excessive heat buildup. Consult cutting tool manufacturers’ recommendations for appropriate cutting speeds and feeds based on the specific stainless steel alloy you’re machining.
Coolant: Adequate cooling and lubrication are crucial to prevent overheating and work hardening of the material. Use appropriate cutting fluids or coolants to reduce friction and dissipate heat.
Tool Path Strategy: Optimize your tool paths to reduce the amount of tool engagement and minimize the heat generated. Consider using climb milling instead of conventional milling to reduce tool wear and heat generation.
Depth of Cut: Take shallow cuts to avoid putting excessive stress on the cutting tool and to prevent work hardening of the material.
Machine Rigidity: Ensure that your CNC machine is properly calibrated and rigid enough to handle the demands of stainless steel machining. Vibration and deflection can negatively impact the machining process.
Material Selection: There are different types of stainless steel alloys, each with varying properties that affect machinability. Austenitic stainless steels (like 304 and 316) are generally more machinable than martensitic or duplex stainless steels. Select the appropriate alloy for your application.
Preparation: Properly secure the workpiece to prevent movement during machining. Soft jaws, fixtures, or clamps can be used to ensure stability.
Post-Machining Treatments: Stainless steel parts may require post-machining treatments such as heat treatment, passivation, or electropolishing to improve surface finish, corrosion resistance, and remove residual stresses.
Safety: Stainless steel machining can produce sharp chips and generate heat. Use appropriate personal protective equipment (PPE) and follow safety guidelines to prevent accidents.
It’s important to note that the specific recommendations and parameters can vary based on the exact type of stainless steel being machined, the CNC machine’s capabilities, and other factors. Consulting with experienced machinists, tool manufacturers, or process engineers can provide valuable insights tailored to your specific machining requirements.